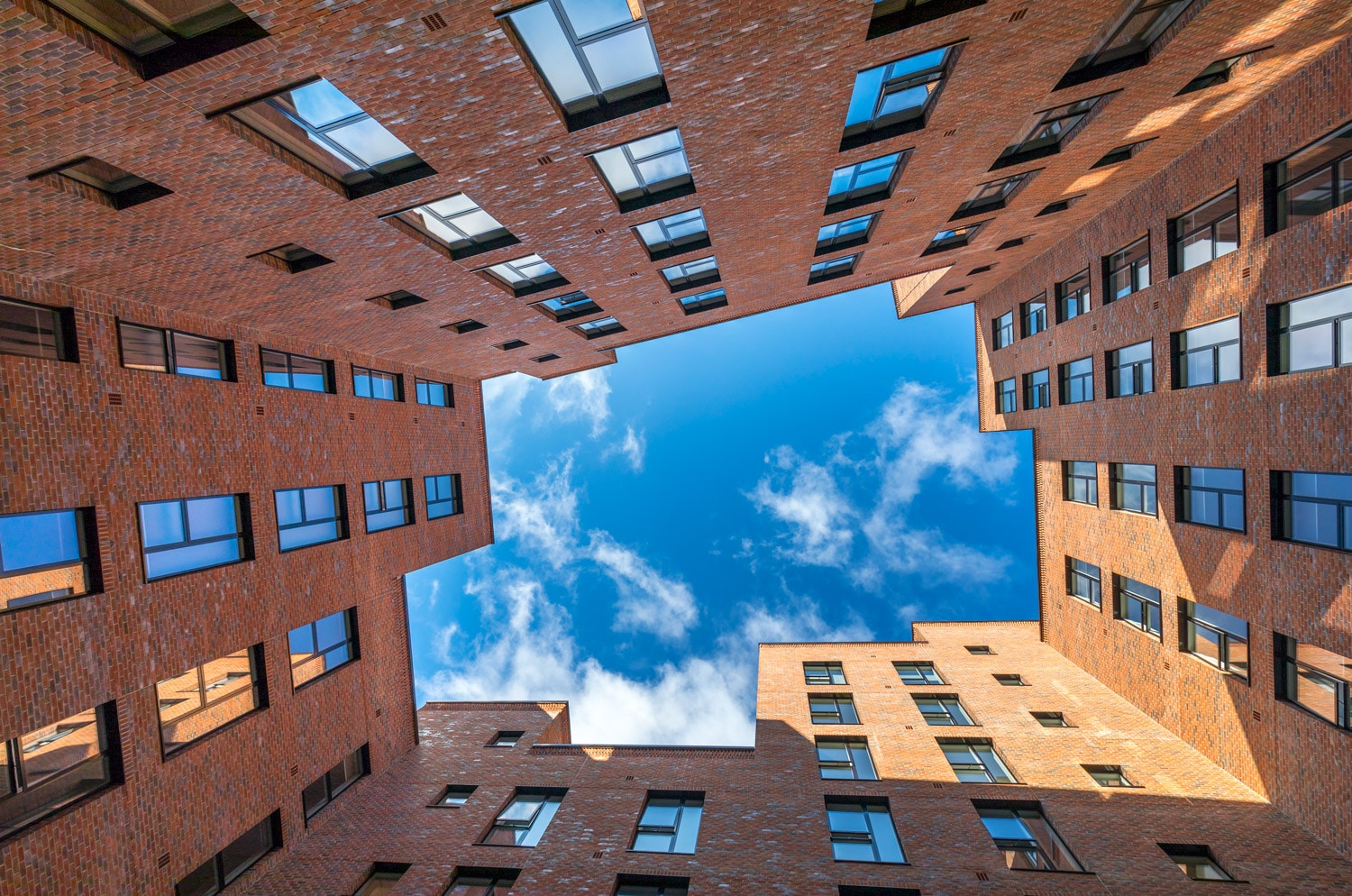
[Photo: Daniel Shearing]
The architects who designed Dalston Works—the world’s largest building constructed out of cross-laminated timber—are in the early stages of what they call a revolution in construction. “It is well understood now that if you live in a building made of healthier materials you are happier, you sleep better,” says Andrew Waugh, partner at Waugh Thistleton Architects and the lead architect on the Dalston Lane project. “We have known this about food for awhile, but we are just starting to understand this with buildings.”
The 10-story, 121-unit residential building was erected on what was once a neglected brownfield site, and it’s built almost entirely of cross-laminated timber (CLT). The use of CLT significantly reduced the carbon footprint of the building in both material production and onsite energy consumption.
Waugh sees it as taking the responsible approach to architecture. “As a practice we look to build in a way that reduces the impact of construction on the environment,” he says. “A building’s carbon footprint is generally measured in terms of its energy use while (occupied), but we are concerned about the footprint of the building materials themselves, which is rarely taken into account.”
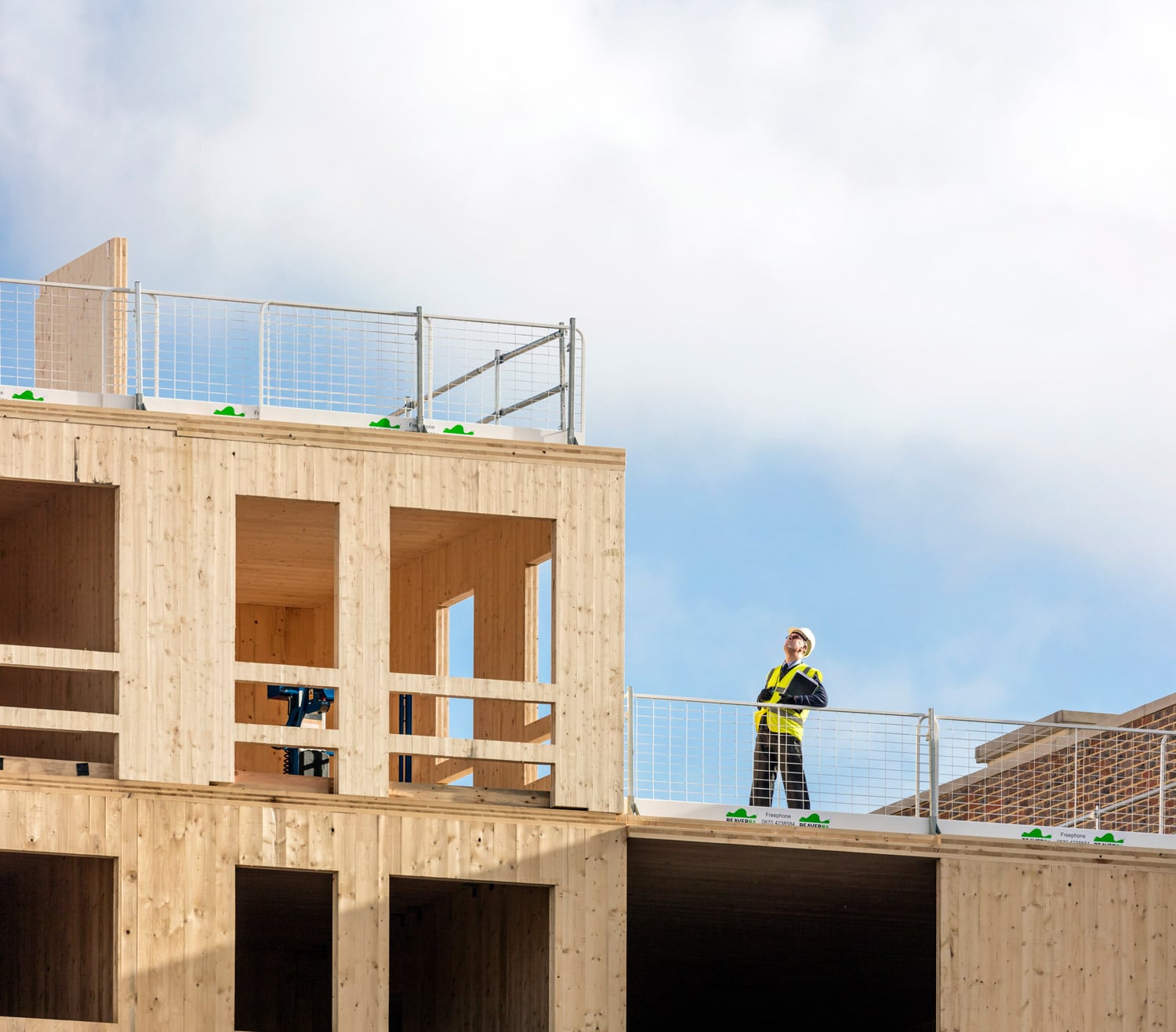
[Photo: Daniel Shearing]
The Human Approach
Construction using CLT—a renewable resource—is faster and cheaper than using traditional building materials. The timber is sourced from sustainably managed forests—when one tree is cut down, five more are planted, Waugh says. Harvested wood products also act as a carbon reservoir—storing carbon for the life of the material. “Architecture is about humanity. It is about far more than choosing the color of the windows. It is about understanding the implications of your actions as an architect,” Waugh says. “The production of concrete and steel are responsible for 18% of the greenhouse gases in the world. It’s about fulfilling your professional role as an architect and refusing to be marginalized.”
CLT is a solid wood panel made from layering boards in alternating directions, bonded together with structural adhesive. The alternating fibers and solid composition of CLT make it a lightweight and strong alternative to other construction materials. Dalston Works weighs approximately one-fifth of a concrete building of the same size. The reduced weight of CLT allowed architects to make the building larger—and complete it faster—to accommodate London’s need for more high-quality, high-density urban housing, according to Damien Cartmell, managing director of construction at Regal London, developer of Dalston Works.
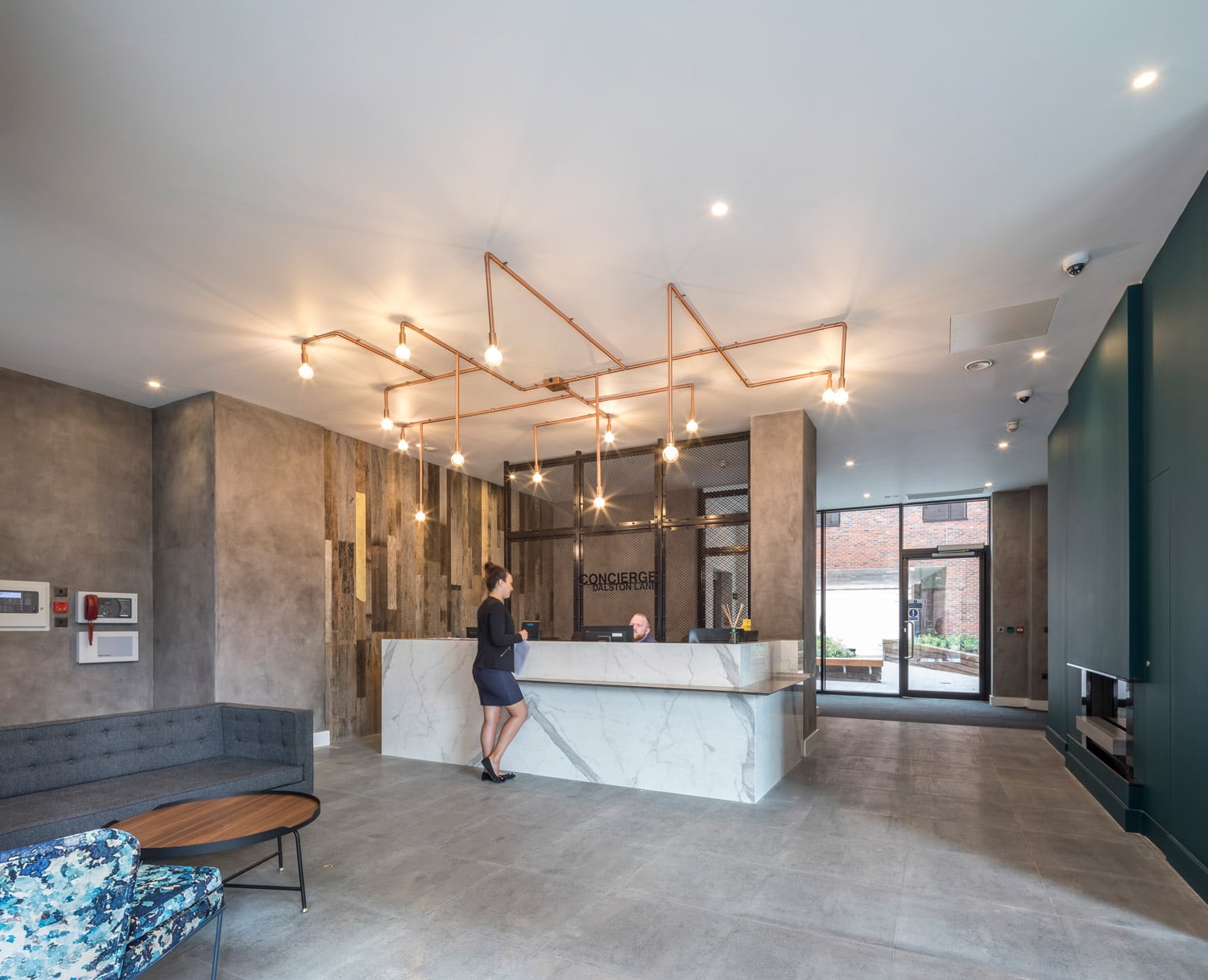
[Photo: Daniel Shearing]
Cleaner Construction
When constructing Dalston Works, all CLT components including floors, walls, stairs, and shafts were prefabricated and then transported to the construction site. Prefabrication meant less noise and dust onsite, creating a healthier work environment for construction workers, who were able to put up a whole floor in a week using a cordless screwdriver. It also meant less waste and onsite deliveries—which were reduced by an estimated 80%. Using CLT allowed the building to be constructed faster than if traditional building materials were used—saving an estimated eight months, Waugh says.
Onlookers would never know the building is made of CLT by looking at it. Cartmell says the entire building is encased to reduce fire risk and meet the requirements for a residential building. The outside of the building—done in clad brick with steel balconies—was designed to fit in with other buildings in the neighborhood. “Brick is very fashionable in London right now,” Cartmell says. “Brick weathers well and adds to the perceived robustness of the building. It is the best of both worlds—timber on the inside with beautiful aesthetics on the outside.”
The building is airtight with a natural ventilation system to help it maintain temperature. It currently operates off a single generator but will later be plugged into a local heat network. Varied roof heights, alternating between five and 10 stories in wave-like structure, are oriented to maximize the daylight received on each of the apartments’ balconies and in communal spaces.
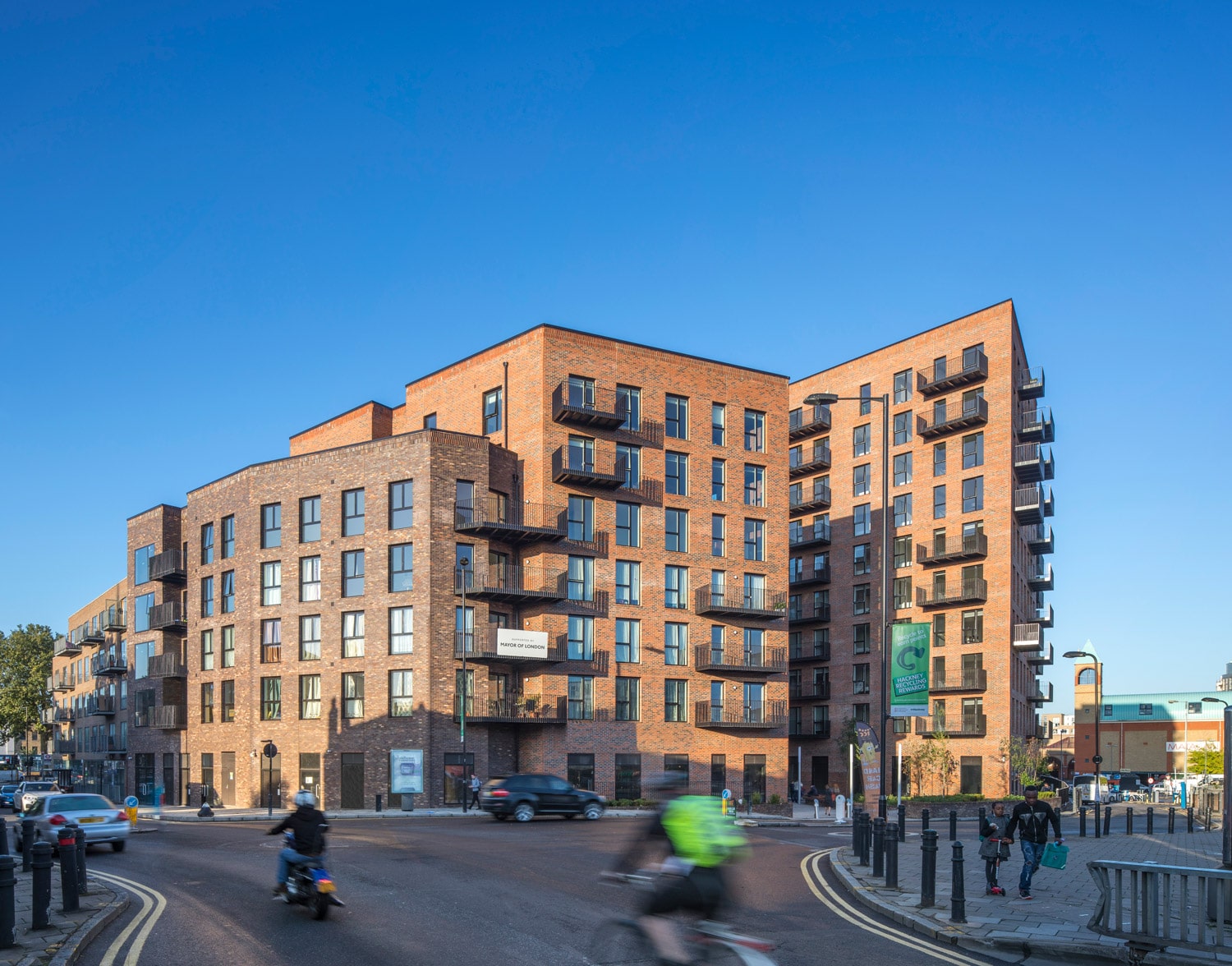
[Photo: Daniel Shearing]
PROJECT
Location
London, UK
Size
14,280 square meters
Cost
Approximately £24 million
Completion
June 2017
AWARDS
Highly Commended for Architects Journal Sustainability Prize 2017; Private Housing Project of the year and Solid Wood Project of the year in Structural Timber 2017; Highly Commended in NLA Housing 2017 and Offsite 2017
TEAM
Architect
Waugh Thistleton Architects
Landscape Architect
Tyrens
Principal Designer
BPM Group
General Contractor
Regal Homes Construction
Structural Engineer
Ramboll and PJCE