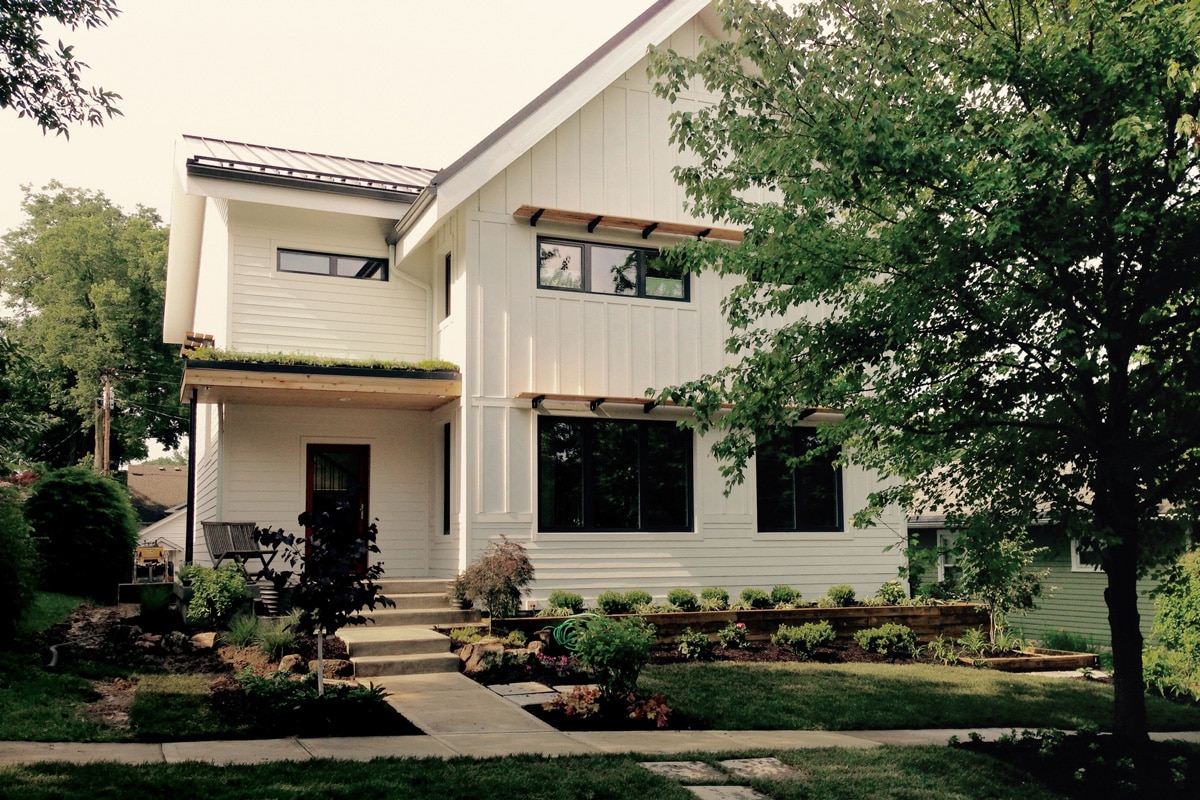
[Photo: Courtesy of FischerSIPS]
FischerSIPS continues to evolve the energy-efficient building material.
More than three decades have passed since Louisville builder Fred Fischer was inspired to use structural insulated panels (or SIPs, for short) to build his home. The result was so pleasing—sturdy and energy-efficient, among other qualities—it sparked the idea for his next business venture. The following year, 1987, FischerSIPS was born.
Starting out with condos and single-family homes, the company soon expanded into commercial construction and, in 1990, helped form the Structural Insulated Panel Association. FischerSIPs now serves a regional market that extends from Florida to Texas, along the East Coast and westward to Kansas and Iowa. Its products have even been used as far away as South Korea, Ireland, Russia,
and the Bahamas. And in 2015, when Super Bowl XLVI came to Indianapolis, FischerSIPs was there, too, providing product for two buildings in the Super Bowl Village complex. “SIPs have really come a long way,” says current FischerSIPs owner Damian Pataluna, who began with the company as a salesperson in 1993 and bought it in 2007.
And the future, he notes, looks promising. These are some of the benefits of using SIPs.
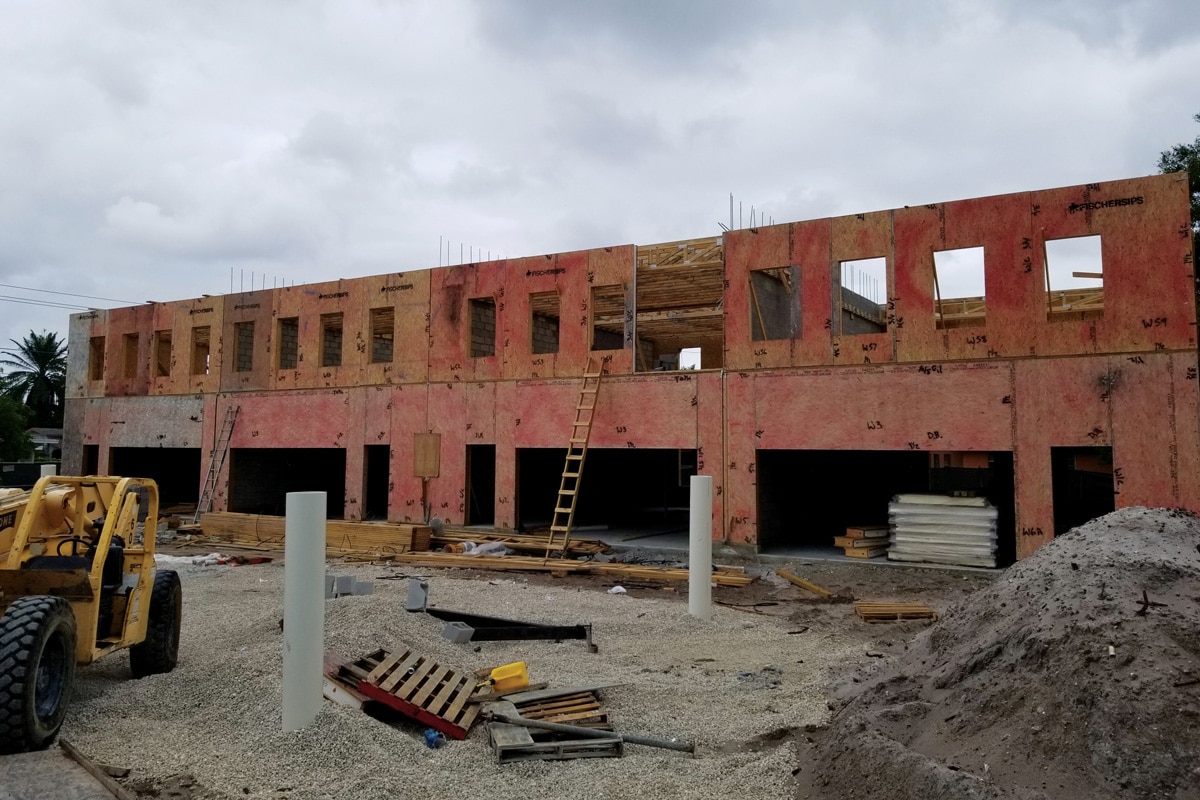
[Photo: Courtesy of FischerSIPS]
Resiliency
Used for walls and roofs, FischerSIPS are made with what’s called oriented strand board (OSB) inside and out that give the resulting laminated panel extreme load-bearing properties that can withstand higher winds than stick-frame structures. “The way SIPs are tied together with the long panel screws creates incredible sheer strength,” Pataluna says. “You won’t typically have situations where the trusses or individual pieces of sheeting can be ripped off the roof because the roof panels are one solid sheet inside and outside that are screwed down to the walls. You’d almost have to pick up the entire house to rip it off the foundation.”
The panels also perform exceedingly well in earthquakes. “We’ve got pictures where the last house standing after an earthquake was a SIP house. Since it’s made of flexible wood and plastic and everything is essentially one big piece, you literally have to take the entire foundation out from under it before it starts to come down. Concrete, which is obviously stronger, is so rigid that when it starts to go, you’ve got issues.”

[Photo: Courtesy of FischerSIPS]
Fast Installation
Because FischerSIPS allows builders to install drywall directly on top of panels, they can skip the step of custom-cutting it to meet studs—there are none. And when it comes to electrical installation, pre-drilled holes for switch and plug height streamline the process.
Most significantly, FischerSIPS employs specialized computer numerical control (CNC) technology (essentially a CAD machine) that quickly and accurately pre-cuts and fabricates SIPs prior to shipping. That means less labor for installers as well as no more costly, time-consuming, on-site cutting. The company also has begun framing out windows, doors, and connection splines to further speed up the process.
“A lot of time on jobsites you see guys out there scratching their heads, trying to figure out how to cut a complex angle and make it work,” Pataluna says. “Or you may have a situation where it’s dangerous because it’s high in the air. If we can get it figured out in a safe factory setting and then ship it out to a jobsite where it’s pre-assembled on the ground, think of the time-saving safety factors that are involved with that.”
Says builder and FischerSIPS client John Barrows, president of J. Barrows Inc., “We cut installation time considerably depending on complexity. But the biggest benefit is that the process forces the design and construction team to work out any inconsistencies or changes prior to panel fabrication. Combine that with the fact that we are also framing and insulating, and the time savings adds up.”
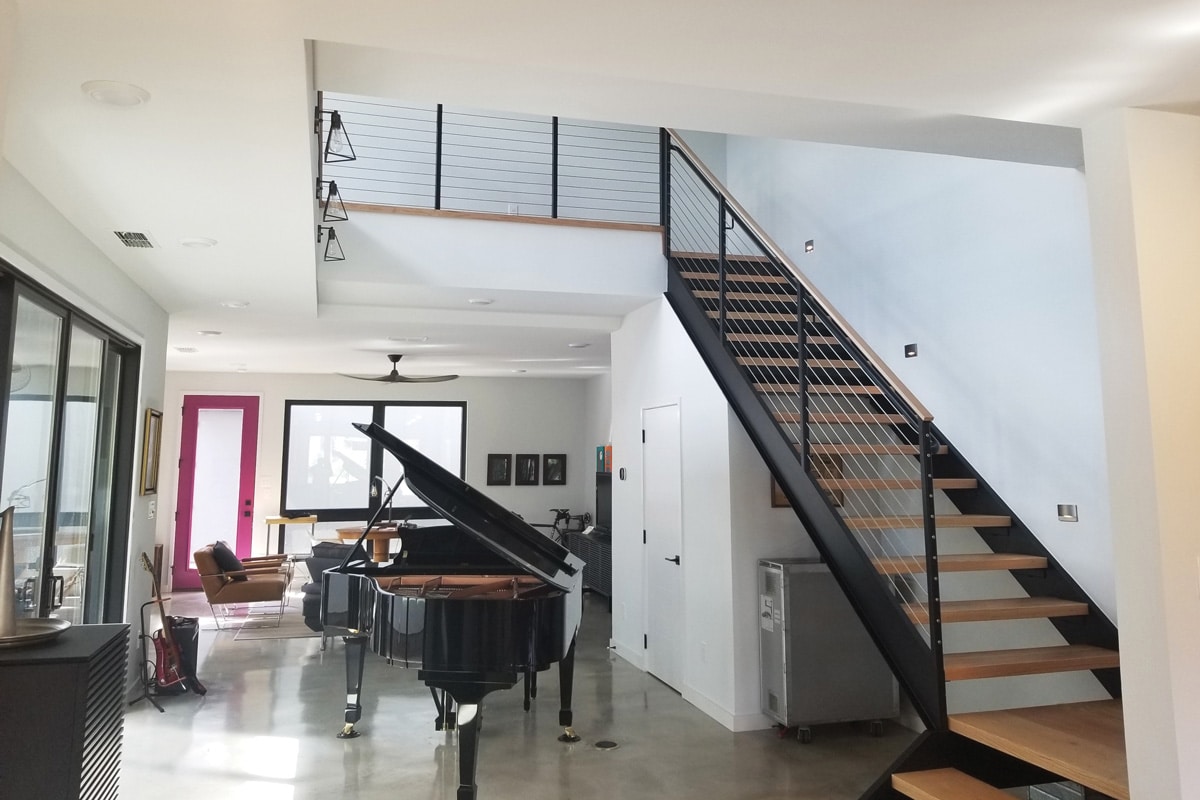
[Photo: Courtesy of FischerSIPS]
Energy Efficiency
Pataluna says SIPs are typically 30 to 50% more energy-efficient than standard construction with fiberglass insulation—which means lower costs from day one. That’s because fiberglass is a porous material that allows air to pass through it. SIPs, on the other hand, benefit from solid foam insulation that Pataluna likens to “living in a big igloo or cooler that will maintain heat or cold, which means homes and buildings can downsize their HVAC systems.”
Not long ago, a FischerSIPS home was one of 10 showcased at a Homearama event in Louisville. It was 90 degrees outside, and at one point the entire block lost electricity. “As customers were coming into our SIP home they kept saying, ‘Oh, you guys still have power,’” Pataluna recalls. “We said, ‘No, it’s been out for an hour.’ But because ours was built out of SIPs, it maintained that coolness, and customers could instantly feel the difference.”
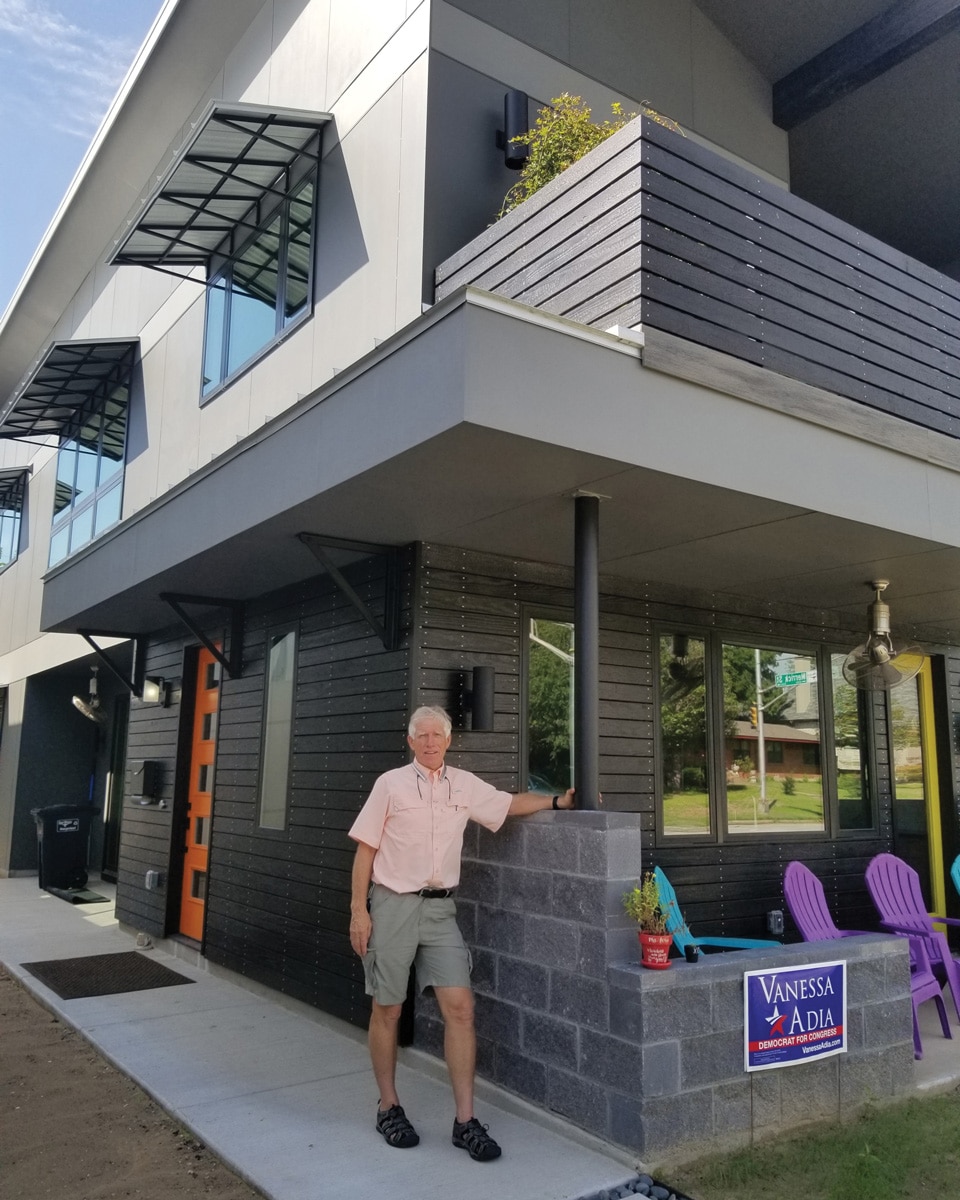
[Photo: Courtesy of FischerSIPS]
Environmentally Friendly
Unlike traditional homes that are built with lumber from old-growth trees, SIPs are constructed in part with ground-up young trees that are regularly replanted. Coupled with the lower energy consumption that’s made possible by the product’s superior insulation properties and far less jobsite waste due to factory pre-cutting, and the environment benefits greatly. Even the air quality in a SIPs home is better.
“Because SIPs are more airtight than your typical structure, you don’t have a lot of air passing in and out of your house. The resulting reduction in dust and pollen
makes it cleaner air to breathe,” Pataluna says.
But don’t just take his word for it. Another FischerSIPs builder, Don Ferrier of Ferrier Custom Homes, prefers working with SIPs. Properly installed, he says they guarantee “exceptional air tightness, insulation, and structural strength. These are foundational to high performance/green construction.”
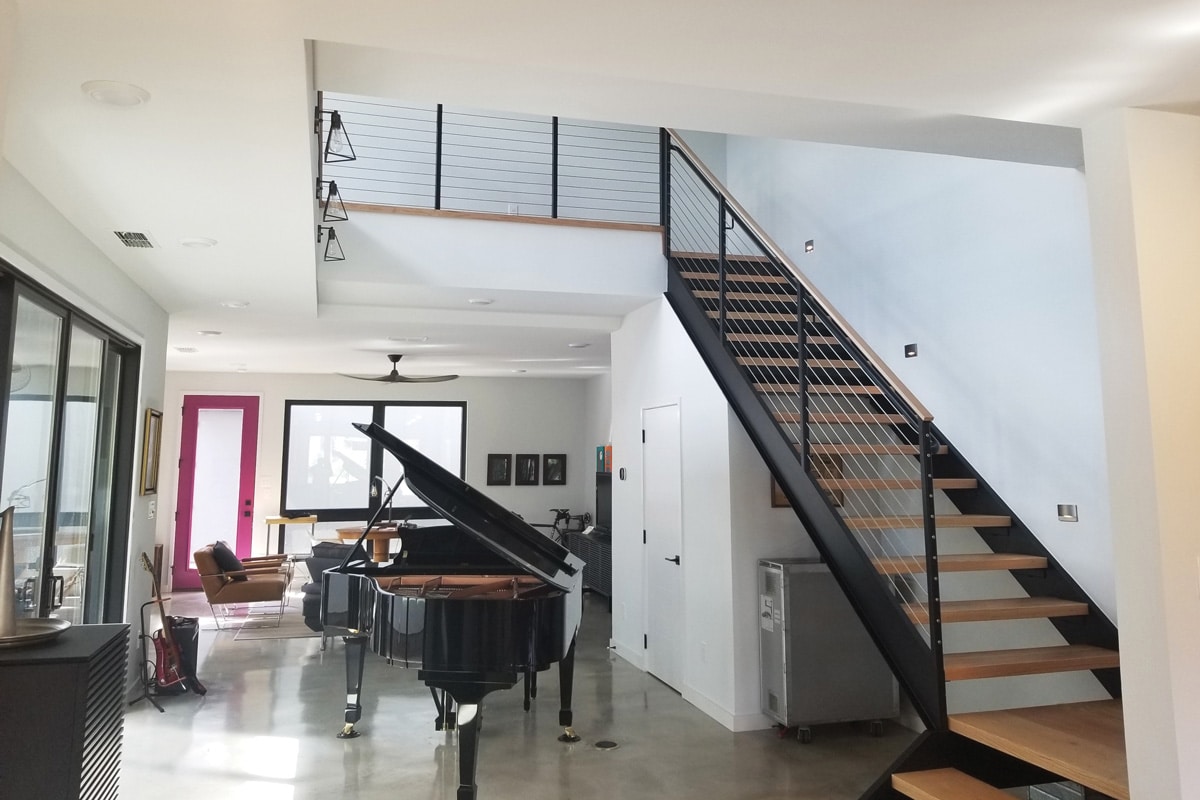
[Photo: Courtesy of FischerSIPS]
The Future of SIPs
Looking forward, Pataluna says there will ideally be more architectural involvement in the SIP prefabrication process. “I hope we get to a point where architects are actually doing the drawings for SIP panels like they do in other industries, so when an order goes to the manufacturer, they’re sending complete files and saying, ‘Hey, can you produce these panels for this project? Here it is.’”
He’s also confident the use of SIPs will rise considerably, especially as energy regulations (like California’s net zero mandate) get stricter nationwide. “We’re looking to get into more commercial projects,” he says.
“And we’re certainly looking to get into more multifamily ones. SIPs are barely 2% of the new residential construction market now, so there’s a ton of room for growth.”