Story at a glance:
- The built environment has the central function of protecting people from the extremes of local climate, but climate change is making those extremes harsher worldwide.
- Designing buildings to counter climate change should incorporate a project’s entire life cycle, from supply chain to maintenance.
- High-performance, low-VOC coatings that can be applied in the field to air-dry are making it easier for owners to protect building substrates against the elements.
Since the dawn of civilization architecture has helped people cope with extremes like heat, moisture, and seismic activity. But with climate change making such extremes more punishing, buildings must withstand stronger storms, higher temperatures, and more devastating floods to protect their occupants.
“Architecture is coming from extremes,” says Kathleen Hetrick, sustainability engineer for Buro Happold, a global sustainability engineering consultancy. “Every aspect of the built environment is protecting people from extremes.” While some areas might feel relatively safe from the most disruptive effects of climate change, the industry is realizing no one is immune—and more RFPs are including resilience in their sustainability goals as a result. Projects must anticipate and meet climate challenges to retain value. And ideally they need to accomplish this without contributing to the factors producing climate change.
Architect Frederick Fisher + Partners’ Santa Monica City Hall East, which Buro Happold also worked on, employed advanced architectural, engineering, and construction practices to confront the challenges of climate change. Built to the Living Building standard and one of the “greenest” buildings in the world, it makes positive contributions to its environment rather than merely lessening its negative impact. Santa Monica City Hall East has automated windows and air quality monitoring to deal with the threat of California wildfire smoke. The building collects and treats rainwater to make it potable, and it features the largest composting toilet installation on the West Coast. The project “really focuses on passive design—having the building work as hard as it can to keep it comfortable,” Hetrick says.
Looking to the Future
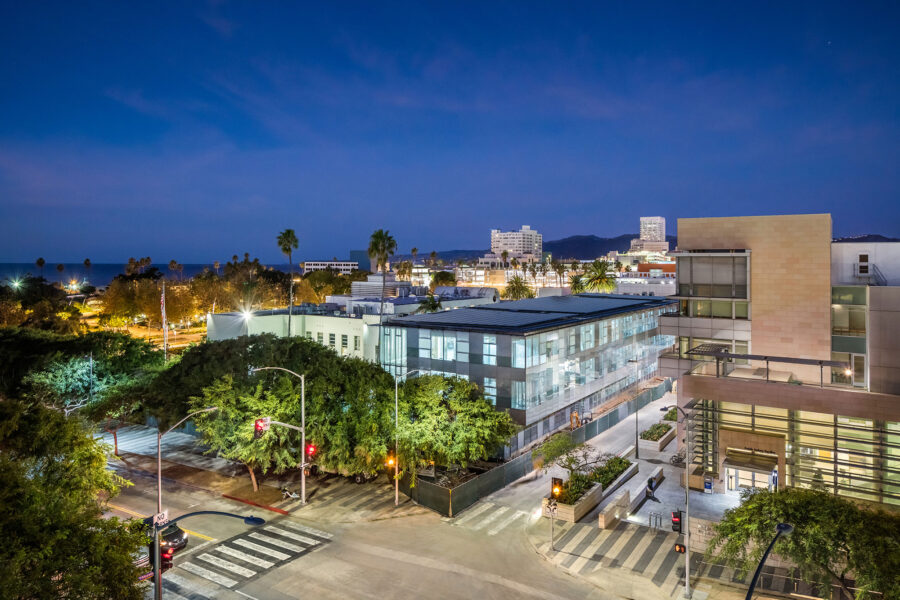
Santa Monica City Hall East is an all-electric, net-zero energy, and net-zero water project. Buro Happold provided integrated engineering and sustainability consulting services. Photo by Alex Nye
Designing for climate change is an exercise in risk management, Hetrick says, though some risks may be more obvious than others. “It’s hard for humans to think about the future. You deliver on time and under budget, and then X, Y, and Z happens, and you didn’t design for those possibilities. Do yourself a favor: Model for every contingency.”
A holistic approach to designing for climate change should extend throughout a building’s life cycle, from supply chain to upkeep. “You have to layer the systems, which is going to cost a little bit more upfront,” Hetrick says. “You’re thinking about all the situations that could come. Even the maintenance is important.”
For example, “When you’re making decisions about finishes, you know that toxic chemicals come cheap, and those materials are manufactured in Texas or Louisiana,” she says. “When a big hurricane comes through, those factories can flood and spread a lot of pollution. Do you want your brand associated with that?”
Do yourself a favor: Model for every contingency.
Any project that prioritizes resiliency represents progress in meeting the challenges of climate change. “These are complex problems,” Hetrick says. “Just because you can’t claim zero carbon doesn’t mean you aren’t making a difference. Take an activist approach: Push contractors in the right direction, and push clients in the right direction.
“This is what people want to see, and it also protects your investment,” she continues. “Climate change is happening everywhere all at once. You want to minimize risk. You also want to maximize opportunity. If you’re spending millions of dollars on a project, it’s a huge investment. Do you want to risk that?”
Renewal vs. Replacement
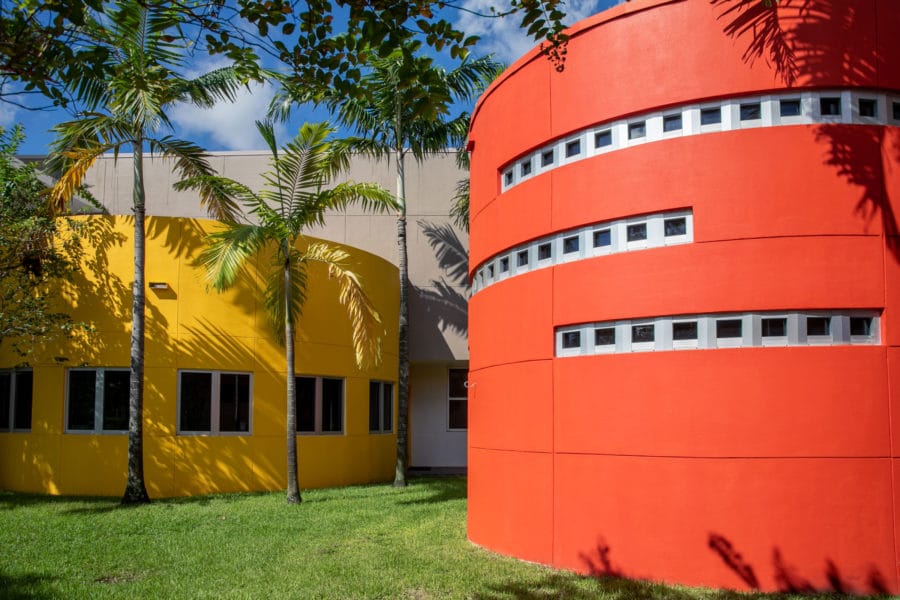
NeverFade is a premium line of low-VOC, water-based exterior architectural coatings formulated with a resin that lengthens the life of building facades. Photo courtesy of APV Engineered Coatings
Weather is harsh on building finishes, and climate change is making the wearing effects of UV light, wind, and water stronger. But advancements in coating technologies can protect a variety of substrates used in construction against the elements for longer periods, and often head off the need for significant repairs or replacement.
Founded in 1878, Ohio-based APV Engineered Coatings custom formulates and manufactures industrial coatings and advanced chemical products. Chief among them is NeverFade®—a premium line of low-VOC, water-based exterior architectural coatings formulated with Kynar Aquatec® PVDF, a resin that is unprecedented in the industry for lengthening the life of building facades.
NeverFade can be used on the entire building envelope, including metal roofs, concrete, walls, and stucco surfaces. While a typical building facade requires recoating every four to six years, the product is warrantied to protect surfaces for at least 15. “It’s not going to break down,” says Ernie Porco, product application engineer at APV. “It’s protecting that substrate for the entire time.”
Recoating vs. Replacement
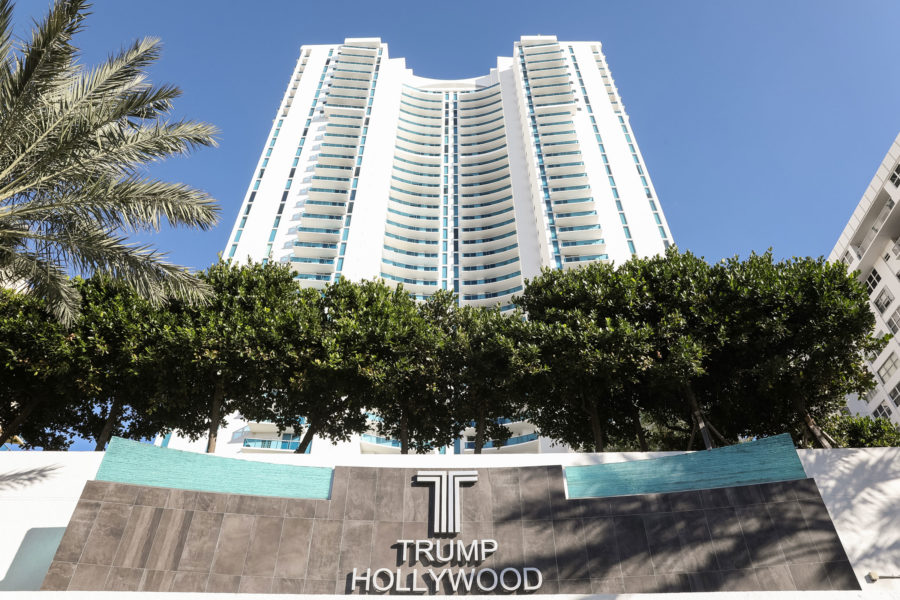
The Trump Hollywood in Florida had a restorative facelift with NeverFade, which helps to protect buildings from high UV rays, high humidity, salt spray, and sand. Photo courtesy of APV Engineered Coatings
Beachfront properties are particularly vulnerable to the elements, being exposed to sunlight, high humidity, salt spray, and sand. When the builder-applied acrylic coatings on the stucco exterior of the 41-story Trump Hollywood condo building in Hollywood Beach, Florida started to get chalky and dull, Capital Contractor Services opted for NeverFade.
“Trump Hollywood’s prestige, size, unique shape, and location, coupled with the fact that it was occupied by residents who didn’t want to be inconvenienced during the facade restoration process, made it imperative for us to work deliberately, safely, and with a high level of quality,” says Alex Forjan, executive vice president of Capital’s Exterior Division.
Another building in Rockwood, New York recently underwent a complete facade restoration using NeverFade. The coating on the 40,000 square feet of aluminum panels had previously been field-applied with an acrylic polyurethane that had degraded significantly due to UV exposure and precipitation.
Both restorations were accomplished with minimal disturbance to building occupants. Unlike most high-performance coatings, NeverFade is low-odor and water-based, Porco says. “We’re doing fully occupied buildings and not receiving any complaints.”
Saving Materials
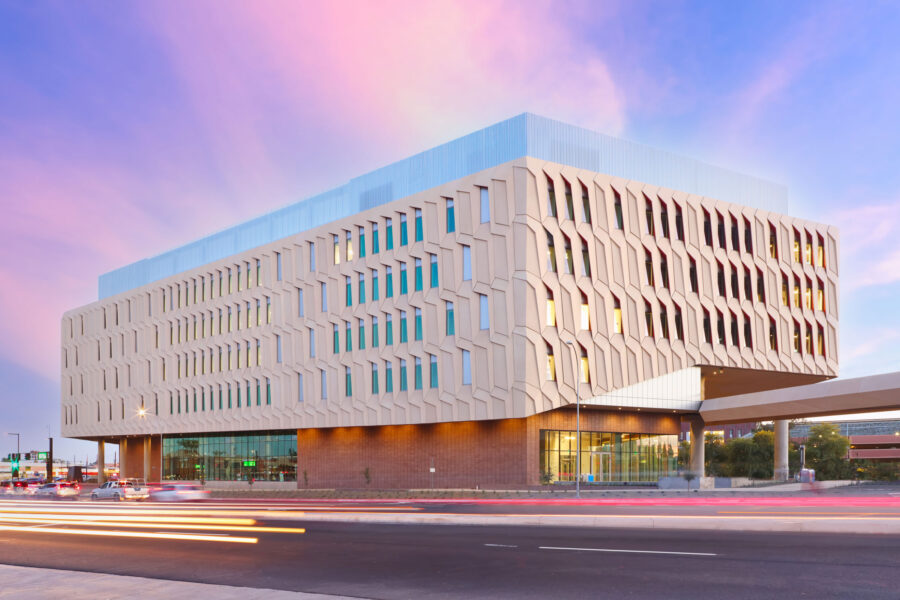
Buro Happold worked on the Rob and Melani Walton Center for Planetary Health for Arizona State University. Photo courtesy of McCarthy Construction
Maintenance and upkeep are expensive, but recoating can often help building owners avoid costlier repairs. “Most of the time buildings will just rip the substrate off and replace it,” Porco says. “We can get another 15 years and keep those materials out of a landfill. And if we can get people to paint the building the first time with it, it works even longer.”
Other APV products include BLOCKSEAL™, a liquid flashing that is AAMA 714-22 verified, low-VOC, fast-drying acrylic adhesive that keeps moisture from penetrating door and window openings beneath a structure’s exterior facade. Another superior product is KAPGUARD®, a line of factory-applied finishes custom-formulated with Kynar polyvinylidene fluoride resin, a tough thermoplastic polymer, in both water and solvent-borne chemistries.
NeverFade often comes in at a higher price point, but this premium coating line offers no-fuss application and ready-to-use formulations. “Building owners see the price tag and shudder a little bit,” Porco says. “But then they realize they’re not going to have to put up swing stages and do all the labor again for 15-plus years.”
“A field-applied product that can be air-dried and have the same performance as a baked-on coating is huge,” Porco says. “Some of the architects we meet ask, ‘Why didn’t we learn about this sooner?’ It’s a next step in the coatings world, especially with VOC requirements.”