Story at a glance:
- Restoring a building’s exterior with field-applied coatings saves money, time, and reduces environmental impact.
- Careful selection of the right coating can be the difference between a long-lasting finish and one that fails in several years.
Reduce, reuse, recycle—the three Rs of environmental sustainability offer actionable strategies to help our society save money, energy, and natural resources. They are key tenets of a “circular economy,” which keeps materials, products, and services in circulation for as long as possible.
Exterior restoration projects are an excellent opportunity for building owners to address the “reduce” strategy. As buildings and structures age, their exteriors can take on a lackluster appearance. Time and environmental conditions take their toll, and a once-vibrant exterior becomes faded and degraded. In this situation owners, architects, and specifiers may be tempted to replace facade materials with new, factory-fresh materials—a costly, time-consuming endeavor that diverts old facade materials to landfill.
Restoring a building’s exterior with field-applied coatings is a better option, as it eliminates the expense, business disruption, and environmental impacts associated with removing and replacing facade materials. Moreover, the right exterior coating can provide the same type of fade-resistant performance associated with its factory-applied counterparts.
In warm, coastal areas like Florida, Texas, and California, it’s not uncommon for off-the-shelf or even premium latex and urethane-based paints to fade and degrade after only about five years exposed to high UV rays, high heat, humidity, and salt spray. This coating degradation creates more than just an eyesore and bad curb appeal; it can also expose the underlying substrate to damage. In addition, degraded, chalky paint can be washed off the building surface during heavy rains or power washing, allowing the residue to enter the ground and subsequently contaminate the ground water.
Careful selection of the right coating system and attention to proper surface preparation techniques make the difference between a long-lasting finish and one that fails in several years and needs to be replaced.
Here are five things you should know before you specify to help ensure the sustainability of your next facade restoration project.
1. Coatings are a System
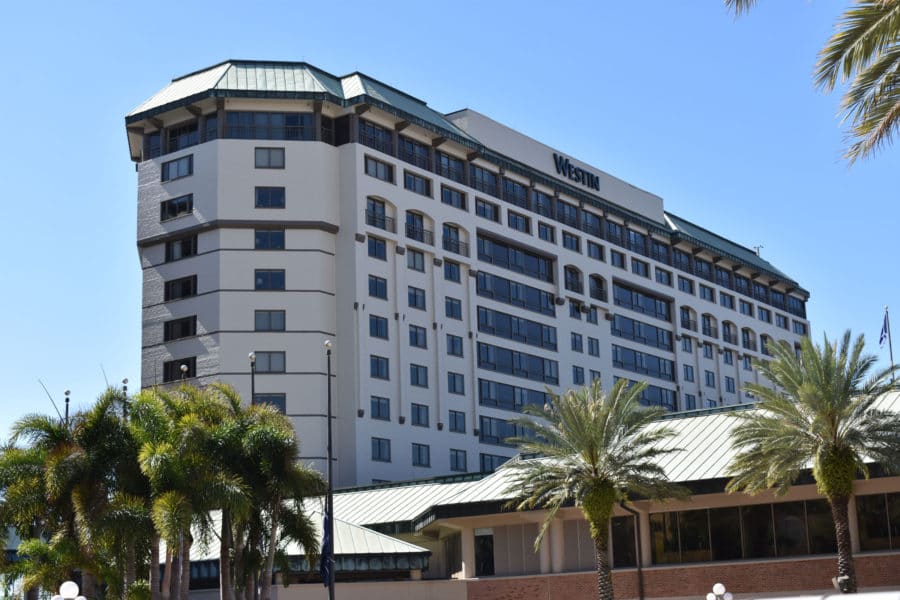
The Westin Tampa Waterside used NeverFade on both the structure’s masonry and aluminum window frames. Photo courtesy of APV Coatings
Building owners and architects are moving away from “off-the-shelf” paint to complete, engineered coating systems that are formulated to bond to a specific substrate. Compatibility among system components—primer and topcoat—and the engineering behind the formulations will help ensure against coating adhesion failure and extend the lifetime of the protective coating.
It’s important to specify a primer and topcoat system from one manufacturer, as they will be specifically formulated and tested for compatibility and inter-coat adhesion. Poor inter-coat adhesion can allow moisture to get in between the primer and the topcoat, leading to blistering or delamination.
While topcoats may get more attention from a curb-appeal standpoint, the quality and performance of coating system’s primer can make all the difference. Primers fill the pores of the surfaces to be coated and increase the adhesion of the coating. A primer coat helps to seal the surface, hide stains, prevent bleed-through, and create a neutral base for any coating color. If the primer formulation is not engineered for the specific surface substrate—a formulation developed for masonry is not suited for steel surfaces—or environmental conditions, pre-existing issues are likely to progress after refinishing. Moreover, the same building material may require different primers based on pre-existing conditions, such as the substrate’s age, type and condition of existing coatings, and the environmental factors the coating will be exposed to after the installation, such as salt and water migration or abrasion.
2. PVDF Binders Create a Tough, Durable Finish
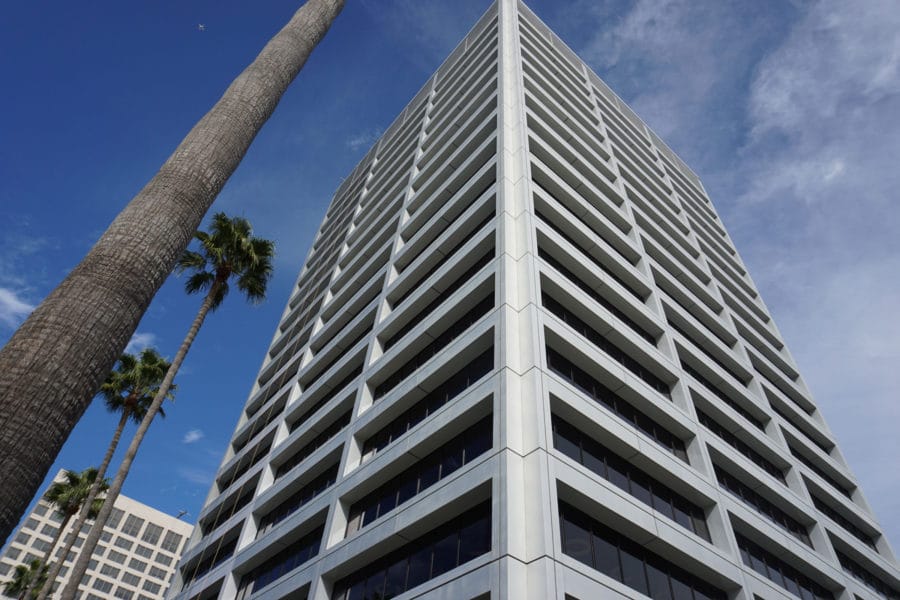
610 Newport Beach, winner of the 2020 Metal Architecture Design Award in the Renovations and Retrofit category, used W-1650 Bonding Primer and a custom metallic NeverFade Metal Topcoat on its anodized aluminum surface. Photo courtesy of APV Engineered Coatings
For decades architects have trusted the long-term, fade-resistant performance of Kynar 500®-based finishes, which are baked onto metal surfaces of exterior building products like aluminum doors and window frames at the factory. Today architects and specifiers can take advantage of Kynar Aquatec®, a water-based PVDF resin similar to solvent-based Kynar 500 but formulated for field applications. The resin is manufactured through an innovative and patented process that uses no PFAS surfactants or any other fluorosurfactants in its ingredients or manufacturing process.
With super-strong carbon-fluorine bonds that do not break down under exposure to the elements, Kynar Aquatec resin-based coatings have consistently demonstrated an ability to resist fading (Delta E < 5) for 15 years or more in high UV settings like southern Florida. They can be applied easily to a variety of substrates, including metals, plastics, wood, concrete, stucco, EIFS and previously painted surfaces, making them ideal for facade and roof restoration. Side by side southern Florida comparisons of Kynar 500 with Kynar Aquatec based coatings for the last 21 years show similar performance with respect to color fade and chalking.
The figure below shows the extent to which UV energy breaks down common coating binders, reducing their mechanical protection properties. Note that PVDF resin has very minimal absorption of UV energy, making it ideal for coating applications needing strong UV resistance.
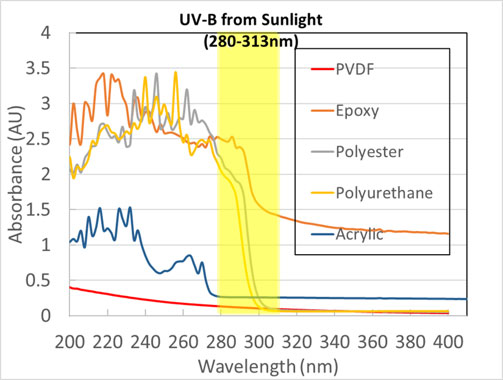
Image courtesy of APV Engineered Coatings
NeverFade® Facade Restoration Coating System from APV Engineered Coatings contain Kynar Aquatec, which when combined with the coating’s complex inorganic pigments, help the coatings resist film erosion, chalking and fading. This long-term performance allows APV to offer a 15-year product-and-labor guarantee that the coating will not fade by a Delta E of five or higher. Transferable to future building owners, the guarantee is unique to the architectural coatings industry.
3. VOCs are a Concern Even Outdoors
While concentrations of volatile organic compounds (VOCs) are consistently higher indoors, they also are a concern outdoors, where once in the atmosphere, they react with oxygen to produce ozone, a key component of smog.
VOCs from coatings and other construction materials can be a nuisance to construction workers, building occupants, and passersby and lead to potential health effects such as eye, nose, and throat irritation; headaches; nausea; and damage to the liver, kidneys, and central nervous system.
In general, higher concentrations of VOCs are found in extreme-durability solvent-borne polyurethane and acrylic topcoats and pretreatment wash primers, where they run in the 600 to 700 grams per liter range. Low-VOC water-based coatings typically contain less than 100 grams per liter, while 5 grams per liter is considered “very low” or “zero.”
With less than 50 grams/liter of VOCs, NeverFade is one of the very few high-performance coatings to meet SCAQMD Rule 1113 environmental regulations. It also meets 40 CFR Part 59, Subpart D, national Volatile Organic Compound Emission Standards for Architectural Coatings (which is capped at 380 grams/liter). The topcoat’s complementary primers also contain less than 50 grams/liter of VOCs.
Low VOCs are an important consideration when buildings are occupied during the coating project, especially when air-handling units bring outdoor air inside. For example, when owners of a luxury high-rise condominium in Florida wanted to improve the curb appeal of their building with a refresh of its exterior coatings, they chose NeverFade Coatings for their low VOC content and low odor that would keep tenant inconvenience to a minimum. Schools and hotels have made the same purchasing decisions, allowing coating projects to proceed and business to be conducted as usual while buildings are occupied.
4. Proper Surface Preparation is Crucial
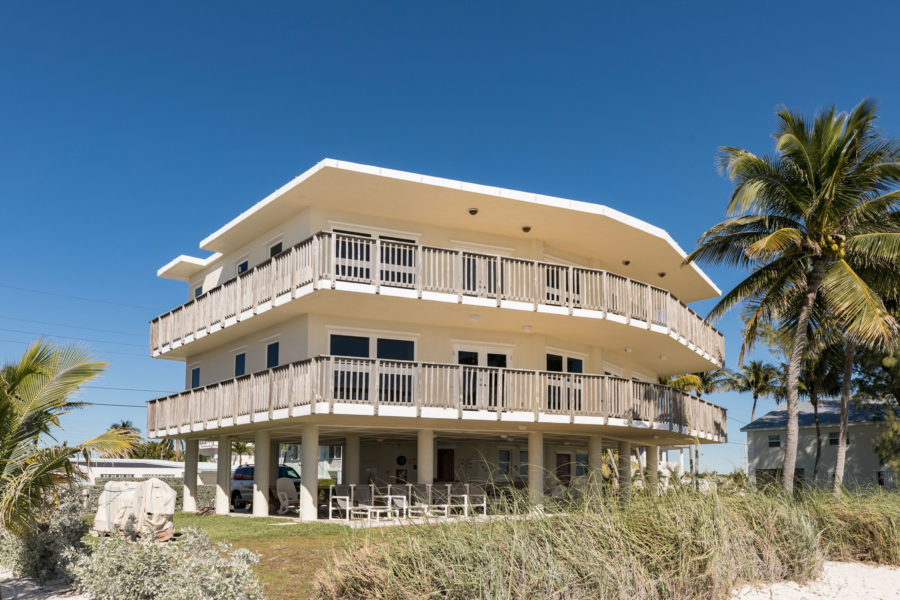
Photo courtesy of APV Engineered Coatings
The process of applying a protective coating to a building’s exterior is more complicated than it might seem—if it is done right. Simply pressure-washing the facade and then painting is not nearly enough.
A careful pre-job inspection should be conducted to assess the structure’s surface conditions and presence of environmental contaminants that need to be removed. Before applying the primer, all areas should be examined for pre-existing coating defects such as holidays, crazing, cracking, blisters, efflorescence, blushing, chalking, etc., as well as surface or substrate defects like improperly welded areas, cracks, mold growth and corrosion.
Proper mitigation should be taken to resolve all issues using SSPC, NACE or ISO standards. Surfaces should be completely cleaned by blast, power tool, or hand tool method as well as solvent wipe cleaning to remove all contaminants including chlorides, sulfates and nitrates, oil, grease, soil, dust, and mill scale. Additional surface preparation guidance should be available in the primer manufacturer’s Field Coatings Guide, technical data sheet and specification document.
A coating’s curing ability, lay down/aesthetics, and dry film thickness (DFT) are impacted by the building’s micro-climate. Coatings applied in poor environmental conditions can risk the long-term performance of the coating and negatively impact its lifecycle. Application will run more smoothly and lead to better results if the coating system has early water resistance and the ability to be applied in a range of temperature and humidity conditions.
Installation mockups can help to ensure issues are addressed before they become costly mistakes requiring re-work. Ultimately, if you’ve done a thorough pre-job assessment and selected a knowledgeable coatings contractor that works directly with the manufacturer, issues should be minimal to nonexistent.
5. Thinner Can Be Better
Applying the primer uniformly and properly is critical, as a corrosion reaction can happen in an area smaller than a pinpoint. To ensure proper primer thickness, applicators should use a wet film gauge and record readings from multiple locations immediately after application. The target wet and dry film thicknesses are based on the solids content of the primer and can be found on the manufacturer’s technical data sheet.
Excessive primer on the surface may result in runs, sags and weak spots, as well as delay dry time and potentially create inter-coat adhesion problems. On the other hand, skips and holidays can result when film thickness is too thin, which could lead to corrosion or adhesion issues from exposing the substrate to the topcoat or even the elements. With uneven film thickness, striping and banding as well as mottling can appear, impairing the overall aesthetic, even after the top finish is applied. Dry film thickness readings are also advised using a relevant DFT gauge per SSPC-PA 2. Record DFT in five locations on the surface, three times in each location, then compute the adjusted average to learn if the coated area is in spec.
NeverFade Coatings keep a nice wet edge, with no hard-to-blend roller marks. In addition, the coating can be applied at a much lower thickness than acrylic-based coatings, which need significantly higher thicknesses than PVDF-based coatings to offset film erosion over time. This reduces consumption of coating product, packaging, and related resources.
Keeping Coating Color & Vibrancy
Thanks to high-performance, PVDF-based coatings, architects are better able to design with and specify bright and bold colors, secure in the knowledge that those colors will remain true for the long term. APV Engineered Coatings takes a unique approach to color. While some paint manufacturers tout their “color of the year” and push customers to their color vision, APV Engineered Coatings lets the customer decide. Every single batch of our NeverFade Coatings is custom formulated to match the customer’s exact color specifications, allowing the building to reflect the owner’s brand standards, school colors or any color aesthetic they desire.