Story at a glance:
- Architects at Gensler are leading the conversation around designing for fire safety.
- Westcoat’s fire-rated waterproofing systems are another tool that can help prevent the spread of wildfires.
It might be nearly impossible, or at least cost prohibitive, for most people to live in homes that can withstand something like wildfire. But given the increase in fires in recent years, architects are talking more about how they as designers can buy people time to get out and reach safety during such an event.
“Prevention on a large scale is something we can do on every project,” says Gail Napell, a global design resilience leader at Gensler. Napell is based in California, where so much devastation from fire has happened in recent years.
Data from the EPA shows that not only are wildfires on the rise, but the extent of area burned by wildfires each year appears to have increased since the 1980s. Fire-related threats are increasing as more people live in and around forests, grasslands, and other natural areas. Between 1980 and 2021 the US had 20 wildfire events that caused more than $1 billion in damage, according to the National Oceanic and Atmospheric Administration. Of those, 16 have occurred since 2000.
Fire Suppression
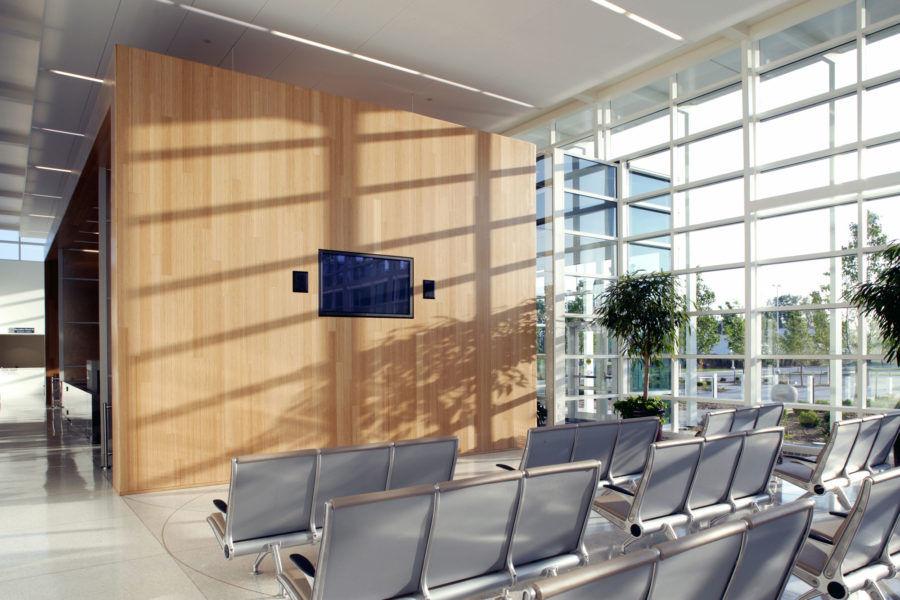
Inside the Gensler-designed Department of Homeland Security offices in Omaha. Photo courtesy of Kessler
Architects are looking at how they can be even more proactive in design to help keep people safe. For starters, they can design and build buildings that use noncombustible materials with combustion-prone features on exteriors, advises the Building America Solution Center, a resource of the US Department of Energy’s Technologies Office.
Even in areas where homes are in close proximity, structures can survive wildfires if the house is made using fire-resistant roofing, siding, and windows with enclosed soffits and decks and minimal vegetation near the building, according to the Building America Solution Center.
Napell has spent much of her career specializing in resilient projects, even before her time at Gensler. In residential design she says being proactive against wildfire damage includes needing to clear the wildfire area away from the building and keep flammable brush at least 30 feet away from the structure—and 100 feet in rural areas.
“Because of the scale of wildfires they create their own weather. You don’t want the fire to get to the building to begin with,” she says. Some projects Napell has worked on in the past also expected homeowners to have their own fire suppression systems—be it a rainwater collection tank, stream, pond, or other way access to water to fight a fire. As for construction, she says the goal should be to design with nonflammable siding and roofing—using materials like metal, seismically safe stone, or Class A roofing.
Then, she says any paths for fire to get into the building—think louvers or chimney vents—should have not only spark arresters, but a fine mesh like steel wool behind them to keep sparks from entering the building, or intumescent paint that swells up and blocks the fire’s path.
Napell says codes increasingly tend to discourage construction and rebuilding in wildfire zones because of the challenges. Gensler is also starting to see more RFPs in which clients are inquiring about robust backup power for grid outages in California.
It may not be that architects can design entirely “fire-proof” buildings, but they should look to suppress fire. “You’re creating an opportunity for those in the building to safely get out,” says Rives Taylor, Gensler’s director of design resilience, based in Texas. “You’re not necessarily seeking to save the structure.”
Taylor says suppression needs to occur with things like roof and deck coatings and moving ground cover and even cars away from a building. “If a fire is moving fast enough, the cars in a parking lot or parking garage can be an issue. In major buildings it tends to be about clearance, and it also tends to be a big investment in fire suppression of a campus,” he says. In some parts of the country Gensler has seen requirements for buildings to have large standby water tanks that can be used both for emergency water needs in case a water main breaks or in the event of a fire.
Air Quality & Changing Tech
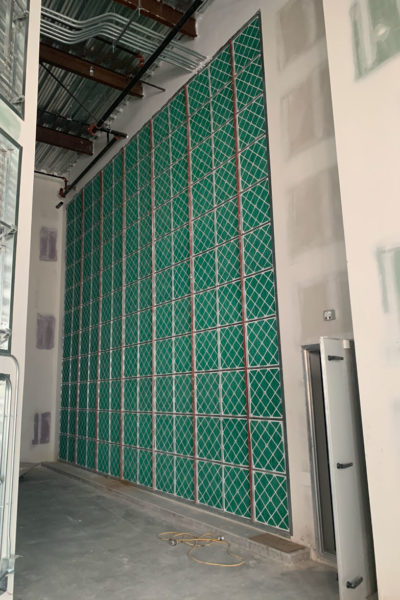
Gensler’s Gail Napell calls the MERV 13 filter one of the “unsung heroes” of wildfire preparedness. The filter is seen here at a commercial office building in San Francisco. Photo by Aaron Baumbach
Taylor says small choices can add up to making a huge difference. “You could be downwind from a fire, so we’re looking at the implications of closing buildings off in terms of their mechanical systems, ventilation, and recirculating air and finding ways to meet oxygen levels without opening up the building. We’re seeing the whole issue of fresh air really have a need for more investigation.” In the Texas office he says they’ve learned how smoke is full of problematic particulates. “We have to rethink the fresh air exchange in our large buildings.”
Napell agrees. She says a change to the California mechanical code a few years ago actually made her sad, as it was an honest acknowledgement of the future. The new code requires that every new building or building undergoing a major remodel—including individual family homes—must be capable of being shut tight and mechanically ventilated. This is because of the dangers of wildfire smoke.
“All new buildings have to have that level of ventilation—and mechanical ventilation. It’s a weird thing for those of us who spent much of our lives trying to figure out how to increase the amount of natural air through a building and reduce the amount of power. It takes more power to force air through a MERV 13 filter, which is now the minimum required in California, in order to make sure you’re getting those the worst of the particulates out. So it’s only amped up the need to design energy-efficient buildings.”
She calls the MERV 13 filter one of the “unsung heroes” of wildfire preparedness. “This is how we continue to breathe fresh air,” she says. “We’ve had some wildfires that were literally weeks long here in California. For six weeks you really couldn’t safely go running. It could be harmful to your lungs.”
Exit codes are another area that need to be revisited, Napell says. “The simple reality of exit codes that help us design in such a way that people always have at least two choices of a way to get out of the building, whether it’s a wildfire or earthquake or something else.”
It really takes a collective team effort to design any good design.”
As wildfires are seen in various geographies, Taylor says communities have to think about how fires react differently when they’re in an open prairie versus dense forest, for example. Both can move quickly, but combustion is different. “Gensler, like many good design firms, talks about the integrated design approach,” he says, pointing to the need for everyone from architects and designers to civil engineers and landscape architects and firefighters to collaborate. “It really takes a collective team effort to design any good design.”
Teams also have to be flexible, as what works now may not work in the future, as populations are in flux, droughts come and go, and even technology like that of drones changes. “The drones represent a very interesting opportunity,” Taylor says. He wonders: Could they carry water to hard to access places to suppress fire?
Napell says California has long prioritized fire-resistant materials, given the state’s propensity for earthquakes. Many architects use concrete, perhaps too much, she says, for its resistance to fire. “We love concrete, but we’re beginning to understand the embodied carbon impact of it,” she says. Cement or gypsum board are also helpful for exteriors, she says, and mass timber is particularly exciting. “It is not necessarily an issue for fire if you use it the right way because it does have that tendency to create its own protective char.” The hope is that that char on the outside of a mass timber structure will massively slow the fire impact to the inner part of the timber—similar to what happens when you put fire-resistant coatings on steel, Napell says.
Coatings
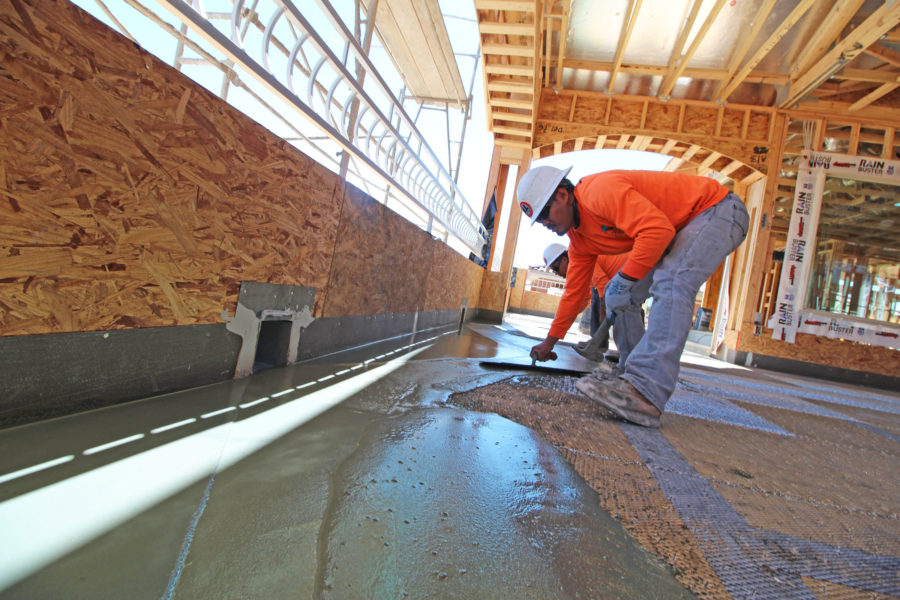
The ALX base coat mixture from Westcoat provides the bulk of the fire resistance when applied to a plywood surface. “It’s a very durable waterproof mixture that is troweled in,” says Todd Cook, product manager at Westcoat. Photo courtesy of Westcoat
Napell says there are also fire-resistant treatments you can put on wood—typically wood finishes or coatings. Westcoat Specialty Coating Systems has been manufacturing deck coatings for more than 30 years, with systems installed all over North America. The manufacturer focuses on resinous flooring—think epoxies and urethanes—and also makes concrete stains, sealers, and cementitious overlays. Exterior waterproof decking has been one of their biggest focus areas lately. Their fire-rated waterproofing systems are another tool that can help prevent the spread of wildfires.
Westcoat’s ALX and ALX Pro Systems can be applied on projects that use a plywood substrate, be it a new build or retrofit. Both are WUI-certified. WUI, or the Wildland Urban Interface, has codes and standards that fall under California Building Code and California Residential Code concerning the construction of buildings in wildfire-prone areas.
“As we build closer and closer to forest areas or areas where there are fires, we’re seeing these [wildfire] maps change,” says Todd Cook, product manager at Westcoat Specialty Coatings Systems. “We want to make sure we’ve tested to these requirements.”
What is ALX?
Westcoat’s ALX and ALX Pro systems comply with the ASTM E 2632—a standard test method for evaluating the under-deck fire test response of deck materials—and ASTM E 2726, the standard for evaluating the fire-test response of deck structures to burning brands. They also have third-party testing that exceeds these standards, Cook says.
The ALX waterproofing system is formulated for plywood surfaces—already a riskier material when it comes to fire concern. One way to reduce the risk is with waterproofing, Cook says. The ALX waterproof system integrates the finest acrylic resins and cement blends into a reinforced, galvanized metal lath. ALX eliminates plywood seams and is ideal for use in heavy traffic areas. ALX and ALX Pro also meet the Class A Fire Test ASTM E-108 and the One-Hour Fire Rating ASTM E-119.
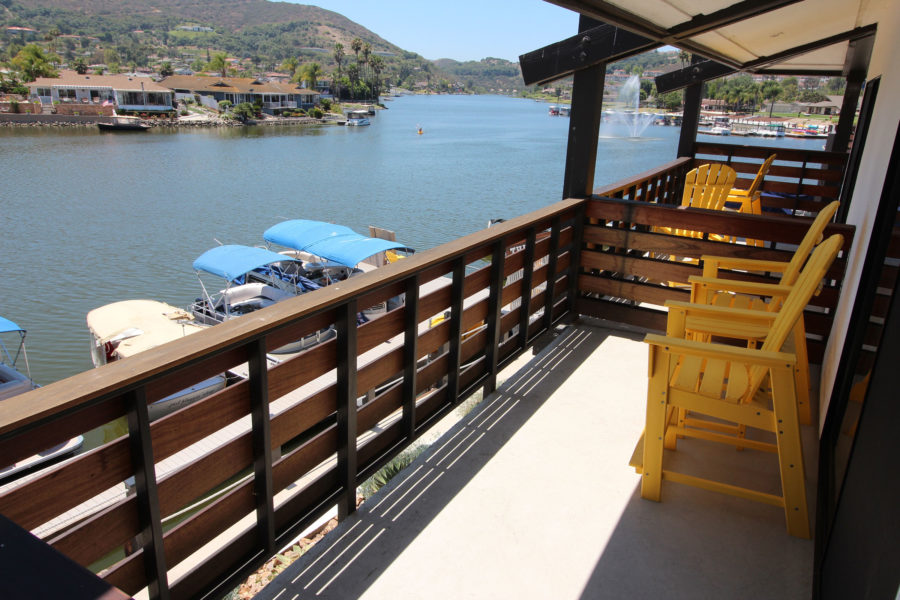
Formulated for plywood surfaces, the ALX system integrates acrylic resins and cement blends into a reinforced, galvanized metal lath. Transform a wood subfloor to a decorative concrete or epoxy finish with ALX Underlayment system; it’s a blank slate for installing tile, epoxy, or other decorative flooring options. Westcoat is one of the only manufacturers of a metal lath system that offers a 20-year warranty. Photo courtesy of Westcoat
“We can come in and rehab a walking surface like a deck or roof deck without seams, without having extensive tear-offs or full demolition,” Cook says. “Our decking systems are a lot easier to troubleshoot because we’re not under concrete or tile. You can walk onto the deck surface. This allows for a better service life and makes for a more durable system long-term.”
Westcoat’s low-VOC products are also safe for the environment and for applicators, and they can help projects earn LEED points. They also offer a wide range of aesthetics to make specifying their solutions even easier. If an architect wants a cohesive look from interior to exterior, Westcoat can make that happen.
“We have a very wide range of materials that can be used to create the look of concrete or tile with color palettes and stains and sealers that can be used to create any aesthetic. In most cases, we can almost replicate any finish.” Recently Westcoat has also seen more demand for solar reflective finishes to help reduce the urban heat island effect and lower surface temperatures for inhabitants.
Westcoat works with city officials, city planners, contractors, and architects alike to make sure waterproofing is done correctly through their Qualified Contractor Applicator program. They also offer many training videos and seminars for architects and other building professionals.