Story at a glance:
- APV Engineered Coatings knows how you can improve your outdoor air quality.
- To avoid VOCs associated with paints and coatings, project specifiers can turn to water-based coatings for exterior restoration projects.
Volatile organic compounds (VOCs) are carbon-containing compounds that have a high vapor pressure and low boiling points that cause odors, environmental pollutants, and health hazards. Many VOCs are the result of chemicals used and produced in the manufacture, use, and sometimes storage of paints, lacquers, paint thinner, and thousands of other products.
VOCs are a particular concern in indoor environments, where they can impact indoor air quality (IAQ) and lead to short- and long-term adverse health effects such as eye, nose, and throat irritation; headaches; nausea; and damage to the liver, kidneys, and central nervous system. While concentrations of VOCs are consistently higher indoors, they also are a concern outdoors, where once in the atmosphere they react with oxygen to produce ozone—a key component of smog.
VOCs from construction materials (including composite wood products, paints, varnishes, caulks, and adhesives) and activities (including diesel exhaust from construction equipment) can be a nuisance to construction workers, building occupants, and passersby and lead to the same potential health effects as in indoor environments. Moreover, VOCs from outside can be drawn into a building through open windows and make up air systems that pull air from outside to the inside of a building.
Why Do Coatings Contain Volatile Organic Compounds?
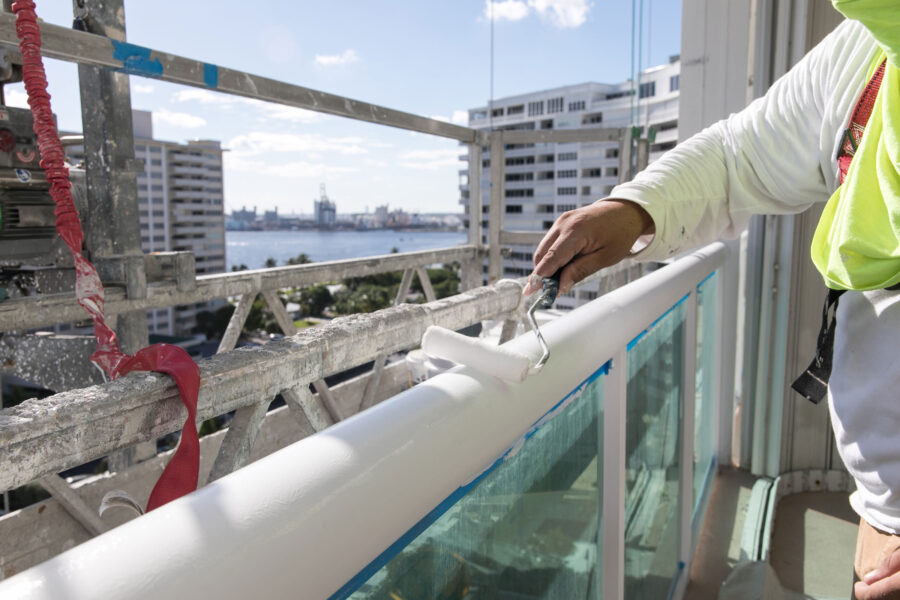
Photo courtesy of APV Engineered Coatings
Virtually everything that is not the dried solid coating in a typical paint formulation is released into the air. VOCs in solvent-borne coatings usually come from the solvents themselves. Solvents act as carriers for the coating’s pigment and resins, helping the coating to wet out on the surface and then dry after it is applied. Once the coating is applied to a surface, the solvent evaporates, leaving the solids content in a dried film formation on the substrate.
In general solvents offer an efficient and low-cost means for dissolving and dispersing raw material components, and they evaporate rapidly, shortening dry times and allowing coatings contractors to be more productive. Solvent-based formulations have an inherently low surface tension and will wet out on a multitude of substrates without the use of additives. They help a coating adhere well to substrates that have less than pristine surface cleanliness.
Water can replace solvents in coatings to reduce emissions and VOCs, but these coatings generally still contain a small percentage of co-solvent to help the process. APV’s chemists who formulate water-based NeverFade coatings understand the characteristics of the polymer chemistry, impact of rheology modifiers, and appropriate co-solvents to optimize a continuous film formation without the need for solvents.
The VOCs in a water-based coating are usually found in the resin or binders, thickeners, certain additives such as defoamers and surfactants, and pigment. It is estimated that each ounce of colorant added to tint paint may contain between 5 and 20 grams of VOCs. Darker color coatings, which require more pigment, could add 300 or more grams of VOCs per gallon of paint, above and beyond the VOCs contained in the solvent.
In general higher concentrations of VOCs are found in extreme-durability solvent-borne polyurethane and acrylic topcoats and pretreatment wash primers, where they run in the 5.0-6.5 pounds per gallon (600-700 g/l) range. Low-VOC water-based coatings typically contain less than 100 grams per liter, while 5 grams per liter is considered “very low” or “zero.”
VOC Regulations
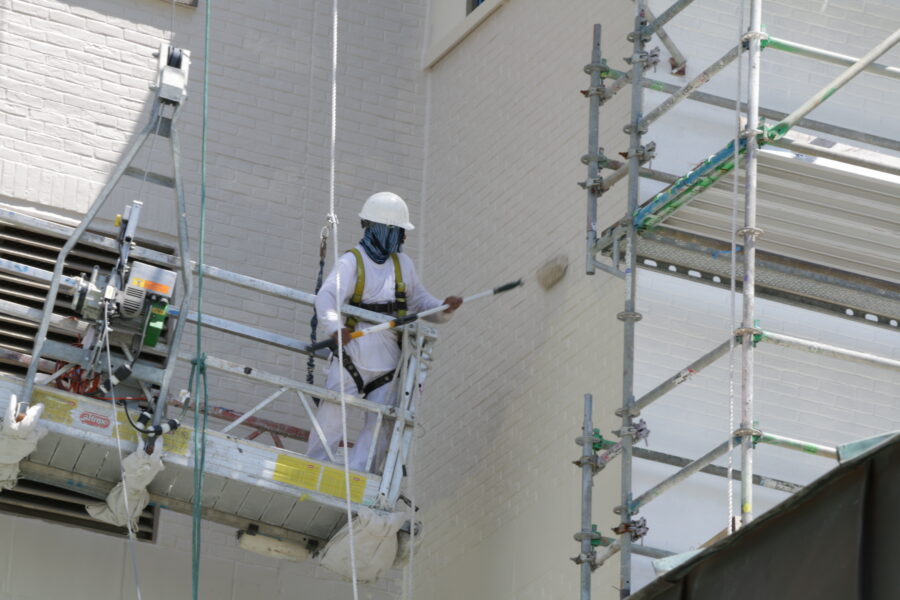
Photo courtesy of APV Engineered Coatings
While few regulations or standards exist for VOCs in outdoor environments, states like California are taking a more aggressive approach.
The South Coast Air Quality Management District in California adopted (and has subsequently amended) Rule 1113 to tackle area source emissions of paint and coatings. It is the most comprehensive and strictest restriction in the US. Many other states have adopted it, and many manufacturers have chosen to follow it as well.
The California Air Resources Board (CARB) also helps to regulate VOCs based on the unique environments and topographies of California and its 35 local air districts. CARB decides whether or not federal guidelines are appropriate for the region and where to tighten restrictions when necessary.
The EPA regulates VOCs outdoors mainly because of their ability to create photochemical smog under certain conditions. VOC-exempt status is granted only to chemical compounds that are negligibly reactive on forming ground-level ozone. To be classified as such the coating must be listed on either of the lists of VOC-exempt materials maintained by the EPA or by SCAQMD under Rule 102. Note that just because a coating may contain VOC-exempt solvents and may be considered EPA-compliant in the US, it might not be recognized as exempt by other countries.
While OSHA does not have a general air quality standard, it does require employers to furnish employees with a worksite that is free from recognized hazards (in the case of painting, by providing appropriate ventilation and respiratory protection) and sets limits on exposure to air contaminants and particulate release.
With less than 50 grams/liter of VOCs, NeverFade Original Topcoat is one of the very few high-performance coatings to meet SCAQMD Rule 1113 environmental regulations. It also meets 40 CFR Part 59, Subpart D, national Volatile Organic Compound Emission Standards for Architectural Coatings (which is capped at 380 g/l). The topcoat’s complementary primers also contain less than 50 grams/liter of VOCs.
Water-Based PVDF Coatings Blend Safety and Performance
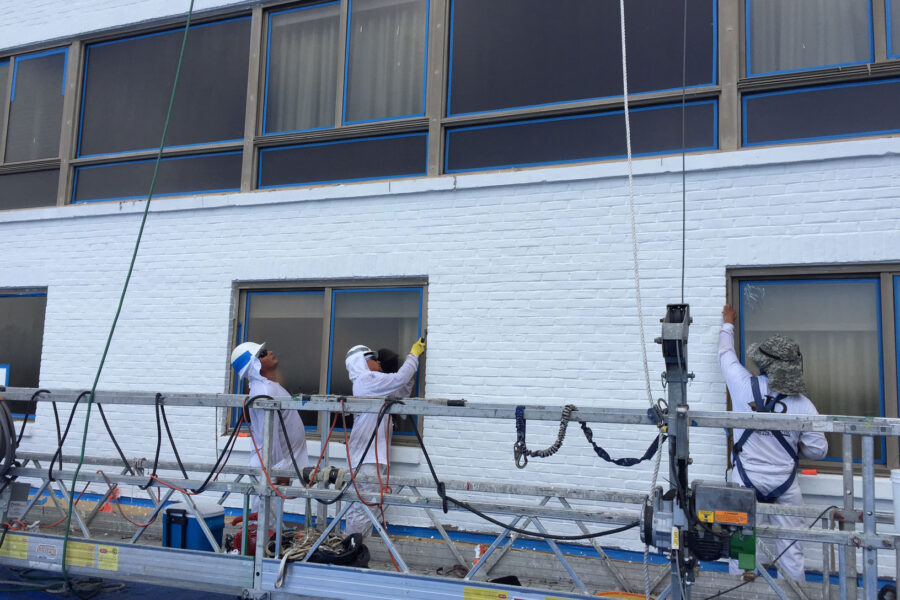
Photo courtesy of APV Engineered Coatings
Some users of high-performance architectural coating technologies may believe that water-based coatings do not provide the same ease of use, long-lasting durability, extreme weatherability, and color-retention properties as solvent-based coatings. This is no longer the case thanks to the introduction of Kynar Aquatec, a polyvinylidene fluoride (PVDF) water-based resin emulsion. This tough engineered thermoplastic has a 20+-year demonstrated record of performance in extreme conditions and serves as the binder in APV’s water-based NeverFade coatings.
Low VOCs are an important consideration when buildings are occupied during the coating project, especially when air-handling units bring outdoor air inside. For example, when owners of a luxury high-rise condominium in Florida wanted to improve the curb appeal of their building with a refresh of its exterior coatings, they chose NeverFade Coatings for their low VOC content and low odor that would keep tenant inconvenience to a minimum. Schools and hotels have made the same purchasing decisions, allowing coating projects to proceed and business to be conducted as usual while buildings are occupied.
Additional Tips for Reducing VOCs During Exterior Renovation
Architects and project specifiers can limit the release of VOCs during exterior renovation projects by specifying a high-performance coating that is water based, such as NeverFade Coatings. To meet the strictest guidelines, confirm that the coating manufacturer complies with SCAQMD Rule 1113 by asking to see its registration under SCAQMD Rule 314.
Application methods that limit thinning of the product, such as brush or roller, will also reduce VOC emissions. If a sprayer is to be used for application, a high-volume low-pressure (HVLP) sprayer will provide the best combination of good transfer efficiency and low overspray.
When working with solvent-based coatings, proper respiratory protection must be used by the contracting crew, and care must be taken with respect to flammability. Water-based coatings require less stringent safety practices (though proper personal protective equipment as directed by the coating’s Safety Data Sheet and label is still required) and can be applied with minimal impact to the safety and comfort of the crew.
Finally, job sites should always follow local disposal agency guidelines for proper disposal of coating-containing waste.