In subtropical climates where buildings are regularly exposed to harsh UV rays, high heat, and humidity, even high-performance paints can quickly chalk, fade, and degrade—especially deep colors and brighter hues. Forward-thinking building owners and architects are seeing a significant impact in sustainability when shifting away from standard acrylics, urethanes, and polyester paints to engineered coating systems with polyvinylidene fluoride (PVDF) resin technology.
Coating systems formulated with PVDF resin deliver long-term performance other coatings can’t. PVDF is a tough, engineered thermoplastic polymer that, when used properly in a paint formulation, promotes excellent weatherability, color retention, and abrasion resistance. This is thanks to carbon-fluorine bonds that do not break down under exposure to the elements.
PVDF Coating Systems Features
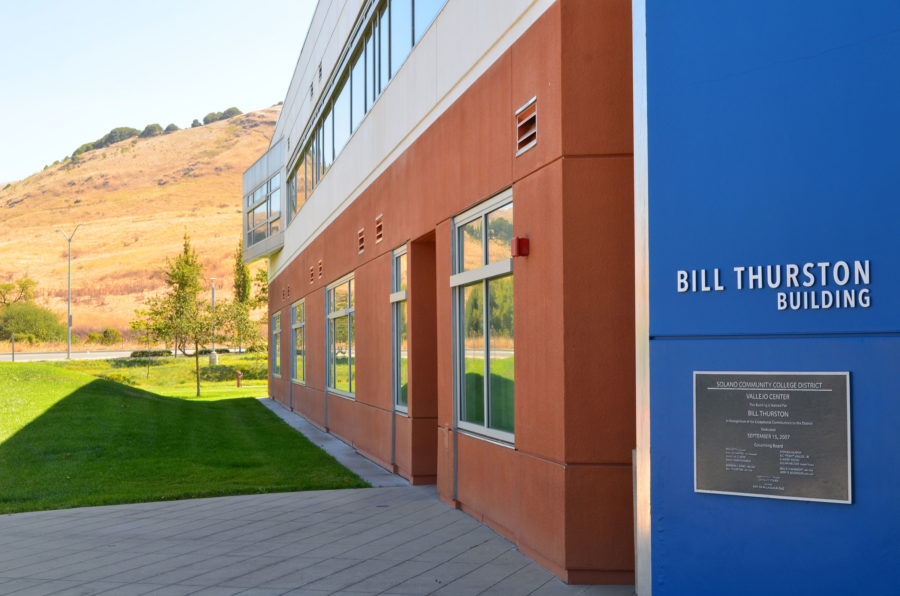
Solano College saved an estimated $48,000 in maintenance costs by re-coating their vibrant-colored exteriors with NeverFade Facade Restoration Coatings that were custom-matched to the school’s official colors. Photo courtesy of APV Coatings
One PVDF resin grade, Kynar Aquatec, helps APV Engineered Coatings’ NeverFade Facade Restoration Topcoats resist extreme UV rays, high temperature, humidity, and abrasion from salt spray, sand, and other windblown particles. The benefits of protective coatings also include hindering mold, mildew, and dirt pickup for over 20 years—a much longer life span than the five-year life cycle typically seen with high-performance urethanes and acrylic-latex paints in climates such as South Florida and Arizona. It’s environments like these where traditional high-performance paints break down under UV exposure, eroding over time, and eventually leaving the building’s substrate bare and open to damage from the elements.
In addition to its ingredients, a coating system’s longevity in subtropical climates depends on whether the chemistry is appropriate for the surface and conditions. Manufacturers of performance coatings conduct a broad series of tests under specifications like AAMA 2605 and Paint 47 and work with ingredients intended to bond to a specific substrate. Manufacturers also test the compatibility between the system’s topcoat and primer. This ensures that a failure will not result in between coats, which would impact the life of the protective coating.
Prepping PVDF Coating Systems
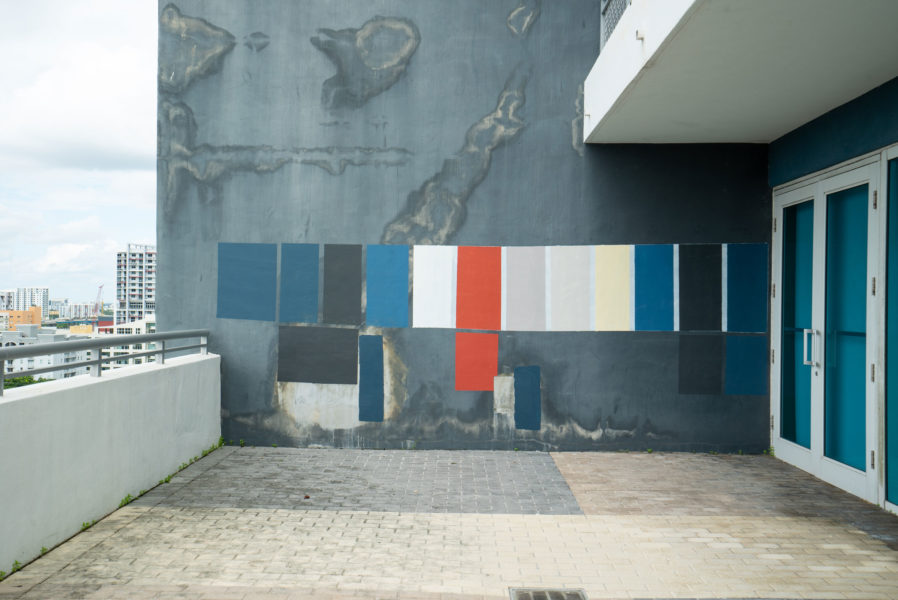
Pre-job testing, color matching, and application mock-ups of NeverFade Facade Restoration Coatings were crucial steps of the coatings application process at the Infinity at Brickell Condos in Miami, Florida. Photo courtesy of APV Coatings
Inadequate surface preparation and improper primer application is another way a coating system can fail, so proper NACE, ISO, and/or ASTM practices for surface prep and profiling should be employed. The primer must be engineered to bond well to the substrate while considering pre-existing conditions.
The coating system also must have early water resistance and the ability to be applied in high temperatures and humidity. It should keep a nice wet edge, with no hard-to-blend roller marks—one of the biggest challenges with rolling a coating onto a surface in high ambient temperatures.
Facade restoration of commercial buildings can be a time-consuming and costly process if not done properly. However, a PVDF-based coating system engineered for harsh UV-prone climates and applied with the proper techniques, can protect a building’s aesthetics, reduce maintenance, and sustainably lengthen its overall life span. This affords tremendous cost savings to building owners.