Story at a glance:
- Utilizing precast concrete’s inherent energy efficiency (high R-value) greatly reduces overall energy usage.
- Building with precast requires less onsite labor, as much of a structure is built offsite in a controlled factory setting.
- Aboveground markets are turning to precast more—including schools, retail stores, car dealerships, and others.
Tall, high-end retail buildings, office headquarters, public schools—more builders across markets are turning to precast to get their projects up fast and sustainably.
“There is a lot of design opportunity with precast, and you still get the benefit of building out of concrete, even when it includes brick or high-end finishes,” says Jackson Metcalf, who co-leads the Critical Facilities Practice at Gensler, responsible for designing many data centers. Data centers used to be what many architects thought of when they heard “precast concrete,” but today they’re designing so much more.
Producing a concrete structure offsite in a controlled factory setting before shipping it in panels to the jobsite is nothing new, but more sectors are considering precast now than ever.
There is a lot of design opportunity with precast, and you still get the benefit of building out of concrete, even when it includes brick or high-end finishes.
For more than 50 years Fabcon has been helping these projects go up quickly, efficiently, and precisely. Fabcon leads the industry in producing precast concrete buildings ranging from very large industrial buildings with heights well over 60 feet to high-end retail and more.
“We’re seeing increased adoption in schools and retail stores. For data centers precast has long been the way to go, but there’s also growth in office buildings and mixed-use development, and we’re seeing a lot of growth in community and public buildings,” says Tim Anderson, vice president of sales and marketing at Fabcon.
Metcalf has also been part of teams designing high-end retail stores using precast, including shopping in Chicago’s Gold Coast, where the material was used to mimic Indiana limestone. In Los Angeles Gensler’s EPIC project used precast to result in a beautiful vertically stacked and terraced office space with views to the Hollywood hills. Completed in 2019, EPIC’s entire punched opening envelope is precast. The building is LEED Gold–certified and is one of the most environmentally friendly office buildings in LA.
We recently talked to experts at Gensler as well as Fabcon about the benefits of using precast concrete today.
Design Flexibility
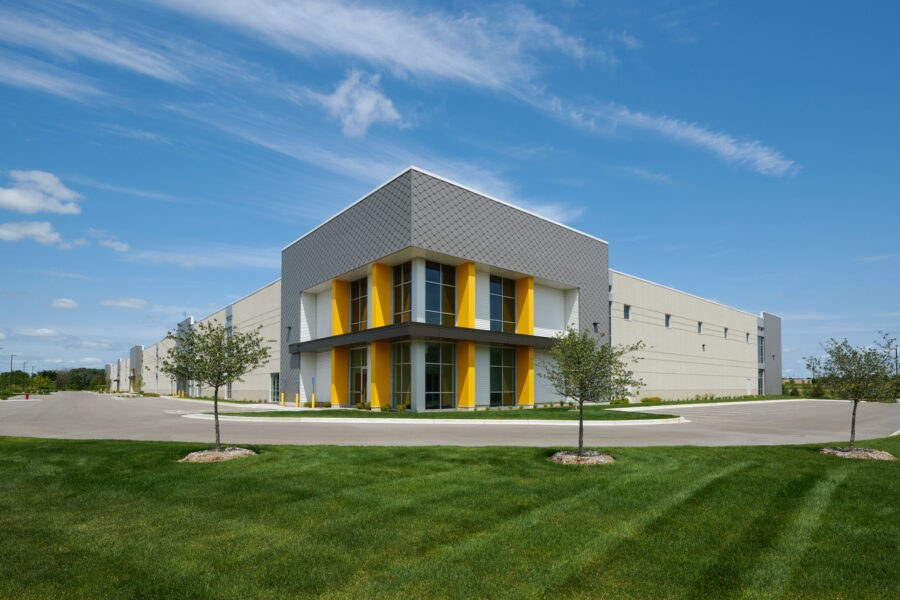
The Chaska Creek building combines precast concrete with color and clerestory windows. Photo courtesy of Fabcon
Beyond its popular use on data centers, Metcalf has worked with precast to build many corporate headquarters—often using it as a horizontal spandrel between sections of glazing, as an accent material, and more. Some projects include an inlay of stone and different types of finishes with precast. “We’ve used it in higher end architecture, and we’ve used it for a long time,” he says.
Precast has long been used in Gensler offices in the Midwest, as Chicago has a competitive precast market. “We have a lot of options. That also means there are a lot of people who really know what they’re doing. We get really good quality material.”
Metcalf says it’s unfortunate that some people misunderstand precast as simply an industrial material or a low-end option because it’s commonly used for warehouses and data centers. “You can design parking garages with actual brick cast into it. You can do a data center and expose the natural material—both for low maintenance but also to be authentic to the material. We also apply aggregates, form liners, and other textures. There are a lot of design opportunities with precast. You can make it mimic things like limestone. It doesn’t have to look like a distribution center.”
Anderson says design teams can easily paint the concrete or cast-in-brick so the finished project itself looks like a brick building. They can add high-end finishes like acid etching and sand-blasting, too.
Precast concrete also comes with an inherent fire rating and durability to protect occupants from things like tough storms. A growing number of storm shelters are being built using precast, Anderson says. He says precast buildings are more likely to stand up to everything from hurricanes and tornadoes to blizzards and earthquakes. “Concrete buildings can be both beautiful and resilient,” Anderson says.
Save Time
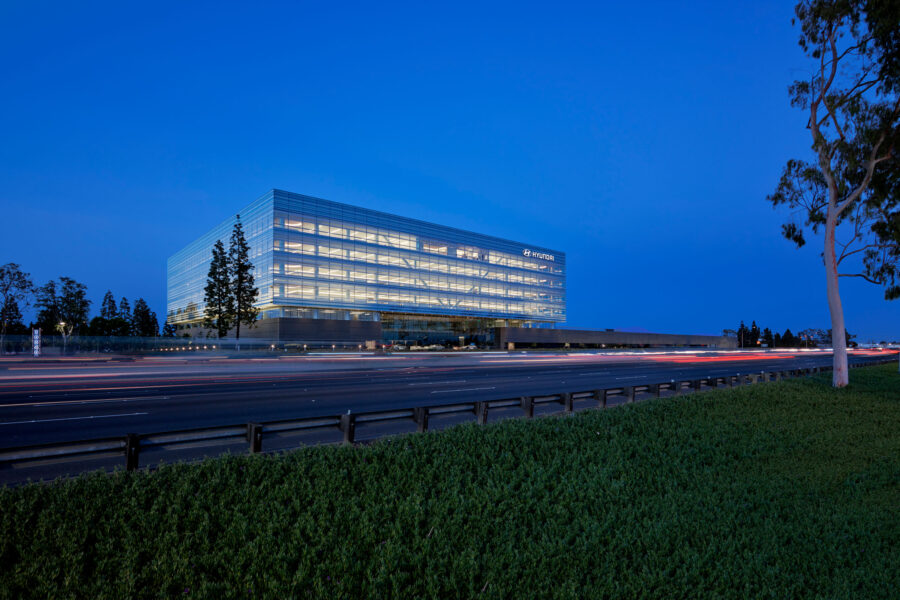
The Hyundai Motor America US Headquarters in Fountain Valley, California was designed by Gensler, built with precast concrete, and encased in a glass and metal curtain wall. Photo by Benny Chan
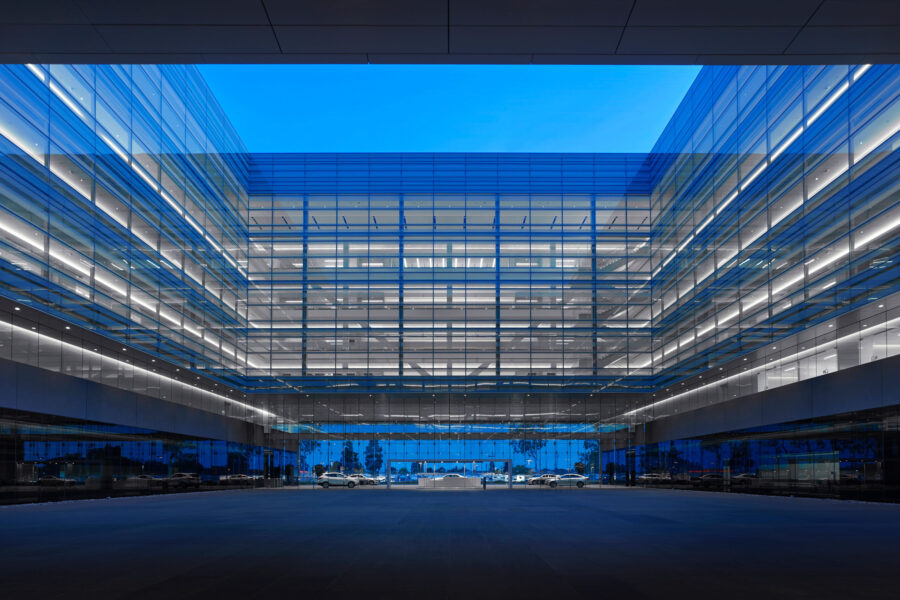
The Hyundai Motors building base, completed in 2015, is all precast. Photo by Benny Chan
Beyond its aesthetics and strength, Metcalf says precast also tends to shrink the construction schedule, as projects go up faster and use a single subcontractor. “You can get an envelope and a whole roof up in a pretty short amount of time. It’s great.”
Anderson says precast allows you to get a building occupied much quicker than with site cast or other construction methodologies. Reducing construction time has been a hot topic for many architects and the public alike, according to Anthony Brower, global climate action and sustainability leader at Gensler. He says many residents express that they don’t want big construction projects in or near their neighborhoods, as they don’t want their children breathing in construction materials for years at a time. “With precast you’re doing more offsite so you can shrink that construction window,” Brower says.
Sustainability
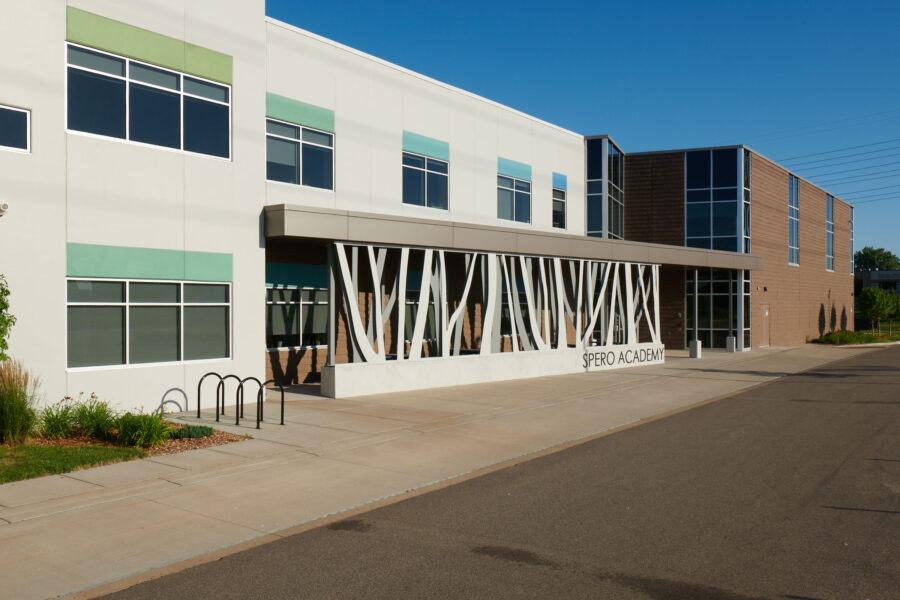
Precast has high load-carrying capabilities and high insulation (R-Value) properties. It was used here for the Spero Academy in Minneapolis. Photo courtesy of Fabcon
In the past concrete and cement were considered to be among some of the least sustainable materials for their carbon dioxide emissions and global warming potential (GWP), but that has changed. Anderson points to the recycled content in precast, for starters. “At Fabcon we use up to 58% post-consumer and post-industrial recycled content,” he says.
And while everyone talks about the GWP of using concrete because making it is so energy-intensive, he says the life of the product also cannot be forgotten. Roughly 85% of a building’s GWP comes not from the actual building materials, Anderson says, but the building in use—what it takes to run the building versus the products used to build it. “One of the big benefits of using precast is that if you build a more energy-efficient building, you can reduce the life cycle usage of the energy of that building,” he says.
And it’s no secret that the construction industry produces an enormous amount of waste. It’s expected to produce 2.2 billion tons of solid waste by 2025, Anderson says. He says precast reduces onsite waste by up to 50%. “We want to push people toward using precast not only for the CO2 emissions or GWP but also from a solid waste reduction standpoint—offsite construction versus onsite, plus the reduction in need for onsite skilled labor,” he says.
More end users are taking sustainability seriously, too, demanding proof that the processes and materials they choose for their projects are environmentally friendly. Anderson says many are asking for Environmental Protection Declarations, or EPDs. “It’s not just what buildings are being built out of but what are the insulation benefits and everything else?” he says. “You’re looking at all that energy use while the building is in operation as well because if the building envelope is more energy-efficient you have to take that into account.”
Precast’s high strength to weight ratios also allow teams to design taller buildings while utilizing less material and increasing energy efficiency through the integral use of insulation. In many areas of the country buildings are being required to have higher R-values, and that’s driving people to more frequently consider precast, Anderson says.
Metcalf says large format precast panels certainly help projects to be more energy-efficient. If precast concrete panels are being used as the primary cladding for a data center, for example, he says that’s likely an insulated sandwich panel, so the building is going to be super well insulated.
Using precast also means the building can live a longer life. When Metcalf started designing data centers Gensler was building them to be 50- or 100-year buildings. They were extremely robust buildings that could also be reused. “It’s well built, and it has the ability to give back with future uses. That’s one of the areas the precast can come into play,” he says. “If you’re building simple lightweight structures, there’s an element of them being disposable architecture. Building with heavier materials that will have a 50- or 100-plus year lifespan, like a precast or other heavier weight material, there’s a greater incentive to preserve those buildings for future use rather than tear them down when they’ve reached their end of first life.”
Exciting innovations are also happening in concrete, Brower says, like CarbonCure—a new, sustainable concrete solution with carbon removal technologies. “This reduces the carbon impact because it reduces the amount of cement,” he says. “Some of our structural engineers say it’s also increasing the strength of the concrete as a byproduct.” That said, he noted that solutions like these are still relatively new, so their firm will see how they stand up over time.
Labor Benefits
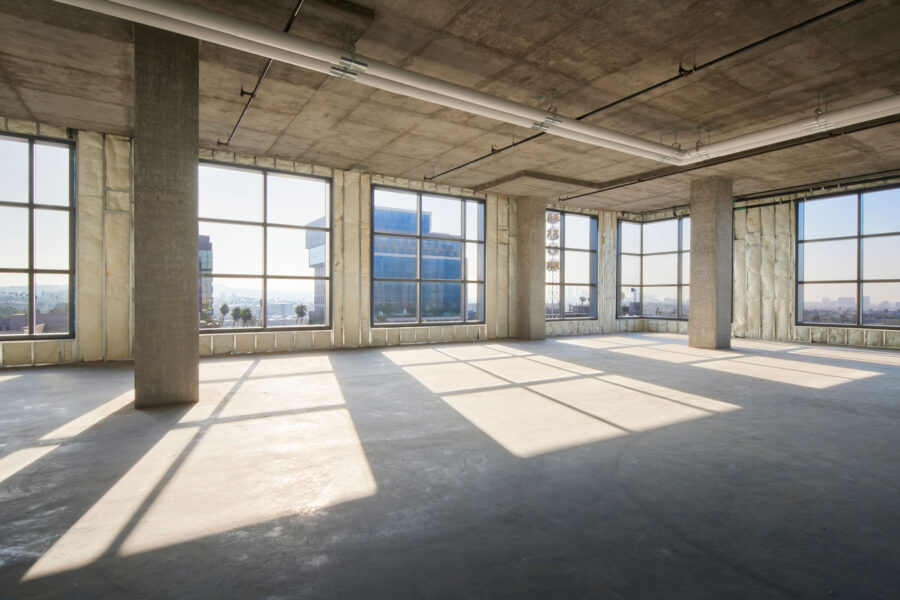
The EPIC project’s entire punched opening envelope is precast. Photo by Makena Hudson
Precast concrete can also reduce labor costs by up to 25%, and Fabcon has its own team at their plant. “We use 25% less labor in our controlled environment than you’d use building a building onsite,” Anderson says.
This continues to be important as the construction industry faced a consistent labor shortage in 2023, according to the Associated Builders and Contractors. “That lack of skilled labor onsite is driving the entire construction industry to offsite,” Anderson says.
When you buy a precast building and work with Fabcon, he says you’re buying an erected finished product and get the benefits of working with their in-house engineering, project management, and construction teams. “You’re getting a turnkey solution, end to end.”