Story at a glance:
- Low carbon concrete is a key strategy toward reducing greenhouse gas emissions in the construction industry.
- Research leaders at Chryso and GCP continue to work to develop innovative, low carbon solutions that are still strong.
- Experts are also exploring new sources of supplementary cementitious materials like natural and glass pozzolans and blended cements.
The construction industry—a significant contributor to greenhouse gas emissions—is undergoing a transformative shift toward decarbonization. One of the key strategies in this journey is the development of low carbon concrete.
This article explores the latest developments in low carbon concrete—including strength enhancers, cement additives, circular economy solutions, and tailored admixture packages.
1. New Developments in Low Carbon Concrete with Strength Enhancers
Traditional concrete has long been a major contributor to carbon emissions due to the energy-intensive production of cement. To mitigate this researchers have been exploring innovative ways to develop low carbon concrete without compromising its structural integrity. One significant advancement in this area is the incorporation of strength enhancers.
Strength enhancers are additives designed to improve the early and ultimate strength of concrete, allowing for reduced cement content, while maintaining the desired performance. CHRYSO & GCP (Saint-Gobain Construction Chemicals) has been at the forefront of researching and developing these enhancers. For example, our EnviroMix® SE is an inventive strength enhancer offering for concrete that reduces the cement factor by approximately 10%, with early and late age strength gains anywhere from an average of 350psi to 600psi up to as high as 1000psi. At a low dose the strength enhancer in addition to a moderate dosage of a water reducer maintains premium concrete quality and performance.
By using less cement, a major source of carbon dioxide emissions, the environmental footprint of concrete can be significantly reduced.
2. Developments of New Cement Additives to Enhance Low Carbon Concrete
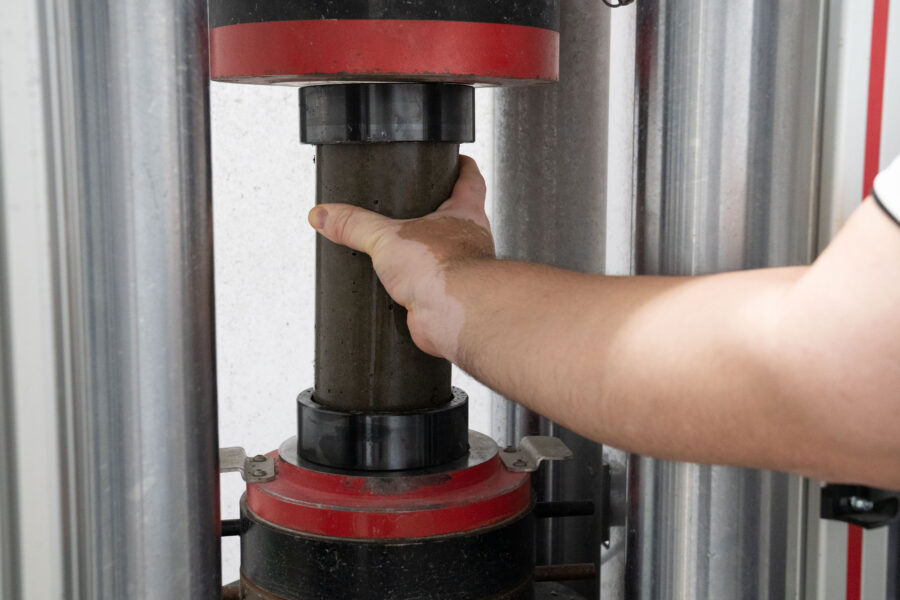
Photo courtesy of CHRYSO and GCP
Portland limestone cement (PLC) and new blended cements using pozzolanic materials (fly ash, natural pozzolan, and calcined clay), as well as ternary binders based on several SCMs, are promising alternatives to conventional Portland cement. PLC incorporates limestone, which naturally produces less carbon. Other natural SCMs, even if transformed through calcination, like calcined clay, or by-products from other industries, also offer a lower carbon footprint. Both options hold great potential for reducing the carbon footprint of concrete.
GCP has been developing new generations of cement strength enhancers that enhance the viability and performance of PLC and blended cements in North America. These additives help overcome some of the challenges associated with these alternative cements, such as increased water demand, reduced strengths, and packset issues.
This new portfolio of patent-pending solutions is a very robust response to SCM content maximization while mitigating SCM mix and quality variations. These innovations pave the way to lower carbon cement production and provide cement and concrete producers with robust quality and performance binders to meet the construction industry requirements. By addressing these issues the adoption of low carbon concrete becomes more feasible in the region.
3. Increasing Adoption of Circular Economy Solutions
In addition to advancements in low carbon concrete production, the adoption of circular economy solutions is vital in the construction industry. Three notable examples are Chryso®Quad, Convert C, and the Recover system from CHRYSO & GCP.
The system is designed to enhance the use of complex aggregates such as harsh manufactured sands. Using lower quality, more complex sands, and aggregates, which are locally sourced, without compromising the concrete quality significantly contributes to reducing supply lead time, costs, and improving the concrete CO2 footprint through reduction in transportation impacts. Our analysis has shown that the use of locally available materials contributes anywhere from 0.4% to 9% reduction in CO2.
Convert C is an additive for the treatment of returned plastic concrete to convert it into a dry, hardened, granular state. After the appropriate drum rotations, the discharge of the granular material, a standard washout procedure, can be used to clean the drum. The output is excellent as a road base, fill materials, or landscape base with good granular distribution and compaction.
The Recover system is another innovative solution that enhances sustainability in concrete construction. According to the National Ready Mixed Concrete Association, 2 to 10% (average of 5%) of the estimated 455 million cubic yards of ready mixed concrete produced in the US is returned to the concrete plant. Recover enables the recovery of fresh concrete that would otherwise be discarded, allowing it to be reused in subsequent batches.
One customer case study shows 275 yards per month of concrete that is salvaged; annualized that is equivalent to 331 tons of carbon dioxide a year of avoided emissions from cement alone—or emissions from 40,263,716 smartphones charged, according to the EPA Greenhouse Gas Equivalencies Calculator.
As a system Recover is also used to make truck washout more efficient, which reduces material, water waste, and minimizes the environmental impact associated with concrete production.
The adoption of circular economy solutions aligns with the broader sustainability goals of reducing waste and conserving resources. It also opens new opportunities for innovation and collaboration within the construction sector.
4. Optimization and Tailored Admixture Packages
While these developments are promising it is crucial to recognize that sustainable solutions often involve trade-offs. The construction industry must carefully balance various factors—including performance, cost, readily available materials, and environmental impact; mix optimization is a key approach to achieving these goals.
Mix optimization involves tailoring concrete mix designs to specific project requirements and environmental objectives. Rather than relying on a single “silver bullet” admixture, this approach considers the complete admixture package that best suits the situation. It allows for a customized blend of additives, including strength enhancers, cementitious materials, and other performance-enhancing compounds. The development of our HRWRs for high SCM replacement and strength enhancers allow us to be creative with admix combinations. To address multiple low-carbon issues, we can tailor an admix package, for example, our Quad system mentioned earlier, combined with our EnviroMix® SE strength enhancer, tackles low quality aggregates alongside cement replacement and cement reduction to drive optimal CO2 reduction.
This approach recognizes that there is no one-size-fits-all solution for carbon reduction challenges in concrete production. Factors like regional differences, project specifications, and environmental regulations all play a role in determining the optimal mix design. By prioritizing mix optimization sustainability goals can be met while meeting the performance requirements of each project.
5. Ongoing Research and Future Prospects
The journey toward low carbon concrete is ongoing, marked by continuous research and development. The industry must remain committed to driving innovation in the field of sustainable construction. This commitment extends to ongoing research efforts aimed at expanding the use of industrial by-products and construction waste streams in concrete production.
One promising avenue of research involves further exploring new sources of supplementary cementitious materials like natural and glass pozzolans and blended cements. These materials have the potential to further reduce the carbon footprint of concrete and offer additional benefits, such as improved durability and reduced permeability.
Ongoing studies are also examining how to effectively incorporate construction waste streams, like demolished concrete and masonry, into new concrete mixes. By diverting waste from landfills and reusing it in construction, these efforts contribute to a more circular and sustainable construction industry.
Conclusion
It is crucial to recognize that sustainability in construction is about making informed choices. There is no single solution to carbon reduction challenges. Instead, it is important to customize concrete recipes to meet specific project requirements and environmental objectives.
The urgency of reducing carbon emissions in the construction industry cannot be overstated. It is vital that industry leaders like CHRYSO & GCP remain dedicated to the pursuit of low carbon concrete solutions, to continue to make significant strides in various aspects of sustainable construction. From the development of strength enhancers and cement additives to the promotion of circular economy solutions and tailored admixture packages, these innovations, and future breakthroughs are paving the way for a more sustainable and decarbonized construction industry. By collaborating and embracing these innovations, the construction sector can play a pivotal role in mitigating climate change and building a more sustainable future.