Story at a glance:
- A new Tidalstone flooring system from Westcoat offers innovative and decorative aggregate blends.
- Tidalstone offers the beauty of terrazzo without the high cost or difficult installation.
Beautiful office spaces, commercial restrooms, laboratories—all benefit from Westcoat’s new Tidalstone Flooring System.
Tidalstone is a multi-layered resinous flooring system that features innovative and decorative aggregate blends. The combination of ultra-fine and oversized particles gives designers and architects the look of terrazzo or polished concrete with the benefits of a resinous flooring system.
Tidalstone takes a various assembly of chemistries and remixes them to focus on one central element—the TC-62 Tidalstone aggregate blend. TC-62 is a synthetic, broadcast medium that is available in seven color blends that can be applied in decorative and industrial solutions. It’s aesthetically pleasing, durable, and chemical-resistant to provide a quality floor coating in showrooms, hospitals, retail, spaces, schools, and more.
We recently sat down with Westcoat Product Manager Todd Cook to learn more about the new system’s aesthetic properties, technical attributes, and other benefits.
What is the new Tidalstone system?
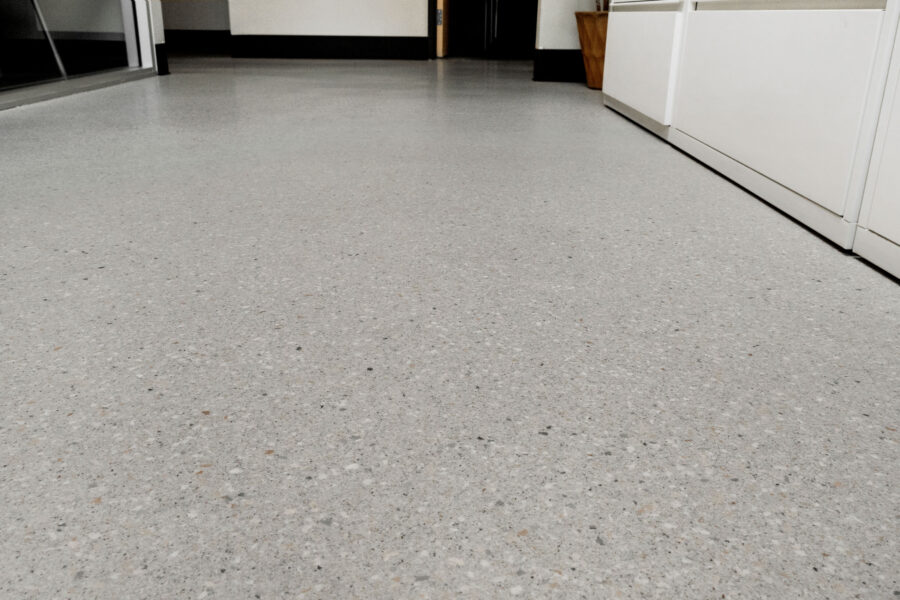
Resinous flooring brings life to this hallway. Photo courtesy of Westcoat
It has this terrazzo, exposed aggregate, polished concrete aesthetic with a variegated, mottled finish. We have seven standard colors available.
Each standard color consists of three or four different colors—even some colors that have some slight variegation to them—and different sizes within so they’re not all one standard size. Instead of having a flat, even, consistent finish, there’s a lot of depth.
We’ll explore this more later, but there are basically two system assemblies available—a Thin Film or a High Build option.
Why choose Tidalstone instead of, say, terrazzo itself?
The number one reason to choose Tidalstone is that it’s going to be cost effective. Especially with the Thin Film option, you’re going to have minimal height requirements. This system is very thin in its standard assembly, which is great for tenant improvements.
Why choose Thin Film?
You might use Thin Film in office spaces where you already have established elevations; maybe the cabinetry and door thresholds can’t be moved. In some cases, when it’s not new construction, you can anticipate the overall thickness of the flooring system. This system will provide you with similar aesthetics to terrazzo or polished concrete, but with very minimal thickness build and elevation required. It allows for great rehabilitation of spaces, whereas you might not have that ability to install a half-inch thick flooring system. This will allow you to come in and get that similar look and high-end performance while still maintaining all your existing elevations, which is really nice.
How can designers play with color using Tidalstone?
There are the standard seven pre-blended values, so you have a really nice array of palette, colors, aesthetics, and schemes to choose from.
Those seven colors can further be influenced or manipulated to expand the palette by utilizing the broadcast color.
What are some of the needs being met with these systems?
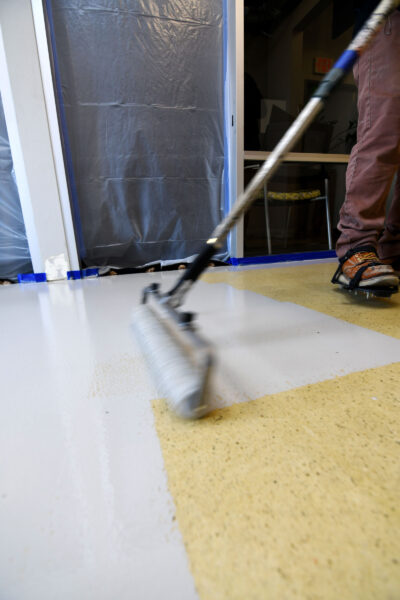
Photo courtesy of Westcoat
The standard thin film system consists of our EC-12 epoxy primer. This is primarily designed for concrete applications. After the concrete has been properly prepared to International Concrete Repair Institute guidelines of surface prep, we would apply our EC-12 primer, which is a very nice, tenacious, moisture-tolerant priming agent.
We can also utilize our EC-15, which is a moisture vapor barrier. We’re still able to service projects with higher levels of moisture by utilizing that moisture vapor barrier. There are a lot of substrates and projects that have higher levels of moisture based on their RH or calcium chloride testing; they might need to use that product.
How does Tidalstone work?
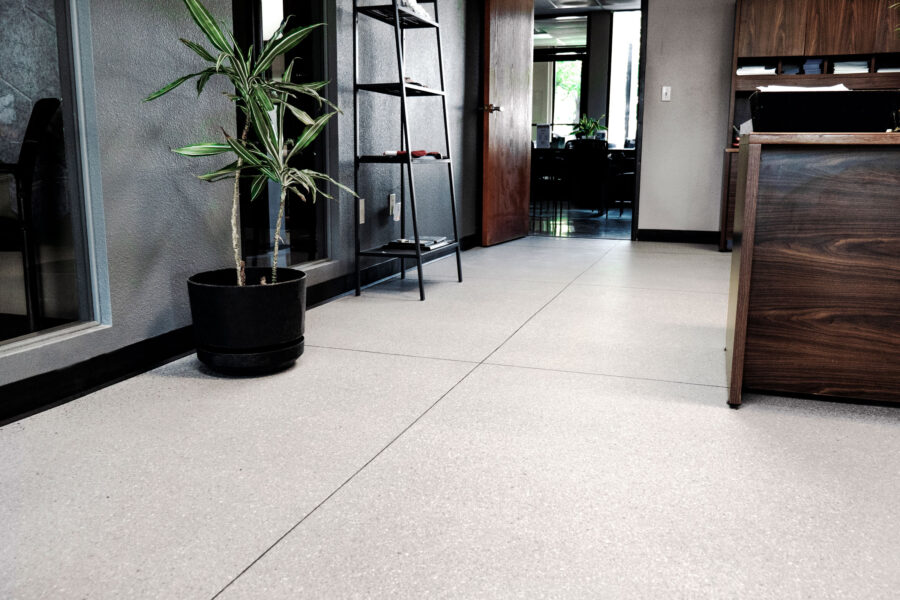
Photo courtesy of Westcoat
After it’s been primed we utilize our EC-102 Polyaspartic, which is a UV-resistant, polyaspartic, fast-drying topcoat material. This will provide a high-service, UV-stable material to broadcast into with the TC-62. By broadcasting into the EC-102 we have a UV stable base, as opposed to using standard epoxies or other materials that might be subjected to yellowing or ambering.
The EC-102 polyaspartic chemistry allows it to be UV stable. This is going to be great for projects with a lot of interior-exterior light—maybe they have roll-up doors or skylights. This is going to prevent that ambering and yellowing.
Then we broadcast the TC-62 into the EC-102. That TC-62—that nice blend of aggregate—is broadcasted into refusal, which means 100% coverage. And then at that point that coat dries. We will do a little bit of light detailing—sanding and scraping—and then collect the excessive or residual TC-62 aggregate blend broadcasts. At that point we will seal the floor with EC-102 polyaspartic in clear, which is the same formulation of fast-drying, High Build polyaspartic. That creates a lot of depth and a little bit more build and protection over the decorative floor.
Lastly, it’s sealed with our SC-65F Water-based Flat Polyurethane Sealer. That creates a low odor, water-based, VOC-compliant, low sheen, flat finish that provides a polyurethane toughness and durability. You have a very nice wear-resistant surface, but you also get this really soft finish.
This is nice because it echoes more of that organic, natural design aesthetic. That’s becoming much more popular in the design field. Also, it’s maybe not as distracting as a gloss floor would be. For example, when you’re doing installations at hospitals, vet clinics, schools, even office spaces—sometimes the gloss finishes can be very reflective. In some cases they can be disorienting where maybe there are dementia patients and maybe some of the very busy, reflective finishes can be distracting or impairing. That flat sheen offers a very nice wear resistance.
Also, sometimes higher gloss finishes will start to wear, especially in high-traffic areas over time. Sometimes they may start off as a gloss and eventually wear and dull—especially in areas like long walkways.
By already starting with a flat natural sheen you’re not going to change that. You’re already creating a very nice expectation of what the space will look like, and it has this very nice consistent finish throughout that’ll maintain and be consistent for the life expectancy of that and the service life of that floor.
What is the service life of that floor?
It varies based on the use and abuse of the space. Our standard Thin Film system and our High Build systems can last in the 10 to 20 years of service life. Like anything, it’s critical that you determine what the correct space is and whether to use the Thin Film or High Build system.
It’s also about maintenance. These are very durable, high-performance coatings, but like anything they require a little bit of maintenance and upkeep. Every five years or so depending on use and exposure, you would lightly clean the surface and abrade it. You could reapply a clear coat of SC-65 and that would extend that service life even further. Essentially that final coat is the sacrificial coat; it’s the layer that takes the burden off the whole system, like a clear coat on a car or a wax. It helps prevent wear. As long as it’s maintained it can last a very long time.
What does light cleaning entail?
A light office space is going to have pedestrian traffic—they could get away with dust mopping. Bigger floors that might see more chemical exposure may have more stringent requirements—they might have auto scrubbers, flooring machines, things of that nature.
But because it is utilizing these polyaspartic and polyurethane finishes as final seal coats, you have really good chemical resistance, so they can handle cleaning agents and exposure to fluids and chemicals that might be found in veterinary hospitals or a laboratory environment.
How do the High Build and Thin Film systems differ?
The High Build system features that same overall assembly but with optimal performance by incorporating our Temper-Crete urethane cement technology in place of that EC-12 layer. Instead of using the EC-12 as the epoxy primer we utilize our Temper-Crete. This offers enhanced bond strength, increased moisture tolerance, will produce a higher build, and offers a self-leveling aspect.
For floors that might need a little bit more build and impact resistance, if you’re looking for extended service life or warranty terms, those are all offered in the High Build system. Again, that utilizes the same decorative finish and the overall comparable barrier is the same, but we utilize a urethane cement that gives us better thermal shock resistance.
That self-leveling is really nice because maybe you need a quarter inch to three-sixteenths to build or want that higher durability achieved by that greater build system. That’s our flagship, the premier system, but we understand sometimes there might be budget restrictions or elevation restrictions, so we have the Thin Film offering to support both avenues. No matter what the client needs, we offer that flexibility.
Where does UV stability come into play?
High Build features a double broadcast, which gives you complete UV stability.
With the High Build our urethane cement gets applied directly over the concrete, it’s self-priming, and we broadcast into that Temper-Crete with the TC-62. Then we apply a polyaspartic EC-102 and do a second broadcast. By doing a second broadcast we ensure there are no issues with the urethane cement chemistry with it not being UV stable, and we’ve created this beautiful canvas.
Also doing a double broadcast ensures you have this nice, even floor finish. This is going to help with floor flatness, floor levelness. It’ll help with a little bit of anti-fatigue because you have these nice cushiony aspects.
What’s the installation process like?
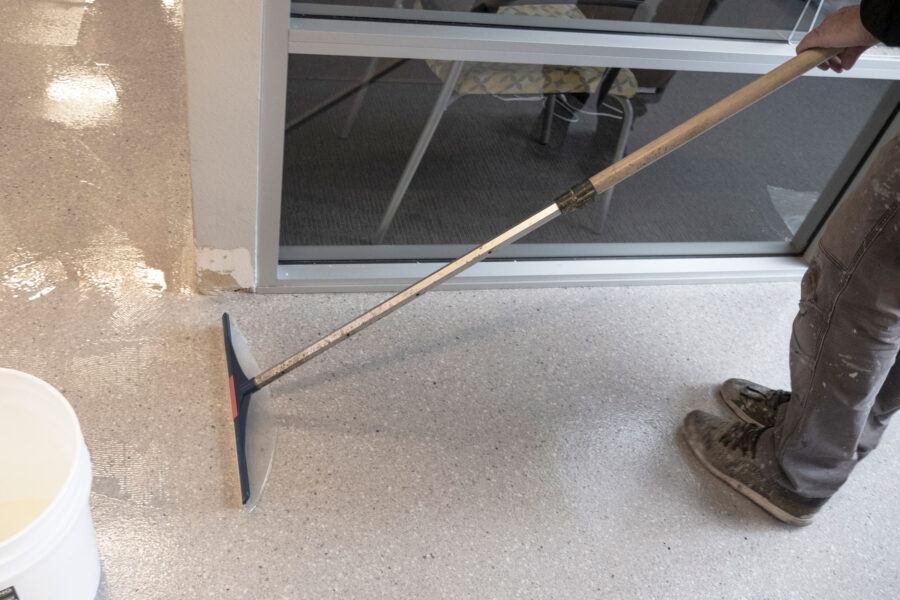
Photo courtesy of Westcoat
The High Build also makes installation easier. By doing a full broadcast and the second broadcast you really help ensure the floor will be flat, even, and have a uniform finish, so when you seal it and do your finish coats it’s a very nice uniform finish that’s fairly easy to apply.
This is going to be a lot more user-friendly for the application team or installers. When you’re out there installing this type of flooring compared to traditional terrazzo flooring or polished concrete, you’re going to have a lot less labor associated with it. It’s a labor set that is aligned with a broader audience.
Terrazzo is very specific. It requires a very specific applicator. These applicators have been doing this for years, and it’s very nuanced, where this can really speak to a broader audience of applicators. It still requires professional applicators, and we always encourage using our QCA (Qualified Contractor Applicator) program—our network of applicators who’ve met certain criteria.
Because it’s self-leveling, because it has this broadcast, it is much more forgiving. It’s also faster drying, which allows for less downtime. Maybe for new construction it isn’t quite as critical, although we’re still trying to keep up with that schedule, but when we’re doing a restoration or renovation project, you might have just one week where you can close the facility. Fast-drying technologies become really important to limit that downtime. These systems have very fast-drying chemistries to offer really fast turnaround to space so you’re not losing revenue.
How are these solutions sustainable?
We look at best practices. A lot of us forget best practices can include small things like saving trips to the job site or buying the correct amount of material. It can also be choosing the right system. Frankly, that’s one of the most important aspects here—taking the time to evaluate what you need for your facility.
Whether it be an office, school, laboratory, hospital, vet clinic, whatever—we want to have that dialogue with the architect, design professional, or facility manager ahead of time so we can give the proper recommendation.
So many times we see in our industry that a design team chooses the lowest bid or a system recommendation that isn’t appropriate for the space. That’s not sustainable. Now you’ve chosen an inferior system that was not suitable for chemical exposure or high traffic.
Let’s say it’s a shopping mall or convention center—that’s a lot of wear, a lot of pedestrian traffic. Or maybe you have some vehicular traffic, hand trucks, things like that. You better make sure you have a system that is designed to handle that, or you might waste a lot of time, money, and resources on a system that is not going to handle that use and abuse.
If you pause and reflect and specify and utilize the correct system from the beginning you’ll have a system that’ will most likely hold up very well, be a lot easier to maintain, and be a suitable alignment based on the requirements of the facility and attributes required.
How do epoxy coatings enhance high-end commercial spaces?
It starts with making the right decision, but we also want to look beyond epoxies. Epoxies are generally part of this bigger category known as resinous flooring. Resinous flooring includes but is not limited to epoxy, polyurethane, polyaspartics, urethane cements, and some additional chemistries. Sometimes they get lumped into just the epoxy vernacular, like Kleenex is a brand name—we all call tissues Kleenex.
With resinous flooring it’s similar. We have all of these different chemistries falling under this division of resinous flooring. As far as what they can do for a facility—how they can help preserve, protect, and enhance—there are a lot of things. There’s safety, cleanability, performance, and decorative benefits.
Let’s start with safety. How does resinous flooring improve safety?
Resinous flooring, epoxy flooring, can greatly help to meet or exceed your slip coefficient requirements. The skid-resistant finishes of a floor can greatly be manipulated with our type of chemistry and our type of flooring.
For example, something like tile flooring has an inherent finish and for the most part they’re really not modifiable. With systems like Tidalstone we can meet or exceed slip coefficient values or requirements for any facility by utilizing non-skid additives and incorporating those into our system in the clear coats in the decorative finish layer. We can utilize our Safe Grip line, which is a non-skid additive, or we can use aluminum oxide. Aluminum oxide is a very hard, fine particulate that is used to increase slip coefficient as well as help with wear resistance.
Additionally you can have something like ESD flooring, or Electrostatic Dissipative flooring. That type of flooring is ideal for data centers or companies that manufacture sensitive electronics that might be susceptible to static charges that could damage them.
Also when it comes to safety we’re protecting the concrete from chemicals and degradation. By utilizing an epoxy or resinous flooring like Tidalstone you’re saving and extending the life of the concrete. A lot of times an epoxy flooring system is simply used to help preserve the integrity of the concrete. That way you’re not having to do these costly repairs because the last tenant, for example, did not have a coating down and that caused the materials or chemicals or exposure to water to rapidly expose the concrete to things that may now require it to be completely removed. That’s a much bigger environmental impact because now we have to cut out the concrete, remove the concrete, pour new concrete. If we utilize a protective coating, we can help eliminate and preserve the life of that concrete so it can go 100 years.
The other aspect of protection is not just for the concrete itself, but in many cases chemical exposure or other types of water can sometimes leach through the concrete. Having a good protective coating like an epoxy system can help prevent chemicals from leaching through and getting into the water or soil if there’s a spill or issue at a facility.
What are the true aesthetic benefits of resinous flooring?
Tidalstone is decorative, and it’s really unlimited what you can do with resinous flooring systems. You can have a standard solid color—a basic monochromatic and even finish—or you can get into something like Tidalstone that has this beautiful terrazzo-esque finish with this variegated, mottled look that’s very natural.
We can also utilize decorative quartz sand blends. We also have standard acrylic chip formulations. We have a metallic epoxy that can create this very nice mottled, dynamic metallic essence.
We can also utilize clear epoxy. In many cases where polished concrete had been the norm or had been specified, we can grind that concrete and refine that concrete, preserve it, saving the life of the concrete, and put a clear sealer over it. Using our clear epoxy or clear polyurethane, we call that a grind and seal. Those are great ways to preserve the look of concrete. By utilizing epoxy polyurethanes and these resinous floors you still get chemical resistance and durability with the look of polished concrete. If a client wants the look of polished concrete, but it’s a restaurant or grocery store, you know they’re going to spill certain things that could possibly stain polished concrete. Resinous flooring gets them the look they want and protects the flooring.
We can also do fun stuff with resinous flooring you really can’t do with other flooring—like we can put logos into floors and clear coat them. We can stain the floor with a decorative stain or add a school logo or corporate office branding. We can use a stencil, paint it, and put a clear coat over to protect that so you have this really nice branding all tied in with the decorative design, as opposed to having a goofy sticker on top of a tile or something that generally will not hold up well.
Can resinous flooring help projects earn LEED points?
Yes. If we’re working with architects and designers, all of our materials in this Tidalstone system meet or exceed VOC requirements. Even in California, where we have pretty much the most stringent VOC requirements, all of our products meet or exceed those. Some may be zero VOC formulations, or some may be very low VOCs.
We also have third-party VOC declarations for these products. That’s going to help with LEED Version 4 Low Emitting. When architects and applicators are looking to get those LEED points and want them for that, one of the critical requirements is that they have that third-party testing done. We’ve gone through, in this case, Berkeley ClearChem Analytical; they’re one of a few third-party VOC testing agencies. We have all that information tested through third-party and listed through their website as well as ours. It’s readily available information so architects and customers can fill out their punch card, finish their projects, and make sure they’re getting those LEED points.
Additionally, it’s just best practice. We’re using products that are less harmful and have less VOCs. In some cases we’re using water-based chemistry and water-based technology, 100% solids. All of these things make for safer installations, less environmental impact, and a better design and function for the finished system.