Story at a glance:
- Westcoat manufactures systems for waterproof decking on balconies and around pools.
- ALX is specifically designed for plywood substrates, while MACoat is specifically designed for concrete substrates.
Protecting facilities from water damage and people from slippery surfaces is paramount across multifamily residential towers and beyond. Westcoat has been manufacturing deck coatings for more than 30 years, with systems installed all over North America. While the manufacturer focuses on resinous flooring—think epoxies and urethanes—they also make concrete stains, sealers, cementitious overlays, and top-quality waterproofing systems.
Westcoat manufactures systems for waterproof decking on balconies and around pools as well as offers solutions for protecting and beautifying parking areas, walkways, or rooftop decks. Whether the project has a concrete or plywood surface, they have a solution to treat and protect.
We recently talked with Westcoat Product Manager Todd Cook to explore the details of the manufacturer’s waterproofing systems.
What are the types of Westcoat waterproofing systems?
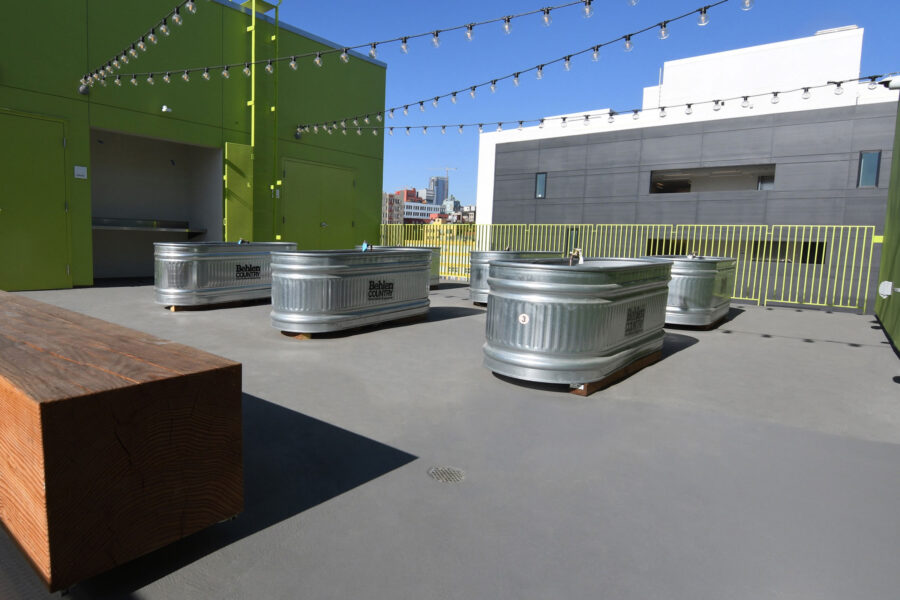
The MACoat system is specifically designed for concrete. Photo courtesy of Westcoat
We have two premier systems—the ALX and the MACoat. ALX is specifically designed for plywood substrates, whereas MACoat is specifically designed for concrete substrates. The ALX is a fire-rated metal lath and cement system.
What substrate does the ALX require?
For all waterproofing systems the substrate is critical. Without a sound substrate there’s no point in continuing with the system. The ALX System requires a minimum 5/8-inch exterior grade plywood, with a maximum joist span of 16 on center. Decks should be tongue and groove plywood that is properly blocked and fastened. This is all going to create a robust substrate that will limit the deflection or movement that occurs, which then will allow our systems to perform very well.
What should multifamily customers be aware of regarding their substrate?
- ALX Pro installed on a multifamily balcony. Photo courtesy of Westcoat
- Photo courtesy of Westcoat
For reconstruction projects it is important to take the time to properly evaluate the existing substrate to ensure it’s free from damage and suitable to apply the ALX system. If they’re building new they can build correctly from the start. It saves a lot of time.
With reconstruction or new construction it is very important to reference the manufacturer’s substrate requirements, as well as local building code. Understanding the minimum requirements can reduce costs, delays, and support for a better overall outcome for the project.
Slope is another key element to consider. Westcoat requires a minimum quarter-inch per linear foot of slope. That’s built into the framing; that way we ensure we have positive drainage, so water is going to really flow off the deck and we’re not going to get ponding or issues with drainage.
How does Westcoat help prevent drainage issues?
Although it is best practice to have sloping built into the framing, we have the functionality in our ALX and MACoat systems to use what we call our Slope Technique. Essentially that is an easy-to-apply component that can be used in tandem with Westcoat waterproofing systems to help create pitch and better flow. For example, a lot of times on a deck they might install drains, and to get the water to go to the drains you need to do what’s called cricketing. Cricketing is basically a way to create positive drainage and slope to those low points or to those drainage points.
What is the best waterproofing for plywood?
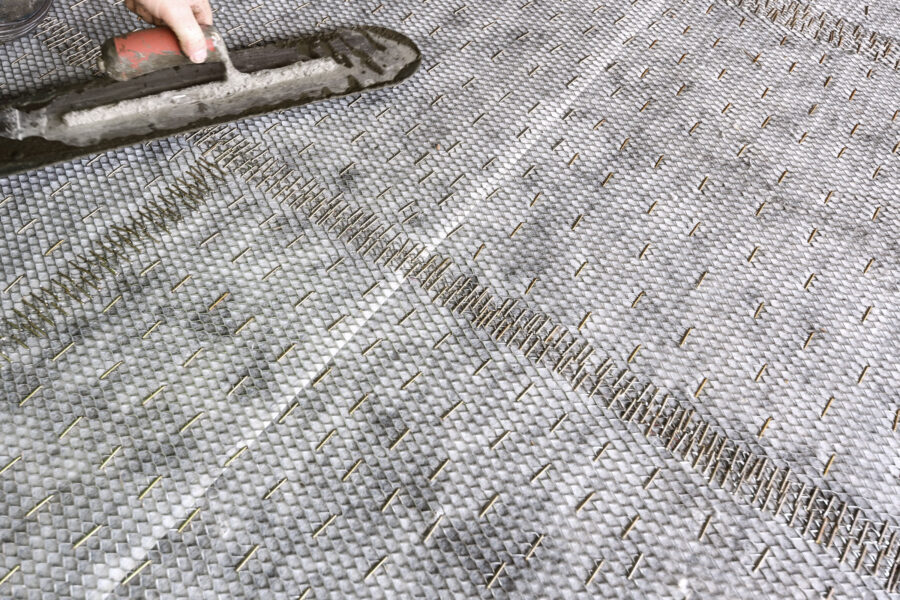
Closeup of metal lath detail in the ALX. Photo courtesy of Westcoat
The ALX System features the WP-40 Sheet membrane. That is a 40-mil thick waterproof membrane that’s applied at a minimum to all plywood seams. It can also be applied across the entire deck providing additional waterproofing. When applied across the entire deck it will provide a Class I vapor retarder per ASTM E96. That’s giving you additional waterproofing, anti-fracture, and it’s a very functional waterproofing sheet membrane that can be used in tandem with a standard system.
Once the sheet membrane is installed we apply our WP-25 Metal Lath, a G60 hot-dipped galvanized metal lath. It’s mechanically fastened down with our WP-10 staples. These are high-quality staples made in America. Those are fastened to create the armature or the skeleton of the system. Next we install a series of polymer modified layers that create a robust waterproofing system. They’re fast-drying, low VOC, low odor, and easy to apply. All of these are acrylic formulations that provide a solvent-free installation. That means it’s going to be much more environmentally friendly.
What are benefits of ALX for multifamily buildings?
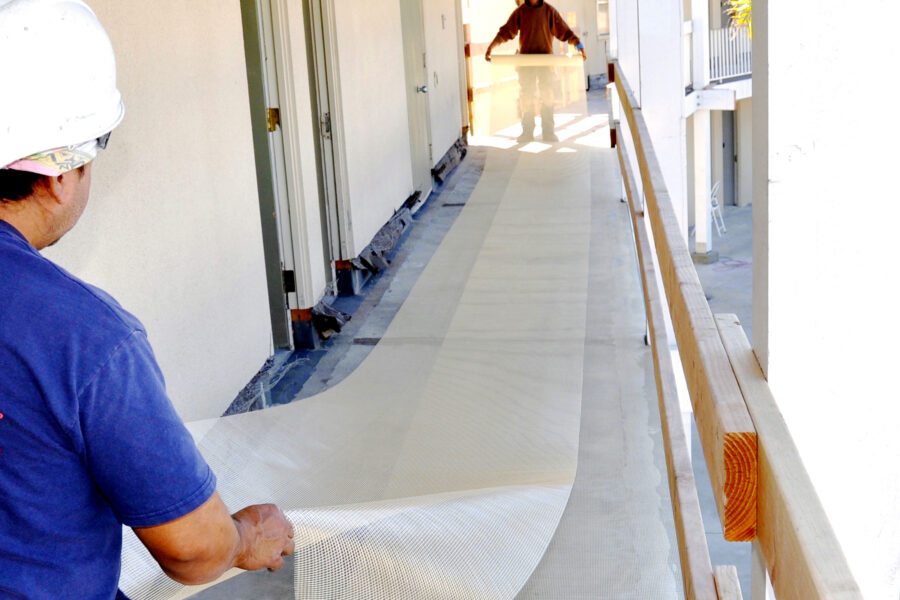
Photo courtesy of Westcoat
A lot of times when we’re working with multifamily reconstruction projects you want to be mindful that a lot of these projects may have inhabitants. We’ve got tenants still living there—how do you work around that? One benefit is having a fast-drying, user-friendly, tough system like ours.
Another important factor for projects with tenants or other trades is avoiding materials with obnoxious odors. Smells can be pretty strong. That’s not the case with either the ALX or MACoat systems because of their low- or zero-VOC materials. That’s going to make it very appealing for property managers because work may resume while you still have tenants occupying some of these units. We can even work around them and create faster drying layers with accelerators and other additives to help work within your limitation.
What if you want something even stronger?
We have our fiberlath resin membrane. That is offered in ALX Pro System—essentially the premier version of ALX; the only difference is we add an additional layer. This adds a high-strength reinforcing fiberlath that is combined with a resin-rich cementitious application.
When is ALX Pro best?
The ALX Pro is ideal for larger decks with larger spans in cases where additional crack resistance is required, additional stability, and/or waterproofing is required. In addition, the ALX Pro will offer an extended warranty because you are upgrading to a bit more robust system with additional layers.
What about slip resistance?
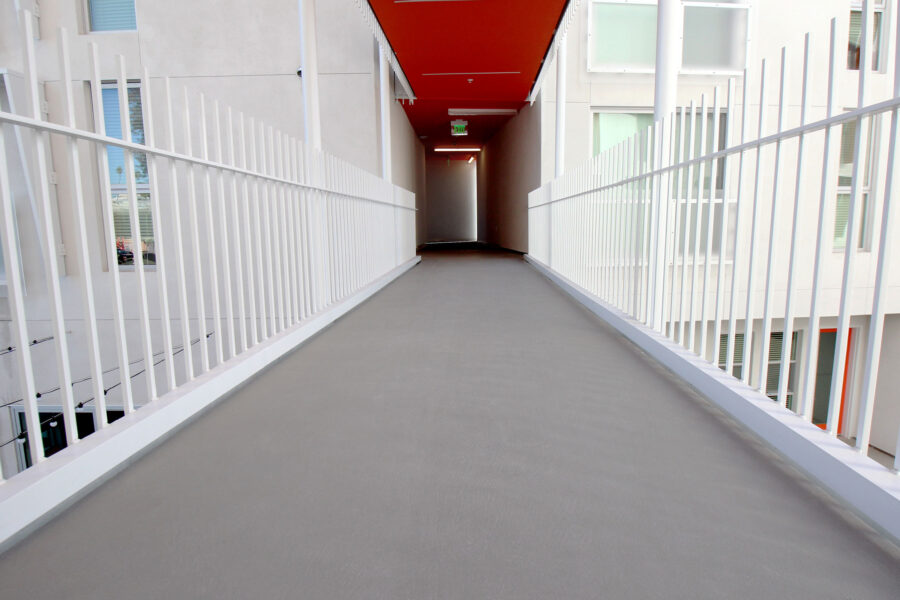
This walkway is protected by the ALX system. Photo courtesy of Westcoat
All of the standard ALX systems have a slip-resistant finish that is easy to maintain with an acrylic topcoat. That makes it durable, functional, and provides a slip-resistant and safe surface.
For a lot of property managers that is a concern—slip and falls and those types of hazards. We have the ability within our system to meet or exceed any slip coefficient values or slip resistance numbers by utilizing our Safe Grip additives. We can provide the needed balance between cleanability and slip resistance.
We also want to have discussions with those clients. If it’s a small deck, for example maybe a small, private deck like a Juliet deck, in most cases we’re not going to do that aggressively textured finish because it’s very small; there are minimal slips and falls, and it’s usually isolated to a single unit. We’ll make that deck maybe a little bit less slip-resistant and easy to clean.
On the flip side, we might have a large podium deck or long walkways and open areas where there may be greater risks of slip hazards. We definitely want to increase our slip-resistant loading there, so we make sure we have a nice safe surface.
What is the AC39 criteria for walking decks?
- Large podium deck with MACoat custom finish. Photo courtesy of Westcoat
- The MACoat waterproofing system has an extensive record of being used as a method of rehabilitation for existing decks. Photo courtesy of Westcoat
AC39 is the acceptance criteria for walking decks. AC39 features a list of required tests, such as accelerated aging, bond strength, water absorption, etc. It’s critical that you meet those tests within AC39 and then work with an evaluation service like IAPMO to produce an evaluation report. This report helps to cover the overall technical review, provides clear installation instructions, definitions of materials and provides proof to the evaluation organization. This documentation demonstrates the overall caliber and durability of the system.
How does ALX hold up in a fire?
The ALX system is really popular not only in California but everywhere nationwide because it offers a Class A and a one-hour fire rating. That is in accordance with ASTM E108 and ASTM E119.
It also meets the Wildland-Urban Interface requirements, which are very important when it comes to fire preparedness. That’s becoming more of a requirement in certain areas, especially in California, but of course with the fires in Canada, it’s definitely becoming more critical to have these additional fire tests.
What about the MACoat system? How does it differ?
The MACoat system is specifically designed for concrete. It consists of a fiberlath reinforced deck system. It’s installed with a series of waterproof acrylic applications. It has a very extensive record of also being used as a method of rehabilitation for existing decks.
How can MACoat improve an existing deck?
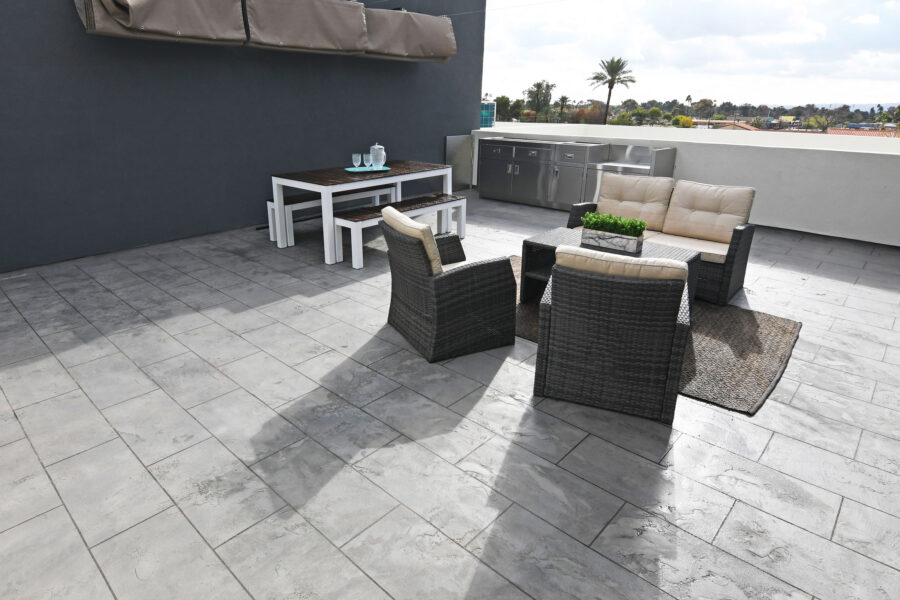
Waterproofing systems like the ALX improve rooftop patio decks. Photo courtesy of Westcoat
Say there’s an existing deck system that’s been down for 25 or 30 years. It’s fairly intact, but you want to extend the life cycle of it. Property managers are faced with a bid to completely remove the system, which in some cases might also mean removing the existing flashing; they might have to remove the siding, the railing, stucco, adjacent finishes. In some cases that can drive the price of a project up extensively, when the system is still intact and the flashing and other areas are still performing very well; they just need a little bit of love or more reinforcement on the waterproofing.
In that case we can put the MACoat directly over a lot of systems to extend that life and help offer a more cost effective method, still providing the waterproofing. That’s a great rehabilitation method that helps with budgets and is a great way to preserve and also reduce sometimes excessive waste.
Sometimes it is absolutely best practice to remove and start over—identify what’s under substrates, examine the adjacent finishes and walls, and install new flashing. But when it’s been determined everything is sound, it’s a perfect solution for using the MACoat system as rehab.
What is MACoat made of?
The MACoat consists of the WP-47 fiberlath, which is a high strength reinforcing fabric. It also features our TC-1 basecoat cement that is combined with the WP-90 waterproofing resin. The WP-90 waterproofing resin is a very high solids, fast-drying, zero VOC resin that offers really good adhesion and great flexibility. Combine those two materials and it creates the MACoat system.
The MACoat system is a Class III permeable vapor retarder and waterproofing system. Unlike traditional urethane deck coatings, the MACoat system can breathe. That is really important when you’re on some concrete decks and traditional urethane coatings have failed. With traditional urethane deck coatings they might blister or have problems because they are not permeable and breathable.
Do you offer solar reflectivity?
In both our ALX and MACoat systems we have a solar reflective finish. This features the same accredited assemblies and the same components for the most part, but it utilizes our solar reflective topcoat line. It provides a very high SRI value and certification through the Cool Roof Rating Council. That will help to reduce the urban heat island effects and for some projects might even contribute to LEED credits. That becomes more and more important as we start to see climate change effects. We’re getting more requests from architects.
What should property managers know when choosing a waterproofing system?
What’s the size of the deck? How much traffic do you expect? Things like that are really important. That may determine what system we choose or what topcoat or finishes are used to create the most durable finish to support that particular project.
We also need to understand if it’s new construction or reconstruction or rehabilitation. What’s the turnaround time? Is the project in the winter or summer?
We also want to know—is there an existing coating? What’s the condition of the substrate? Is it structurally sound? Is it clean? Is there damage? Was there an existing coating or waterproofing type of technology? If so, what’s the condition of that coating? And what was its history?
That information can be helpful because if there was an existing coating, and let’s say it didn’t perform as intended, we would not want to repeat with a similar type of chemistry. But if they put down something that didn’t hold up very well, we want to know why it didn’t not hold up very well. Maybe it was installed incorrectly, or it was not appropriate for that environment. Having these general checklists and scripts will help you get a better understanding of what the project is and how to move forward.
It’s really important to choose a waterproofing system that has been evaluated for the AC39 acceptance criteria for walking decks. It’s really important that they check that because in that system criteria they test for bond strengths, freeze/thaw, accelerated aging, and a lot of really critical tests that are in AC39.
Additionally, make sure it has an active evaluation report through organizations like IAPMO or ICC. That gives a lot of checks and balances and accountability, ensuring the manufacturer is being held responsible for what they’re saying.
What about aesthetics?
We have really unlimited capabilities as far as textures and patterns and can support custom colors for those projects that require this. All finishes are covered in our Evaluation Report.
Decorative patterns and textures are all possible. In some cases customers want to do traditional finishes; for example, they want to put tile down. Our waterproofing underlayment versions of ALX and MACoat are a complete waterproofing system that allows for tile, concrete, or stone as the decorative finish.
Who can install these systems?
We like to ask: What’s the skill or ability of the applicator or contractor? We recommend people choose a licensed and insured applicator. We have our QCA program, and we recommend you utilize these types of applicators because we’ve done some auditing and determined that yes, they have the extensive experience to install these types of chemistries and systems. They’re licensed and insured.
Where do warranties come in?
Everyone’s interested in a warranty. In addition to seeking that accredited and evaluated system, it’s important to look at the warranty. There might be different lengths of warranties depending on which system. For example, at Westcoat we offer up to a 20-year warranty on our ALX Pro premier system. That’s industry leading in terms of a metal lath system.
Deck Inspection Checklist
Westcoat also offers a helpful deck inspection checklist for above grade decks, balconies, and walkways. This can be utilized by property managers or owners. That inspection checklist helps to promote education and awareness around some of the key elements associated with waterproof decking.