You can find them on skyscrapers or single-family homes. Gas station canopies and stadium scoreboards. Explore contemporary buildings around the world, and you’re bound to see many examples of a transformational architectural material—although you might not realize it.
Used to clad entire building envelopes or to provide simple detailing support, sustainable metal composite material (MCM) is used in all types of architectural projects. For more than 50 years these products have provided highly engineered solutions for even the most challenging construction, and they are a favorite across the industry. MCMs have reshaped skylines, enabling architects to realize visions that were previously impractical or wholly impossible less than 50 years ago.
What is MCM?
Durable, low-maintenance, and easy to fabricate, sustainable metal composite materials, or MCM, provide versatility for facade design.
MCM is produced by bonding thin sheets of metal to either side of a thermoplastic core with heat, tension, and pressure. It provides the rigidity of plate metal without the weight or the distortion referred to as oil-canning.
Often made with painted or treated aluminum, also known as ACM, composites are also produced with zinc, copper, stainless steel, and titanium, often referred to as natural metals. Collectively we use the term MCM to talk about all metal composites.
A Little History
MCM was introduced in 1969. From that time, adoption grew exponentially as architects, fabricators, and building owners discovered the functional advantages and beautiful possibilities of this remarkable new material.
Manufacturers have continued to innovate with MCMs since they were first introduced a half-century ago. Advancements in image transfer have enabled realistic patterns of stone or timber to provide the aesthetic beauty of nature without the limitations of weight, maintenance, and cost. Pigmented zinc and tinted anodized aluminum let the brilliance and texture of the natural metal shine through subtle hues. Precision color matching with advanced fluoropolymer paints gives the color you want with a warranty of up to 30 years. Even fabricators are pushing the limits, creating complex forms to address new challenges in the areas of acoustic design and extreme weather conditions. It is these new possibilities that have revolutionized the experience of modern architecture, transforming cities around the world in our lifetimes.
How It’s Made
Rigid, lighter, flatter.
MCM sheets are manufactured in a process using two thin skins of prefinished metal—often aluminum. Natural metals like copper, zinc, stainless steel, and titanium are also available. The metal skins are continuously bonded under pressure and heat to an extruded thermoplastic or mineral core. No glues. No adhesives. The standard product features metal skins 0.02″ (0.5mm) thick. Heavy-duty 0.032″ (0.8mm) skins are also available.
The core produces a sheet that is lighter in weight when compared to solid plate metal and easy to fabricate, flat, and durable. The thermoplastic core can be a traditional PE or fire-resistant, which is required for buildings over 40 foot from grade. The finished product is available in thicknesses of 3mm, 4mm, or 6mm, with 4mm being the most commonly used. Standard panel dimensions are 50 inches or 62 inches wide and 146 inches or 196 inches long, with custom sizes also available.
Painted aluminum composite material (ACM) is coil-coated using an advanced die coat process or a reverse roller coater. Most finishes incorporate a fluoropolymer paint system such as FEVE or PVDF. These finishes provide a range of colors and glosses unmatched by any other architectural coating.
To protect and beautify the aluminum skin, ACM is finished with a primer system on both sides and a color coat on the outward-facing side. Some finishes also have an additional clear coat to enhance and preserve a special effect, such as a metallic or prismatic look. Another option is to brush, polish, or anodize the aluminum surface itself to protect the resulting effect with a clear coat.
When installed on a building, these corrosion-resistant skins are visually indistinguishable from solid sheets of the same metals. Copper and zinc develop a natural patina over time, while stainless steel and titanium maintain their initial appearance indefinitely.
Virtually Any Finish
The range of possible finishes is spectacular. Choose from solids, micas, metallics, prismatics, decorative metals, shimmer effects, and even realistic stone or timber patterns with the advent of advanced image transfer processes. It’s even possible to provide a multi-color finish on a single panel.
If a standard finish doesn’t quite capture the architect’s intent, MCM manufacturers can custom-match virtually any color imaginable. Corporate identity programs offer the exact colors you expect to see in the buildings that represent scores of internationally known brands.
They are easy to clean without the need for harsh chemicals, and they are warranted not to fade, crack, or peel for 10, 20 or 30 years. They’re designed to make any imaginable vision vibrantly real and to ensure the initial look and quality endures for the life of the building.
The finish possibilities of MCM have revolutionized the look of today’s most eye-catching buildings. Gloss ranges from 6 to 70 allow for understated matte and the most opulent high gloss in shades across the spectrum. MCM can shimmer with special effects and prismatic finishes can even change appearance depending on the viewing angle. Printed patterns create the look of marble and timber without the cost, weight, or maintenance.
Endless Fabrication Possibilities
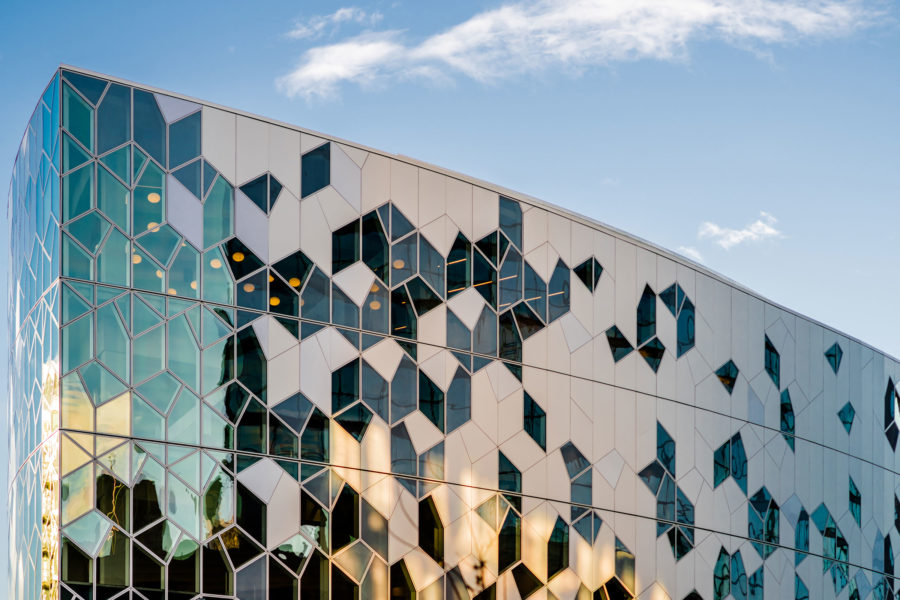
Interspersed with the glass and natural wood accents, ALPOLIC MCM creates a lace-like effect across the building’s facade. Photo courtesy of MCA-ALPOLIC Division
MCM can be used to create a practically unlimited world of complex forms and shapes. These composite materials are far more versatile and easier to fabricate than solid sheet plate metal. Cutting, grooving, punching, drilling, bending, rolling, and many other fabrication techniques are easy to perform using ordinary woodworking or metalworking tools—with no special tools required.
The thermoplastic core makes MCM far lighter in weight than sheet metal, with no loss in rigidity. Composite materials are more affordable, easier to install, and they offer superior flatness, durability, stability, vibration damping, and ease of maintenance. Sheet metal tends to distort, or “oil can,” due to differential expansion and contraction in changing weather conditions. MCM are impervious to this effect, remaining flat and stable season after season—even in the harshest climates.
The superior fabrication capabilities of MCM enable architectural possibilities ranging from advanced rainscreens designed to withstand hurricane force-winds to incredible angled, radiused, and even origami-like forms that would be prohibitively expensive or outright impossible to create using other materials.
Reputable MCM manufacturers will produce sheets that are trimmed, squared, and with a protective film that performs double duty, protecting the finish as well as providing directional arrows for installation assistance. Materials are primed on the unfinished back for additional protection. Quality production operations ensure sheets are shipped in custom-built 6-sided pallets, sized to each order, to mitigate potential damage during transport. Materials can be flipped to order, delivered with the finish side facing up or down as requested. Premium MCM can be easily formed into complex shapes, challenging curves, and fit numerous installation systems.
How MCMs Contribute to Sustainability
All ALPOLIC materials are designed, manufactured, and supplied with sustainability in mind. The high-recycle content of our MCM can support LEED projects looking to qualify for an Innovation credit. Most architectural stock colors earn a “cool” rating from the Cool Roof Rating Council (CRRC) by reflecting heat instead of absorbing radiant energy, reducing energy usage.
In addition, MCM manufacturer ALPOLIC uses a factory-applied die-coated paint system that virtually eliminates harmful VOCs before they enter the atmosphere. Precision die-coating also creates less paint waste and promotes sustainable manufacturing.
At ALPOLIC we’re committed to transparency in the manufacturing industry, supporting the adoption of Environmental Product Declarations and being the first in the industry to promote Product Transparency Declarations. Manufactured in our American headquarters in Chesapeake, Virginia, we actively strive each day to reduce our energy consumption and environmental impact.
Our Operation Encore program encourages new and innovative uses for expired MCM and is a testament to our commitment to end-of-life recovery. Components accepted through this recycling program are distributed to their appropriate industry recycling streams and featured in a variety of community and nonprofit projects.
Consider the Advantages
MCMs provide superior flatness, stability, fabrication ease, and long-term performance. They’re available in an inspiring variety of finishes and colors. They’re exceptionally strong yet light, with only one-fourth to one-third as much metal content compared to 1/8″ sheet metal. They’re also more affordable and environmentally sustainable.
Getting the right look that lasts starts with a great finish. These innovative products meet the AAMA 2605 standard, have built-in graffiti resistance, and are easy to clean and maintain. Quality composite panels can come with finish warranties of 10, 20, or 30 years and deliver the look, performance, and longevity every building owner deserves.
Sustainable MCM is made from highly recyclable materials that support efforts in LEED certification. Our accessible American manufacturing headquarters provides quick service and Made in the USA products on-demand. In as little as 1,000 square feet, affordable MCM can be produced to custom order with manageable lead times, but sometimes faster is better. With more than 100 finishes in stock, these premium materials are ready to deliver exceptional results.
MCM manufacturers should be there through the entire process, just a call away. Manage tight lead times with responsive customer support, order free samples and literature for your design board, and reach out to the manufacturer’s technical service team to get reports like the EPD, PTD, or SDS or to help navigate specifications. From the regional sales manager to the quality assurance department, find a support team that is standing by for your toughest questions.
Building design comes with several considerations and design challenges. MCMs offer a versatile, sustainable, and cost-effective solution. Build your next project with the help of metal composite materials. You can request samples here.