Story at a glance:
- Gensler is driving toward a zero carbon impact portfolio by 2030 and released new material standards in early 2024.
- Manufacturers like Autex Acoustics seek to move beyond carbon neutral with pelletization and rethinking the resources we already have.
Forget carbon neutral. Autex Acoustics wants to be “nature-positive.”
“The purpose of Autex is to care for people, and to do that we have to make sure the world we live in and the resources we use are looked after and valued because they’re finite,” says Jonathan Mountfort, creative director at Autex Industries, based in New Zealand. Mountfort oversees product development and new product design as well as sustainability and compliance.
Autex aims to become a nature-positive company by 2036, emphasizing regenerative processes and paying close attention to ecological outputs. Since its start in New Zealand in 1967 the company has pushed the envelope for what non-woven architectural textiles and modern acoustic solutions can be. The third-generation family-run manufacturer has solidified itself as an award-winning global design practice that innovates to transform spaces. The company has expanded to serve more than 18 markets, plus manufacturing and finishing networks in Australia, the UK, and the US. In 2024 they brought their pelletization technology, which aids in recycling Autex products, to the US.
Partners for Positive Change
Currently Autex Acoustics is looking to scale up work like what they are doing in the US. “The pelletization process was developed in New Zealand and trialed and then taken to the States and implemented there, albeit at a very small scale,” Mountfort says.
Autex innovated the world’s first pelletizer on its journey to circular manufacturing when it couldn’t find a simple effective process already out there. “The thought behind the project was, if this textile has come from a solid material, then a truly circular product should be able to return to a solid material,” Mountfort says.
If we get all the technologies right and the material selection correct, we can live in partnership with nature, as opposed to on top of nature.
In California Autex takes its offcuts and finds other uses for them. “There’s a partner less than 20 miles away from our Riverside, California facility where our pelletizing machine is that we’re already talking to to start doing it for America.” Now they want to scale up and make pelletization available to even more people.
“There is potential for a company to make product that makes the world better and therefore usher in a life of abundance,” Mountfort says. “And we don’t have to do that in a way that’s ridiculously restricted, because if we get all the technologies right and the material selection correct, we can live in partnership with nature, as opposed to on top of nature. I fully believe it’s possible.”
The Role of Pelletization
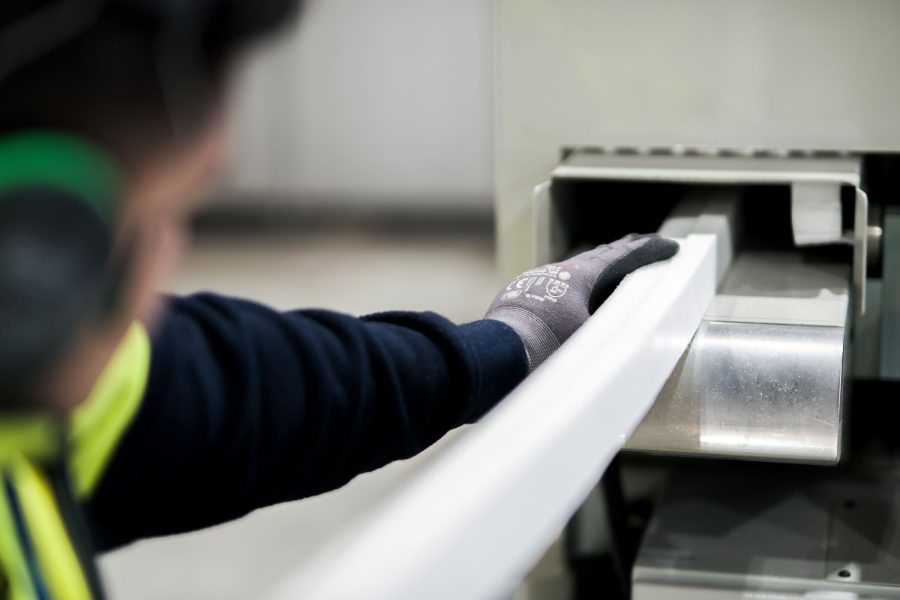
Photo courtesy of Autex Acoustics
Pelletization provides a tangible way to manufacture products in a circular way. Collecting used products or material offcuts is one thing, but transforming them into a useful product extends the material life cycle and actively reduces waste in the landfill, Mountfort says. Because the product entering the Autex Pelletizer is made of Autex material already, solutions like the company’s SpinFix adhesive-free mounting kits or Frontier End Caps (accessories made from pelletized PET) can be recycled with Autex products or through standard curbside recycling processes globally.
“Now that we have rolled this technology out to each of the countries we operate in, we want to ensure we continue to improve, increase, and partner with other businesses in the industry to scale the capacity. Eventually we can build out an industry solely fueled by reclaimed materials that are re-manufactured into high-value long-lasting products,” Mountfort says.
He says the scaling up and continuing to evolve the technology is one of the most important things that could be done in the industry today. “It’s acoustics agnostic. It’ll work for fashion. It’ll work for building products. It’ll work for other textile product streams. It will give a pathway to a whole host of material out there that doesn’t, at present, have a solid pathway, and it will increase the value of that material through it.”
The Possibilities are Endless
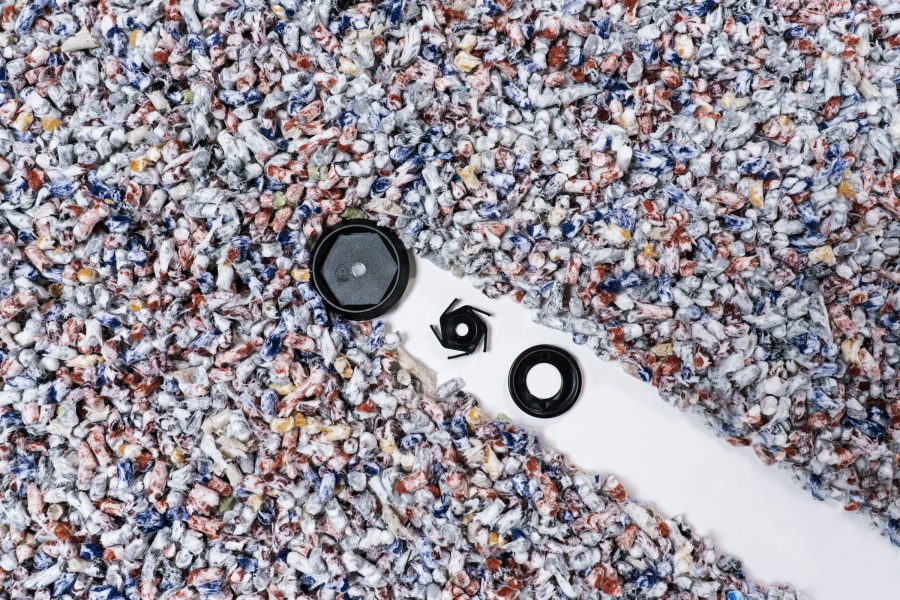
Photo courtesy of Autex Acoustics
Already some recycling companies take material and recycle it “in a really sort of blunt form,” Mountfort says. He points to the example of mining cities and says the possibilities for new material—even right from our landfills—is tremendous. “There’s phenomenal opportunity for a company to become a modern Industrial Revolution version of a mining company, where they mine cities and take minerals and raw product from feedstock that we would now consider waste. There’s massive opportunity for landfill mining, for city mining, and taking usable materials and adding processes to turn those into feedstocks for other industries.” Conversations around turning what was once considered waste into something useful in a low or zero carbon manufacturing way are happening now.
All of Autex’s products are carbon neutral already, and the company established a zero-waste product line back in 1990, before most manufacturers took the concept of zero waste seriously. But what’s next?
The research and development Autex is known for reaches far beyond acoustic solutions, as the built environment at large can benefit from its circular design strategies. “Acoustics are just our vehicle,” Mountfort says.
“If we dial in and focus on acoustics, that’s part of a building that’s not really focused on at the moment, it’s not really taken into account across the world and building code and all that’s required to make a building habitable for people, but we feel it’s so important. The ability to hear and be heard—that’s a fundamental component of what it is to be human.”
The concept of waste doesn’t exist in the natural world, Mountfort says. “Everything has a pathway back into another form.” And yet, we as humans take a material, make a product, use the product, throw it away, and it ends up in a pile of junk. “It’s insane. If you actually value the material, put the value not on the product; put the value on the material. Then all of a sudden that’s got value through the whole chain, and therefore the concept of waste is removed. It’s a simple shift, but complex to implement.”
An Architect’s Perspective
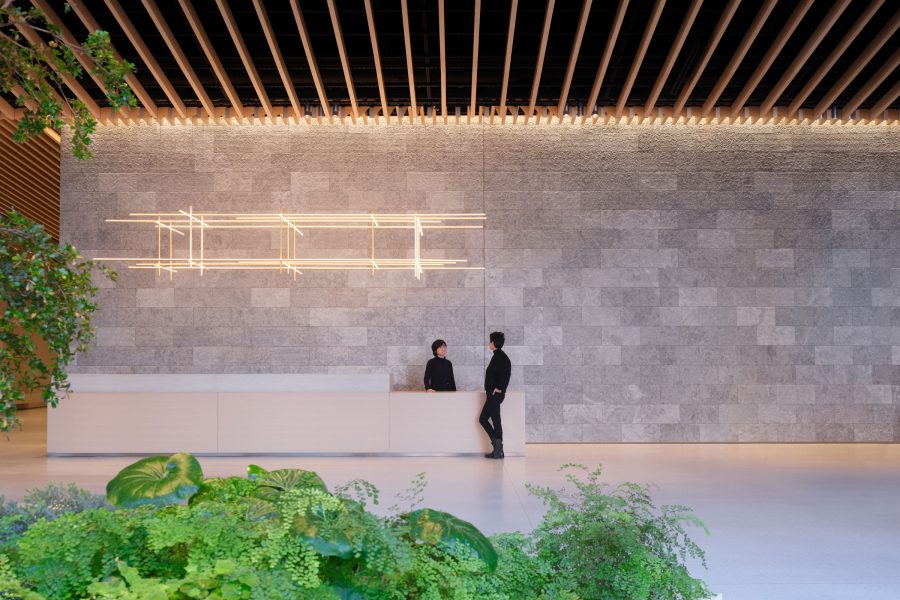
At 200 Park Avenue Gensler worked with client Jay Paul Company to design a fully electric, 19-story office tower in an underdeveloped corner of downtown San Jose, California. The project team emphasized sustainable materials at every turn. Photo by Jason O’Rear
Autex already works with many sustainable leaders in the industry, including architecture giant Gensler. The firm itself is well on its way to carbon neutrality in all of its work by 2030.
“We’re making progress on our goal, which would be described as a zero carbon impact portfolio in 2030, and that’s a big investment,” says Stephen Katz, a technical director in Gensler’s Chicago office. “It’s a big leadership moment for us.”
Katz says the next step toward zero carbon requires better data collection and tools for tracking embodied carbon from the built environment. That’s part of why Gensler released its new material standards in early 2024. Starting with the most common, high impact product categories, the GPS, or Gensler Product Sustainability Standards, program is a way to establish sustainability performance criteria. It all starts with managing the data so you can better understand it and plan for a greener future, he says.
Reuse is one area where Katz sees room for improvement in the built environment. “It’s a really interesting challenge, how to reuse existing materials and furnishings,” he says. “It’s going to take some outside the box thinking in terms of the construction procurement process.”
He says this new approach in the industry would have enormous carbon savings. “For us we find that has a lot of potential, and we’re really excited about that.”
Having the right partners and a seat at the table is important when it comes to making big moves in the industry. Autex is already part of Gensler’s standard product library as a carbon neutral solution, but at a higher level they’re in discussion about a carbon negative product, too, Mountfort says. “I’m really keen for the uptake of this type of thinking to be connected to the material and the product, shifting away from credits and offsets and connecting the environmental measurement to the material,” he says. “We’ve got a carbon neutral company here producing carbon neutral products.”
Actions Over Words
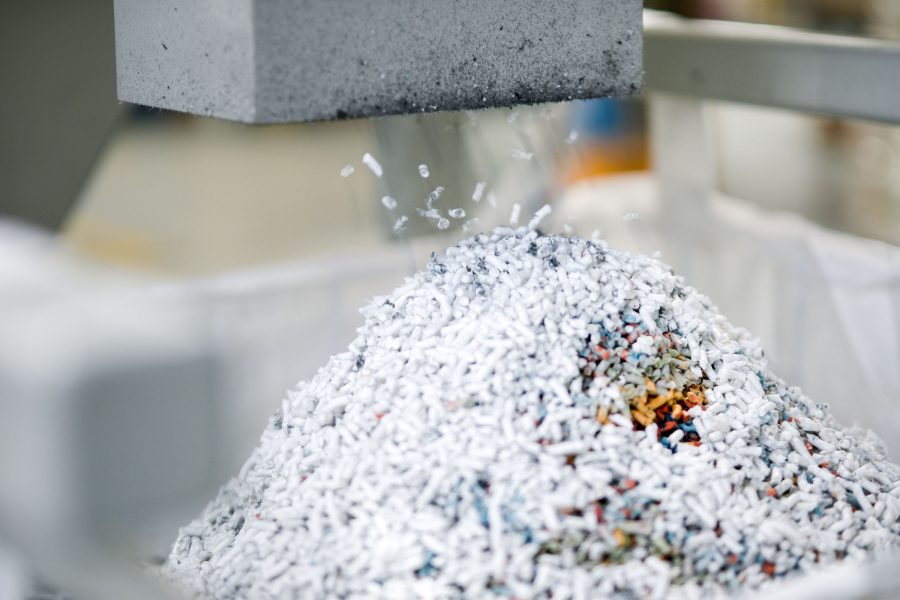
Photo courtesy of Autex Acoustics
When it comes to specifying recyclables, though, Mountfort urges attention to detail. “Just because it is recyclable doesn’t mean it gets recycled. It’s on our architects and the people going into fitouts to consciously work through their demolition plan, because when a new company moves in, they’ll walk in with their architect and they’ll go, ‘What can we do here? We need to make it look like x, y, z.’”
What if, instead, they walked in and asked, “What can we reuse?” he says. “That would massively reduce the global warming potential and the environmental load that construction and fitout has on our planet.”
All of this is a massive opportunity to create new industry and more than economically viable businesses.
And while recycling has been around for decades, we’re only now living in an age when people expect things to actually be recycled, Mountfort says. “It takes that long for a technology to be taken up. Initially people resist it.”
He says the next phase of technology is reliance, and that’s where he expects society to move in the next five to 10 years, as the world begins to rely on the recycled product stream working. Still, Mountfort says massive education is needed across the industry. Not everyone knows plasterboard can be recycled, for example, he says. “It’s a really useful material. All of that has to be thought about.”
“All of this is a massive opportunity to create new industry and more than economically viable businesses being made out of mining our cities and mining rubbish,” Mountfort says. “Focus on it. Get the investments going, and don’t try and tackle the whole thing by yourself. Everybody has a part to play. Look at that pathway, and start filling gaps.”