Story at a glance:
- For centuries all-natural terra-cotta’s adaptability and durability has made it an attractive building material.
- Ludowici can customize terra-cotta, creating profiles to mimic those on historic buildings or making an architect’s unique color choice a reality.
David Jensen never gets bored. As color consultant for Ludowici, Jensen develops new colors, coordinates samples, and oversees the production process for the company’s glazes to ensure they meet quality standards. Since 1888 Ludowici has been creating architectural terra-cotta for roofing, cladding, and flooring from clay and water. And, just as in 1888, Jensen says production still is very hands-on.
“Every tile is still handled by people. They’re still sprayed by people. They’re still set on carts and transported by people,” he says. “There are textures, in particular, that involve very hands-on processes, like hand slushed, for example. It’s exactly what the name implies—sliding a wet clay slurry on the tile to give it this rough, Old World texture that makes it look like it was made 100 years ago.”
How It’s Made
- Photo courtesy of Ludowici
- Photo courtesy of Ludowici
Jensen likens the Ludowici team to potters in their studio, mixing the ratio of stains and oxides to create a glaze with a mixer, not unlike a kitchen mixer.
“We’ll then spray small clay chips with the glaze we’re considering. I’ll use a spectrophotometer, or color meter, to read the glaze. I’ll then assign a numeric value to the color and will compare that to the set standards we have for each glaze and determine how close it falls to our standards or if I need to make further adjustments,” he says. “Once we like the color we’ll repeat the process at a much larger scale, using larger mixers and giant tanks to hold the liquid and glaze. We’re working in the realm of 1,600 pounds of material—not including water.”
Ludowici offers matte and gloss glazes, which are chemically adhered to the tile itself. “I always stress these glazes are, in many ways, a part of the tile,” Jensen says. “These are coatings we apply before the tiles are fired. By the time they come out of the kiln at temperatures up to 2100 degrees Fahrenheit, the glaze is chemically adhered to the clay surface. It won’t peel or separate.”
The Looks
Ludowici has 58 standard colors, but Jensen’s team can customize these colors to make them unique. “We can add top sprays; we can adjust those top sprays; we can spray certain colors certain ways,” Jensen says. “The limitations are only what you can imagine, rather than what we can do.”
If a designer is looking for a custom color, sending Jensen a visual reference is a good start. “Color is something everybody sees differently. The way one person describes what they’re aiming for could be entirely different from what another person would describe, even if they’re talking about the same idea.”
Once Jensen completes samples of the glaze the tiles are sent to the designer to be viewed in their lighting situation and so the designer can have a tactile experience with the product.
In addition to customizing terra-cotta’s color, Ludowici’s team can adjust the surface texture. “We can weather a tile, which is basically sandblasting the clay tile before it’s glazed and fired, giving it this very rough texture. Then the glaze goes on, so it can help the tile look aged and weathered without sacrificing the durability,” Jensen says.
Endless Possibilities

Photo courtesy of Ludowici
Customizing tiles to match profiles on a historic building is one of the company’s specialties. For example, tiles can be scored, which makes them look like wood shakes. Jensen is especially proud of terra-cotta roofs in Colonial Williamsburg, Virginia, that are difficult to distinguish from their wood-shingle counterparts.
“Colors and textures typically are driven by the needs of our projects,” Jensen says. “We have an incoming sample process for matching historic tile, so we’re receiving new tile every day. Sometimes it can be a very simple match—a tile we made 100 years ago. Other times it will be a tile made by a company that existed for two years in the 1920s and completed only two houses with its own profile and colors. In that case it’s a much more complex matching process, but it is fun developing new colors and textures to match the surface.”
The firing process that chemically melds the glaze to the clay also builds fire resistance and durability into the tiles. In addition, all Ludowici tile is ASTM C1167 Grade 1–certified, meaning it conforms to specified values of durability, freezing and thawing, transverse breaking strength, efflorescence, reactive particulates, and permeability.
Incredible Strength
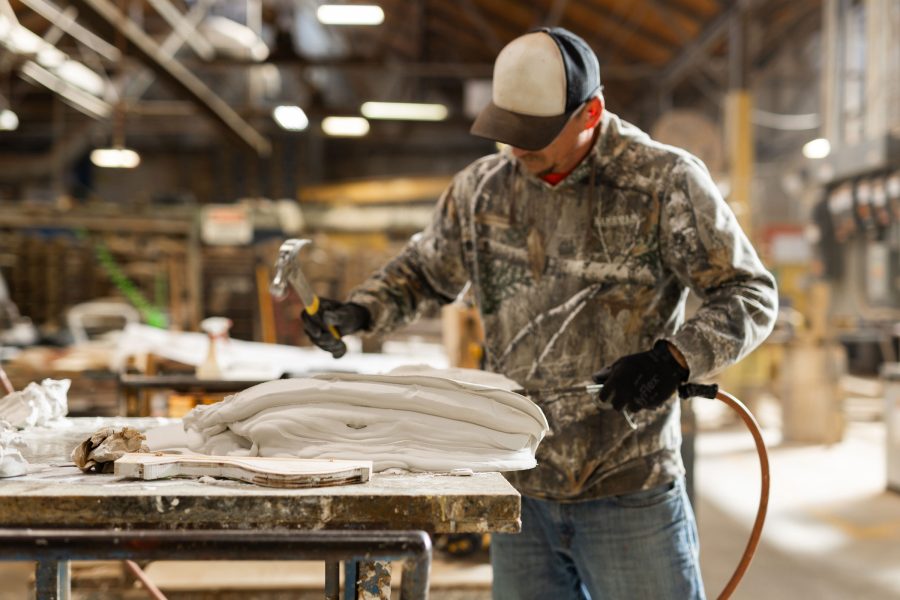
Photo courtesy of Ludowici
Because of terra-cotta’s durability Ludowici offers a 75-year warranty, but Jensen says he has seen roofs much older than 75 years still in great condition. “It’s more likely you’ll have to replace the underlayment and substructure than the tiles,” he says. “Now we’re getting to the point where tiles made 130 years ago still are serving very well. The longer we go the more we see tiles keep surviving.”
As more architects and building professionals discover terra-cotta’s innate durability and the many ways it can be customized for building projects, the material is enjoying renewed interest. “I’ve been seeing more appreciation for terra-cotta, and I’m really excited to see where it goes,” Jensen says. “Working with terra-cotta keeps my life interesting. I never know what’s going to come up each day. And it’s neat to be able to work on amazing projects, playing a role in making the color for them.”