Story at a glance:
- Superior fade performance is a top attribute of PVDF-based NeverFade coatings.
- PVDF-based NeverFade coatings also provide the benefits of reduced cleaning and maintenance.
- PVDF’s incredibly strong carbon-fluorine bonds stand up to film erosion, even under exposure to the elements
For decades, architects, project specifiers, and building owners have trusted polyvinylidene fluoride (PVDF)–based finishes to protect the color integrity of building materials. Whether applied in the factory or the field, PVDF-based coatings have proven their long-term fade resistance, even with the darkest, boldest colors and in the sunniest and harshest conditions.
One example of a PVDF-based, field-applied coating with superior fade resistance is the line of NeverFade Facade Restoration Coatings from APV Engineered Coatings. These coatings contain Kynar Aquatec—a water-based PVDF resin similar to the solvent-based Kynar 500 used by building material OEMs for more than 55 years.
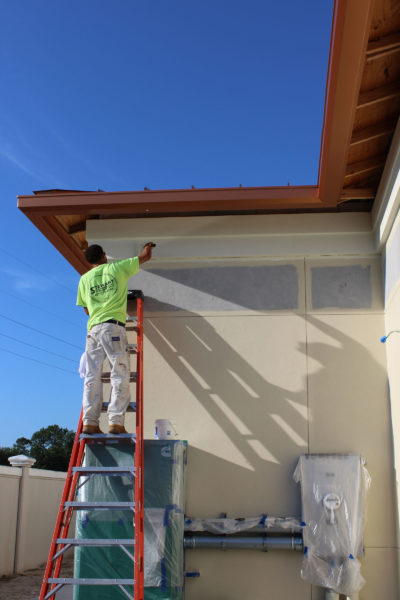
Photo courtesy of Arkema
Kynar Aquatec resin-based coatings have consistently demonstrated an ability to resist fading (Delta E < 5) for 20 years or more in high UV settings like southern Florida. They can be applied easily to a variety of substrates—including metals, plastics, wood, concrete, stucco, EIFS, and previously painted surfaces, making them ideal for facade and roof restoration. Side-by-side southern Florida comparisons of Kynar 500 with Kynar Aquatec based coatings for the last 21 years show similar performance with respect to color fade and chalking.
In addition to superior fade performance, PVDF-based NeverFade coatings afford another benefit to building owners: reduced cleaning and maintenance. That is because the same properties that allow PVDF-based coatings to resist color fading also allow them to resist the dirt, bugs, mold, and mildew that can turn a vibrant building exterior into a maintenance-intensive eyesore.
Tough, Durable Finish
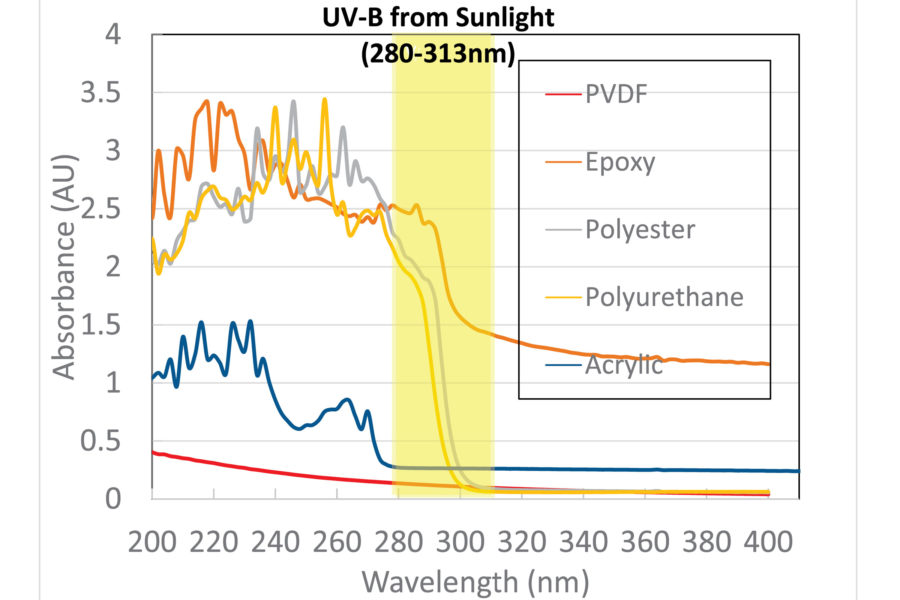
Chart courtesy of Arkema
Not all coatings provide long-term durability, even if they promote the product in that light. For example, premium acrylic latex binders in exterior paints break down over time when exposed to UV rays, humidity, windborne particles, chemical pollution, and other corrosive environmental elements—allowing dirt and bugs to stick to and ultimately infiltrate the coated surface.
While some exterior grade acrylic-based latex coatings may claim exceptional cleanability or hydrophobic properties, this performance may only last for a short period, especially in harsh environments. Over time the additives, pigment, and resin in these coatings break down, creating a chalky residue. This is primarily due to UV energy and environmental stressors. Eventually this chalked coating wears away from the substrate or is washed away by rain, wind, pressure washing, or cleaning until the coating film is gone and no longer protects the substrate—leaving it bare and open to further damage from the elements. The chalky residue changes the coating’s surface energy, and it serves as a food source for mold and mildew growth, which further degrades a building’s appearance and create cleaning and maintenance problems.
Coating systems formulated with Kynar Aquatec PVDF resin, on the other hand, resist photochemical degradation to maintain their original film thickness. PVDF’s incredibly strong carbon-fluorine bonds stand up to film erosion, even under exposure to the elements, allowing the resin’s protective and cleanability properties—including dirt shedding and mold/mildew resistance—to last significantly longer.
The figure above shows the extent to which UV energy breaks down common coating binders, reducing their mechanical protection properties. Note that PVDF resin has very minimal absorption of UV energy, making it ideal for coating applications needing strong UV resistance.
Surface Energy
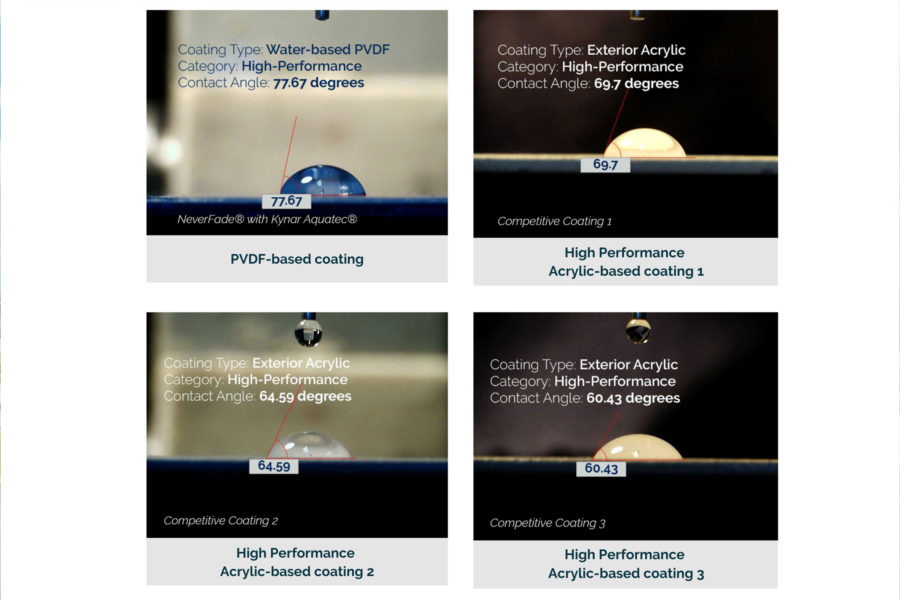
Image courtesy of APV Engineered Coatings
Chalking and coating film erosion impacts surface energy. For a baseline, think of the surface energy of cookware coated with a non-stick treatment. The inside of most cookware is coated, rigid, and nothing likes to stick to it. This surface is considered an ultra-low surface energy material with a high-water contact angle, which is how surface energy is measured in a lab.
In the case of NeverFade, the PVDF resin greatly contributes to the formula’s low surface energy properties in a cured state on the surface of a variety of building materials. One of the challenges from a chemistry standpoint is properly formulating the coating to completely wet out the surface. Proper wetting out provides continuous coverage of the paint film, adhesion, and optimum aesthetics as it is applied, and this must be accomplished through proprietary performance additives. As NeverFade dries and cures, the surface of the film adopts a much lower surface energy with a higher contact angle and excellent non-stick properties. The PVDF bond uniquely flexes throughout the coating’s life cycle, preventing the bonding of dirt and debris on the coating and causing contaminants to resist adhering to the surface instead of abrading it and degrading the coating film.
The images above show contact angles of coatings with various resin binders. In this laboratory test, a bead of water is dropped onto a coated surface and the angle between the bead of water and the coating film is measured with a goniometer. The greater the angle, the better the coating’s ability to resist penetration by water, dirt, and debris, and the easier it will be to clean.
To translate this laboratory testing into real-life performance, the figure below demonstrates the ability of a coating made with Kynar Aquatec resins to resist film erosion after outdoor exposure compared with a high-performance acrylic resin-based coating. Both formulations shown utilize cobalt blue pigment, which is one of the most lightfast of the blue pigments. Therefore, any degradation of the coating from weathering is related to the resin binder system only. After seven years of exposure in south Florida at 45-degree angle facing south, the acrylic resin-based coating demonstrates film erosion and significant fading, chalking, and degradation. The Kynar Aquatec–based coating is still intact with no film erosion and therefore, negligible fading and chalking, thus protecting the substrate for a much longer period of time.
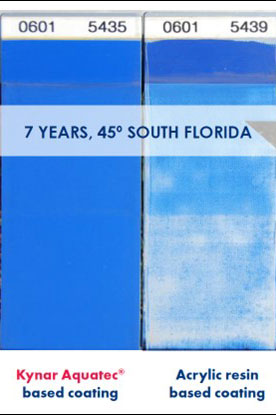
Image courtesy of Arkema
Reducing Environmental Impacts
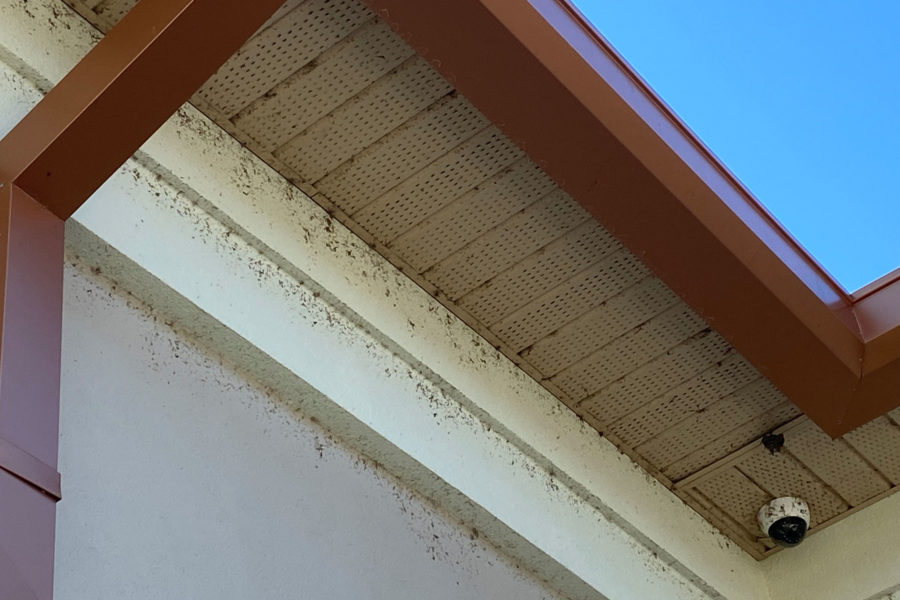
Photo courtesy of Arkema
The ability of PVDF-based coatings to resist dirt pickup, bugs, and mold/mildew growth can help building owners reduce their reliance on costly and resource-intensive exterior maintenance procedures like power washing, which consumes extra energy, water, and chemicals—the latter of which end up being released into the ground during the cleaning process.
While dirt, debris, and bugs may adhere to a PVDF-coated surface for a short time, once it rains, they typically wash right off. Consider the experience of one organization, whose new southern Florida stucco headquarters was coated with PVDF-based NeverFade. The building’s security lights regularly attracted the type of bugs that would normally adhere strongly to the surface of the building and require manual scrubbing or power washing to remove. But thanks to the PVDF-coated exterior, the bugs easily slough off the surface with just a light spray from a garden hose.
PVDF-based NeverFade Coatings also offer additional environmental benefits as well:
• Their dirt shedding and mold/mildew resistance properties help to reduce a building’s heat build-up and related energy consumption, as cleaner surfaces improve the solar reflectance of roof and façade materials.
• They can be applied at a much lower thickness than acrylic-based coatings, which need significantly higher thicknesses than PVDF-based coatings to offset film erosion over time. This reduces consumption of coating product, packaging, and related resources.
• The coatings’ Kynar Aquatec resin is manufactured through an innovative and patented process that uses no PFAS surfactants or any other fluorosurfactants in the manufacturing process, allowing building owners to maintain an environmentally responsible supply chain.
• Because they are formulated with ultra-low volatile organic compounds (VOCs), there are fewer nuisance odors that can be objectionable and disruptive to building occupants. In addition, they are one of very few high-performance coatings to meet strict South Coast Air Quality Management District (SCAQMD) Rule 1113 environmental regulations in California.
High-performance PVDF-based coatings provide more than just long-term fade resistance. They also reduce maintenance and environmental impacts. When specifying coatings for your next project, along with color fade resistance, be sure to evaluate the dirt pick-up performance of the options you’re considering.