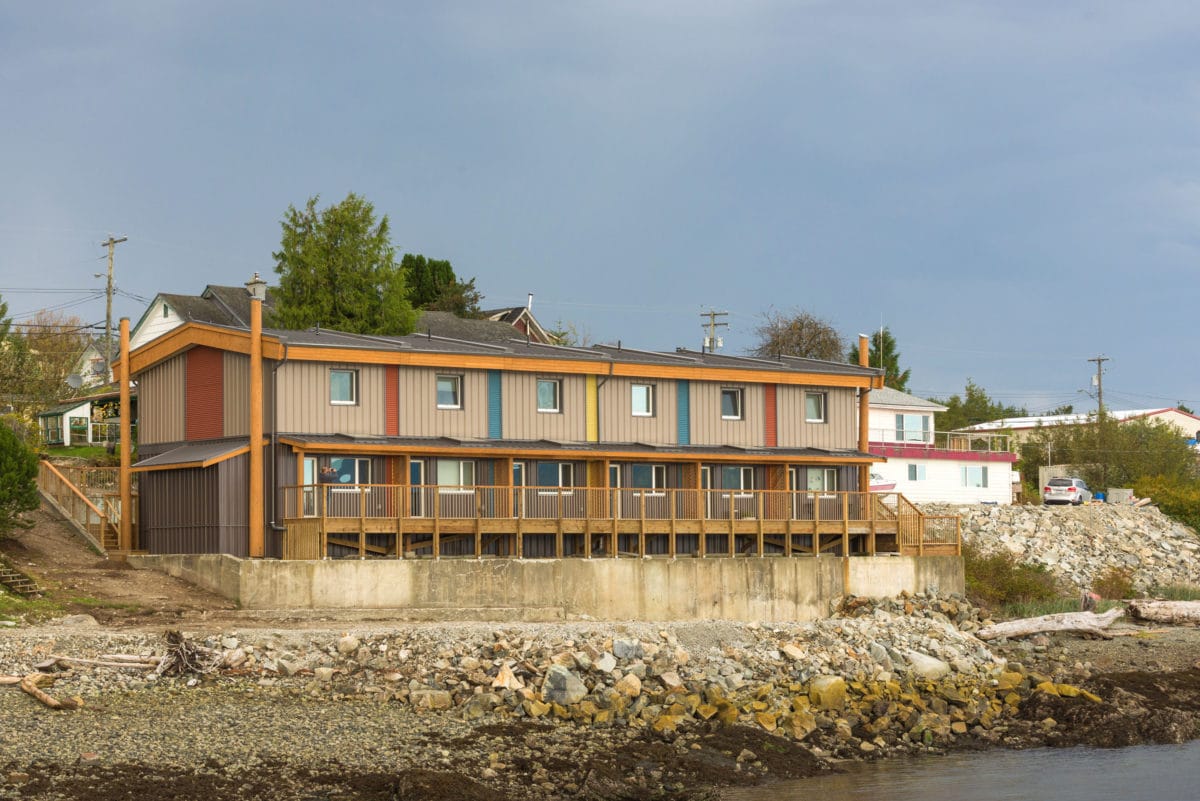
The Bella Bella house for staff of a remote hospital was built to Passive House standards, quickly and efficiently, using prefab techniques. [Photo: Courtesy of Vancouver Coastal Health]
On a remote island off the coast of British Columbia, the Bella Bella Passive House proves anything is possible
PROJECT
LOCATION
Bella Bella, British Columbia
SIZE
5,376 square feet
AWARDS
Audience Choice, Clean
Energy B.C. Generate 2015
COMPLETION
Early 2016
COST
$2.6 million (roughly a 5% premium on a conventionally built facility)
TEAM
CLIENT
Vancouver Coastal Health Authority
ARCHITECT
Mobius Architecture Inc.
STRUCTURAL ENGINEER
CanStruct Engineering Group
MECHANICAL ENGINEER
ITEC Systems Design Ltd.
ELECTRICAL ENGINEER
Opal Engineering
PASSIVE HOUSE CONSULTANT
Red Door Energy
BUILDING ENVELOPE
RDH Building Science Inc.
GENERAL CONTRACTOR
Spani Developments Ltd.
MODULE FABRICATOR
Britco LP
When a fire destroyed hospital staff housing in a remote part of British Columbia, no one was surprised by the plan to rebuild. But its location on rugged Campbell Island—where most of the 1,500 people living on the island belong to the Heiltsuk First Nation and it’s not uncommon to see whales swim by—made access to supplies and construction crews tricky. Add to that the decision to go from LEED to Passive House standards, and the undertaking was no small feat.
But it was all accomplished in just nine months.
The Bella Bella housing exists to help attract health care professionals to the far-flung hospital, which is part of Vancouver Coastal Health (VCH). The Bella Bella Passive House for employees at R.W. Large Memorial Hospital is made up of six, two-story attached townhomes. VCH has long been committed to energy conservation with sustainability policies that govern the design and construction of their health care facilities. But since the Bella Bella project wasn’t a clinical project but simply residential, the decision-makers were allowed to think outside of the box. That’s where prefab plus Passive House comes in. “It presented an opportunity for VCH to be innovative in trying a new energy conservation strategy more closely designed to meet residential needs,” says Glen Garrick, sustainability manager, transformation and innovation for VCH. “In the end the project was completed at a cost of $2.6 million—about $500,000 less than it would have cost to construct the development onsite.”
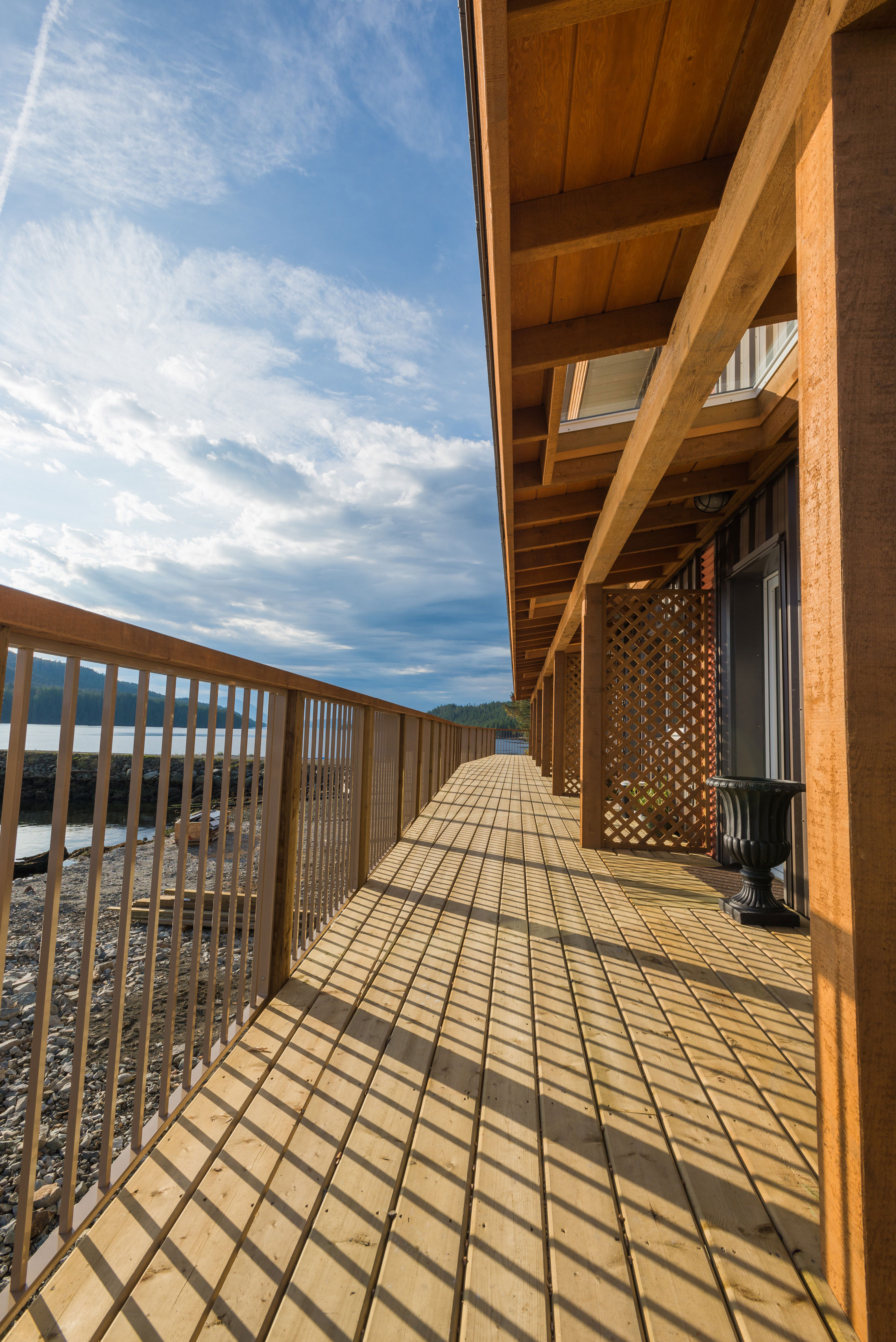
[Photo: Courtesy of Vancouver Coastal Health]
Considering its remote location—you literally have to travel over ocean from the mainland to get there—getting a construction team and supplies to the site was a top challenge. And finding the supplies and technical abilities there would be difficult, too. “A prefab structure taken up by barge presented a very quick and cost effective way to efficiently meet what would be needed in Bella Bella,” Garrick says. “They needed staff housing as soon as possible.”
The prefab structure was designed, constructed, and tested in a closed environment, ensuring a high-quality build and eliminating concerns like weather. Each story of each townhome was a module in and of itself—each approximately 32 by 14 feet, weighing more than 30 tons—made at a Britco factory in the province. The wood-frame construction included mineral wool, fiberglass insulation, and metal cladding built to Passive House standards, airtight windows, split-system heat pumps, and heat and energy recovery ventilation units. While the modules were being built in the factory, prep work started on the Bella Bella site—a common prefab practice that can result in a 30% shorter construction period.
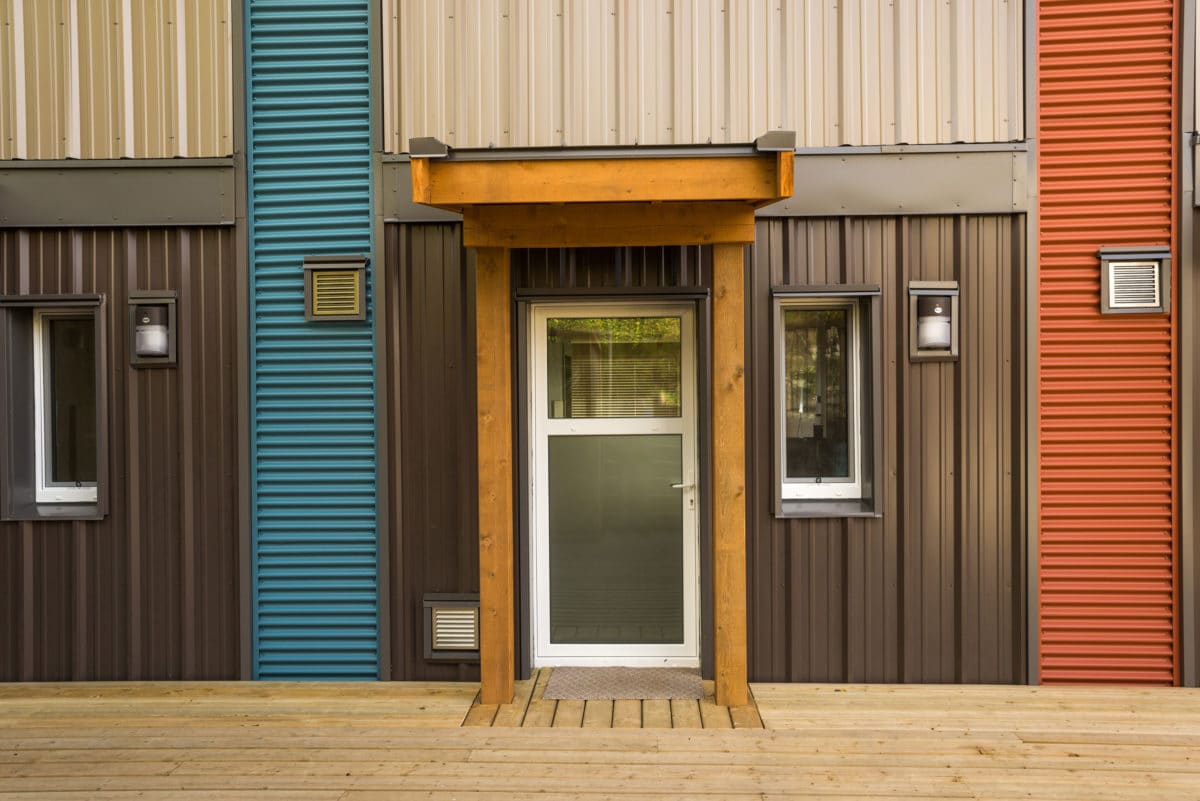
[Photo: Courtesy of Vancouver Coastal Health]
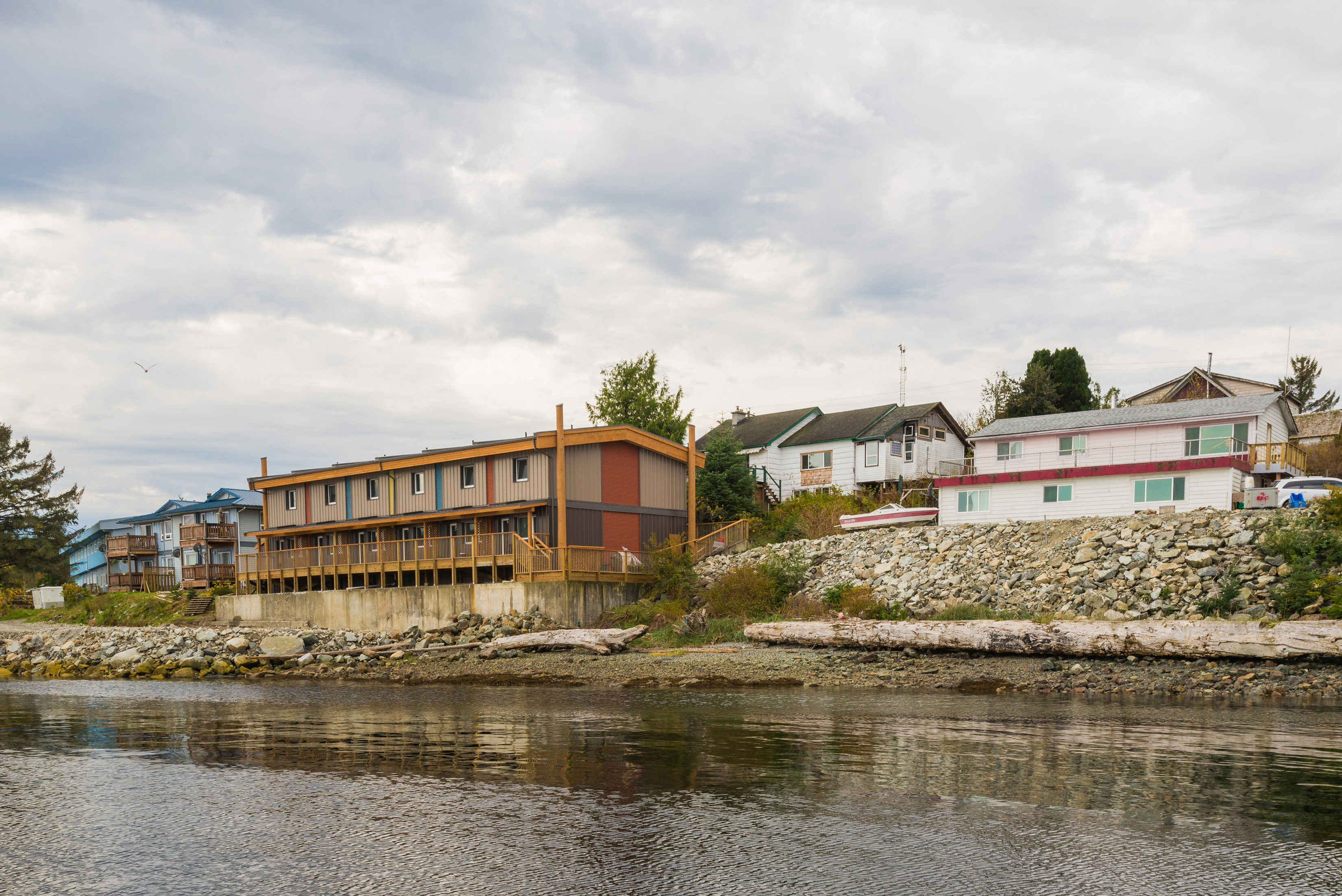
[Photo: Courtesy of Vancouver Coastal Health]
While the process wasn’t without its myriad discussions, all of the back and forth decision-making paid off in the end. “Whenever you push the envelope or try something new, it makes people uncomfortable,” Garrick says. “And those responsible for budgets and maintenance of facilities like this are the most anxious when trying something completely new. In the end, facilities management along with the energy and environmental sustainability team were able to educate key decision-makers enough to gain a level of trust to get the project approved.”
At the end of the day, it’s all about saving energy. While the final results haven’t yet been measured and verified,
Garrick says the savings is clear. “On one of the coldest nights of the year in Bella Bella, the occupants can still be kept cozy with just 600 watts of energy—that’s the equivalent of six incandescent light bulbs.”