Story at a glance:
- Modern exterior product solutions should be designed to adapt to unpredictable weather patterns.
- Inpro’s 650 Series is engineered beyond current codes—to anticipate future requirements, particularly regarding wind resistance.
How do you design and build for the future in a world that’s unpredictable?
Climate change has led to an increased number of severe storms, and building codes are changing rapidly to ensure modern projects stand a better chance to weather the storm. Expansion joints may be niche, but they’re a crucial part of the resiliency conversation when it comes to the building envelope, says Matthew Fisher, senior product design manager at Inpro’s Engineered Metal Division. And he’s not just saying that because he designed the latest in Inpro’s 650 Series. The former architect and construction manager has been a LEED AP since the inception of the sustainable certification program in the early 2000s, and he’s passionate about designing better buildings. “It’s always been a topic I’ve been sensitive to,” he says. “I will always try to lean toward the smarter, more durable solution, ensuring we’re using something that is responsibly resourced.”
Fisher says expansion joints have to withstand daily, seasonal, and seismic movement patterns. “There is driving rain trying to push moisture into every crack, and high temperature differentials from interior to exterior create tough HVAC loads. The covers and their accessories also need to resist hurricane force winds, fires, insects, et cetera—all while being adaptable to the multitude of building veneers that architects design with.”
Beyond Codes
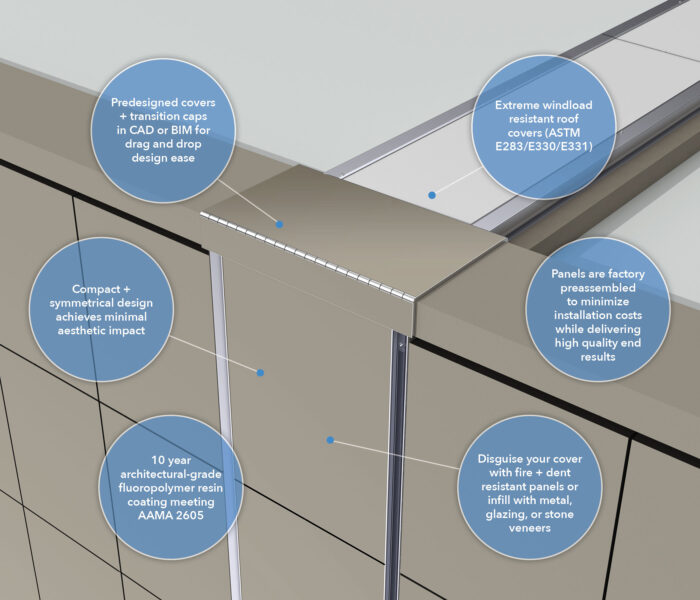
Inpro’s 650 series was tested and developed to anticipate even more stringent codes of the future. Image courtesy of Inpro
Architects are reporting a growing need for wider expansion joints in projects than they used to encounter. Take a New York tremor that occurred in early April 2024, registering at 4.8 magnitude, or indications in Texas of increased joint width requirements on new buildings even though no fault lines exist in that state. Fracking is thought to be creating unusual soil displacement resulting in tremors; the number of encounters has doubled to 201 events in 2021 alone, according to the Bureau of Economic Geology at University of Texas in Austin. And Miami-Dade County in Florida is infamous for encountering hurricane level events so often their ultra-stringent wind resistance code is being adopted in other regions experiencing similar high wind events, including projects in Oregon along the West coast.
“If you don’t plan for proper expansion joints, Mother Nature will install one free of charge, and it will likely not be a nice straight line,” Fisher says. He says expansion joints are a necessary evil that architects and structural engineers must plan for, and that while many architects and designers don’t love them, modern solutions from Inpro will surprise them.
“Architects think expansion joints all leak, and they’re all ugly. That’s not the case,” he says. “I can make it be a chameleon in the background. I can make sure it’s waterproof, that it addresses your thermal needs, and I can even make them acoustically dampening.” He says few people like these functional joints, as they interrupt the aesthetics and complicate the cohesive skins on the project, but Inpro offers solutions to meet these challenges that are also designed to a higher durability than code currently requires.
“Elongating the product’s lifespan while allowing for adaptability to changing conditions is always a goal I strive to achieve when we begin a new endeavor. I first start with a responsible material—in this case aluminum. Then I ensure we have a modular-based design that is easily customizable and adaptable. I then ensure the cover is able to camouflage itself in its environment while balancing safety with durability, all the while not losing sight of the core function of addressing dynamic structural movement,” Fisher says.
Modern Expansion Joints
- Photo courtesy of Inpro
- Photo courtesy of Inpro
While the purpose of expansion joints is to break up the structure into individual sub-structures, the role of the architectural joint covers is to mask that break and give the appearance of a seamless, large building, Fisher says. Projects with the most common application of expansion joint solutions include but are not limited to mass transit (railway and airports), educational campuses, stadiums, civic centers, and mixed use developments employing parking with featured plazas above them.
“The key to a successful expansion joint solution is proper product selection specific to the unique project challenges,” Fisher says. “Coordination with surrounding substrates and waterproofing measures is key, then tight trade sequencing is required through the multiple stages for success.”
Unlike most building products, he says expansion joints reach across nearly every building material—concrete, steel studs, fireproofing, waterproofing, wall, floor, and plaza finishes. “These needs continue all the way up the roof. This presents a unique challenge versus most other products you will specify.”
When expansion joint conditions fail, the threat of water intrusion increases the opportunity for mold to grow, Fisher says. “If that occurs, accessing these often tough conditions is the first problem, followed by removal and disposal of many finishes, degradation of the structural integrity, and downtime for operations in those affected finished spaces,” he says. “If thermal considerations are not implemented on joints, air drafts, loss of heating and cooling efficiency, and potential reduction of the life safety accessories behind the covers can also result.”
What is the 650 Series?
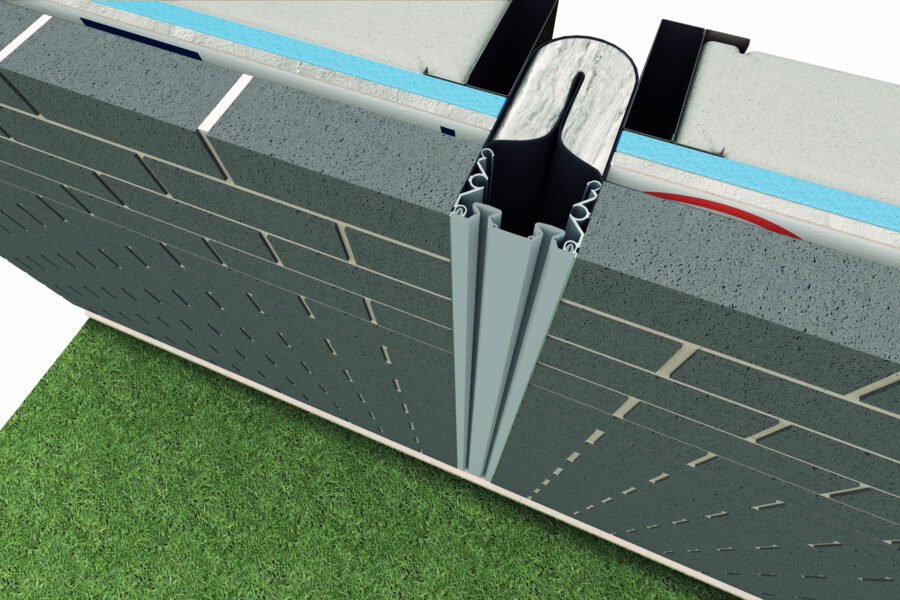
The dynamic movement insulated moisture barrier is mounted behind any expansion cover within the throat of the joint to address moisture and interior R-values. Rendering courtesy of Inpro
The 650 Series is a complete building envelope solution in one product, and it’s the first of its kind in the industry, Fisher says. Unlike competitors’ roof and wall systems, 650 was designed to work together—from roof to wall. It’s designed to handle complex transitions seamlessly. “I’ve designed the first cohesive system that addresses the wall, the roof, and every change in direction with the same system,” Fisher says, adding that those transition points are critical, as that’s where 90% of leaks are found. “You start letting in water or letting out heat or cold, and that’s not a good sustainable life cycle for that building to undergo.”
The 650 allows for full 100% three-dimensional movement along with full lateral shear capabilities. Inpro’s panels are factory preassembled to minimize onsite installation labor costs. The installation for the walls is similar to and as simple as hanging a prefinished door on its hinges within your home, Fisher says. The roof system locks down tight but can open and close like the hood of a car, allowing for ease of annual inspections of the waterproofing membrane under it.
The systems’ modular design allows for project-specific customization without the cost and complexity typically associated with this approach. Inpro engineering teams also designed and tested every component to endure hurricane level winds, particularly on the roof’s leading edge, where the most uplift forces culminate. “These are designed to survive a seismic event. Most earthquakes last about 45 seconds. Buildings are moving and swaying violently in that time. This system is designed to survive all of that swaying without getting damaged, so the expansion joints can be reused.”
Details Matter
Small things are important, especially to the overall sustainability of a project, says Brian Crilly, a senior associate and designer at Stantec.
“When you get down to the heart of the matter, a different architect or designer might give you a little bit of a different answer, but from the standpoint of Stantec, we’re absolutely committed to the environment and also preserving what we’re creating,” he says. “Our lives are changing because of what we’ve done to the climate, and we’ve got to do something about it.”
Stantec is very much concerned with building projects that last with durable materials, and in the instances where a building is being torn down, looking at how that can be done more sustainably, too. Material choice, he says, is of utmost importance. Architects can design a beautiful, flexible space a client loves, but that client may not always be there. Hopefully the next client loves the space, too, but that’s not always the case, Crilly says. The next tenant may make significant changes to the building, and some buildings are even torn down.
“Let’s not use materials that when thrown away are harmful toward the environment,” he says. “It’s about identifying materials or promoting ideas where there is a longer life to what we’re doing. And if there’s not, making sure that if something is removed, that it’s not harming us when it’s thrown away or recycled. It gets down to the basic tenets of resiliency really.”