Today’s architects, contractors, and building owners have their sights set on the same goal: to get the highest thermal performance out of a building envelope. Although advanced glass infill solutions such as low-e glass or argon-filled have traditionally been viewed as the easiest way to improve performance, upgrading a building’s framing system with aluminum frames can be the most cost-effective option for exercising environmental intelligence, improving a building’s thermal performance, and gaining LEED Gold or Platinum certification.
Advancements in Aluminum Framing Systems
In the past, aluminum framing systems were known for their high thermal conductivity, or vulnerability to heat gain and loss. As a result, as architects sought to meet or exceed code requirements, they defaulted to advanced glazing infill solutions to make the difference.
But in recent years, innovations in framing have driven thermal performance to new heights, helping to meet and exceed evolving energy codes, and solidify its primary position in a building’s energy-efficient design.
Here are three areas in particular where aluminum frames have evolved.
1. Thermal performance
A framing system’s thermal performance is less effective when the aluminum that sits inside the conditioned space connects with the outside unconditioned material. In cold climates the aluminum acts like an ice cube in your building, which requires more energy to control interior temperature. This makes the type of framing system, and the performance of that system, critical when considering the energy performance of a building.
Thermal breaks in aluminum framing systems were first introduced to help solve the issue of high thermal conductivity nearly 35 years ago as part of the response to the energy crisis in the 1970s. Today thermal break technology has become more advanced. Aluminum framing manufacturers often use one of two methods: pour and debridge or polyamide struts.
A pour and debridge process creates thermal breaks and improves energy performance by filling a channel in the aluminum extrusion with a polyurethane material and then removing, or debridging, the bottom of the channel. The outside of the aluminum frame is thermally isolated from the inside of the aluminum within the glazing system. This process delivers strong energy savings economically.
Many manufacturers have come up with more innovative pour and debridge processes, for example YKK AP’s ThermaBond Plus, which improves the adhesion of the polyurethane material to the aluminum extrusion in the pour and debridge method. Another example is YKK AP’s MegaTherm, which uses 6/6 nylon polyamide glass fiber reinforced isobars to join two separate extrusions into one thermally broken mullion. These methods save energy and reduce condensation, delivering proven performance over the life of the building.
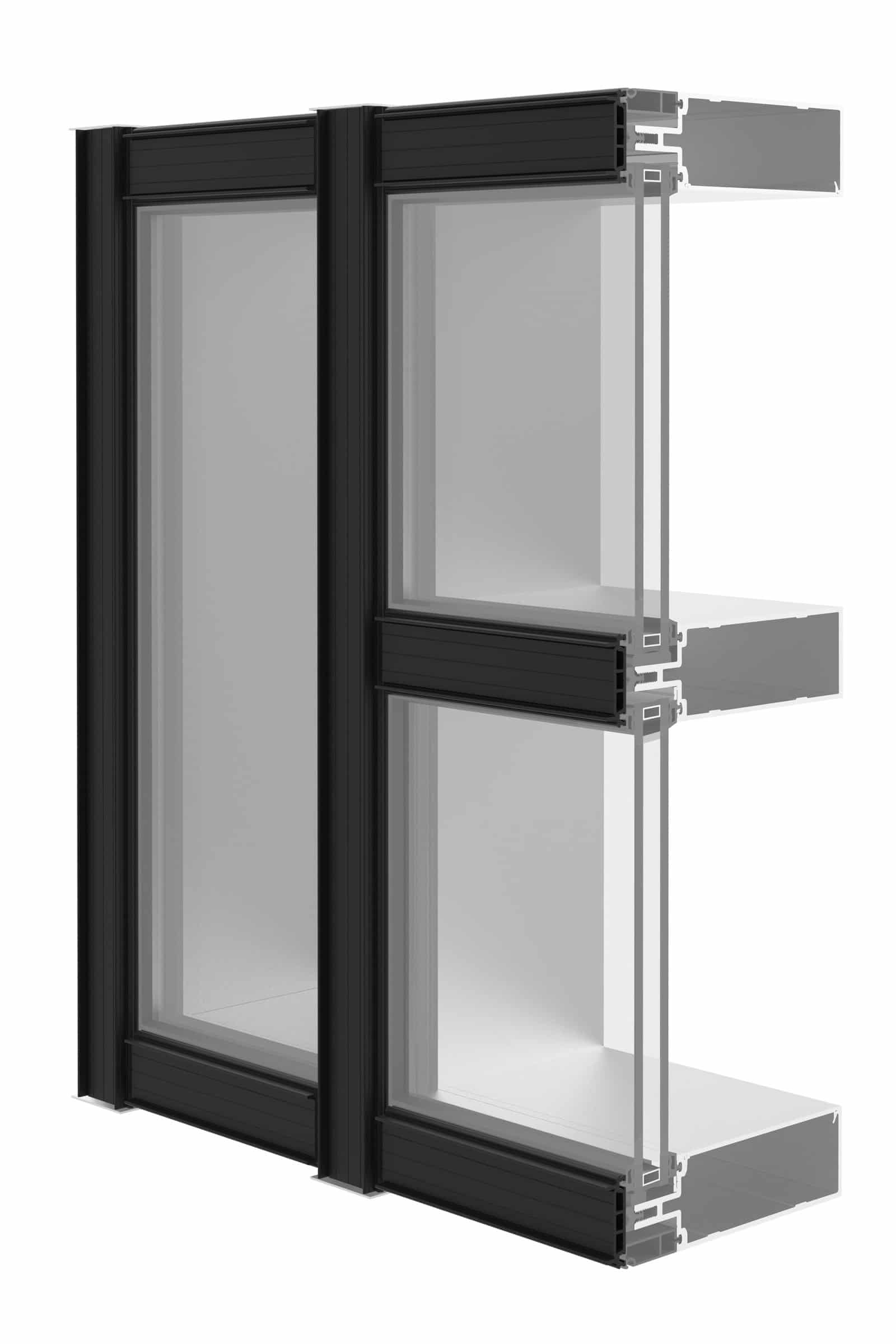
A polyamide pressure plate framework, which replaces the traditional aluminum plate. Photo courtesy of YKK AP
Additionally, new uses of material have been discovered, particularly in curtain walls, by using polyamide to replace the traditional aluminum pressure plate. A polyamide composition, for example, has significantly lower thermal transmission values than aluminum, providing structural and thermal performance that yields performance increases of up to 20% reduction in U-factor.
Fiberglass is also used in thermal breaks but the industry has migrated away from it because fiberglass is harder on tools and requires significant personal protection equipment to ensure proper industrial hygiene.
2. Condensation resistance
Condensation resistance is critical to the thermal performance of a building. The Fenestration and Glazing Industry Alliance (FGIA) developed the condensation resistance factor (CRF) as a method of rating the ratio of the surface to ambient temperature difference. Thermal enhancement technologies in aluminum framing systems significantly reduce heat loss during cold weather yielding warmer interior surface temperatures on the frames, which helps to mitigate condensation and thereby increasing a building’s thermal performance.
FGIA created the CRF Tool to help calculate the CRF based on specific environmental conditions. Thermal modeling technologies like the NFRC Component Modeling Approach (CMA) Software Tool, can assist in identifying specific framing attributes to take into account where condensation is a concern and also helps a framing selector compare one product to another. AAMA 515-9-19 was published by FGIA to supplement AAMA 501-19. AAMA 501-19 specifically addresses the interior surface temperatures of commercial fenestration systems. The AAMA 515-9-19 standard can be used to evaluate condensation of exterior wall systems using surface temperature. It provides a surface temperature measurement procedure that can be used to evaluate wall mockups for possible condensation as specified in contract documents.
3. Sun control
Aluminum sunshades integrate seamlessly with a building’s framing system. They have become a preferred method for improving a building’s energy efficiency by reducing the solar heat gain coefficient (SHGC). Sunshades offer design versatility, and can be customized depending on which way a building faces to reduce the amount of harmful light, while bringing visible light in to achieve optimal daylighting and improve occupant comfort.
When attaching sunshades to curtain walls it is critical to ensure the anchoring system is thermally broken. By doing so, SHGC is reduced and a building’s U-factor is improved by 5% more than a traditional non-thermal anchoring system.
Prescriptive vs. Performance Building Codes
There is more than one path to achieving energy code compliance. The most common route is to meet the prescriptive code, or the minimum acceptable standard for each element of the building. This method is straightforward; it simply involves following the proper local building codes.
The second strategy to achieve energy code compliance requires modeling the building to predict energy usage. An acceptable standard is established in this scenario and a virtual model is typically leveraged to gain a sense of how the building would perform under certain conditions.
Both prescriptive and performance pathways will enable architects to achieve energy code compliance. The virtual modeling used in conjunction with the performance strategy provides enhanced visibility into the whole building envelope, making it easier to identify and make trade-offs between various components of the building envelope.
Beyond the Framing: Identifying Trade-Offs
When designing a building to meet or exceed energy codes, it is important to examine the whole building envelope. If certain elements perform extremely well, architects and contractors may have more leniency on other building elements.
Traditionally advanced glazing infill solutions like double low-E coating, high-performing spacers, and argon-filled glass, are looked to first when seeking to improve a building’s performance. However, these high-performance solutions can greatly increase overall project costs. When examining the whole building envelope, it is crucial to look at whether standard framing with an advanced glazing solution like an argon-filled glass meets the needs of the project, or whether a high-performance, thermally broken framing system that allows for standard glass may fit the bill.
Additionally, a highly insulated roofing material may allow for a lower performing window system. This optimizes the various building components, equipment and assemblies, saving money, time and operating expenses.
Mechanical trade-offs like the HVAC system are also important to keep in mind. Because advanced framing systems work to improve the thermal performance and energy efficiency of the building, the initial tonnage of the HVAC may also be reduced, maximizing upfront cost-savings. The cycling time of the HVAC is also reduced considerably. This translates to less use of the HVAC and, ultimately, longer longevity and considerable energy cost savings.
Tools to Improve a Building’s Thermal Performance
Many innovative tools and services exist today to more easily calculate a building’s thermal performance. These fall into the category of building envelope modeling (BEM). Not to be confused with building information modeling (BIM) software applications like AutoDesk Revit and IES Virtual Environment that enable architects to create a model of the entire building to allow for design, plans, and specs, as well as project management and scheduling. In many cases the BIM models contain metadata related to each building component’s performance. BIM models are often the input used in BEM software based on the initial design. The model may identify areas that diminish performance or elements that can be value engineered to optimize building performance. The energy.gov website offers a very useful rundown of the processes as well as software options available today.
Building envelope consultants work specifically toward helping architects and building owners achieve their thermal performance goals. They can be especially helpful in using whole building energy modeling to identify the right product mix as well as professional guidance to establish the proper trade-offs to achieve the highest thermal performance possible, saving energy costs, and time.
Additionally, customized engineering services provided by manufacturers should not be overlooked. The in-depth support provided can be instrumental in pulling the various levers of glazing, framing, roofing, mechanical, and more to meet or exceed the requirements for a project, while balancing the overall project costs.
To easily calculate the thermal performance of various glass packages, apps also exist. myThermalAssistant, for example, uses YKK AP-specific products to provide framing and glass recommendations based on your desired energy performance.
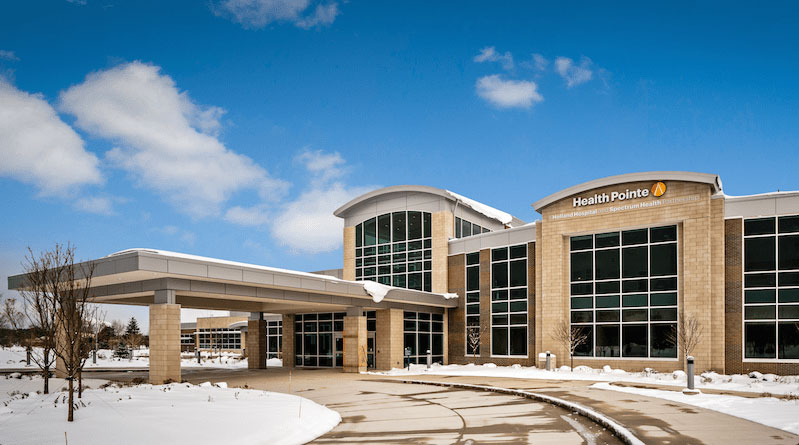
The AECOM team chose YKK AP products to stand up to the cold. Photo courtesy of YKK AP
Case in Point: Health Pointe
The importance of a thermally-broken framing system to a building’s performance is illustrated in Spectrum Health’s integrated clinical facility, Health Pointe in Grand Haven, Michigan, where the architectural team at AECOM was challenged with designing a facility that would stand up to the extreme cold. In addition to maintaining warmth, the team wanted to integrate natural sunlight into the design, as it’s been scientifically proven that access to natural light enhances positive health outcomes in patients.
To achieve these goals, the team chose a thermally broken curtain wall system, integrated with a sunshade with a thermally broken anchor. Initially the biggest challenge was the curtain wall around the perimeter of the building due to the CRF requirements. The combination of the curtain wall and sunshades with thermally broken wall anchors addressed this issue by offering the best CRF and U-value.
The health care facility now provides ample sunlight, comfort, and warmth to its patients as they undergo treatment.
Framing the Future
It is because of these developments that many framing manufacturers now offer advanced framing with extra thermal performance in storefront and curtain wall applications that achieve U-factors under 0.39 Btu/hr.ft2.oF (W/m2.oC) to meet and exceed codes and to save energy, without the need for advanced glazing.
With more municipalities adopting robust thermal codes like IECC 2018, an increased drive to improve employee comfort and reduce energy costs, it is critical that all the people in the value chain work together to meet demand for higher performing buildings. It is no longer a focus on “green” building certifications or saving “green”—it has become part of the fabric of construction. By taking a closer look at the framing system and the glass, and how these two crucial elements of a building work together, architects and contractors can better understand the performance impact of each element.