Story at a glance:
- Exterior paints and coatings protect facade materials from damage caused by UV rays, chemicals, mold, and other environmental and weather conditions.
- Off-the-shelf paints may come with a lower initial price tag, but they also come with a shorter lifespan.
- Frequent repainting—needed every five to 10 years when latex- or urethane-based formulas are used—is costly and disruptive.
Exterior paints and coatings play both decorative and protective roles on a building’s facade. The right coating, when expertly applied, delivers a curb appeal that reflects the occupants’ tastes and the building’s purpose; think bold, primary colors for a school, softer sand-and-sky colors for a coastal home, or sleek, metallic hues for a high-tech office.
Beyond aesthetics, exterior paints and coatings protect facade materials from damage caused by UV rays, rain, humidity, windborne particles, chemicals, mold, mildew, and other environmental conditions. Without protective coatings, facade materials can become exposed to the elements, eventually degrading to the point of structural instability. At that point they likely would need to be replaced—a costly, time-consuming and disruptive endeavor that adds to our globe’s landfilled waste stream.
Faded and degraded building facade materials are more than just an eyesore. They are also an expensive maintenance headache and can pose a threat to the environment. Therefore, building owners, architects, and project specifiers want exterior coatings to provide long-term protection. Now they have a new tool—the Society for Protective Coatings (SSPC) Paint 47 Standard—to help them determine how well the field-applied coatings they choose will stand the test of time.
When Coatings Fade
Commodity, off-the-shelf paints may come with a lower initial price tag, but they also come with a shorter lifespan. Even high-performance paints can quickly chalk, fade, and degrade, especially those with deep colors and bright hues. Chalking, caused by a physical breakdown of the coating’s polymer, creates a white, powdery residue that compromises the coating’s appearance and eventually gets washed off into the ground, where it can serve as a pollutant. A chalked surface also becomes a food source for mold and mildew growth and makes conditions ripe for dirt collection. Chalking isn’t always easy to see on white or off-white coatings, but it is quite obvious on darker colors as it changes their hue.
Chalking is a common problem, even with high-performance urethanes and acrylic latex paints, and especially in climates such as South Florida and Arizona, where their typical lifespan is about five years. Coating systems formulated with polyvinylidene fluoride (PVDF) resin, on the other hand, deliver longer-term performance—more than 20 years. This tough, engineered thermoplastic polymer promotes excellent weatherability, color retention and durability thanks to carbon-fluorine bonds that do not break down under exposure to the elements.
First Standard for Dark, Saturated Colors
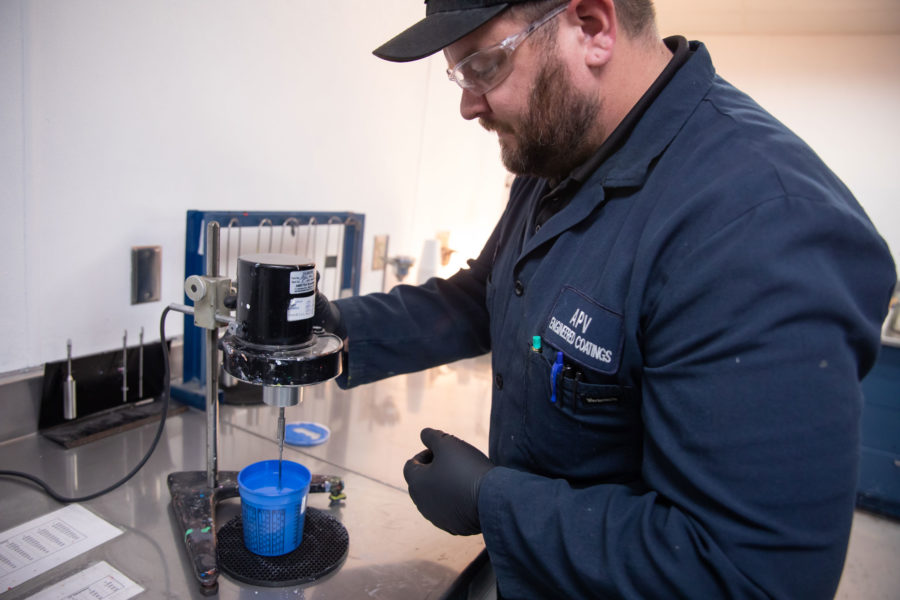
Mixing a sample batch of NeverFade Metal topcoat. Photo courtesy of APV Engineered Coatings
Specifiers of protective and architectural restoration coatings have several standards against which to measure coating performance (see table). However most, including the traditional standard for field-applied topcoats, SSPC Paint 36, were written around conventional 2k urethane technology and tested only in white. Even the Master Painter Institute (MPI) 311/315 Standard used by the federal government does not address the needs of project specifiers looking beyond white, acrylic-based paint technology.
The industry’s need to validate color retention in high chroma or saturated and bright colors prompted efforts by the main protective coatings trade association, the SSPC, to develop a new standard to address the gap. (SSPC has recently merged with NACE International to form AMPP: The Association for Materials Protection and Performance.) The SSPC’s C.1.8 Fluoropolymer Topcoats Committee reached out to asset owners, architects, coating and raw materials suppliers, municipalities, and other stakeholders to ensure the new standard would meet their needs for color and gloss retention in “safety” and dark colors.
The resulting new SSPC Paint 47 standard—formally known as SSPC-Paint 47-2020, Highly Weatherable Fluoropolymer Topcoat, Performance Based—issued at the end of 2020. It is the first standard explicitly designed for high-performance, field-applied coatings in darker and saturated colors. Coatings meeting the requirements of this new standard will provide superior color and gloss retention properties when used as a topcoat over multiple substrates, including metals, plastics, wood, concrete, textiles, and even some previously painted surfaces. Because chalking is limited to negligible levels under the performance standard, asset owners can be ensured the coating will remain intact for the long term and not be dispersed into groundwater.
Accelerated Weathering Tests
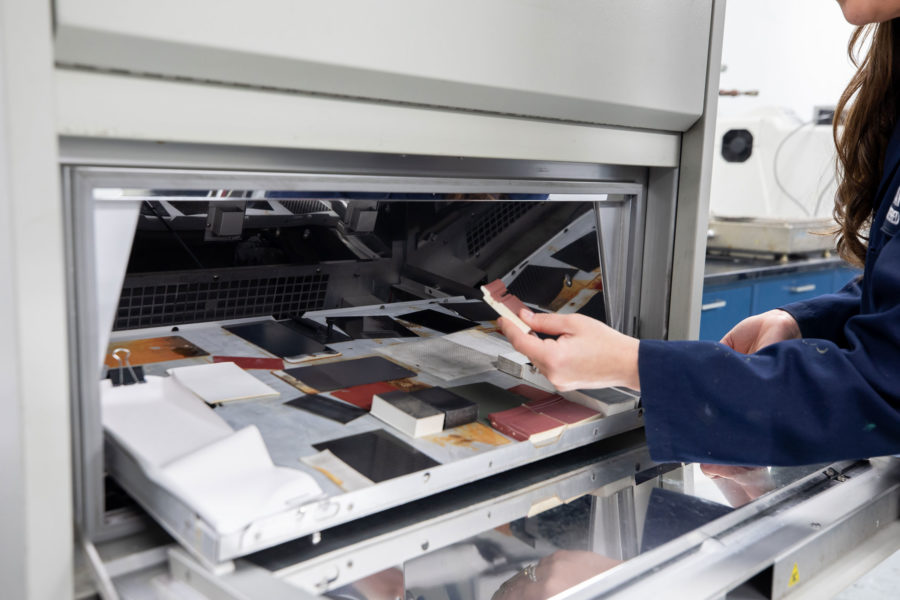
Reviewing samples from the Xenon weathering test chambers. Photo courtesy of APV Engineered Coatings
Part of the SSPC committee’s challenge was identifying a set of accelerated weathering test conditions to allow coating formulations to be qualified more quickly than possible with traditional outdoor service life tests, which can run for 10 to 50 years. This would allow project owners to more easily specify coatings with specific pigment combinations for their projects.
The committee followed the tenet that identifying an appropriate performance-based standard for low-color-fade fluoropolymer coatings should be restricted to specific fluoropolymer resin chemistries with proven performance. Moreover, the accelerated testing criteria for each chemistry type should be selected based on historical data for how commercially relevant coatings perform under natural as well as accelerated conditions.
Anonymized, round-robin weathering tests were conducted at two independent laboratories. Thirteen coatings (representing both fluorinated and non-fluorinated resin systems) from 10 manufacturers were tested in four reference colors: white, NTPEP gray, mid-tone blue, and safety blue.
The most discriminating set of accelerated test conditions identified by the round-robin testing used a standard fluorescent test cabinet with aggressive UVB-313 bulbs, in a legacy cycle for 4000 hours (about six months). In that time, those accelerated test conditions accurately differentiated between high-weatherability fluoropolymer formulations and conventional SSPC Paint 36 (2-component polyurethane) and MPI 311 (latex) formulations, as shown in the Figure below. The accelerated test also uses virtually the same performance criteria specified in the well-recognized AAMA 2605 standard for factory-applied coatings undergoing a 10-year Florida exposure:
• Gloss retention >50% (ASTM D523)
• Color retention Delta E <5 units (ASTM D2244)
• Chalk rating > 8 (> 6 for whites) (ASTM D4214 Test Method A, in which 10 indicates no chalking)
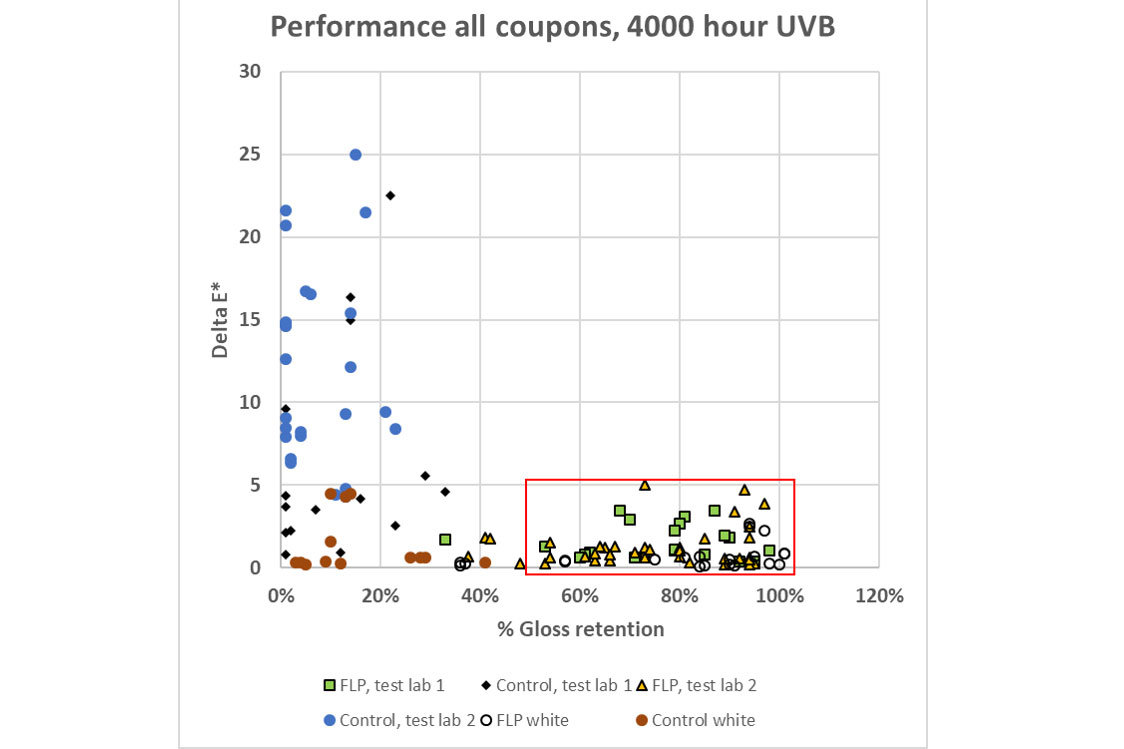
Graph courtesy of Kurt Wood
Specifying for Sustainability
Frequent repainting—necessary every five to 10 years when latex- or urethane-based formulas are used—is costly and disruptive to building occupants and visitors. It sometimes requires old paint to be stripped off and disposed of as solid waste. It also requires the manufacture, packaging, and shipping of new paint—activities that are energy- and water-intensive and further add to the solid waste stream. Plus, if the paint is solvent-based, it emits volatile organic compounds (VOCs) during the drying process, which can be both a nuisance and a health hazard as well as contribute to the formation of greenhouse gases.
Water-based coatings with long-term resistance to fading and chalking have a lower impact on the environment. They are known to be lower in VOCs, hazardous air pollutants and odor, and applicators can use water instead of solvents or paint thinner to reduce the product as well as clean their hands and flush equipment.
One such coating, which meets Paint 47 specifications, is the NeverFade® Facade Restoration Coating System from APV Engineered Coatings. NeverFade Coatings contain Kynar Aquatec® PVDF latex, a water-based PVDF resin similar to the solvent-based Kynar 500® finishes trusted by architectural metal component OEMs for 50 years. Moreover, the resin is manufactured through an innovative and patented process that uses no PFAS surfactants or any other fluorosurfactants in its ingredients or manufacturing process.
Combined with the coating’s complex inorganic pigments, the Kynar Aquatec® resin helps NeverFade coatings resist film erosion, chalking and fading, allowing APV to offer a 15-year product-and-labor guarantee that the coating will not fade by a Delta E of five or higher. Transferrable to future building owners, the guarantee is unique to the architectural coatings industry.
Of note, NeverFade is one of the very few high-performance coatings to meet strict SCAQMD Rule 1113 environmental regulations in California. APV has long been committed to producing environmentally conscious products and sourcing responsibly and will re-engineer or custom develop formulations to meet EPA restrictions or other environmental concerns.
As with any coating, the long-term performance of NeverFade and other formulas meeting Paint 47 specifications depends on proper planning. Topcoats are normally used as part of a multi-layer coating system. Each coating in that multi-layer system needs to be designed to be compatible with the full coating system, for the application in which it is used. Formulating the coating’s ingredients to bond to the specific substrate helps ensure against coating adhesion failure and lengthens its useful lifecycle.
Inadequate surface preparation and improper primer application are other ways through which a coating system can fail, so proper SSPC, NACE, ISO, and/or ASTM practices for surface prep and profiling should be employed. The primer must be engineered to bond well to the substrate while considering pre-existing conditions. Installation mock-ups can help to ensure issues are addressed before they become costly mistakes requiring re-work.
NeverFade Coatings with Kynar Aquatec PVDF resin also can be formulated in custom colors, from whites and metallics to bold, bright hues like those covered under Paint 47, giving building owners, architects, and project specifiers a way to colorfully and sustainably lengthen the life of their building facades with performance they can trust.
Lon Bauer contributed to this article.