Story at a glance:
- Unprotected slabs without the proper moisture-barrier can compromise the home’s interior by allowing pathways for water vapor and soil gas to travel through.
- A properly selected and installed under-slab vapor retarder is the first line of defense against water vapor and soil gas migration.
- Once concrete is poured, fixing problems becomes cost and time prohibitive.
Concrete is a staple building material for residential construction and a crucial part of the home’s structure. A new change in the 2021 International Residential Code (IRC) requires better performing vapor barriers under the concrete slabs. The change means homeowners will enjoy better protection against moisture-related flooring failures, healthier indoor air quality, and increased structural longevity.
Although concrete is long-lasting and durable, it is also naturally porous. Unprotected slabs without the proper moisture barrier can compromise the home’s interior by allowing pathways for water vapor and soil gas to travel through concrete. Water vapor migration can cause flooring failures, high relative humidity, mold, mildew, and degradation of the concrete slab and its components. Soil gasses like radon and methane can also readily move from the soil to the indoor environment—negatively affecting occupant health and safety.
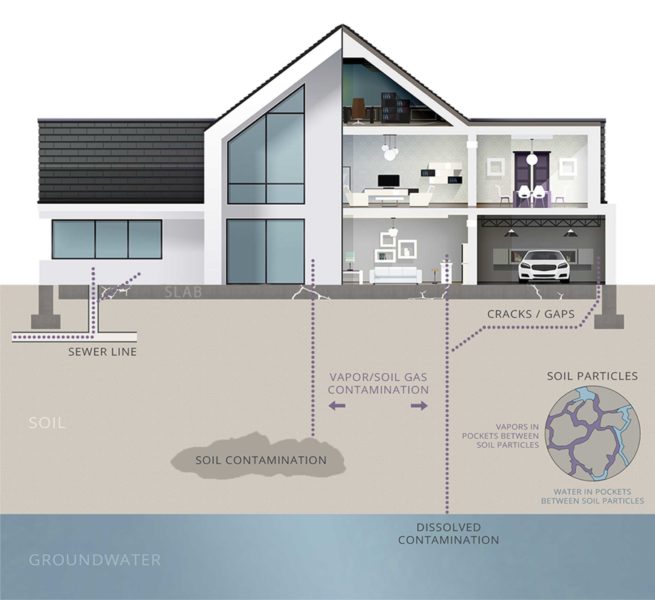
Common pathways for moisture and soil gas intrusion. Image courtesy of ISI Building Products
A properly selected and installed under-slab vapor retarder is the first line of defense against water vapor and soil gas migration. Guarding against such hazards is imperative for successful flooring systems and healthy indoor environments.
Previous versions of the residential building code required a 6-mil vapor retarder to be used under concrete slabs. In the 2021 IRC, the requirement is upgraded from 6-mil vapor retarder to a 10-mil vapor retarder conforming to the industry recognized ASTM E 1745 Class A standard for under-slab vapor retarders.
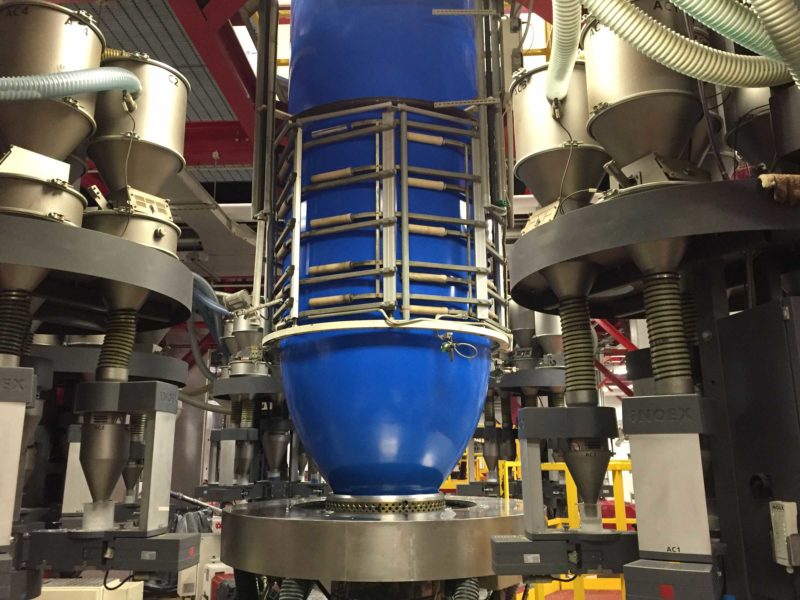
High-performance vapor barrier manufacturing. Photo courtesy of ISI Building Products
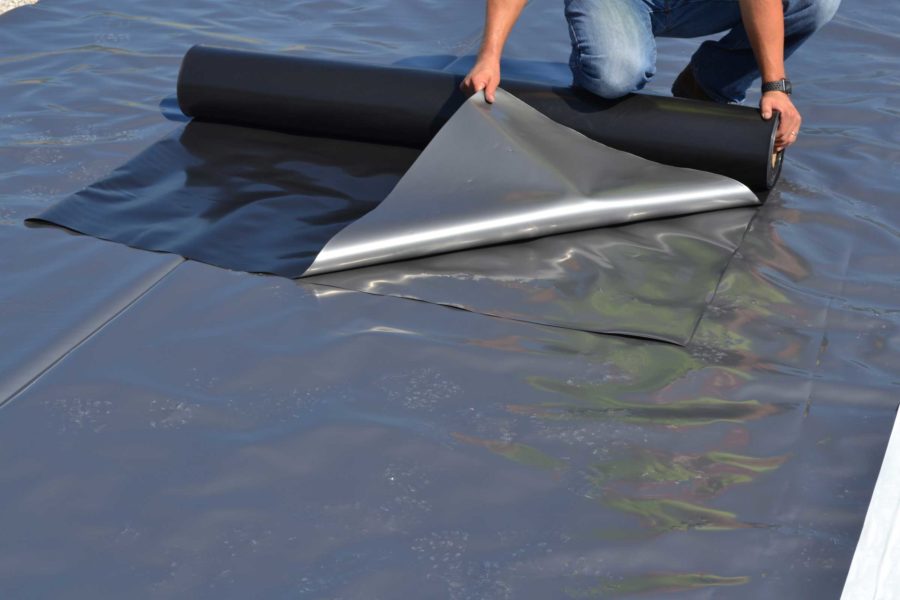
20-mil thick Class A vapor barrier membrane. Photo courtesy of ISI Building Products
ASTM E 1745 classifies materials as A, B, or C based on the product’s puncture resistance, tensile strength, and water vapor permeance. Class A vapor retarders and barriers carry the highest puncture resistance and tensile strength, with Class C being on the lower end of the scale. The water vapor permeance requirement is currently set at 0.1 perms for all three classifications, making the separating factors puncture resistance and tensile strength.
The primary reason the new code specifies a Class A vapor retarder is to ensure the integrity of the membrane during installation. To provide the highest level of protection, a vapor retarder should be continuous (without gaps or tears). Class A vapor retarders provide robust protection against degradation from construction foot traffic prior to the pour.
In addition to the 2021 code requirements, several variables are critical when selecting the best membrane for a home’s concrete slab. First, it is important to understand the difference between a vapor retarder and a vapor barrier. The industry recognizes a vapor retarder as having a water vapor permeance rating between 0.1 perms and greater than 0.01 perms. Vapor barrier materials are considered to have a water vapor permeance rating below 0.01 perms. The lower the water vapor permeance, the higher the quality of the vapor retarder.
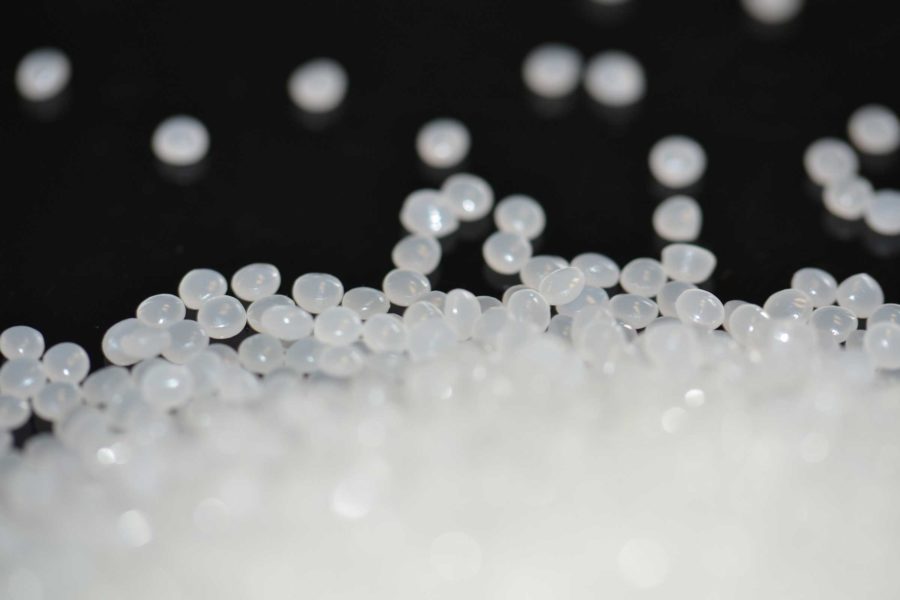
Virgin resin helps create high-performing membranes designed to protect for the lifetime of the slab. Photo courtesy of ISI Building Products
Secondly, it is important to look for moisture barrier products manufactured from 100% virgin resin. These products are typically manufactured in a multi-layer or co-extruded fashion. Co-extruded films are superior to single-layer products, as they incorporate the best properties of different resins and link them all together into one film structure.
Selecting Class A membranes with water vapor permeance values below 0.01 perms and manufactured using co-extrusion technology with 100% virgin resin will not only ensure compliance with the 2021 IRC but will also provide the best possible protection for the lifetime of the slab.
Once evaluation and selection of a proper under-slab vapor retarder or barrier is complete, efforts should turn to proper installation. ASTM E1643 is the standard practice for selection, design, installation, and inspection of water vapor retarders used in contact with earth or granular fill under concrete slabs. The standard outlines parameters for proper installation, including:
● Properly level and compact the sub-base material to minimize risk of punctures.
● Create a monolithic membrane between the surface of the slab and moisture sources below the slab as well as at the slab perimeter.
● Roll out vapor barrier with the longest dimension parallel with the direction of the concrete pour. Face overlaps away from the concrete pour when possible.
● Extend vapor barrier over footings and seal to foundation wall, grade beam, or slab at an elevation consistent with the top of the slab or terminate at impediments, such as waterstops or dowels.
● Extend vapor barrier over the tops of pile caps and grade beams to a distance acceptable to the structural engineer.
● Lap all joints a minimum of six inches and seal laps in accordance with manufacturer’s recommendations.
● Seal all penetrations, like utilities and columns, per the manufacturer’s recommendations.
Once the concrete is poured, fixing problems becomes cost and time prohibitive. The best opportunity to protect a structure from the harmful effects of moisture infiltration through the slab is to specify ASTM E 1745 Class A vapor barriers made from 100% virgin resin and adhere to the manufacturer’s installation guidelines. Not only will the requirements of the 2021 IRC be satisfied, but the structure will be safer, healthier, and more durable for years to come.