Story at a glance:
- Consider these seven tactics to help prevent leaks in the envelope.
- Cross-team collaboration is essential to improving building envelope connectivity.
- Air, vapor, water, and thermal should all be factored in for the highest performing structure.
Even with the most forward-thinking design decisions, a building is only as good, safe, and secure as its structure and exterior shell. When issues like air and water infiltration arise, the color palette of a space, the beautifully sourced furniture, all of the modern amenities—none of it matters.
The challenge is that you can’t always see leaks in the building envelope after the cladding and finishes have been installed. And by the time you do, the damage is already done.
Although finding the initial source of the problem can be difficult, it usually ties back to lack of water management. “Anything that’s in the built environment needs to have the appropriate shedding capability,” says Marcy Tyler, director of building science at Tremco CPG. “Having a structure that has all the appropriate connections is super important. And that’s what we miss in a lot of instances, or it’s done incorrectly, or it’s done with materials that can’t handle the movement that’s needed to be able to perform long-term.”
How Can Architects Design to Prevent Leaks?
So, what can architects and designers do to specify the right building materials and prevent leaks from day one?
The answer is complex because every product, application, building, and location are different and do not exist in isolation from each other and the environment.
“When it comes down to it, it is a holistic approach that improves building connections,” Tyler says. By focusing your time on only one area, you might neglect key factors that influence the performance of your building, which could lead to incomplete architectural details or assemblies with vague installation processes. To alleviate this risk, Tyler offers seven actions to take on each project to strengthen its building envelope connectivity.
1. Communicate. Like any good relationship, Tyler says the foundation of a good build—both literally and figuratively—is communication. Communication is essential at the preconstruction meeting, preinstallation meeting, and at any point during the project where there are any concerns, questions, or ambiguity.
In fact, when Tyler asks construction and design teams about their triumphs in the field and how they overcame challenges to get the job done, “the biggest thing that they always say is communication,” she says.
“It can be as simple as: We’re going to waterproof the structure. What are we going to do when we meet grade? How are we going to make that connection? We need to make sure we have the right material, the right drainage, right protection, right amount of insulation, and so on. But then we need to say, well then how do we connect it to that air barrier? And then how do we connect that air barrier to everything that is going to connect to it, like windows, doors, and eventually the roof?”
When you get all the disciplines in a room as early as possible and work out these transitions, that’s where leak-free building success is born.
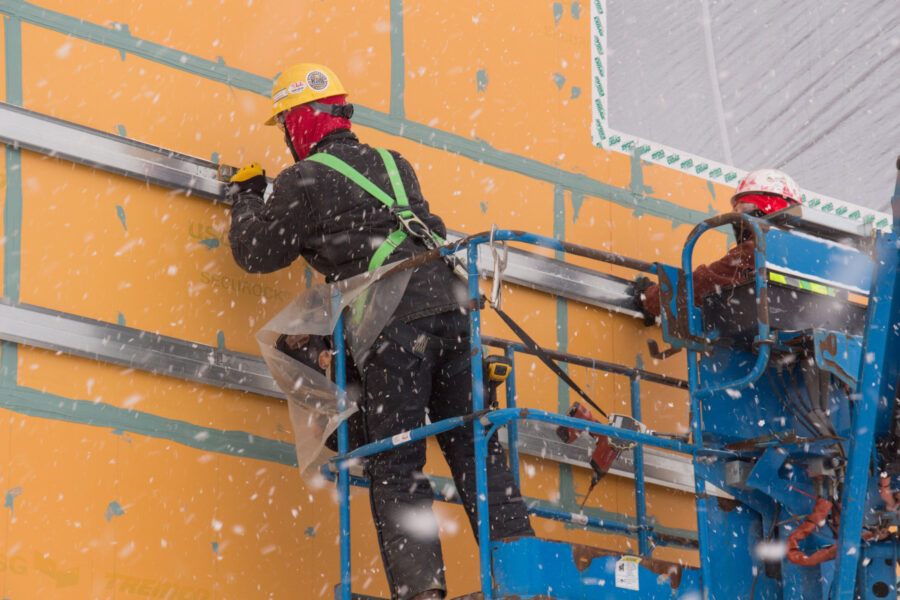
Photo courtesy of Tremco CPG
2. Take a systems approach. A building is a sum of its parts. Each element has a chemical composition and performance characteristics that will impact other materials. Add in environmental factors like UV, precipitation, humidity, wind, and movement, and there are numerous variables that need to be considered at every connection point to prevent air and water leaks.
“Sometimes we take our buildings and we’re like, ‘Oh, this building works here. Let’s just build it everywhere.’ There needs to be that time and understanding to know the purpose of the building, intent of use, as well as where it’s being built,” Tyler says.
To put it into perspective, she challenges the industry to think of buildings as if they were purchasing a car. “If I’m going to be hauling material, I need a certain type of car. If I’m going to be driving in bad weather, I need a certain type of tire. You’re not going to buy a convertible if you live in an area that has potential for not very sunny days.” Taking each building system in the context of its individual environment will save designers and contractors headaches in the long run.
3. Ensure durability. Long-term performance of every building material and interconnected system can impact the structural integrity of the building. It is important to consider everyday stresses as well as extreme forces from potential natural disasters like earthquakes, tornadoes, or hurricanes.
How will each individual product hold up to the expected movement, impact, and environmental conditions? Then, consider what degree of durability the building will achieve when all of these elements come together.
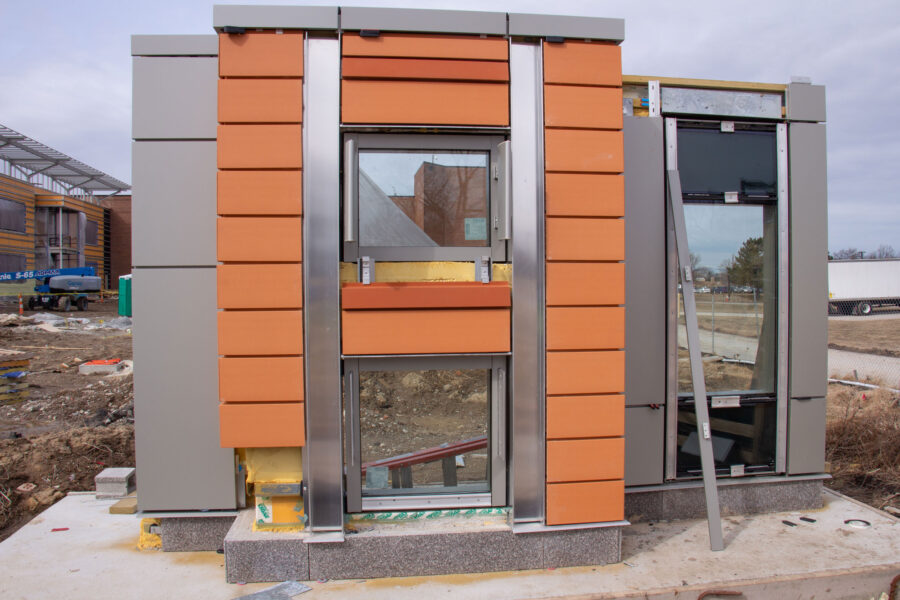
Photo courtesy of Tremco CPG
4. Factor in air, vapor, water, and thermal. The four control layers of a building envelope should all be equally considered in the design and application of materials. If air can get into the wall assembly, then moisture can, too. This could lead to condensation, liquid water trapped behind the exterior cladding, and ultimately mold.
When evaluating different air, vapor, and water barrier technologies, also factor in the necessary permeance rates and drainage. Heat transfer through the wall also impacts the envelope and its energy efficiency, so designers should strive to minimize thermal breaks that put added strain on the building’s HVAC systems.
5. Consider compatibility and adhesion. It may sound elementary, but you need to think about how each product will perform. Is it going to adhere to the substrate or materials beneath it? How is it affected by temperature and moisture during installation and throughout the life of the building? How does proper application play into its ongoing effectiveness?
Just because two materials stick together does not mean they are necessarily compatible. So, as you are specifying products, review how each may be affected by the chemistries of the adjacent materials. And if you aren’t sure, test it. Choose material manufacturers who will do that for you. Better yet, consider a single-source wall assembly where all components have already been thoroughly system tested and performance validated.
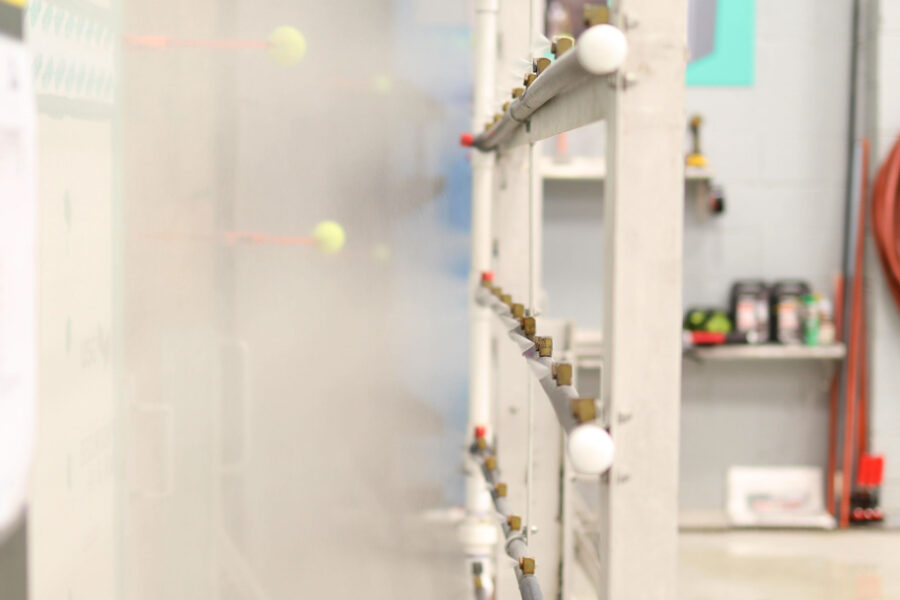
Photo courtesy of Tremco CPG
6. Conduct air and water testing. Prior to breaking ground, you should always review existing test data and consider specifying additional tests of building details that are vulnerable to air and moisture infiltration, such as the window-to-wall condition.
Through the testing mock-up process, the entire project team can evaluate system performance, investigate the cause of any failures, and work together to determine solutions before large-scale construction.
However, testing should not be conducted in a vacuum. “Sometimes people like to hold themselves accountable to certain performance criteria. Maybe they had an issue with that specific performance criteria in the past, so that’s why it’s important to them,” Tyler says. But that one test result doesn’t paint the full picture. Testing of individual products does not factor in their compatibility with other building materials. Therefore, assembly tests are critical, and their results and prescribed changes in design or application should be communicated to all the project stakeholders.
7. Define project sequencing. A common source of confusion on a job comes during the overlap between different trades. The order of building material installation, especially across subcontractors, should be clearly outlined. The various trades need to be aware of what products will be applied before and after they arrive onsite, as it could impact their scope of work. For example, installers should know the proper cure time of a deck coating before stepping across it or ensure they detail any penetrations to a preexisting air barrier.
Leak-free wall systems may sound easy to achieve, but countless variables play into their effectiveness.
“As an industry I don’t think we’ve gotten to the point yet where we truly understand the impact of each of the building materials we choose. It’s not until the facade has to be removed or we have to dig around the base of a building to investigate a leak that we grasp the gravity of the situation,” Tyler says.
Even a small, isolated area can cause widespread damage with negative structural, safety, and financial consequences. But by proactively reviewing the connectivity of building materials and their effect on each other, we can reduce building envelope failures to create longer-lasting and energy-efficient structures.