Story at a glance:
- Carnegie Fabrics is now offering WOOD-SKIN panels, innovative architectural panels made in Italy.
- WOOD-SKIN panels are created using technology that tessellates the surface of a 3D model.
- The architectural panels are easily customizable using an online configurator.
Carnegie Fabrics and WOOD-SKIN are taking interior spaces to the next level with innovative WOOD-SKIN panels—a 3D design that quite literally jumps out and adds detail in surprising ways, whether you want to add some visual oomph to a wall or bring life to a ceiling.
“We’ve been working at the intersection of the digital and the physical for years, with the aim of creating a high-strength material that shares the same properties as a fabric,” says Giulio Masotti, CEO of WOOD-SKIN, in a press release. “WOOD-SKIN systems are the result of a hybrid approach between unmatched Italian design and advanced manufacturing technologies based on parametric design.”
Milan-based WOOWOOD-SKIN is an interdisciplinary company of architects, designers, and engineers who are passionate about materials, details, digital manufacturing, and software. Carnegie is the sole North American distributor of the company’s paneling products, which utilize the patented WOOD-SKIN process that makes rigid surfaces flexible and flat surfaces three-dimensional.
“Carnegie has always championed innovation within the design industry, and we’re thrilled to add WOOD-SKIN to our diverse portfolio of offerings,” says Heather Bush, chief creative officer of Carnegie Fabrics, in a press release. “We strive to create unique products that provide novel solutions and are excited to see how our clients will utilize such a versatile material within their projects.”
Compelling Geometry
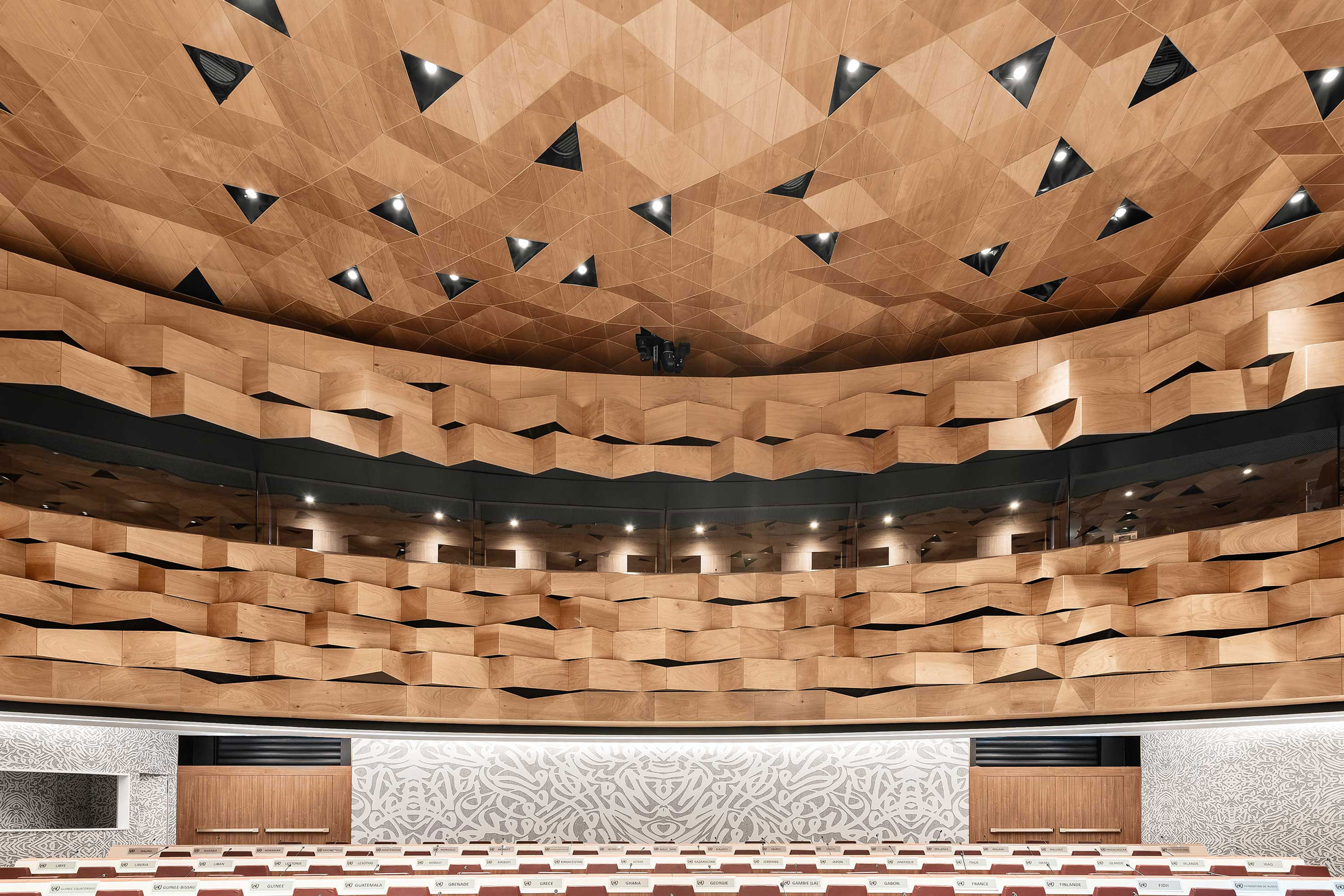
WOOD-SKIN architectural panels. Photo courtesy of WOOD-SKIN
WOOD-SKIN panels are created using proprietary software and technology, a direct file-to-machine process that tessellates the surface of a 3D model, generating its precise unfolded geometries onto sheets of rigid composite material.
Once machined, each sheet is connected through a textile core to re-create the exact configuration of the digital design without the use of heavy and expensive structures.
Plentiful Options
- WOOD-SKIN’s Mesh Sheets. Photo courtesy of WOOD-SKIN
- WOOD-SKIN’s Mesh Sheets. Photo courtesy of WOOD-SKIN
Clients can define the external layers by choosing from a wide range of materials, including wood, laminates, aluminum, and felt. The brand offers three systems: Mesh Sheets, Fold Panels, and Tailor Made.
WOOD-SKIN Fold Panels are 3D panels with intriguing geometries, built within a rectangular or square module. Fold Panels is designed to transform a space with the colors and configurations that best fit the project’s overall vision. A robust frame keeps the shape and makes it easier to install on walls and ceilings. The design is highly customizable, too, with an online configurator designers can use.
With Mesh Sheets, you can create sleek, 3D membranes using rigid materials like wood or aluminum while achieving the look and feel of lighter, flexible materials like paper or fabric. Considering the varied size of the facets and the parametric nature of the product, its curve radius can be very tight while still maintaining fluidity.
The standard solution uses certified metal wires with a quick tensioning system to connect the wooden flaps on the WOOD-SKIN assemblies to the ceiling/wall.
Giving Back
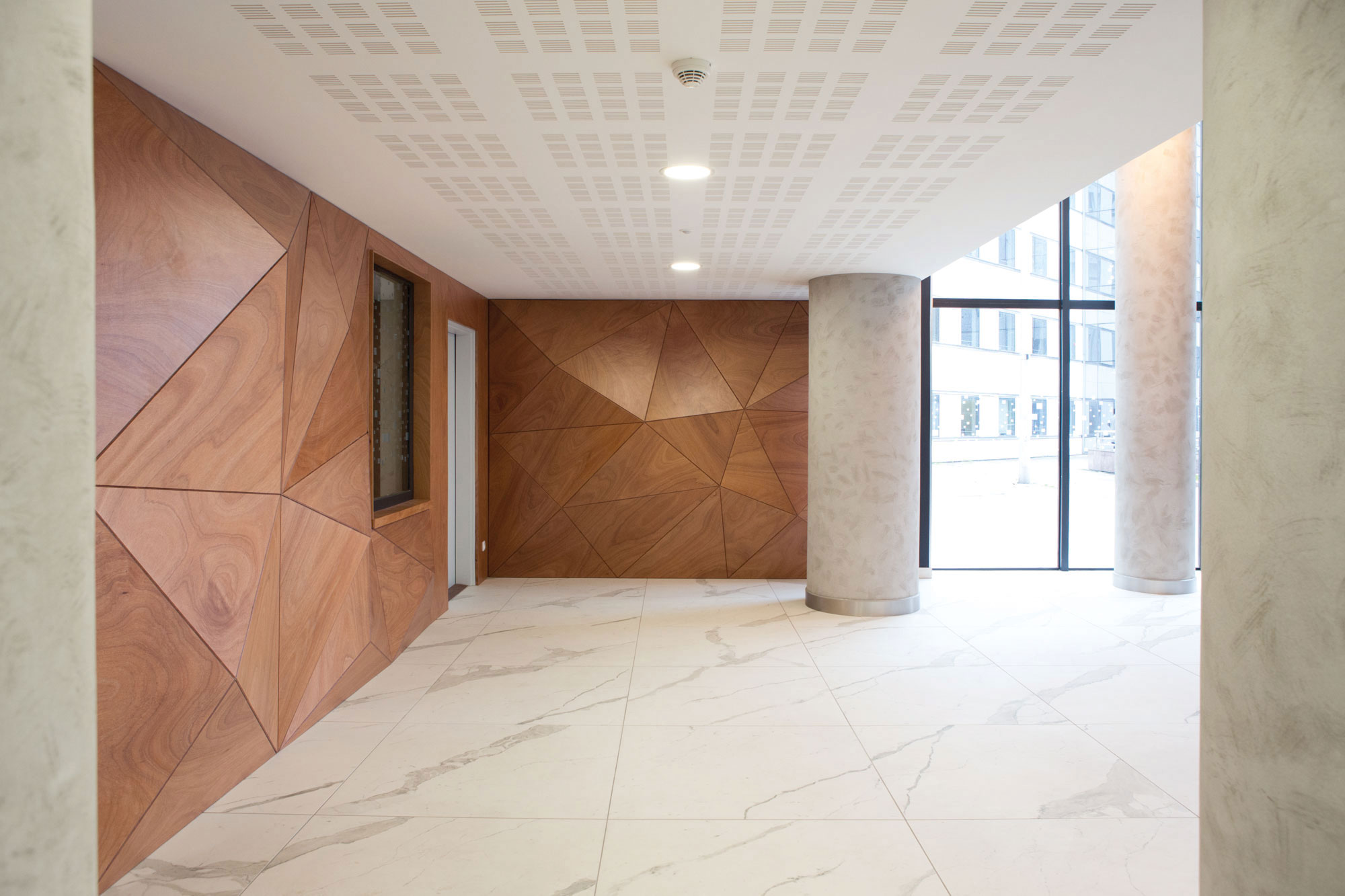
WOOD-SKIN Fold Panels. Photo courtesy of WOOD-SKIN
WOOD-SKIN is an FSC-certified Italian company and uses local materials wherever possible. The earliest iteration of WOOD-SKIN was made with wooden composite, as the name implies, and is still the main material for the company’s projects.
WOOD-SKIN started a collaboration with an Italian firm that supports farmers who want to plant fruit trees, financing their work in the early years when the trees are not yet productive. They already have a small forest of 400 trees that will grow with WOOD-SKIN in the years to come. They’ve also committed to planting one tree for every 10 square meters of WOOD-SKIN produced for each project.