Story at a glance:
- Unitized facade systems solve many of the ongoing hurdles facing the construction industry, including tight construction schedules.
- Unitization improves quality control because of preassembly in a shop where it is protected from environmental elements.
- In recent years the unitized market has incorporated new wall materials, like terra-cotta, wood, stone, brick, and metal.
It’s no secret that in today’s construction climate, increasingly tight schedules and rapid building close-ins are critical to success. Many factors contribute to a successful project, but the type of system and method of installation used on the building facade can have a large impact on a structure’s overall timeline.
Unitized construction is not a new development, but given the importance of quality, time, and ongoing labor challenges today, it’s a growing and evolving one. Here we take a look at the differences between stick-built and unitized facade systems, the benefits of unitization, and how new exterior wall materials are being used to drive the next phase of growth in the unitized market.
Stick-Built vs. Unitized
Let’s take it back to the basics and look at some key differences between stick-built and unitized facade systems.
Stick-built assemblies require an aluminum fenestration system to be delivered to the jobsite. The installer then assembles and installs the individual components on the structure, piece by piece. It can provide upfront cost savings over a unitized system as well as offer shorter product lead times.
However, stick-built systems require more onsite labor, which often results in more time spent on the installation process. Environmental considerations like weather delays can also impact the timeline. This can also be a factor in the quality control process, as more extreme conditions like high humidity, dirt, and temperature swings can impact the sealing process.
Unitized systems, on the other hand, are fabricated, assembled, and glazed in a factory environment, then shipped to the jobsite for installation. The large glass units are then hoisted onto anchors connected to the building.
A Deliberate Shift Toward Unitization
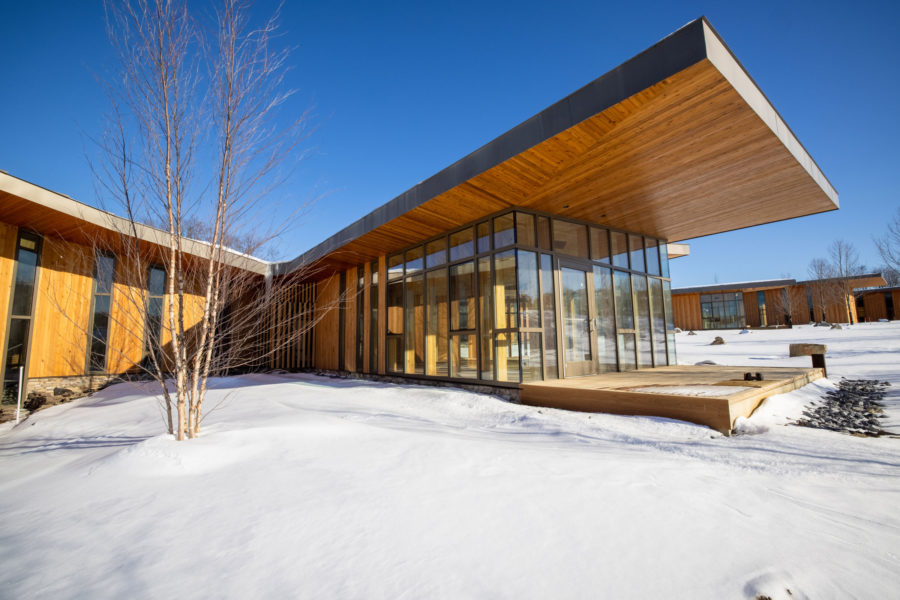
The JST Production and Engineering Center leverages YKK AP America’s YES SSG curtain wall to meet aggressive sustainability requirements. Photo courtesy of YKK AP
There has been a deliberate shift toward unitized systems to solve many of the ongoing hurdles facing the construction industry. Tight construction schedules, crowded jobsites, and a shortage of skilled workers and installers continues to plague the industry. Unitization addresses these issues while providing a high level of quality assurance and reducing overall project costs and time to close the building.
Traditionally unitized systems have been used in curtain wall applications and predominantly in high-rise projects like condominiums. However, there has been a more recent movement toward unitized or pre-glazing for low- to mid-rise projects. This has expanded the unitized market to products like window wall and storefront, bringing the benefits of unitization to a wider range of projects regardless of size or complexity.
The Benefits
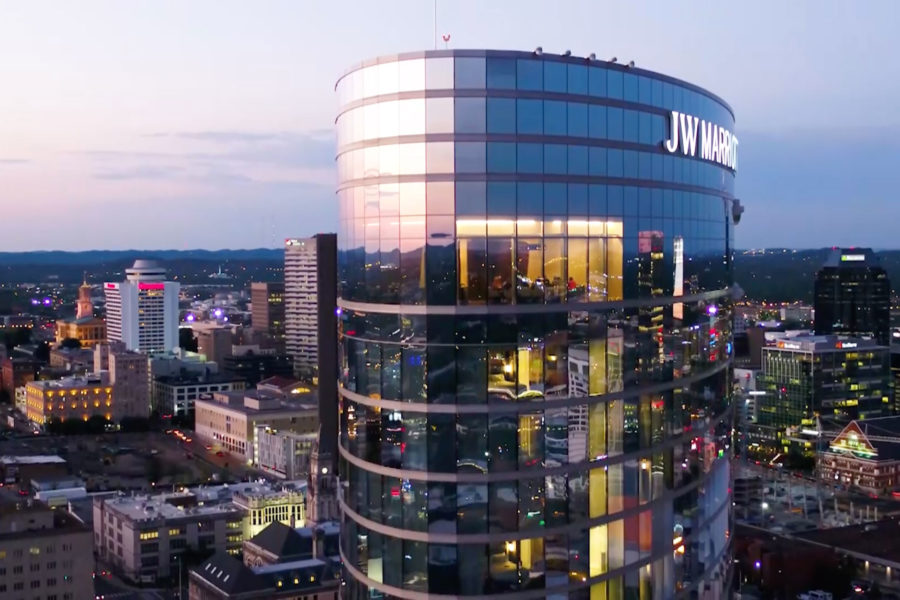
The JW Marriott Nashville utilizes YKK AP’s YWW 50 T window wall system to mimic the look of curtain wall. Photo courtesy of YKK AP
Unitized facade systems’ rising popularity is partly due to its various benefits.
Reduced Costs
Unitization lessens the use of more expensive field labor, often reducing overall project costs. As the labor shortage continues to plague the construction industry, the lack of skilled workers has raised the cost of field labor. Because unitization provides for shop fabrication, glazing, and assembly, it drastically reduces the amount of labor needed at the jobsite. More can be done at the jobsite, working faster to meet demanding deadlines. This can lead to huge overall cost savings for the project.
Improved Quality Control
Unitization improves quality control because of preassembly in a shop where it is protected from environmental elements. In a more traditional, stick-built approach, units are assembled in the field, where environmental conditions and disruptors at the jobsite may impact the end product.
Unitization takes this out of the equation and brings the entire fabrication and assembly process into a controlled environment. The manufacturers or glazing contractors shop is an ideal setting for critical seals, where environmental factors like dirt and rain are not a problem. Dry-in time can be significantly faster than onsite glazing, expediting the time it takes to close the building. Additionally, staff is more closely supervised in a shop environment—from monitoring attendance to supervising work assignments—which provides improved quality assurance in the fabrication of all components.
Suitability for Dense Areas
Unitization can bring strong benefits to projects in large cities where there may not be enough space or time. The unitized movement has been most apparent in densely populated urban markets, where labor is expensive and installation is difficult from a logistics standpoint. As unitized systems come to the jobsite ready to be installed, they save a significant amount of space in these urban environments where there is a limited ability to store materials, stage, and glaze large units onsite.
New and Innovative Materials
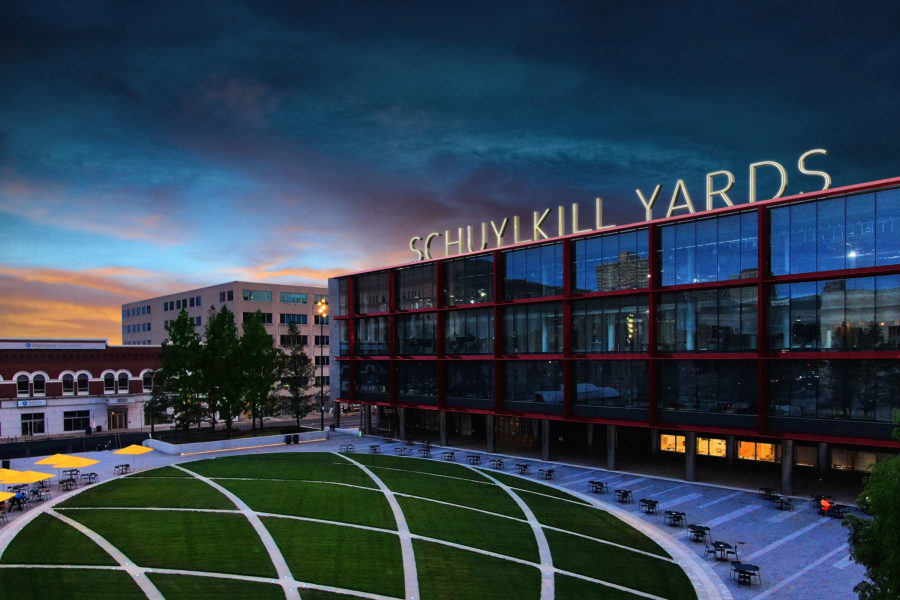
Photo courtesy of YKK AP
Over the past year, one of the biggest changes in the unitized market has been the incorporation of new wall materials. Terra-cotta, wood, stone, brick, and metal are the new go-to materials to create a more innovative facade.
“We’re seeing continued demand from architects to incorporate materials like terra-cotta and metal panels,” says Tim Thomas, president of YKK AP subsidiary, Erie Architectural Products. “This is definitely a growing market, and we see the ability to glaze in other materials in the future.”
These infill materials are inserted into the curtain wall panel between the aluminum mullions. In the past materials like spandrel glass have been incorporated to provide a unique all-glass facade. Today stone and terra-cotta are providing more sophistication and more dimension.
The ability to provide a unitized curtain wall with these new materials allows architects to meet the same tight deadlines and provide a rapid building close-in while continuing to push the envelope with an innovative building facade.