Fabcon goes head-to-head with other construction methods.
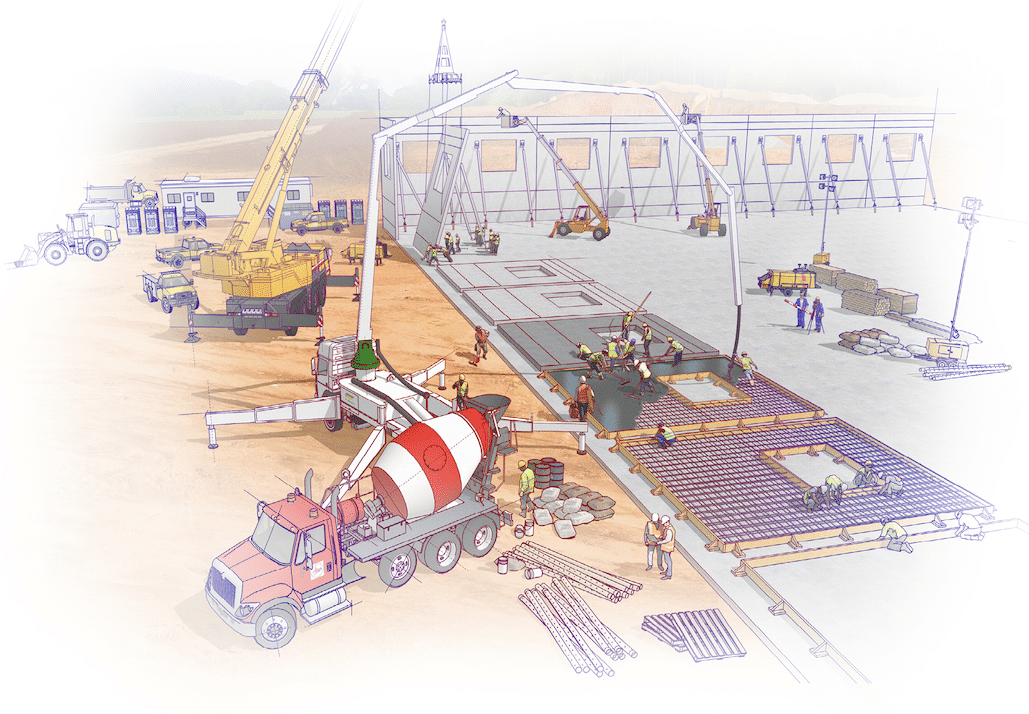
Site-cast projects pour their panels on-site and in the open. They require much larger crews and are generally on the jobsite for longer periods of time. [Illustration: Courtesy of Fabcon]
Whether site-cast, masonry, or pre-engineered steel construction, Fabcon Precast is taking it on as part of their new VERSUS campaign. “We are trying to be as objective as possible while outlining the advantages of any structural insulated precast concrete panel,” says Tom Ostrom, owner of Ostrom Creative and manager of the campaign.
Launched in June 2018, the campaign—coupled with a continuing education course—is designed to clear up any confusion surrounding precast and how it works. One common area of contention is the use of the phrase “tilt-up,” which is frequently used to refer to both precast and site-cast panels, giving the idea that the two are the same when, in fact, they have many significant discrepancies. “Both precast and site-cast projects have a point in the process where the wall panels are literally tilted into place by cranes. To the untrained eye it might seem like the technologies are identical, but the two construction methods are very different,” Ostrom says.
Fabcon understands precast may not always be right for every project. The main idea behind VERSUS, though, is to start a conversation. “You don’t know what you don’t know. We aren’t trying to be everything to everyone,” says Jim Houtman, vice president of sales and marketing at Fabcon. “It is really about educating the consumer. By furthering the conversation, people will have a better grasp of all their options.”
Right now, availability is the biggest concern Houtman hears from consumers. Precast is gaining in popularity and, as a result, sometimes demand exceeds supply. It’s just another in the list of reasons why the campaign is important. “Start the conversation early. Include your precast provider in the early discussions and the design process so you aren’t scrambling at the end,” he says.
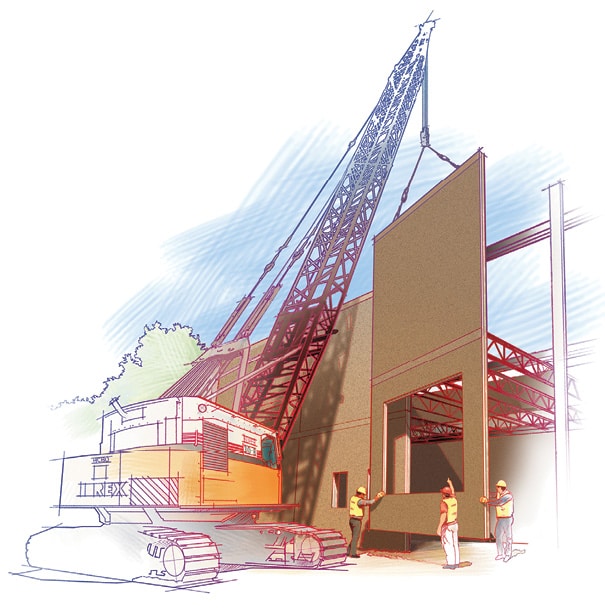
Both precast and site-cast panels are lifted into place by cranes, but they are very different products. [Illustration: Courtesy of Fabcon]
Precast Vs. Site-Cast
Precast panels offer a number of benefits over those built on-site. Precast panels are produced in a climate-controlled factory environment to ensure consistency and eliminate weather delays and environmental inconsistencies. Then they are transported to the job site and organized to be easily tilted into place with a small crew, resulting in less job site disruption and crew cost.
Site-cast panels lack the integral insulation precast offers. Precast panels have insulation sandwiched into the panel. Fabcon’s VersaCore+Green delivers insulation values ranging from R-13.6 to R-28.2. Insulation on a site-cast panel is added after install and usually requires a separate crew to fur out the surface and glue or tack the insulation to the interior.
Height can become a concern with site-cast panels, too. Anything exceeding 40 feet can pose engineering challenges and result in additional labor and equipment. Precast panels can be built greater than 73 feet. The factory environment also allows precast panels to come in a variety of finish options, giving them versatility and unique design quality that’s difficult to achieve with site-cast panels.
Higher LEED ratings can be more easily achieved with the use of precast panels made from 58% post-consumer recycled content. The panels have a long life and are durable and energy-efficient. They can also be repurposed in situations where renovations require changes to the structure.
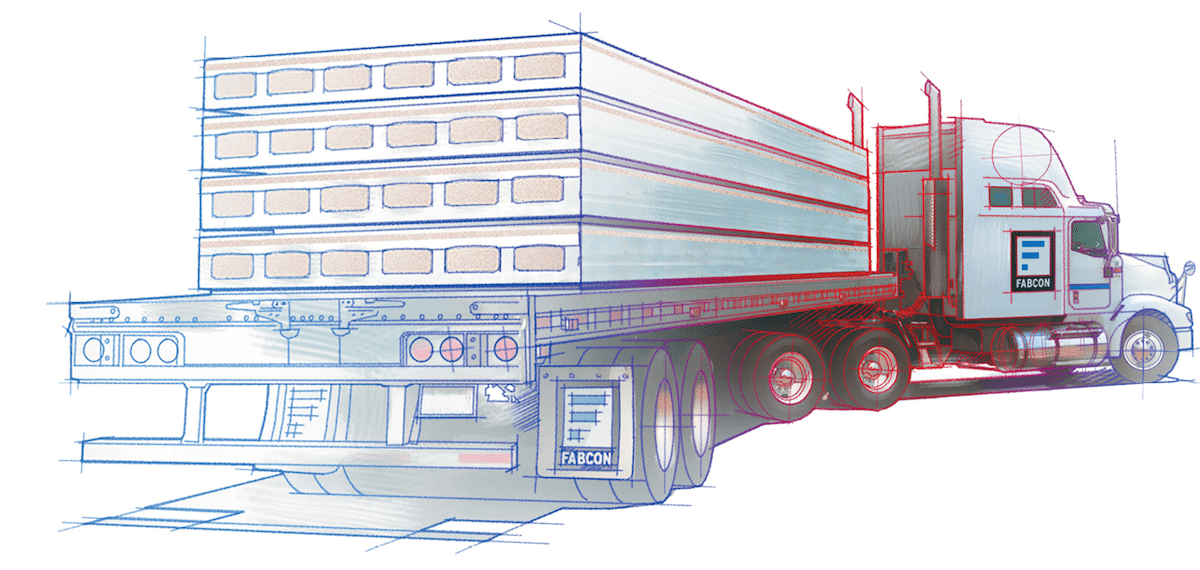
Fabcon manufactures panels even before the site is ready. Once footings are poured, trucks deliver the panels in sequential order. [Illustration: Courtesy of Fabcon]
Precast Vs. Masonry
Masonry is labor intensive. It requires a lot of workers, time in the elements, and can be hard on your hands and health. “There are not a lot of young people wanting to do it,” Houtman says. “It’s hard to find enough people to get the job done.”
It’s also disruptive to the job site, making it difficult for other work on the project to continue while masonry is being completed. It often leaves the job site torn up and contributes to substantial waste and debris. “It is an expensive system and is much less energy-efficient than precast,” Houtman says. Masonry is also permeable to the air, contributing to a lower quality internal environment and lack of vapor tightness—problems that will need to be dealt with in other ways.
It’s difficult to build high with masonry due to concerns with weight and the need for more structural components. More personnel risk and cost for scaffolding is associated with taller buildings. “We can do a better building faster with less money and manpower,” Houtman says.
That being said, Houtman agrees masonry is great for a single-story office with lots of entrances. “We don’t do really great with short offices, and they don’t do really well with a taller warehouse,” he says. Fabcon frequently tells clients to “save the brick, stone, and block for dressing up entryways and use precast on the main structure,” he says.
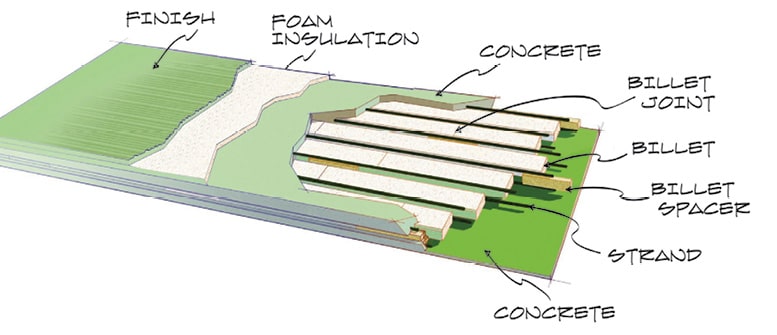
Fabcon structural precast sandwich panels provide thermal performance ratings as high as R-28.2 and can be produced to heights up to 73 feet. [Illustration: Courtesy of Fabcon]
Precast Vs. Pre-Engineered Steel
Pre-engineered steel is great for enclosing bulk spaces with little requirements. It’s cheap compared to other means of construction, but, as Houtman says, “It’s also a cheap building.” Metal buildings lack durability and don’t age well. “It is a disposable building with a relatively short life,” he says. “You can have one that is six months old but employees bump into the side and put wrinkles and dings in it and it looks pretty shabby.”
Metal structures have lots of connections that compromise energy efficiency, and structural compression leads to low insulation value. Metal itself is a lightweight material that’s highly susceptible to damage from wind and other environmental factors. Fires can be devastating to steel—unlike precast panels—making it difficult to get good fire ratings.
Chemicals and food-production environments can be hostile to steel, which is highly corrosive. “Those are two huge industry segments where metal buildings don’t work,” Houtman says. “Precast doesn’t rust and is much easier to keep clean.”