Story at a glance:
- IMETCO partnered with European ceramics industry veteran Gresmanc Group’s Favemanc.
- IMETCO added TAJO natural clay-based cladding to its facade options to meet the growing demand for aesthetically pleasing, ventilated facades.
- A well-chosen rainscreen system reduces reliance on sealants while providing a hygrothermally designed air-water barrier, continuous insulation, secondary structural framing, and a vented cavity.
When it comes to green building techniques, weather is often more foe than friend. From high winds to blistering sun, the exterior of any building must be able to withstand all environmental extremes to protect both occupants and structural integrity over time. And nothing can be more damaging to a building than water. “Traditionally, building facades were all sealed from outside in to prevent any kind of water leakage,” says Jonnie Hasan, director of engineering and sales support at Innovative Metals Company (IMETCO), a leading US manufacturer of premier metal products for the building envelope. “However, sealants over time can deteriorate or break, making building facades leaky.”
Leaks not only damage structures. Water seeping into buildings can promote mold growth, encourage insect infestation, and impact the lived experience of occupants. For green builders, creating an exterior barrier against weather that is both strong and sustainable, beautiful and affordable, energy-efficient and effective, is top-of-mind when planning any project.
Enter IntelliScreen rainscreen systems. Although rainscreens are a time-tested building practice and can often last many years—if not generations—not all rainscreens are made equally. And not all rainscreens can effortlessly integrate with some of the most sustainable, highly customizable cladding options—such as TAJO Ceramic Facade systems.
What is TAJO? Partnering with European ceramics industry veteran Gresmanc Group’s Favemanc, IMETCO added TAJO natural clay-based cladding to its facade options to meet the growing demand for aesthetically pleasing, ventilated facades in the architectural community. The organic origin of the clay cladding ensures TAJO products have a low environmental impact throughout their entire cycle of life. TAJO also has limitless design options, glazes, colors, and profiles and easily integrates with a field-tested rainscreen product like IntelliScreen—offering a seamless design (these two were literally made for each other) that saves builders and designers time, money, and stress. In fact, the IntelliScreen complete rainscreen wall system delivers all this under a single-source warranty.
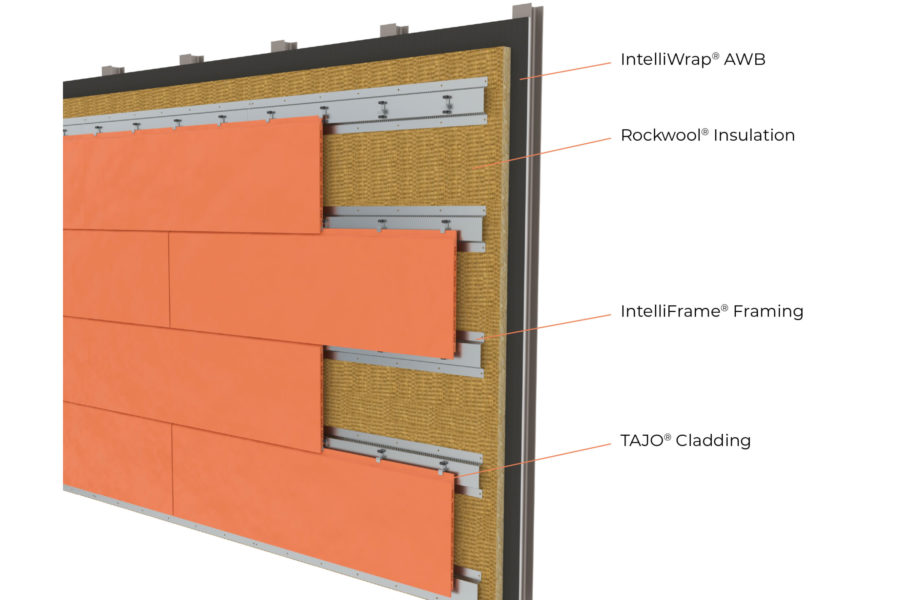
TAJO IntelliScreen. Image courtesy of IMETCO
A rainscreen system like IntelliScreen and TAJO can work wonders in any environment, Hasan says. Typically rainscreens consist of three layers—the cladding itself, an essential air gap, and a water-resistant barrier. A well-designed, fully integrated system does even more. “Properly designed, rainscreen systems can provide long-lasting, beautiful, energy-efficient facilities,” Hasan says. A well-chosen rainscreen system reduces reliance on sealants while providing a hygrothermally designed air-water barrier, continuous insulation, secondary structural framing, a vented cavity (designed to drain residual liquid as well as to provide air circulation to dry out the interior of the assembly), and, ideally, beautiful exterior cladding.
We recently asked engineering guru Hasan to walk us through the big questions: Why choose an integrated rainscreen system like IntelliScreen and TAJO? How does the integration work to keep buildings safe and dry? And what makes a rainscreen system like theirs a more sustainable choice—from the materials used to its net zero potential?
How is an integrated rainscreen system a benefit to customers?
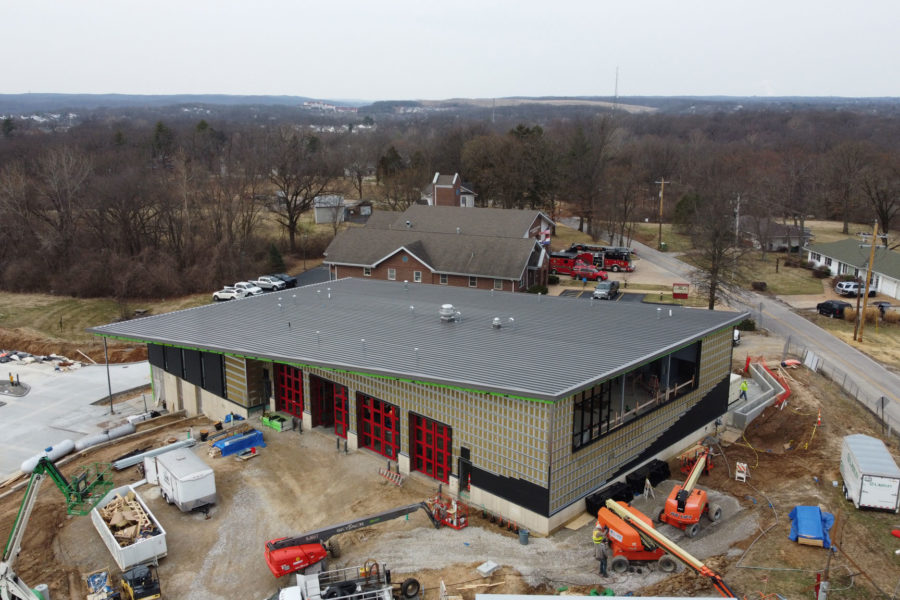
Valley Park fire station in progress. Photo courtesy of IMETCO
Design and specification of ceramic terra-cotta facade systems such as TAJO requires coordination on multiple fronts. Traditionally a designer would have to reach out to multiple vendors, various consultants, and contractors to merge all the different aspects of the design into one construction document. Some of these entities include (but are not limited to) the facade manufacturer, primary structural engineer, specialty structural engineer, waterproofing consultant, secondary framing supplier, air and water resistive barrier vendor, and contractors—all to ensure they are compatible and constructable. The liability and burden of coordinating and ensuring all the components of a ventilated facade system falls under the designer of record.
By using IMETCO’s IntelliScreen System, we take care of all the coordination and design elements. IMETCO will work with the customer (owner, architect, engineer, or contractor) to provide the aesthetic and engineering solutions—from air barrier all the way to the exterior facade. We also work hard to stay within budget, so owners/contractors can plan accordingly.
How does IMETCO work with customers to design their systems?
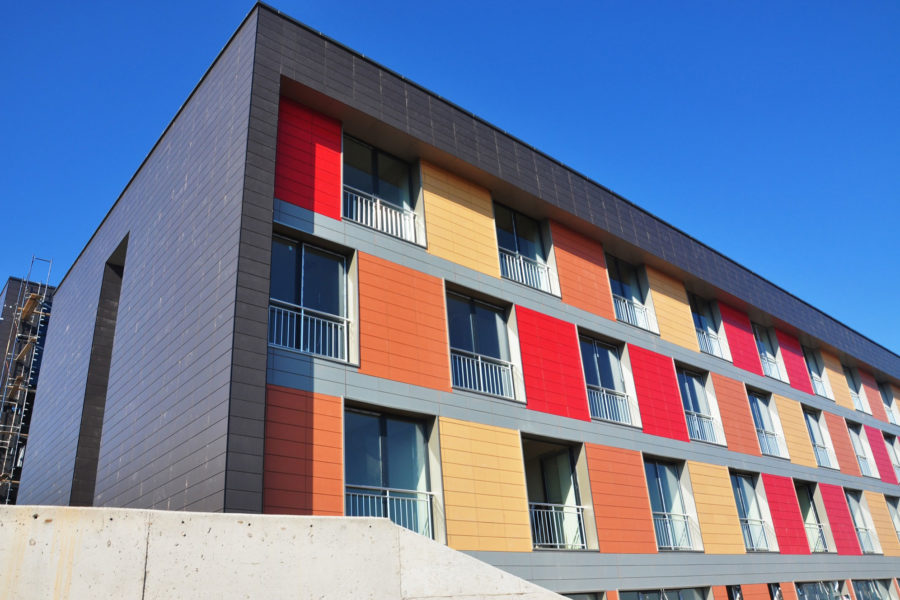
Photo courtesy of IMETCO
A ventilated ceramic facade system includes four components for coordination and design: air/water barriers (AWB), insulation, secondary framing, and ceramic facade. IMETCO’s IntelliScreen system provides fully coordinated design recommendations specific to each project.
For example, IMETCO, in partnership with Favemanc, can provide various size panels, color, pattern, texture etc. to meet the needs of modern or traditional architectural design. We will provide recommended panels that meet or exceed local and national codes, such as for structural integrity, aesthetic integrity (efflorescence, freeze-thaw), impact resistance, wind resistance, etc.
When it comes to secondary framing, based on the recommended panels, IMETCO can provide a fully engineered secondary framing system to carry the required facade load. Our IntelliFrame system is fully integrated to meet the required International Building Code (IBC)/American Society of Civil Engineers (ASCE) code requirements. These systems are also designed to provide the required ventilation space for continuous air movement to keep the system dry.
From there, IMETCO will recommend the required continuous insulation (such as Rockwool) to meet International Energy Conservation Code (IECC) and American Society of Heating, Refrigerating and Air-Conditioning Engineers (ASHRAE) standards. We also provide a National Fire Protection Agency (NFPA) standard 285-compliant system to meet or exceed fire-rating requirements.
Finally, we have the AWB (IntelliWrap). IMETCO will coordinate and provide recommendations on the type of AWB needed for the project. We go through various WUFI (heat and moisture transiency) simulations to design and recommend the required PERM rating (measurement of water vapor flowing through a square foot of material) of AWB.
Based on the substrate and/or building, we also coordinate and provide recommendations on type of AWB such as self-adhered or liquid applied. IMETCO’s integration of all the above design and construction components into a single compatible system is a big advantage for our customers.
How do these products fit into a sustainable or green build?
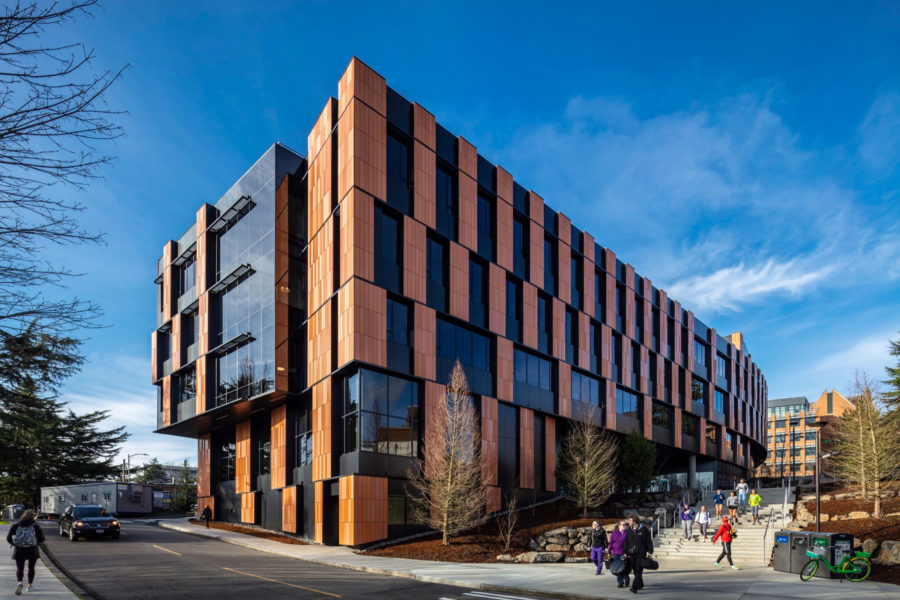
The Bill & Melinda Gates Center for Computer Science & Engineering. Photo courtesy of IMETCO
As part of IMETCO’s overall mission of providing sustainable products for building, each of the four components of IntelliScreen systems can qualify a building to achieve LEED green building certification. The IntelliWrap AWB system, when used under the “optimize energy performance” category of LEED, can obtain up to 20 points. This product also qualifies for additional points under “low-emitting materials.”
The Rockwool insulation is another benefit. Mineral wool insulation comes from volcanic rock (a naturally abundant material). Mineral wool insulation qualifies for recycled content (MRc4), regional content (MRc5) credits under LEED. Our metal secondary framing (IntelliFrame) support systems are also manufactured from recycled content and are recycled at the end of their life. LEED credits can be obtained for recycled and regional content for this category.
Finally, the ceramic facade itself (TAJO), is made from topsoil and returned to the land as topsoil at the end of its life. Fully 95% of the raw material for TAJO is recycled content. Under LEED, TAJO qualifies for many credits, including, waste management, recycled content, and more.
IMETCO strives to provide products that have high-recycled content, low embodied carbon, and are delivered to the jobsite from the closest manufacturing facility. Through our extensive due-diligence process, we try to ensure responsible sourcing from our suppliers. We also look at end-of-life cycle for each product to understand its impact on the environment. Every product we develop and market, we strive to stick to meet the cradle-to-cradle ideal.
Providing sustainable products is meaningless if they are not used effectively. This is where IMETCO is ahead of the curve. Designers/architects do not have a lot of expertise in product application knowledge. Since IMETCO integrates all the components under one system, we can provide the necessary guidance required to design long-lasting and resilient building envelope systems. The second part of our mission is to assist architects and owners in understanding sustainable, compatible products, so they can effectively use them to design green buildings to achieve their targeted sustainability goals. Our in-house engineers and architects provide hygrothermal simulations, effective R-value calculations, water-proofing recommendations, air-barrier terminations, and energy calculations. Using our resources, architects are able to create long-lasting and low-energy consuming facilities.
How does this product meet a growing emphasis on net-zero?
As the world rebounds from the pandemic and builds back better, more and more cities/countries/private companies are pledging to get to “net-zero,” essentially removing as much CO2 emissions as they produce.
De-carbonizing requires a mix of reducing energy consumption and waste, usage of renewable energies such as solar and biofuel, and carbon capture technology. To date, over 30% of global carbon energy demand can be contributed to buildings. A Zero Net Carbon (ZNC) building is defined as being a highly energy efficient building that can produce or procure enough renewable energy to meet its annual energy consumption demand.
This is where a properly designed IntelliScreen system with TAJO can help achieve optimal energy efficiency with little-to-no waste. Research published in the journal Applied Thermal Engineering (May 2014), shows an 80% reduction in energy usage when ventilated facade systems are used compared to the traditional non-insulated buildings.
We can lower the carbon-based energy consumption of a building by assisting designers to effectively create lean building envelope systems. We can further reduce the embodied carbon of each building by assisting the owner/customer in selection of long-lasting sustainable products. By lowering the operational energy usage of a building, we can offset the remaining carbon-based energy consumption through usage of renewable sources such as solar panels on roofs. IMETCO can assist customers in sourcing these alternative renewables as needed to achieve net zero.