Story at a glance:
- Increased off-site construction can help to solve some of today’s biggest industry challenges.
- Off-site construction, often called modular or prefab, can provide superior energy efficiency, significant cost efficiencies, and more.
There is no hiding that the US building industry currently faces a myriad of challenges— including workforce availability, supply chain variability, stagnant productivity and costly delays, job site safety, housing affordability, building quality, and sustainability.
Conventional building and construction practices continue to yield inefficient productivity to meet current demands, with more than 75% of projects being late, over budget, or both. Building construction also generates a significant amount of waste. Roughly 30% of all building materials delivered to a conventional construction site ends up as waste, with more than 600 million tons of US construction-related waste produced in 2018 alone.
Clear barriers to affordability and sustainability of conventional construction practices opens the door for innovation. The expanded use of off-site construction (often called modular or prefabrication) offers a promising solution to address the pressing challenges the industry faces today and those we will see into the future.
What is Off-Site Construction?
Off-site construction includes a variety of processes—including production of volumetric modules (fully enclosed rooms with six sides), wall panels with integrated insulation and building system components, bathroom or kitchen pods, prefabricated accessory dwelling units (ADUs), manufactured housing, tiny houses, and shipping containers that are fabricated in a factory. Off-site construction processes vary from traditional construction such that on-site inspection methods are not adequate to determine compliance with building codes.
Benefits of Off-site Construction
Prefabricated buildings are an attractive option for developing new construction projects because of their potential advantages over conventional construction. Off-site construction can provide superior energy efficiency, tighter building envelopes, carbon and waste reduction, significant cost efficiencies, buffering of supply chain delays, and attractive employment for a new generation of the construction workforce, among other benefits.
With national housing costs rising 52% from 2017 to 2022, modular construction offers an affordable solution, capable of curbing construction timelines and reducing costs. Off-site construction can deliver projects 20 to 50% faster than traditional methods, which can provide cost savings of up to 20%. Off-site construction processes also allow multiple building components to be constructed simultaneously while protecting the components and workers from weather-related and other risks.
In addition, off-site construction provides climate mitigation benefits. According to research by the University of Cambridge and Edinburgh Napier University, off-site modular constructed homes can provide embodied carbon savings of 45% over traditional methods of residential construction. It is ever critical to reduce the environmental footprint of the construction sector as embodied carbon associated with the production and transportation of construction materials in conventional practices accounts for 11% of global emissions—a major driver of climate change.
However, the economic, environmental, and time-saving benefits of off-site construction quickly diminish if states and localities do not have efficient mechanisms to determine the compliance of off-site construction with applicable building code requirements.
Fragmentation of Off-site Construction Processes
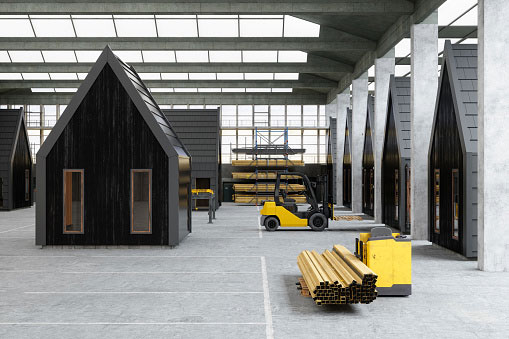
Photo courtesy of ICC-ES
Currently a patchwork of compliance processes exists for off-site construction—hindering some of the efficiency gains that off-site construction can provide. The economic and time-saving benefits of off-site construction quickly diminish if states and localities do not have efficient mechanisms to determine the compliance of off-site construction with applicable building code requirements.
Currently 39 states plus Washington, D.C. regulate off-site construction at the state level. State programs are responsible for plan review and inspection of off-site construction components. However, these programs vary significantly from state to state—some states allow third-parties agencies to conduct both plan review and in-factory inspections whereas others only allow state employees to perform these functions.
There is also inconsistency in the types of projects and components covered in each state—some only cover residential construction and others just commercial, and some include closed panels where others only cover volumetric modules. Varying requirements increases costs for manufacturers and the resulting variation in construction practices can make code enforcement more difficult.
Where a state does not have a program, all requirements fall to the local authority having jurisdiction (AHJ) over building regulation—including plan review and in-factory inspection—which can present capacity and capability challenges for both local code officials and the project team.
Inspection and plan review of modular components requires both specialized expertise as well as the means to conduct inspections in factories that may be miles away from the final job site. Where a state or local government does not have the necessary expertise, staffing, or resources to facilitate these activities, off-site construction can be significantly stalled or prevented altogether. Third-party agencies, including ICC-NTA, can be leveraged to provide this expertise, often resulting in quicker turnaround times without impacting quality or department revenue.
The current code landscape and regulatory barriers reflect the construction industry’s aversion to change. Growing recognition that a mechanism to help both jurisdictions and project teams best utilize off-site construction, while assuring these projects meet building code requirements, was imminent to unlock more streamlined and efficient approaches to construction.
Standards for Off-site Construction
- Cover courtesy of ICC-ES
- Cover courtesy of ICC-ES
To address the gap in consistency of off-site construction processes, the International Code Council (ICC) and Modular Building Institute (MBI) partnered to develop a coordinated set of standards that cover the entire off-site construction process, capturing best practices and supporting a consistent approach to verifying compliance. The standards apply to all componentized, panelized, and modularized elements in both commercial and residential buildings, except manufactured housing. Note that “manufactured housing” is defined as a form of off-site construction, but its design and assembly is regulated by the US Department of Housing and Urban Development. Local code officials retain responsibility to site work, installation, and accessory structures. ICC/MBI 1200 and 1205 do not apply to manufactured housing.
ICC/MBI Standard 1200-2021: Standard for Planning, Design, Fabrication, and Assembly in Off-Site Construction. Standard 1200 provides requirements for designers, manufacturers, transporters, and assemblers to assure off-site construction components are produced under a quality assurance/quality control process and that they can demonstrate compliance with building code requirements.
ICC/MBI Standard 1205-2021: Standard for Inspection and Regulatory Compliance in Off-Site Construction. Standard 1205 addresses the compliance verification process including permitting, in-plant and on-site final inspections, third-party inspections, and the role of Industrialized Building Departments, state modular programs, and the AHJ.
ICC and MBI are also in the process of developing a third standard, ICC/MBI Standard 1210: Standard for Mechanical, Electrical, Plumbing (MEP) Systems, Energy Efficiency and Water Conservation in Off-site Construction. Standard 1210 will address requirements for the energy efficiency and water conservation of off-site construction projects and the planning, designing, fabricating, transporting, and assembling of commercial and residential building MEP system elements. The implementation of this standard following its development will further enhance the sustainable benefits of off-site construction.
The aforementioned standards provide an off-site construction specific mechanism to assure compliance with any edition of the building codes. They do not provide alternatives to existing code provisions but rather a process for verifying compliance given that part of the construction process occurs in a factory and not at the final job site. These standards are intended to sit alongside existing codes and standards to provide the process whereby off-site construction compliance with state or locally adopted building codes and standards is verified.
Innovation Driving Progress
Achieving affordability and sustainability in the building and construction industry requires innovative approaches to the conventional methods that have created stagnancy. Breaking the mold of traditional construction paradigms will welcome more innovation and advanced building construction solutions.
Harnessing off-site construction as a solution to the challenges faced throughout the industry can enable economies of scale, increase job site safety, ensure greater and more consistent construction quality, and enhance sustainability through reduced waste and product spoilage. It also can address climate change through enhanced energy efficiency, reduced greenhouse gas emissions, and embodied carbon savings. With growing support and uniformity through standardization of processes, off-site construction addresses the social, environmental, and economic struggles of an industry that continues to fall behind the needs of society.