Story at a glance:
- With wall and window systems already offering great environmental efficiencies, eliminating thermal bridging in the building envelope is the next step in reducing energy loss sustainably.
- Municipalities, architects, and engineers are increasingly looking to install thermal breaks at all junctions in the building envelope to keep cold air and condensation out.
- Thermal break assemblies can eliminate up to 95% of energy transfer, reducing the burden on heating systems and the need for costly maintenance.
Buildings exist to protect their inhabitants from the harsh extremes of the climate outside. But no building is hermetically sealed; despite advancements in insulation and fenestration, they continue to allow the transfer of heat and energy.
“Energy is going to find the path of least resistance,” says Nate Lambrecht, regional sales manager for Schöck North America. “It’s like in a cartoon where someone sticks their finger into a leak to stop it and a new leak springs up. Even if you plug all of the holes, whatever is on the other side is going to try to get through.”
Junctions in the building envelope may be the final frontier in lessening the effects of energy transfer or thermal bridging, particularly when the outside air is colder than the conditioned environment inside.
“Walls are already doing a really good job at mitigating heat loss,” says Cody Belton, passive house specialist and building enclosure consultant with Stantec, the global engineering, architecture, and environmental consulting firm. “It’s the transition details that are the problem. [We recommend] trying to mitigate thermal bridging at any transition in the building envelope.”
That’s where thermal breaks come in. Low-conducting structural elements used to separate building components and stem the transfer of heat and condensation, they are catching on throughout North America as building codes become more environmentally conscious.
“Some municipalities are already pushing thermal breaks from a code standard,” Lambrecht says. “But you’re also seeing the design community say, ‘We want to put forth a good product,’ so this type of thing is coming into a lot more conversations.”
Understanding Thermal Breaks
- Thermal breaks at Stantec Tower. Photo courtesy of Schöck
- Photo courtesy of Schöck
Company founder and civil engineer Eberhard Schöck was vacationing at a Swiss ski lodge in the 1970s when he noticed moisture and mildew growth on the ceiling of his room. Cold from the exterior balcony slab in the unit above was penetrating the concrete and reinforcing steel, cooling the surface to a temperature below the dewpoint of the interior air.
“Whenever you have a surface that’s below the dewpoint of the humidified interior air you are going to get condensation,” Lambrecht says. “This is a durability problem and a health concern. If you’re going to build a building to the best possible standard, you’re going to use a thermal break to not only minimize heat loss but also eliminate the risk of condensation.”
Schöck’s Isokorb® portfolio of structural thermal breaks includes products designed for concrete construction, steel construction, floor slabs, and other applications. But the company is perhaps best known for the concrete-to-concrete thermal breaks used on the cantilevered floor slabs that form balconies.
Thermal Breaks in Action
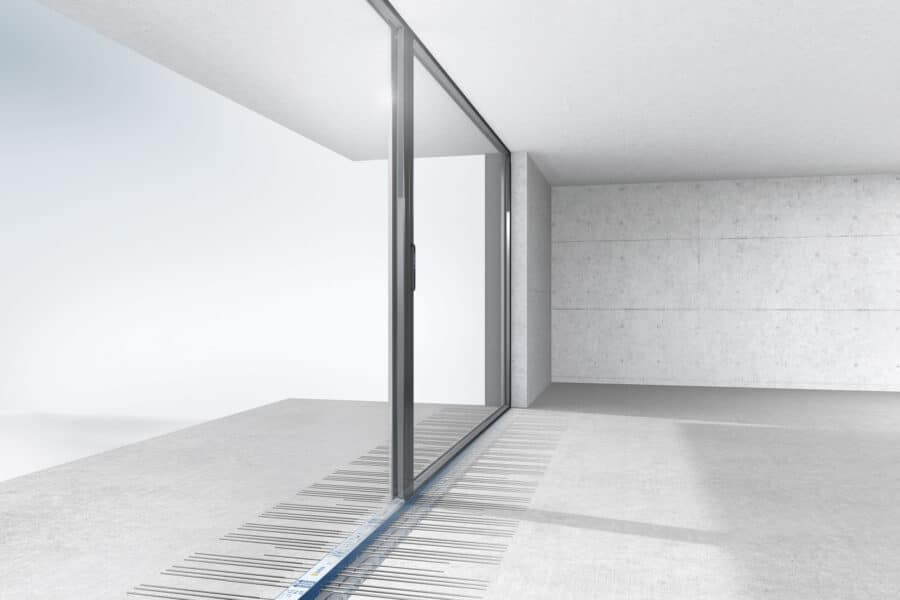
Image courtesy of Schöck
The Stantec Tower in Edmonton, Alberta demanded thermal breaks to head off the potential of considerable energy transfer. The tallest skyscraper in Western Canada at 66 stories, the LEED-certified building houses the company’s headquarters and 36 floors of condominiums—17 of which have expansive balconies overlooking the city and windswept prairie beyond.
Architects specified load-bearing, concrete-to-concrete thermal breaks—1,590 in all—to create an insulated barrier between the balconies outside the building and the floor slab inside. Most are Isokorb assemblies, which feature a graphite-enhanced block of expanded polystyrene insulation and stainless steel rebar for tension and shear resistance.
Depending on conditions, Isokorb thermal breaks can eliminate up to 95% of energy transfer through a concrete connection, according to Schöck. Thermal modeling indicated that the temperature of the Stantec Tower’s interior slabs would be up 6 to 7°C warmer with thermal breaks, eliminating the need for baseboard heating, preventing condensation from forming on adjacent surfaces, and reducing energy consumption for heating 7.3% compared to constructing the building with uninsulated balcony slabs.
Pros & Cons
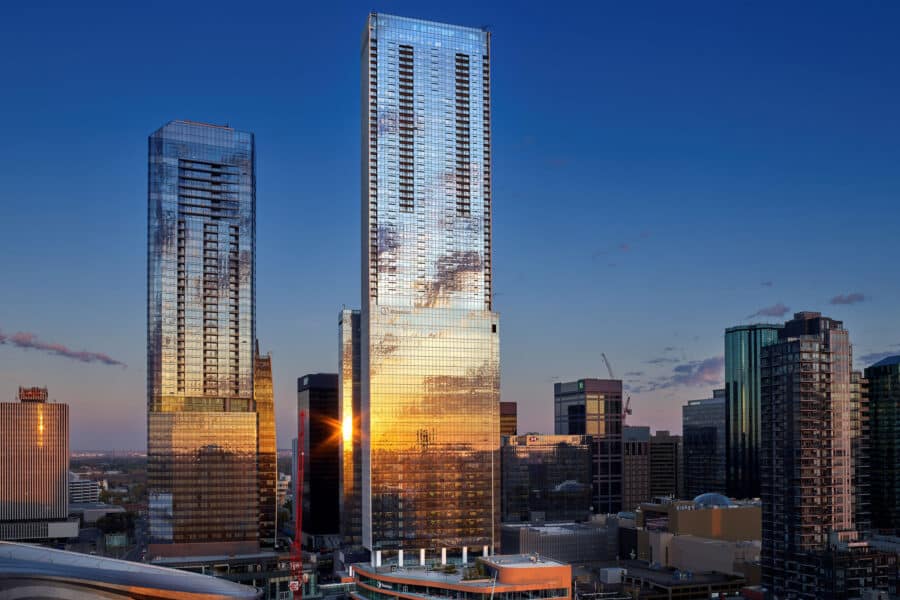
Stantec Tower in Edmonton, Alberta stands at 69 stories. Photo by Merle Prosofsky
Designing for thermal breaks has a few minor challenges. Primarily architects and engineers need to think beyond the uninterrupted slab to forecast the building envelope’s performance and structural integrity.
“It isn’t difficult to integrate thermal breaks into a typical project,” Lambrecht says. “There can be occasions where the loading is outside of what would typically be possible, but if considered early enough in the design process there is usually a solution.”
What’s more, thermal breaks are only part of the answer to an energy-efficient and sustainable building. “If you interrupt a high-performance wall assembly with a highly transferable assembly of concrete and steel, you instantly reduce the benefit from the wall itself,” Lambrecht says. “And if you bought the cheapest window system, adding a thermal break is not going to solve your energy issues.”
The cost/benefit analysis of incorporating thermal breaks should consider their effect on the overall performance of the building envelope. The energy savings delivered has allowed some projects to downgrade from triple-glazed window systems to double-glazed systems, offsetting costs while still meeting operational and environmental goals.
“When you can mitigate heat loss and conserve more energy, you can significantly downsize mechanical systems,” Belton says. “Instead of putting a lot of money into oversized mechanical systems for heating or cooling, you can transfer that initial capital investment into a high-performance building enclosure.”
In abating moisture and condensation, thermal breaks can also head off costly maintenance. “A lot of people overlook the durability aspect,” Lambrecht says. “Beyond the energy performance, you’re looking at reduced overall maintenance and upkeep costs.”
Users benefit from an engineered and tested assembly. “We provide a nice, clean pass-through to simplify the geometry and still provide continuity to the building envelope,” Lambrecht says. “We can build to a higher standard without massive increases to cost if we plan it well.”
Design for Net Zero
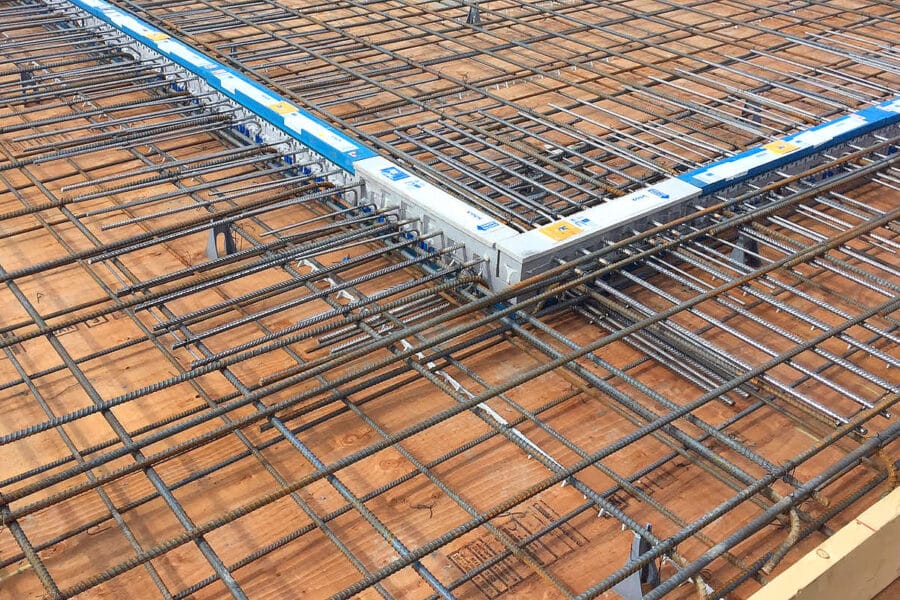
Photo courtesy of Schöck
While some building codes still ignore the problem of thermal bridging and require only added insulation, others are embracing thermal breaks as a step toward net-zero energy or net-zero carbon goals.
“We’re getting much more sophisticated with our building envelope design,” Lambrecht says. “Major municipalities are updating building codes, and they’re pushing thermal breaks to be more of the norm as opposed to the exception. It’s part of a more holistic approach of saying, ‘OK, how do we make the tightest building envelope possible?’”
Architects, engineers, and developers seeking to decrease energy transfer and preserve building integrity are also waking up to the benefits, particularly in settings where consistent interior temperatures are desired. Several museums (including the Statue of Liberty Museum), the under-construction Obama Presidential Center in Chicago, and a hospital above the Arctic Circle have Isokorb breaks specified to guard against energy transfer.
“Higher performance energy targets are changing the way we design buildings for the better,” Belton says. “We definitely need solutions such as Isokorb—anything that’s going to mitigate thermal bridging.”
A Window to the World
In a post-construction research study led by Belton, Morrison Hershfield (now Stantec) applied the lessons learned from 825 Pacific to develop a market-ready, high-performance window connection for wall assemblies that use exterior insulation. The Akira Window Connection is a window and door dead load support system with intermittent brackets fastened to the backup wall structure and continuous angle supported by the brackets. The continuous angle is decoupled from the backup wall to reduce heat transfer and simplify air and moisture barrier detailing.
This connection method results in nearly thermal bridge–free linear transmittance values at window-to-wall transitions, improving whole-building thermal energy performance. On an affordable housing project in North Vancouver, for example, the company found that incorporating Akira Window Connections cut the 10 inches of exterior insulation needed to satisfy thermal energy demand intensity (TEDI) targets in half.
Armed with a Building Excellence Research & Education Grant from BC Housing, Stantec’s goal is to provide open-source thermal bridging data on the new system’s performance for any project team to use. “Adding insulation is kind of the go-to solution to address energy loss,” Belton says. With the Akira Window Connection system, “we can make facades more cost-effective by decreasing exterior insulation costs. That thins the external walls and has the potential to create more interior floor area.”