Story at a glance:
- Old Mill Brick’s patented wall systems offer thin brick finishes that are as durable and sustainable as they are attractive.
- The systems meet the International Energy Conservation Code and the International Building Code with R-values ranging from R-5 to R-20.
- The material footprint of Old Mill Brick’s thin brick systems is just one-fifth of typical full thickness brick units.
Classic kiln-fired clay brick has long been an architectural staple, adorning some of the most beautiful buildings in the world, from picturesque historical structures to polished, contemporary office buildings. Yet in many cases its high costs and difficulty of later remodeling efforts render brick out of reach. Consequently, thin brick adhered veneers that ensure flexibility, lower costs, and smaller material footprints have increasingly gained traction in recent years.
Thin brick specialist Old Mill Brick takes these benefits a step further by offering their patented Brickwebb and Panel+ engineered wall systems, which not only provide attractive thin brick finishes but integrate them into consolidated solutions that can help architects, designers, and building owners to meet code and cut costs while enjoying the peace of mind delivered by the Old Mill 15-year System Warranty, which means their project is as aesthetically pleasing as it is durable and sustainable.
“Our products comply with numerous codes as well as being the easiest and most cost-effective way to get a job done anyway,” says John Striednig, vice president of commercial operations at Old Mill Brick. “If you have a high-performance option that costs less than the others and offers the additional benefit of sustainability, why would you use anything else?”
Meet stringent requirements.
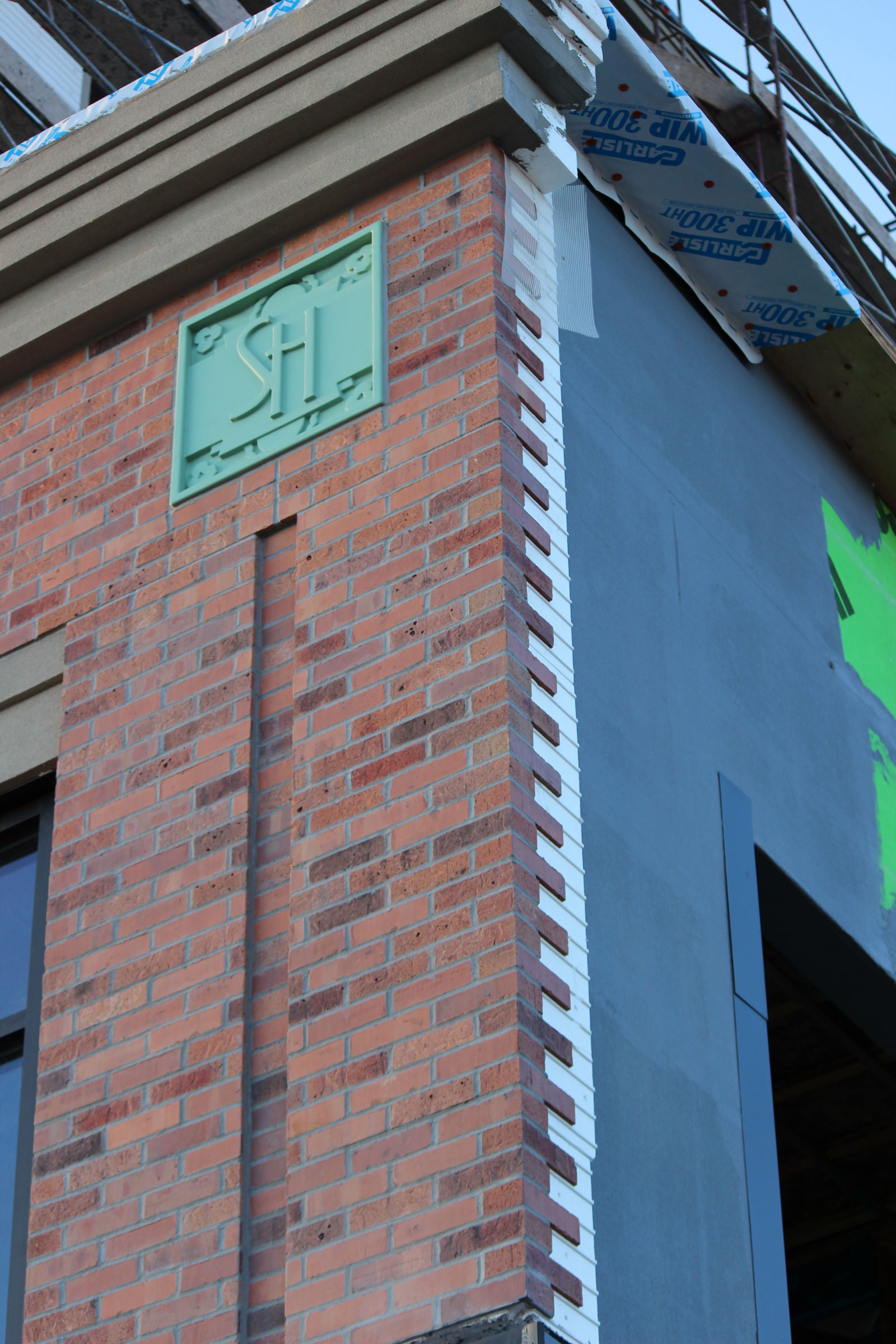
Note the architectural relief achieved through foam thickness variations like vertical reveals and corbelling. Multiple finishes like EIFS, cast stone, brick, and stone can all be incorporated using the Old Mill Panel+ System. Courtesy of Old Mill Brick
Old Mill Brick’s Panel+ solution in particular not only provides the aesthetic appeal of thin brick at a low cost; it can also help to meet continuous insulation and air and water barrier requirements set forth in the International Energy Conservation Code and the International Building Code.
Continuous insulation requirements necessitate that insulation is consistent across the entirety of a structure, lest thermal bridges—gaps in a building’s envelope caused by conductive surfaces such as wall studs and cladding—allow heat to flow in and out, lowering occupant comfort and raising energy bills. Similarly, air and water barrier requirements mandate weather barrier materials must not exceed a certain air or moisture permeability.
Panel+, which allows thin brick flats to be easily mounted on an expanded polystyrene rigid foam substrate, meets and exceeds these requirements. The Panel+ system features R-values ranging from R-5 to R-20 along with fluid applied air and water barrier liquid and water channels on the back of the foam to allow drainage and ventilation that keeps the panels dry while ensuring peak thermal efficiency.
Installation is easy.
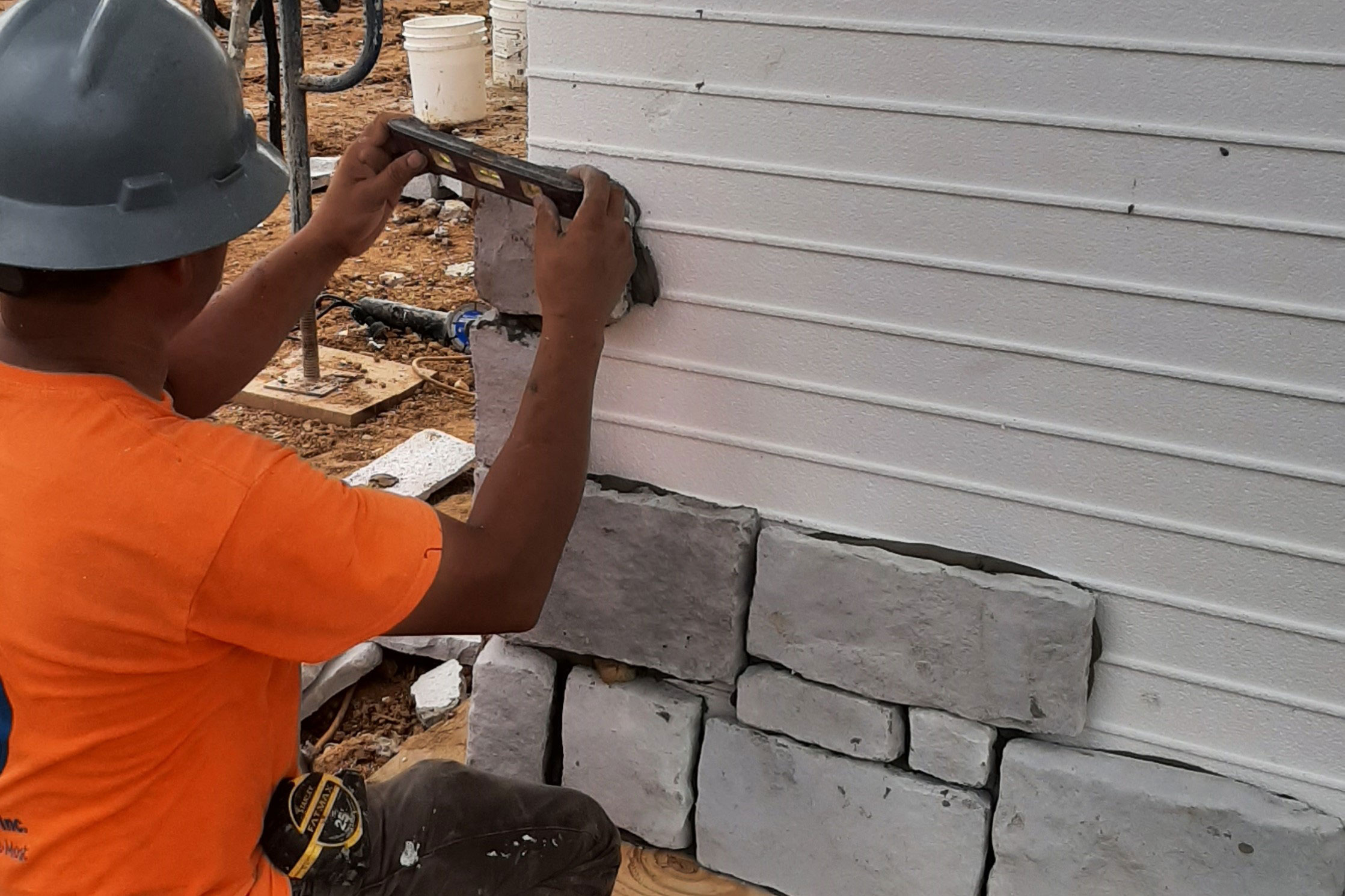
The Panel+ System easily accommodates all adhered veneers, including brick, natural stone, manufactured stone, and other commonly adhered materials. Courtesy of Old Mill Brick
Whether you’re using Brickwebb or Panel+ for your project, ease of installation can be guaranteed. Brickwebb, which is a patented mesh-mounted system for mounting and aligning thin brick flats, can reduce overall installation time by two-thirds, Striednig says. He likens it to panels made for mounting glass mosaic tiles, which feature 144 one-inch square tiles attached to a single mesh backing. Rather than go through the labor of adhering each tile individually, you simply need to attach the panels. Brickwebb is similar, featuring 12 brick flats per Brickwebb mesh panel already spaced, coursed, and affixed in place.
Similarly, Panel+, while ultimately a rigid foam insulation panel, features alignment tracks on its outer surface that allow thin brick flats to be perfectly spaced and leveled without any fear of irregularity occurring. This not only assures a perfectly applied veneer but also reduces the requisite labor expenditures.
“Brick masons know how to stack a brick and get it aligned and coursed properly, but thin brick is a bit more like tile. When it comes to sticking it to a wall, getting all the lines straight and the spacing correct requires a different skill set,” Striednig says. “We’ve found that by creating these two systems, we’ve provided an assurance of perfect alignment and the ability to save labor at the same time.”
Shrink your material footprint.
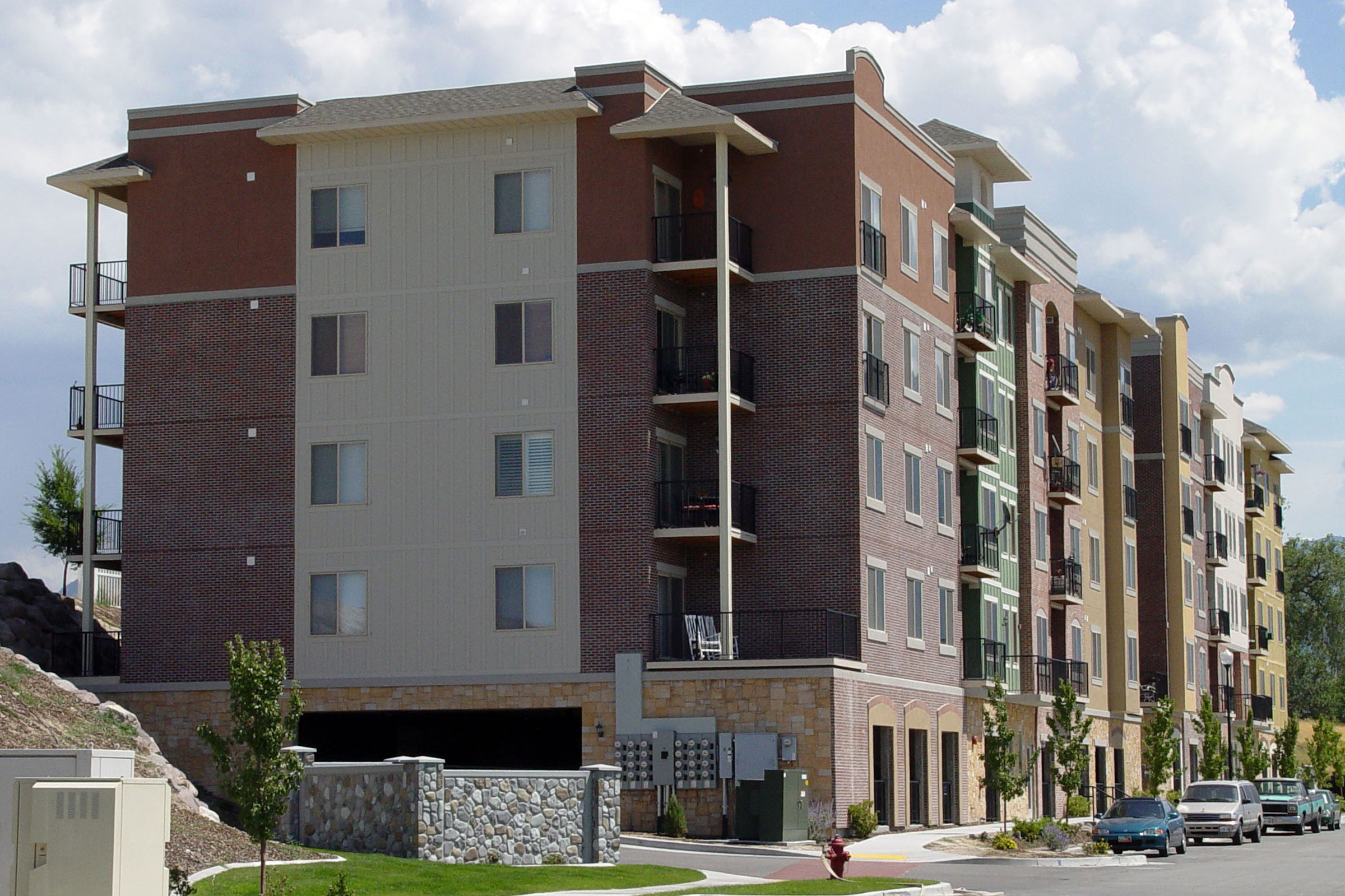
This highly efficient home uses the Old Mill Panel+ System. Whether you’re building new or remodeling, the Panel+ System is simple to include in your design. Courtesy of Old Mill Brick
Sustainability is another area where Old Mill Brick’s solutions shine. Striednig says that while thin brick flats are made of real kiln-fired clay brick, their overall material footprint is just one-fifth of typical full thickness brick units. That means the thin brick itself has a smaller footprint and less emissions are created by the extraction, manufacture, and transportation of surplus materials further down the supply chain. And because of thin brick’s reduced weight, buildings with lighter foundations can more easily accommodate it, allowing for further material reductions like the elimination of wall ties and support metals.
Take, for example, an instance in which a 16-inch thick wall is reduced to 12 inches due to the use of thin brick. In this case less steel and concrete are needed to support it, and by moving the wall to the perimeter of the slab, the owner realizes the additional finished space inside their building. This makes thin brick ideal for retrofits and renovations, too. Without needing to alter a building’s foundation, the charm and elegance of brick detailing can be attained.
“In the old way of doing things, after sheathing a wall up, it would go to a waterproofing contractor to apply the air and water barrier. Then another subcontractor would install the insulation, then finally the mason or exteriors contractor would install the finish. With us, everything can go to just one contractor, and that simplifies trade coordination and accelerates the job,” Striednig says. “You can look at labor hours, material footprints, or anything else you want, but whichever way you crunch the numbers, you find that you save.”