Story at a glance:
- We explore five ways press technology differs from traditional methods.
- Press technology is growing in popularity in the US and has long been popular in Europe.
Press fittings are a quick and simplified alternative to traditional methods like welding, threading, and soldering.
Press technology describes the method of joining pipe together with a metal press fitting that is crimped onto the tube or pipe with a special tool.
This capability—which leaders at Viega say is more efficient, safer, and faster than traditional methods—has long existed, but now you can do more with it than ever before.
“A lot of people are embracing it. In Europe it’s been around longer than the US. In Europe they’re about 80 to 85% press versus traditional. Here in America we are 20 to 25% press versus traditional,” says Colton Henkowski, a Viega technical training consultant who trains contractors, engineers, and wholesale reps through in-person and online workshops. “Tons of people use it. Huge companies also use it, amd hospitals use it. There are press fittings in the Pentagon and in a lot of really important places you may not necessarily see.”
Viega’s popularity and market share is continually increasing year over year,, though not everyone knows the value of press technology just yet, Henkowski says. Viega’s most powerful systems are ProPress and MegaPress. ProPress is available in sizes of one-half-inch to four inches and can be used on potable water, heating and cooling glycol lines, and even compressed air. MegaPress is available up to four inches and is made for black iron, carbon steel pipe, and stainless steel pipe systems.
Here are five ways press technology differs from traditional methods.
1. It saves time.
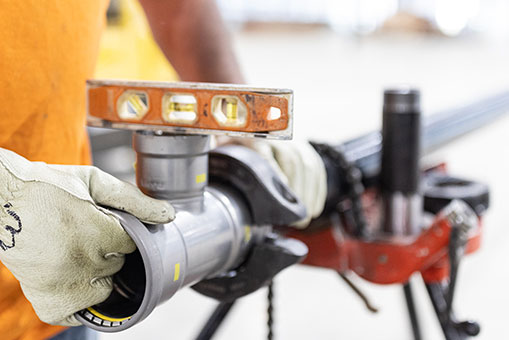
MegaPressG fitting for gas applications. Photo courtesy of Viega
Pressing allows you to finish your job in a fraction of the time so you’re onto the next jobsite sooner. Traditional methods—including welding—require a lot more time and tools. “The big difference is your time on and off the job,” Henkowski says. “I can walk into a ProPress or MegaPress job with one set of tools versus having to source things like a torch, a welder, a threader, threading oil. It really is just that efficiency factor that sets us apart from traditional.”
Saving time often means saving money, too. “We want to speed up people’s project timelines,” Henkowski says. “That not only saves money but with a decreasing workforce and less people doing the jobs we have to be able to do more per person per day.”
2. It is safer.
Henkowski has seen many of the dangers of traditional welding and other skills in the field up-close. He worked as a pipefitter for 15 years and has more than a dozen welding certifications. He says working with Viega’s solutions like ProPress and MegaPress is much safer. Much of his work before joining Viega involved welding.
“It was a dangerous process—not only dangerous to me but also dangerous to the building,” he says. “When you’re working inside a building and you have to create connections using flame, you have to shut down the system, and the majority of the time you need to fire-watch onsite.”
3. It is more reliable.
Traditional methods like soldering have many factors that can lead to inconsistencies during installation. “Even if you’re really good at it, there’s always that human or environmental error. With press fittings like ProPress the prep and install is the same every single time,” Henkowski says.
Viega offers the same consistent press every time, with an incredibly low failure rate. “Less than one in a million of our fittings don’t do exactly what they’re supposed to do. If you want to go out and have a job done right the first time, this is your best bet.”
4. It is easy to learn.
- Viega in-person training. Photo courtesy of Viega
- Demonstration of durability of MegaPress fitting. Photo courtesy of Viega
Henkowski says contractors with a background in plumbing or pipefitting can learn how to install ProPress and MegaPress fittings within an hour or so. “I could have them trained on all three Viega systems for installation. Of course, to understand every last bit and the multiple approved applications takes a little bit more time, but the training itself is a whole lot simpler. Think about it; it took me about 13 years to get all the different welding certifications I have, and I can train somebody in an hour to learn how to do MegaPress correctly.”
Viega is dedicated to offering quality training and supporting the trade, pushing people to learn a new skill that may ultimately make their lives easier. The company also does a lot of workforce development, providing education through programs like VTEN—the Viega Trade Education Network that works with trade and vocational schools to show young people that there are other career options out there.
5. It can be used most anywhere.
Anywhere a pipe is going into a building, Viega’s press technology should be there, Henkowski says. “We can do everything from your domestic water to deionized water to natural gas in someone’s house. We can do biodiesel at an industrial facility. There’s a ton of applications.”
Viega’s press technology is even more durable than other systems, Henkowski says. “More than anything to us it’s about helping people understand that our product is as durable and just as long-lasting
Henkowski says it’s because, sometimes, old habits die hard. “We’re old-school construction workers. ‘My dad taught me how to weld. I’m going to weld until the day I die,’” he laughs. “Even me—all I ever knew was one way of doing things.”
When he first saw ProPress, he was taken aback. “At first I was one of those guys, too. I was like no way. It took a lot of me working with it before I realized: Here’s a really cool product that does exactly what I want it to do every time.”
Viega never stops innovating. The company is currently focused on continuing to develop new products and accessories, including fittings for refrigeration. “We have more than 17,000 different products,” Henkowski says. “We have things like valves, balancing valves, ways to direct your flow in different ways, unions, all these different things. We continue to push further so we have everything that anyone could ever need.”