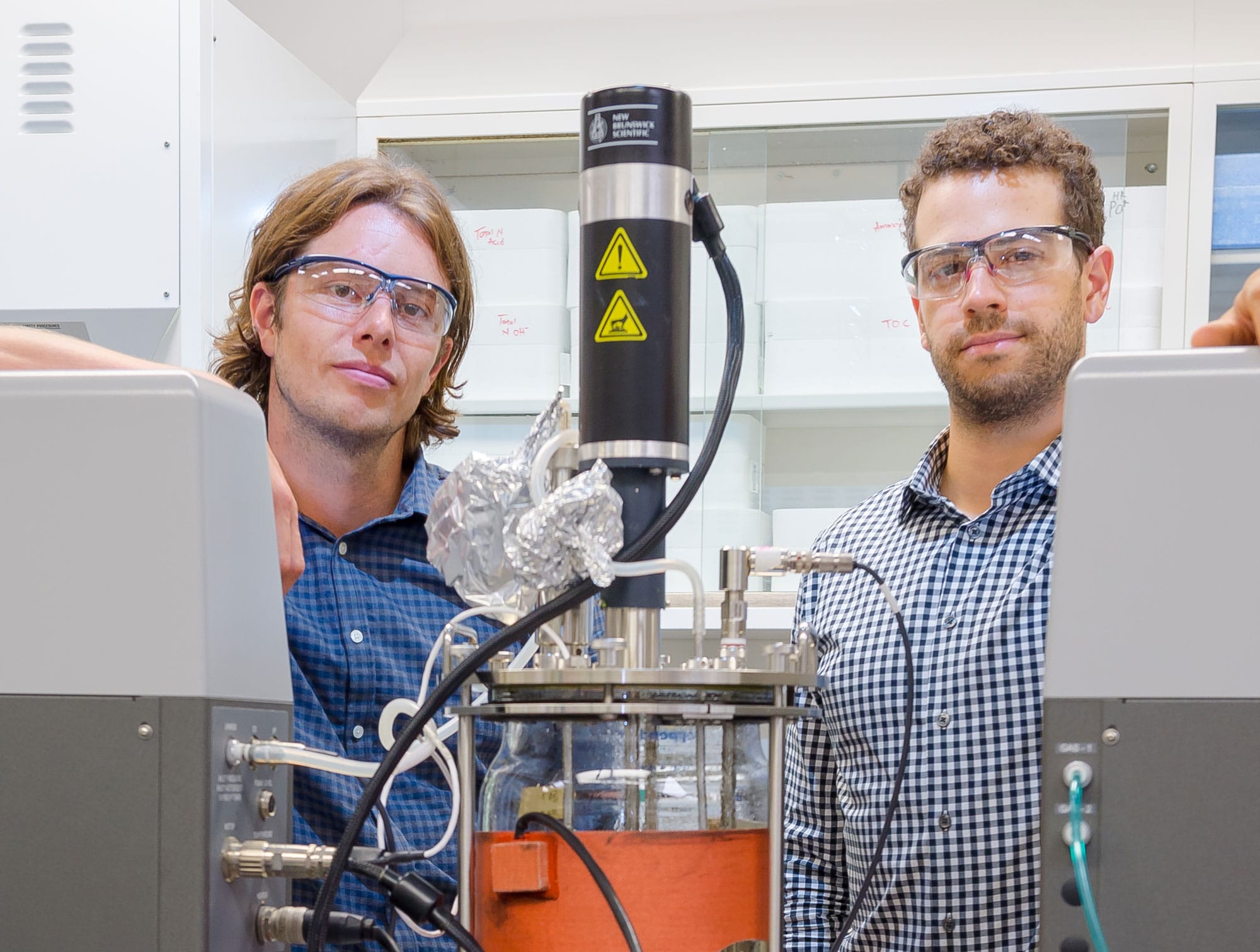
Emergy can help reduce the chemical and energy industries’ operational costs by 25%—using less energy, less raw material, and less storage and shipping space, and requiring less maintenance.
[Photo: Mark Lopez]
Emergy Labs Cofounders, Chicago, IL
Lithium-ion batteries, air and water filtration, gold mining—the porous carbon grown by Emergy Labs can be used just about everywhere and can replace some very inefficient materials, it seems. Emergy, started in 2015 by then-University of Colorado Boulder students Tyler Huggins and Justin Whiteley, is now getting the help it needs from Argonne National Laboratory to get off the ground and into the market, where it can make a real difference in a number of industries.
“I don’t think people truly appreciate where a lot of these fundamental materials are derived from,” says Whiteley, chief technology officer for Emergy. Whiteley runs the company alongside its only other full-time employee, CEO Huggins. He says people often wonder about coal power, asking why we’re still using the filthy resource. But coal isn’t just used for power. In fact, an extensive amount of materials comes from coal, including the majority of water filtration materials. “How about replacing some of these materials that are derived from coal?” he asks, noting the resource’s CO2 emissions.
Through the Chain Reaction Innovations (CRI) startup program at Argonne, Emergy Labs is developing its sustainable carbon material in an effort to do just that. CRI sets out to provide a stronger bridge from great idea to marketplace—a path where, historically, most innovative ideas die due to a lack of investment and support.
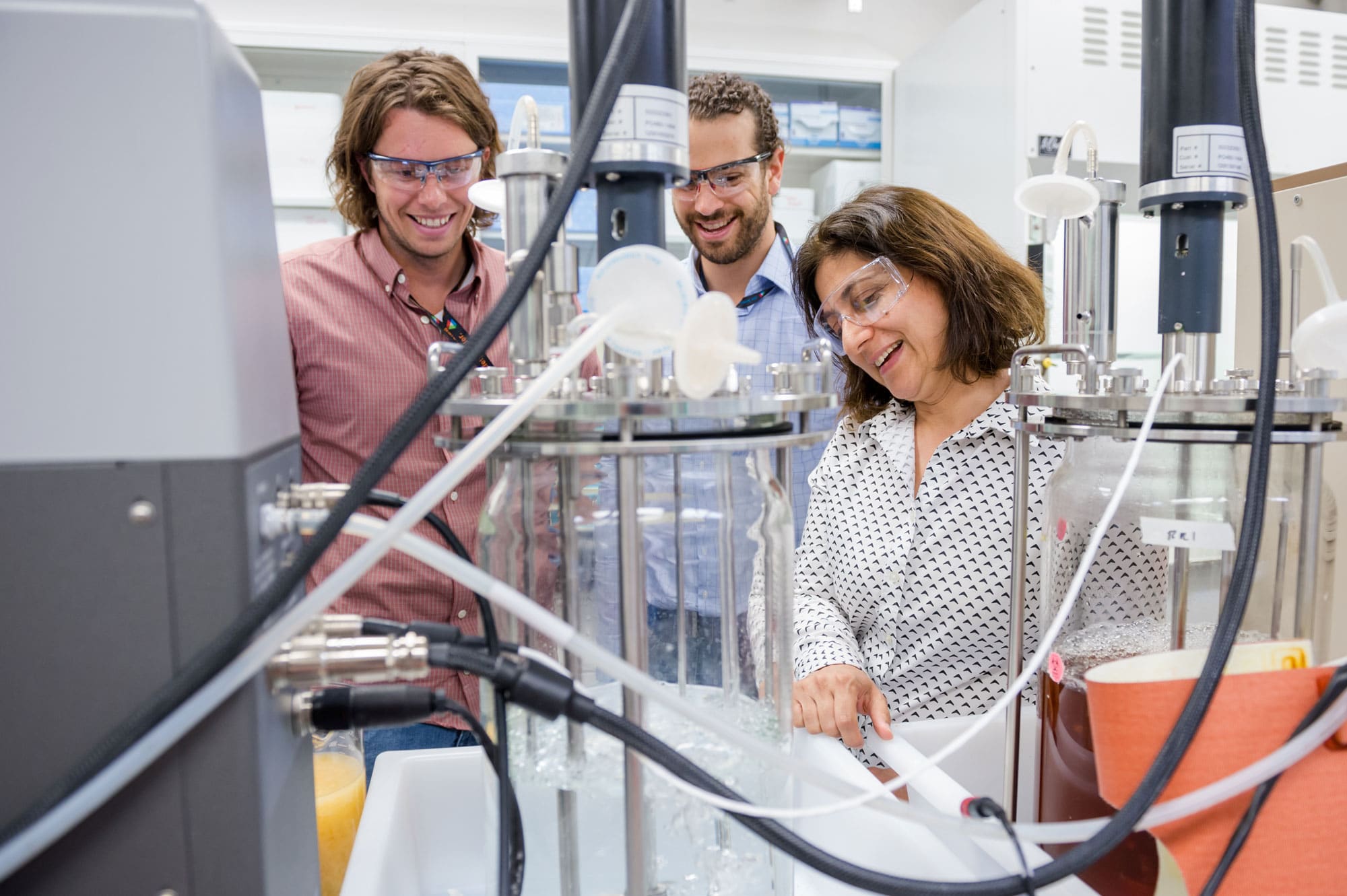
[Photo: Courtesy of Argonne National Laboratory]
But how does it work? Emergy uses a filamentous organism to capture renewable and sustainable carbon from wastewater to grow fungus and create products like battery electrodes. Emergy’s carbon can replace that which comes from more intensive manufacturing processes from coal, coconut husks, or wood. “We don’t have to go out and harvest some natural resource or grow a whole field of coconuts to produce a material. We can produce this more simply and in a much more geographically diverse way—where we need it.” Rather than produce, say, tons of coconuts in Asia and then pay to ship them all over the world, we could produce a more sustainable material close to home. “That’s where we see ourselves. Producing more material where you need it,” Whiteley says.
Huggins says the benefits are clear. “For industry, the processes become more efficient and use less resources. For society, we can greatly reduce the carbon footprint.”
Huggins and Whiteley say they are fortunate to have won funding and support from Argonne, as they’re now in the midst of working with experts at the world-class lab to further test the abilities of the material and find commercial partners. We recently sat down with the innovators to find out what it all means—and what’s next.
“I believe entrepreneurship guided by sustainable principles can have the greatest impact.”
gb&d: What drew you to this type of work?
Huggins: I have always been passionate about sustainable development. Initially I started a land restoration company working on forest health improvement projects, but it seemed I was limited by a lack of experience and credentials. I felt I needed to go back to school and get a few more letters after my name before people would take me seriously. So I did, getting a master’s in sustainability engineering and a Ph.D. in environmental engineering. I was always looking for a technology I felt could help create a more sustainable society. I believe entrepreneurship guided by sustainable principles can have the greatest impact. The technology we’re working on now, I believe, has the right combination of advanced technology, practicality, and addressing a real need, to make it a success.  Â
Whiteley: Carbon materials haven’t changed really over the last 100 years. They remain derived off coal, wood, or coconut. They have locked intrinsic features. If you want to change them, you have to use energy intensive manufacturing processes. Since we have precision control over how the organism grows by changing the organism and not the manufacturing process, we can actually grow a variety of materials for a whole suite of applications in a single facility using a single process line.
gb&d: What inspired you to create a new material?
Huggins: A lot of the inspiration behind this came from observing biological systems in nature. Biology has unmatched efficiency at the molecular level, with the ability to produce extremely sophisticated materials, unlike anything we can make in the lab, with little waste and energy. Nature has a billion years’ head start, and we can learn a lot about how to make stuff sustainably. But biological systems are inherently selfish, allocating energy and resources for self-preservation and reproduction. It is our goal at Emergy to harness natural processes but guide them into making materials used to solve problems in our society effectively. We are taking an engineered approach, which preserves the efficiencies intrinsic to biology but allows us to make much higher performing materials than you would get if you just went out and harvested naturally grown biomass. Â
gb&d: How do you hope this new material can be used?
Huggins: Ultimately I hope to see it disrupt the activated carbon industry. Activated carbon is ubiquitous, used in almost every major industry of our economy, yet it is produced using unsustainable methods with little change in the last 70 years. If we can scale our production process, while maintaining our higher performance and lower cost, we will be able to provide a competitive alternative to conventional activated carbon that has significantly less impact on the environment.
gb&d: At first you focused on batteries. What changed?
Whiteley: We had a material that performed well as a lithium-ion battery anode, so we thought we’d start investigating the possible paths for commercialization by contacting battery manufacturers. We realized this path would be a tricky way for us to start. If you look at lithium-ion batteries, they’ve been using the same materials since 1991, and trying to convince them to take a risk and use a new material would be at least a 5- to 10-year approach. So we pivoted and started looking at the strengths of our materials.
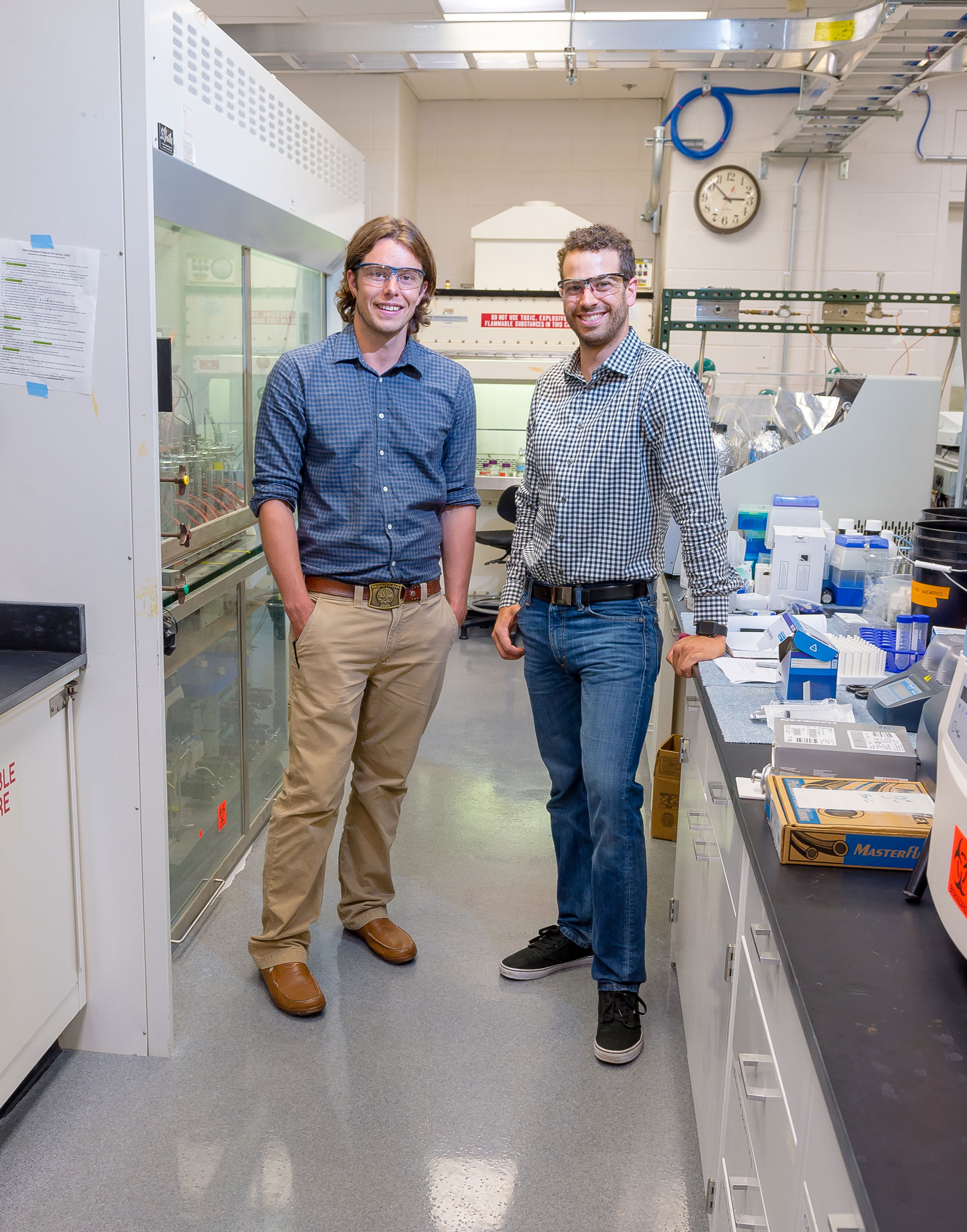
[Photo: Mark Lopez]
gb&d: So where do you fit in?
Whiteley: One avenue we’re pursuing is water filtration. Both of us recognize the extreme importance of clean water, and we would focus on targeting more specific components, such as lead. The metric for success in this case would be if we could make our carbon the premier material at removing some of the toughest components.
One application we’re pursuing is in the gold mining industry. In gold mining, large amounts of activated carbon is used during the gold extraction process, and this carbon is completely derived from coconut shells—a resource-limited and geographically isolated material that needs to be shipped all over the world. We’re working with some commercial gold mining partners to test out our material, proving that this would indeed work better. It means higher gold recovery, greater efficiency and, if you step back and look at it overall, lower energy consumption per amount of gold recovery.
gb&d: What has being part of the Argonne program meant for you?
Huggins: First off, it was a highly competitive process with many talented participants and great ideas, so I am very honored to be accepted into the program. Being part of this program means I can continue the development and commercialization of a technology I believe can help make the world a slightly better place, which I would not be able to do otherwise. It’s not like we could max out our credit cards and move into our parents’ basements; it is just too complicated. Â
Whiteley: It’s really invaluable. When we started to think about next steps for our company while still at Colorado, we were like, “We need to start a research lab.” That could cost a couple million dollars. Now we have lab space here that one of the scientists provided us. We have access to all the equipment. It allows us to work with the University of Chicago Booth School of Business—one of the best business schools in the world—who is helping us with business development.
gb&d: What’s been most surprising?
Huggins: That how good an idea is plays a very small part of what makes a technology successful. As I mentioned, activated carbon is used in a lot of major industries, some of the biggest, like energy and manufacturing. These industries are huge and slow moving, reluctant to try new things. The process of technology development takes time.
Whiteley: When we first started we didn’t have a whole lot of commercialization expertise. We’d been working in the lab for so long—you get this idea that what you’re working on, because it’s so amazing and so great, why wouldn’t people want this? You start realizing that some of the things you think are most interesting, like the sustainable aspect of this new material, are the least interesting to the person who’s going to be buying the material. We found that in order to really get these new renewable sustainable solutions out there, you have to be able to far exceed the performance of what they already have—and it’s going to have to be the same price or less … even if it is vastly outperforms it.”
gb&d: What’s next?
Whiteley: We are a quarter of the way in with the program (in July). We’ll be in the lab the rest of time. And we do still have access to these world-class labs after that (past the funding limit of two years). We fully intend to continue to research past that two-year timeframe. Next year, ideally we would like to set up a pilot plant.