Story at a glance:
- Cellulose acetate (CA) is a bio-based polymer used in a wide array of products.
- Modern green chemical techniques to form CA heighten its appeal as a sustainable building material.
- Research suggests that a hemp/CA biocomposite could serve as a building material substitute for wood.
Cellulose acetate (CA), also called simply acetate, is a semi-synthetic polymer composed of chemically treated cellulose mainly sourced from wood pulp or cotton. CA is also technically a thermoplastic because it melts and can be molded when heated, then solidifies upon cooling, like its fossil fuel-derived thermoplastic counterparts. CA may also be spun into textile fibers or cast into hardened sheets.
How is cellulose acetate made?
Traditionally harsh chemicals are needed to purify cellulose from its source, followed by other strong chemicals that modify the cellulosic structure to form CA. This method is still commonly used today to make CA. However, modern green chemistry, relying on eco-friendly chemicals, has the potential to make CA an even more sustainable material, though this methodology is still mostly in the R&D stage. Thus far, it has been demonstrated in the lab using corn cobs and sugarcane bagasse as the cellulose source.
After CA is formed in the lab, plasticizers (mainly phthalates) are commonly added to CA to make it more flexible. Phthalates are associated with several environmental and human health harms. In fact, several phthalates are banned from use in certain products because of the hazards they present.
Does cellulose acetate biodegrade?
Research shows that CA degrades more rapidly and more completely under certain conditions than other bioplastics, making it more environmentally friendly compared to many other materials. The process could take a year or more. Other investigators note that adding titanium dioxide to CA accelerates its decomposition.
CA in cigarette butts is a major ocean pollutant, degrading into ubiquitous microplastics found in the Arctic, on mountaintops, and in plants and animals, including humans. Preliminary reports indicate microplastics are associated with multiple adverse health outcomes.
What is cellulose acetate used for?
Cellulose acetate is used to make many diverse products including:
● Gown linings
● Award ribbons
● Draperies and curtains
● Home furnishings
● Diapers
● Jewelry
● Eyeglasses
● Cutlery handles
● Photographic film
● Reverse osmosis water filters
● Dialysis machine membranes
● Cigarette filters
Cellulose Acetate in Design
Research testing a hemp/cellulose acetate composite indicates CA has the potential to become a major player in sustainable design. The investigators showed that the mechanical testing of a hemp/CA biocomposites demonstrated that it has strength properties comparable to structural lumber and higher than plywood. So, it could be a substitute within buildings for framing, flooring, or decorative paneling or in construction as formwork or scaffolding. In fact, biocomposites have the potential to replace plywood within formwork, in this case for a slab form.
Additionally, the researchers suggested that in formwork, a hydrophobic biopolymer coating on the biocomposite would increase the form’s ability to be reused but would not
compromise its ability to biodegrade.
The Oakland, California–based manufacturer Model No. used CA in some of its interior furnishings made with plant-based, regenerative, and recyclable materials. “Everything we do, all of the materials we print with, are all a kind of bioresin. We don’t use any petroleum-based products. What we’re really excited about, though, is we’re transitioning to cellulose acetate, a material that’s 93 to 94% biodegradable because it’s made from wood pulp and cotton,” says Phillip Raub, CEO of Model No., in a previous article for gb&d.
Benefits of Cellulose Acetate
Since CA is derived from common sources, it is inexpensive. Other benefits of cellulose acetate vary depending on the product. In eyewear, for example, CA is stiff but flexible, characteristics which appeal to users. As a fabric, CA is hypoallergenic, dries quickly, and does not cling.
Since CA is not derived from fossil fuels, it is more biodegradable than plastic, which is derived from those nonrenewable sources and is largely indestructible.
Other New Sustainable Materials
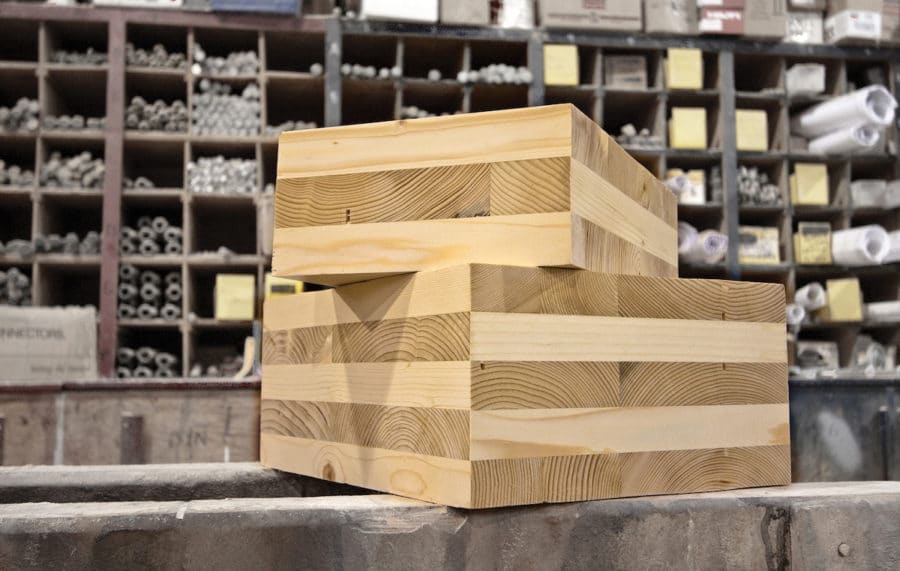
Cross laminated timber is a strong, lightweight, and sustainable building material. Photo courtesy of Oregon Forest Resources Institute
Besides cellulose acetate, there are other new sustainable building materials available to designers and builders. A few of them are wood-based like CA often is.
Timbercrete is made of sawdust and wood chips combined with cement, water, and binding agents to form a building material that has insulating ability. It’s not as strong as concrete but will work in exterior walls and roofing.
Cross-laminated timber (CLT), composed of wooden planks glued together, arrives premade at construction sites. Because it is stronger than traditional wood, it can serve as a substitute for concrete for some applications.
“With normal construction you have tons of waste. It’s a much cleaner way of making houses. It uses less space because as the wood arrives at the building you mount it immediately. You don’t have to store the materials. You can reduce the number of trucks going out and coming in [and their] carbon emissions,” Paulo Martins, principal of Paulo Martins Arquitectura & Design—the firm that designed one of Portugal’s first mass timber homes—previously told gb&d.
Another sustainable building material that is also prefabricated is structural insulated panels (SIPs). They may be used to create walls, floors, roofs, and even foundation systems.
SIPs consist of an insulated core sandwiched between two sheathing panels. As a result, they improve energy efficiency by 50% or more compared to conventional timber-framed buildings. “Because SIPs are more airtight than your typical structure, you don’t have a lot of air passing in and out of your house,” Damien Pataluna, owner of FischerSIPS, previously told gb&d.