Story at a glance:
- Liquid-applied waterproofing is typically preferred in construction.
- Builders often wonder when to use cold vs hot applied liquid waterproofing, as each has benefits.
- Cold, liquid-applied waterproofing can be applied to a broader area in less time than hot rubberized asphalt (HRA).
Commercial construction projects come in all sizes and can include anywhere from a dozen to hundreds of scenarios. For starters, the project may be in a large city downtown or in a less congested suburban area, and it may involve construction of a new building or the renovation of an existing one. Many areas of a newly constructed or renovated building will require waterproofing, particularly green roofs, balconies, terraces, covered podiums, and plaza decks. But when should you consider cold vs hot-applied liquid waterproofing?
Depending on the project, commercial builders, designers, and architects will find that there are numerous types of waterproofing products out there that may work for their project. Liquid-applied waterproofing is typically preferred, but choosing cold vs hot-applied liquid waterproofing is a common question, as each has benefits for certain scenarios.
There is a wide range of construction scenarios in which using a cold-applied liquid waterproofing product is the more practical choice. Several factors affect waterproofing product selection—including safety, construction environment, required performance, project size, and application speed.
To answer when to use cold vs hot-applied liquid waterproofing, we example several scenarios in which cold-applied liquid waterproofing works best.
When there are safety concerns
- Photo courtesy of GCP
- Photo courtesy of GCP
Hot liquid waterproofing like hot rubberized asphalt (HRA) requires the use of double-jacketed kettle, or melter, for warming the asphalt, which must reach and maintain 360 to 400°F prior to and during application.
Since both open flame and heat are produced and there is a high capacity for combustion, many local building codes have restrictions on the use of HRA or don’t allow the kettles to be brought onsite.
Also, local fire marshals may require special permits to be pulled for this type of work. In urban areas like New York City, you’ll often encounter limitations on the building height at which the kettles may be used.
In addition to the safety of the surroundings, the safety of the waterproofing applicators must be considered because they are dealing with materials that are molten and nearly 400°F. Using a cold-applied liquid is the logical option where using hot liquid is either not allowed or deemed unsafe based on local regulations and/or the surroundings.
When odor may be an issue
A frequent concern with HRA is the strong odor that results from melting the product which can permeate the surroundings. If the renovation or construction project is being conducted near occupied buildings, particularly a hospital project or office, the odor can pose a problem and lead to complaints from the building inhabitants. Since many cold-applied liquid waterproofing systems have very low odor, they can be beneficial in projects in heavily populated areas.
When performance and durability is critical
Depending on the construction project’s job sequencing, subsequent trades, equipment, or foot traffic may be moving on and around the waterproofed area. In that scenario, there’s a tremendous opportunity for the waterproofing membrane to get damaged, especially if it isn’t fully cured.
Fast curing, cold-applied liquid waterproofing is a more robust material under these conditions. Its higher shore hardness and puncture resistance allows it to stand up exceedingly well to heavy traffic and limit trade damage—a factor that elevates it over HRA options when durability is absolutely essential. Even with a protection board, HRA’s resistance may not be sufficient.
When the project size or application area is large
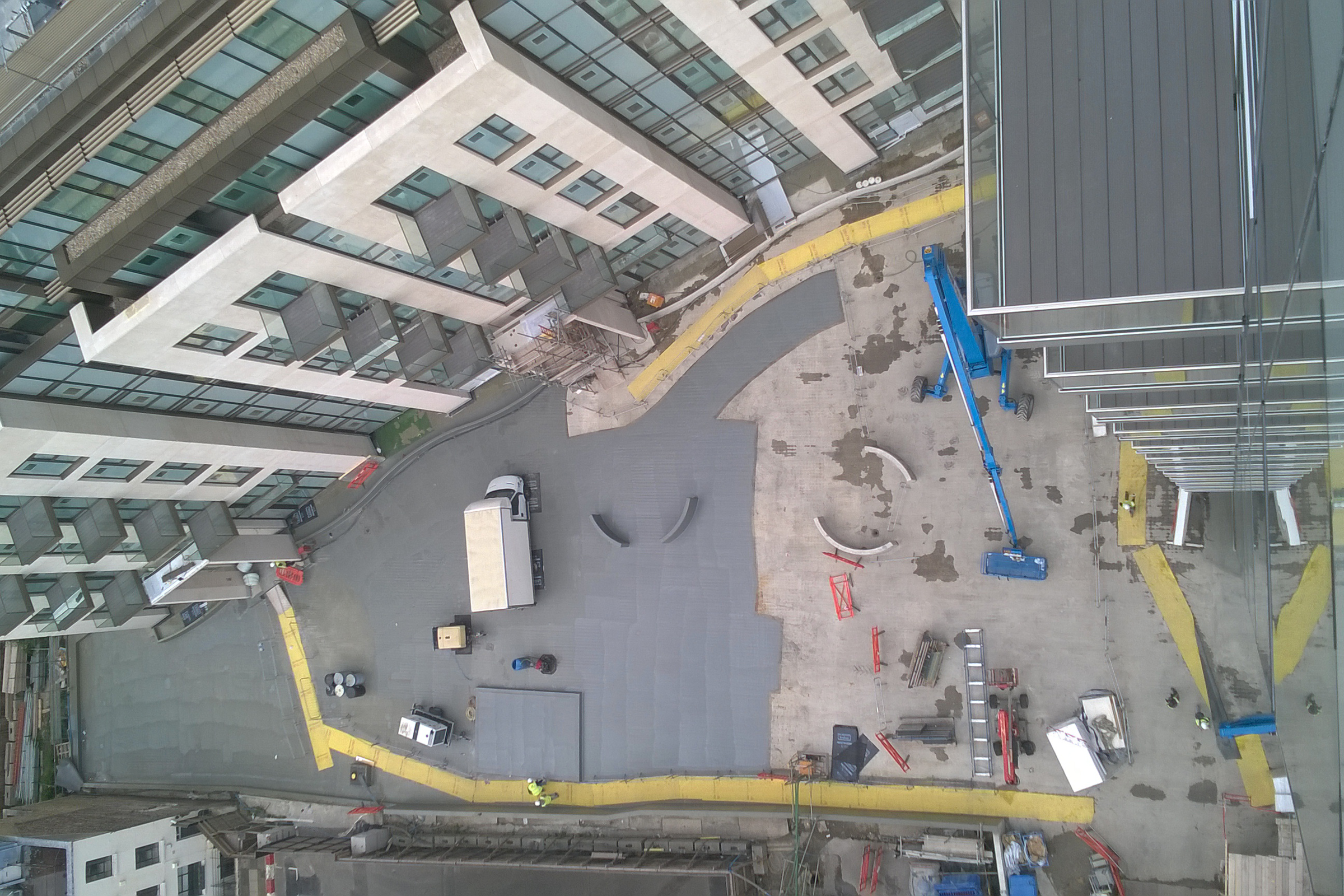
Photo courtesy of GCP
Time is money with construction projects, and there are tight schedules with deadlines that need to be met. Because cold, liquid-applied waterproofing can be applied to a broader area in less time than HRA, especially if it is spray-applied, builders can save a great deal of time and even labor costs by going with this solution. This speed of application benefit increases with the size of the project—the larger the square footage, the greater the time savings and benefits over hot-applied/HRA liquid waterproofing.
With HRA, the applicators must spend time filling buckets or carts with the asphalt and running it around the construction site. Spray-applied cold liquid waterproofing can cover large areas due to its ability to potentially run several hundred feet of hose off the spray pump. The spray pump is more mobile than a hot rubber kettle, and liquid doesn’t have the long heating or start up time that HRA has. As a result, it has an advantage over HRA with respect to preparing, transporting, and conveying the equipment and materials.
With small or highly detailed surfaces
With waterproofing projects that include small or vertical surfaces, flashings, or intricate details, cold, spray-applied liquid waterproofing does not have the limitations or involve the multi-step, multi-layered process that HRA has. Because it’s fast curing, a cold, spray-applied waterproofing has no vertical limitation. It only requires application of a primer and the monolithic coat, which covers across the entire area, up the verticals, around the curb flashings, and onto all penetrations. When cold-applied liquid waterproofing is used, none of the reinforcements that HRA solutions require are needed.
With green roofs or planters
With green roofs and planters you have vegetation and soil on top of the waterproofing membrane. As a result the membrane must be able to resist plant root growth that could be potentially damaging and diminish its protection of the surface below. The chemistry of the material in cold-applied liquid waterproofing has been tested and found to naturally function as a necessary root barrier for green roofs and planters. Unlike it, hot-applied/HRA liquid waterproofing requires the application of an additional protection layer to provide any root growth resistance.
When submerged underwater
With tanks like stormwater retention tanks that need waterproofed linings, cold-applied liquid waterproofing has proven to be most effective.
When time is a factor
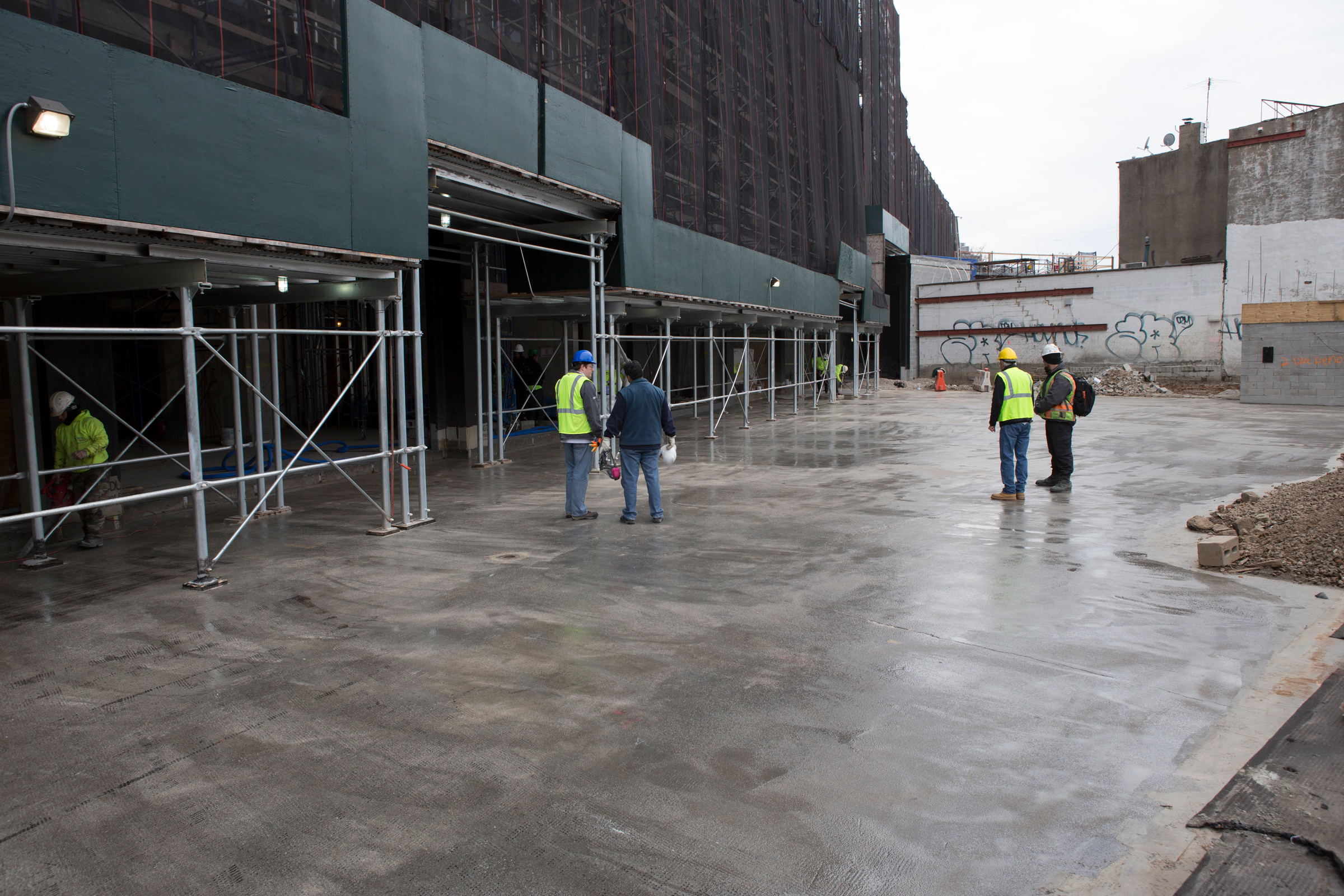
Photo courtesy of GCP
A project’s overall costs can increase exponentially when delays occur. With waterproofing it’s critical that the material preparation, application, and curing times are efficient. When comparing cold-applied versus hot-applied liquid waterproofing systems, the number of installation steps and requirements for each step determine the total time required for system installation. (Application guidelines, including the minimum concrete cure time and required preparation, are provided by the waterproofing product manufacturer and should be reviewed specifically for each project.) Cold-applied waterproofing systems typically require less installation time because the detailing is simplified and the total number of installation steps are reduced.
With HRA, fresh concrete must be cured per the waterproofing manufacturer’s installation guidelines prior to preparing the substrate. Once the concrete is ready, it can take multiple days to prepare the substrate by completing the required priming and detailing for the entire section to be waterproofed. Then, to apply the membrane, several hours or more are needed each day during installation to heat up the rubberized asphalt prior to mopping.
Alternatively, with a cold-applied system, the product components are mixed and ready in minutes to be applied as a membrane on the prepared substrate. The reduced material preparation time alone saves hours per application day. Installers have reported that cold-applied waterproofing has a two to three times faster preparation time than hot-applied systems.
Building the membrane with a hot-applied liquid waterproofing system requires around five to six layers, including the rubberized asphalt, neoprene flashing, and the reinforcement and protection layers each made of separate materials. The detail work is separate. The cold-applied liquid waterproofing membrane requires only two to three layers, which takes much less time to apply. No reinforcement layer is required, as the membrane is self-leveling. The cold-applied liquid waterproofing application saves steps that need to be taken with a hot-applied system, making it 3.5 to four times faster to install than hot-applied.
The time that it takes for the hot-applied installation to cure or harden and for the surface to be ready for return to service could be 24 hours. The cold-applied installation can withstand foot traffic as well as resist rain in two hours, making it up to 12 times faster than hot-applied to cure, enabling a faster return to service.
In Conclusion
There are some scenarios in which either cold vs hot-applied liquid waterproofing products work well and even a few in which hot-applied, specifically hot rubberized asphalt (HRA), may be the preferred option. However, for most construction site waterproofing scenarios—particularly the performance-critical and time-sensitive ones—cold-applied liquid waterproofing like GCP’s SILCOR® liquid waterproofing line has been proven to be the better option.