Whitacre Greer’s permeable clay pavers make more construction projects possible.
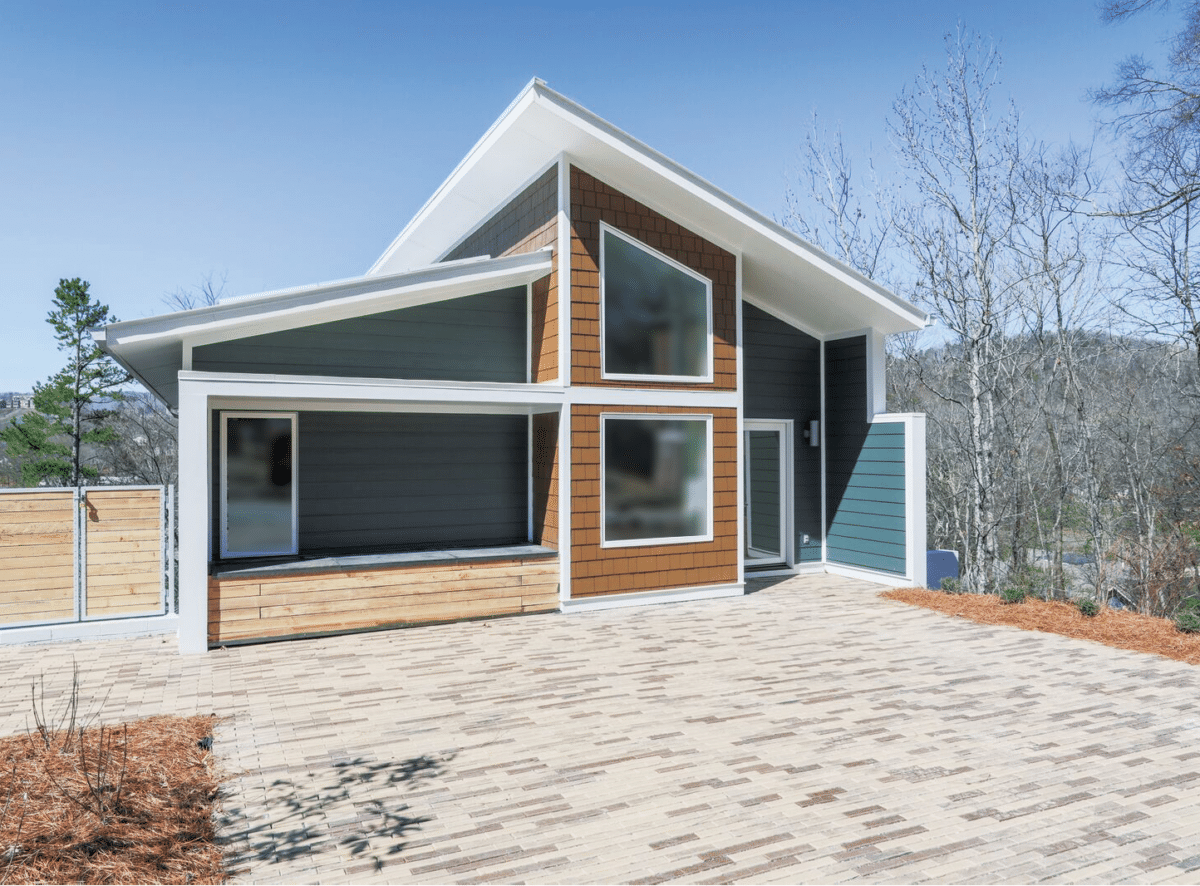
[Photo: Courtesy of Whitacre Greer]
Stormwater is a big problem for much of Chattanooga, Tennessee, but not for homes in the NextGen Homes development, thanks to permeable pavers.
Stormwater buildup leads to millions of gallons of combined sewer overflow dumping unkempt—and unsanitary—sewage into waterways each year, says Michael Walton, executive director of green|spaces. That’s why the nonprofit architecture firm decided to use permeable pavers by Whitacre Greer for its zero-energy, water-efficient, healthy home development.
FROM OUR JANUARY+FEBRUARY 2018 ISSUE
The preferred publication of leading green professionals.
Quick Look
- Traditional clay pavers in 15 colors and 19 sizes
- Firebrick in 23 sizes
- Custom-blending available
Exactly what they sound like, permeable clay pavers have larger spacing lugs that allow water to pass through the joints—mimicking how water is absorbed naturally into the land to slow runoff. Without them, the NextGen Homes development would likely not even exist.
At the start of the development’s planning process, green|spaces learned they would need to include a retention pond. But the project’s location—on the side of a hill—made such a task impossible. “It would have been a deal breaker,” Walton says. Fortunately, the design team had already decided to install permeable pavers in the homes’ driveways, so the project became possible without installing a pond. “Having (the pavers) in the project from the beginning really helped us clear some of those hurdles as quickly as possible.”
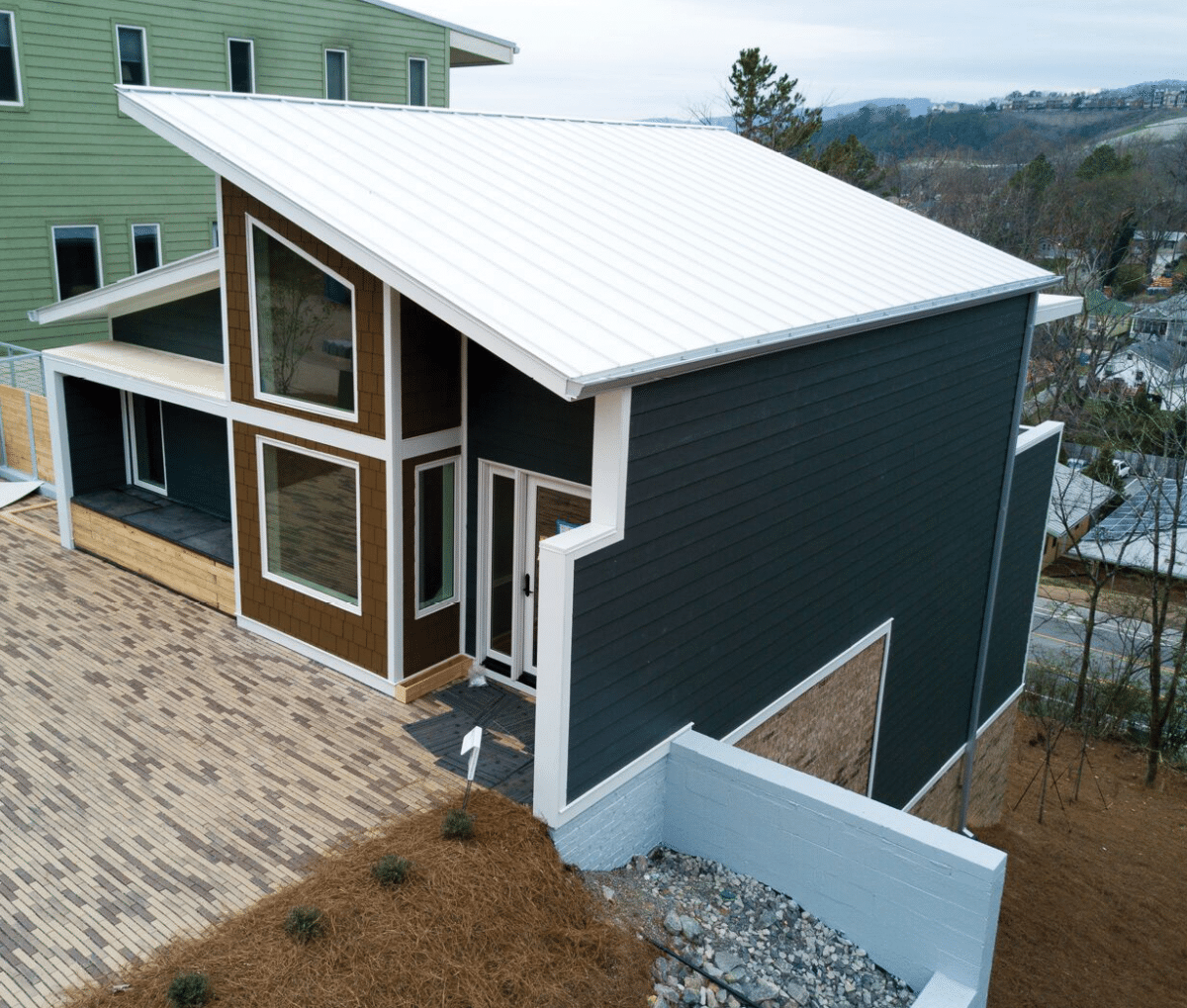
[Photo: Courtesy of Whitacre Greer]
Functionality & High Design
Water runoff is a big problem with any construction, causing most projects to require some kind of retention pond. But ponds aren’t always ideal and can lead to problems with mosquitos and an increased risk of disease. By using permeable pavers, the water goes back into the ground and impurities are filtered out naturally through the stone layers. “This allows the end user to decide where the water goes, and it is safer than sitting in a pond,” says Chris Kaboth, president of Whitacre Greer.
Whitacre Greer’s popular boardwalk pavers can withstand 1,300 inches of water per hour, while the smaller, traditionally sized pavers can withstand 970 inches of water per hour. Unlike traditional brick, which uses sand in the joints, #9 stone is used in the installation of permeable pavers—creating a natural water filtration system.
“Bricks and sustainability go hand-in-hand with each other.”
—
Chris Kaboth, Whitacre Greer
The pavers have durability on their side, too. “Bricks and sustainability go hand-in-hand with each other,” Kaboth says. “The largest road in the world was Appian Way (made of brick), and it still stands to this day. If we do our job and manufacture bricks correctly, they can last 150 to 200 years at least with the right installation.”
The pavers come in two designs, allowing architects and customers to design whatever they want, as well. “They can let their mind and their design run wild,” Kaboth says.
The boardwalk-style pavers—which have a long, thin design—used in the NextGen Homes project are frequently a point of praise from onlookers and homeowners alike. “It is one of the things people always comment on,” Walton says. The aesthetic value allowed green|spaces to sell the homes—which have no garage or carport space—at a higher price point. “We wouldn’t have been able to do that if we were using asphalt pavement. Using the pavers made it OK that we did not offer a garage.”
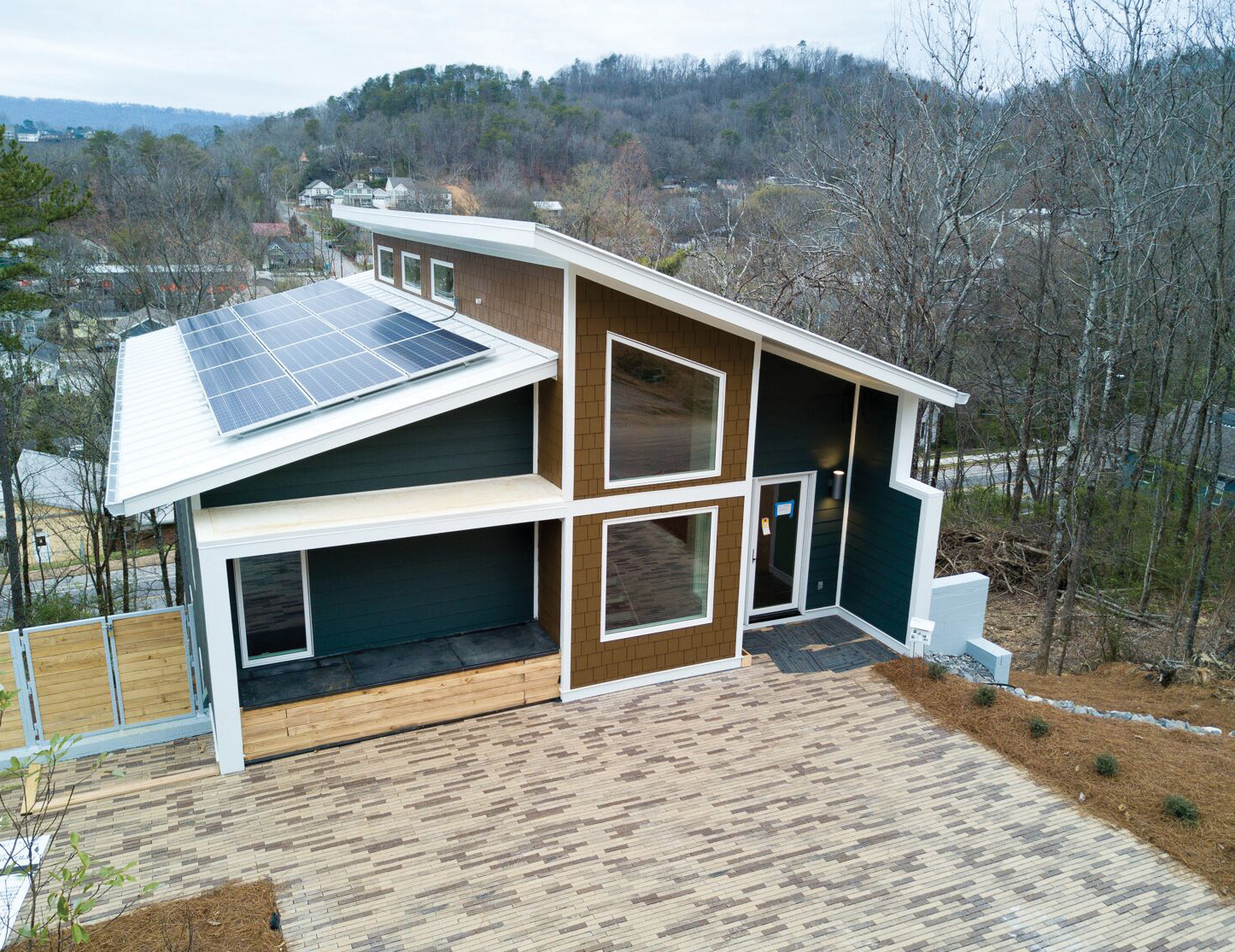
[Photo: Courtesy of Whitacre Greer]
All in the Family
Whitacre Greer—located in Alliance, Ohio—is not the only company that produces permeable brick pavers, but they were one of the first. The family-owned manufacturer of fired-clay paving brick and firebrick is now in its 101st year of operation. Kaboth is the fifth generation to lead the charge. “It has always been a point of pride,” he says.
The company decided to create a permeable brick paver in response to the growing emphasis on LEED credits in the brick industry, and the decision has paid off. “As we received more inquiries at trade shows, we came up with the design and got them to run quickly,” Kaboth says. Feeling the push to be more sustainable as an industry, the company has been working to transform its current location—purchased in the 1970s—“away from the 1950s and closer to the 2000s.” They continue to add more environmental controls, including dust collectors to cut down on dust from brick production, and have renovated their kiln to become more energy-efficient. The updated kiln uses half the natural gas as the old kiln.
Whitacre Greer is one of two U.S. manufacturers to use the dry-pressed process to form all products and fire them in natural gas-burning kilns. The company started using the dry press method in the 1990s to create a smoother finish on their brick. All products are produced using raw materials extracted in Northeastern Ohio.
Dry-Pressed Manufacturing
Dry-pressed manufacturing of brick used to be common, but now only a handful of structural clay manufacturers utilize this production technique—and Whitacre Greer is one of them. The process creates a more dimensionally- stable product than the commonly used extruded manufacturing process, says Kaboth.
Dry-pressed brick contains 6-8% moisture, whereas extruded brick contains 16- 18%. Less moisture means less shrinkage and deformation of the brick. Dry-pressed brick withstands multiple freeze and thaw cycles better than its counterparts, too, Kaboth says.
The process begins with mechanical presses— producing two to four bricks with each stroke. The presses use steel molds and a vacuum system that extracts air from the molds so the materials can be pressed tightly together. The pressed, unfired brick is then inspected for any irregularities and transferred to the kiln. In the kiln, the bricks are fired at 2,000 degrees Fahrenheit. During the firing process, a thermo-physical change takes place in the material creating strong, beautifully colored brick.
Learn more about Whitacre Greer and see more gb&d permeable pavers stories.