Story at a glance:
- Before you choose what type of “concrete look” you’re after, you need to consider your substrate.
- Polished concrete and grind and seal concrete may look similar to the naked eye, but there are many differences.
As a leader in innovative specialty coating systems, the experts at Westcoat field a lot of questions—both in the field and during AIA presentations.
We recently talked with Westcoat Product Manager Todd Cook to explore solutions like concrete flooring, which coatings to use where, and more. Here we share his responses to some of architects’ top questions—and some they should be asking.
How do I achieve the concrete look?
There has been a huge demand for the concrete look for the last five or 10 years. Often an architect or flooring professional sees another project and points to that as a reference. This is a great starting point, but you also have to think about your substrate and the overall function and use of the space.
Some questions to consider:
- Is this project a new construction or reconstruction?
- Are you going to pour new concrete?
- Are you working with the existing slab?
- Is it on-grade, or is it elevated above-grade (for example, a wood subfloor and no concrete to actually work with)?
These questions should help inform clients about some of the limitations but also the possibilities so they clarify expectations. It’s critical with any project to clarify and manage expectations.
What should I consider in new construction?
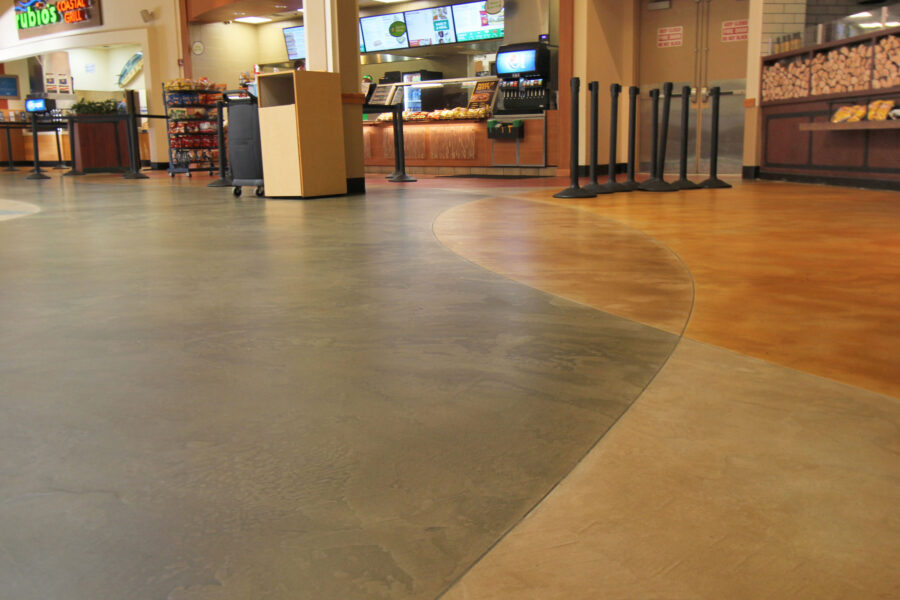
Photo courtesy of Westcoat
When we’re talking about new construction or projects with new concrete substrates, you have a lot more control. In that case you can design the look of the slab, you can add color, you can decide how the slab should be finished, and how it should be protected. You’re working from a new canvas.
What should I consider in reconstruction?
When you have a reconstruction project you’re stuck with the existing slab. You have to work with what’s available to you. That means that for certain desired finishes, like a grind and seal or a polished finish, all the repairs, cracks, and other attributes are going to become an inherent part of that finish. In some cases this may work for the overall design. For example, maybe you’re looking for something more rustic or industrial. But in other cases clients aren’t going to be happy; they want more of a polished, finished, refined look. That prompts one of the most critical aspects of all of this—the mockup.
Why do I need a mockup?
Mockups are so important for all projects, and they’re especially critical when we’re dealing with grind and seal or polished finishes in reconstruction. That’s because we’re dealing with an existing substrate.
When making a mockup make sure you factor in adequate size in a suitable location so you accurately represent the overall finish and target to the client. You don’t want to do your mockup on the best piece of the concrete, when 90% of the floor doesn’t look like that one area, for example.
What is polished concrete vs. grind and seal?
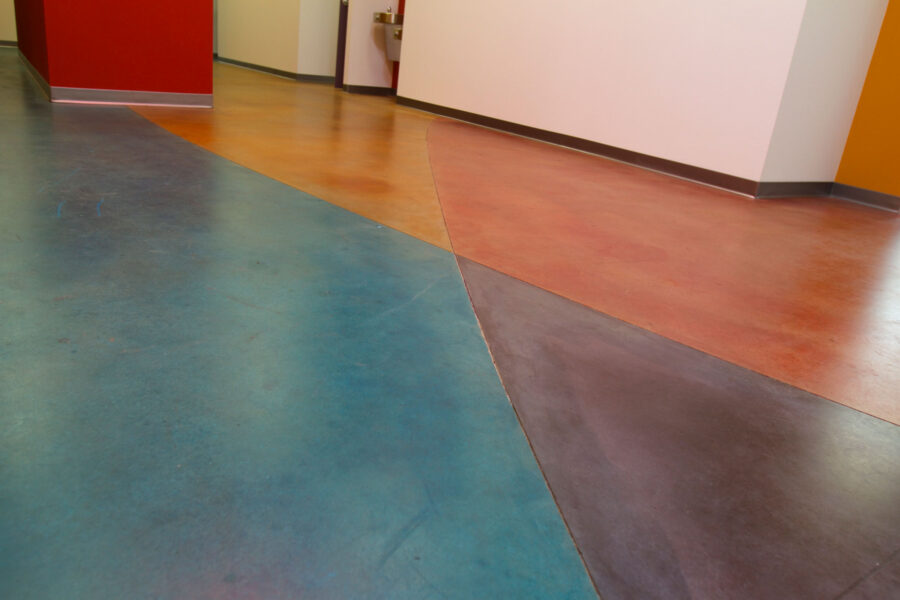
A fast stain grind and seal solution from Westcoat is seen here in a university project. Photo courtesy of Westcoat
That is a question we get very often because some people don’t know the difference. These two terms sometimes look almost visually the same. You can be on the floor and think, “This is a beautiful, polished floor,” but it’s grind and seal.
What is polished concrete?
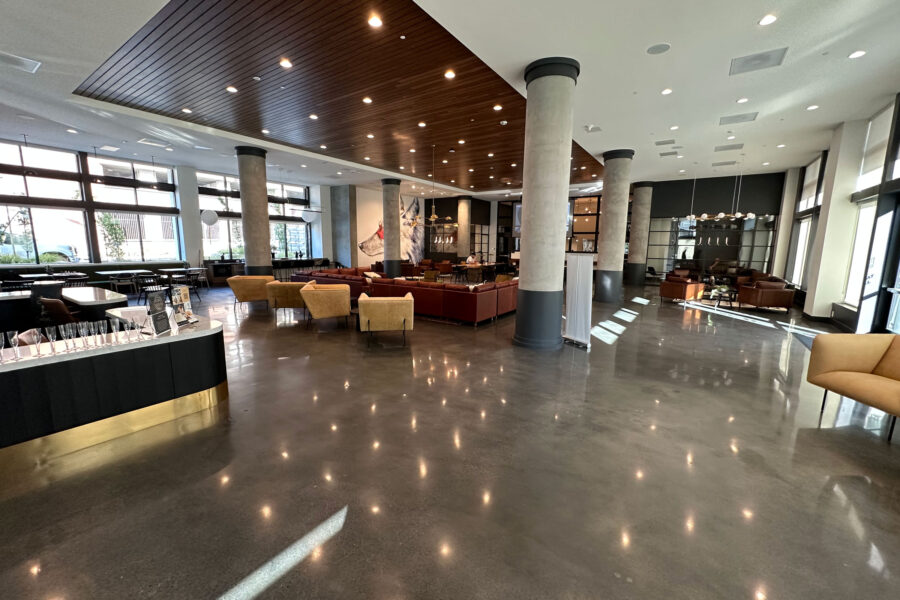
The concrete look in this restaurant provides a shiny, also mirrored feel. Photo courtesy of Westcoat
Polished concrete is a multi-step process where the concrete is mechanically ground with a series of abrasives. It will start with coarser metal bond diamonds. They’re used for the initial passes to cut the floor and to help provide the desired aggregate exposure. The Concrete Polishing Council has provided what they call an aggregate exposure chart that outlines the levels of exposure. In layman’s terms what you’re doing is exposing more of the aggregate as you cut deeper into the concrete; generally the size of the aggregate will increase. A light grind will get you that salt and pepper exposure whereas further into that concrete matrix you get into larger aggregates.
After they’ve utilized those metal bond diamonds they’re going to transition over to resin bond diamonds. Those tools are specifically intended to hone or polish the concrete. Sometimes if it’s a really high polish you can see the lights bouncing from the floor off of it—almost a mirrored appearance.
What materials are used in the polishing process?
In addition to the mechanical process where you’re using these tools and grinders, there are some specific products used in the polishing process. These materials are called densifiers, grouts, and guards. They’re typically used for the entire polishing process.
- Densifiers are commonly applied earlier in the polishing process. They react with the concrete to help provide a surface that’s more resistant to water damage surface abrasion. They help reduce dusting and provide for a greater ease of maintenance.
- Grout materials, resinous or cementitious, help to fill small pits and other minor surface defects.
- A guard is applied over the polished surface.
These materials will help to increase the overall gloss or sheen and also aid in stain resistance.
What is grind and seal concrete?
A grind and seal starts off similar to the polished concrete. It uses the same type of metal bond diamonds, but the concrete surface isn’t refined and honed like it is with polishing. That’s because we want to have a more porous concrete substrate because we’re going to apply a topcoat or sealer. We need a little bit of porosity to promote adhesion for topcoats.
There are a lot of different topcoats and sealers that can be used in grind and seals depending on the design and use of space. It could be acrylic, epoxy, or polyurethane. At Westcoat we offer both polished and grind and seal systems. We believe both have a place. Both can offer a natural finish; they can accent the existing color of the concrete or the substrate itself. You can utilize concrete stains with either polished or grind and seal application so you can have that influence of color.
When should you choose polished concrete?
Polished concrete is generally a great option for projects looking for a cost effective, durable, environmentally friendly solution. Polished concrete does require maintenance and proper cleaning. Sometimes there’s a misconception that polished concrete is maintenance-free when it is not; it’s still a decorative finish, and it does require some upkeep. Like any surface you have to maintain it, but it has a really great lifespan when kept up.
Additionally, polished concrete can be a really nice solution when you have projects that might have high levels of moisture. For example, maybe moisture is coming up through the slab. In that case a polished system can let it breathe. There are no topcoats, no coatings.
When should you choose grind and seal?
Grind and seal is excellent for clients who want a concrete look with greater chemical resistance. They typically use two components, clear topcoats such as epoxies and polyurethanes. This is especially true in areas like cafeterias or grocery stores—places where there are more frequent spills and staining. Something I’ve seen over the years working with architects is that they specify polished concrete and find it’s not holding up in certain environments because it should have been set up with a grind and seal application. That’s going to get you better cleanability.
You can also get a lot of gloss or sheen control from grind and seals because you have a lot of options with regards to a gloss or a semi-gloss flat. You can utilize these different sheens to control those gloss levels even on the same project. You can have an area over here that’s gloss and over there that’s semi-gloss.
We also get a lot of questions about slip and falls. It can be hard in a polished system to add non-skid additives; some polished floors can have a pretty good slip resistance. But when you’re considering ramps or areas exposed more to liquids—cafeterias, grocery stores—a grind and seal in some cases can be a better option. Then not only do you get the chemical resistance and stain resistance, but we can utilize skid-resistant additives that will increase the slip coefficient. Now you have safe floors with adequate skid resistance, the concrete look, and decorative finish.
What happens when concrete cannot be finished?
In some cases there was extensive damage to the slab or maybe it’s an older slab or was exposed to a lot of water or chemicals, or maybe there was poor maintenance. Architects ask us what they should do when they want a concrete-like finish, but the floor isn’t suitable. That’s when we look to cementitious toppings.
What are cementitious coatings?
Cementitious toppings consist of a polymer-modified cement formulation. They’re intended to be applied directly over concrete that was properly prepared. These coatings can typically go anywhere from a 16th of an inch up to a couple of inches thick, depending on the overall use and design.
For example, they can work with your existing elevations; maybe you’ve got your doors in place already and you want that concrete look, but you find that you can’t put two inches of concrete on this. That’s where a cementitious topping can be a great option.
These materials are typically either self-leveling in nature, which can help to even out floors, or they can be applied by hand with a trowel or squeegee. You’ll see them offered in white-gray formulations, but they can be integrally colored, they can be stained, and they can be sealed.
Some of the self-leveling options can feature a decorative aggregate. This can be nice when you want to recreate that concrete exposure look; you can basically pour these topping slabs, grind them, and either polish or seal as mentioned before.
When you’re working with cementitious toppings it’s really important that any client reaches out to the manufacturer of these materials ahead of time. You want to discuss the desired look, talk about the limitations and what required surface preparations may be required, and then your dive into the options with regards to finish. Then request some samples and color charts.
What’s really cool about cementitious toppings as opposed to working with the existing slab or canvas is that these are manufactured. This allows for an applicator to produce mockups off-site. We can make samples for architects, and that’s really helpful; they can then compare that against the carpets, the wall finishes, and so forth. It allows them a little bit more freedom. Again, visualization and expectations are really critical.
What are my cementitious coatings options?
At Westcoat we offer a full line of cementitious toppings in our TC—or Texture-Crete category. We also have our ALX Interior System. This is a perfect solution for projects that have wood subfloors and want that concrete-like finish. The ALX Interior can be installed directly over plywood. It starts with our WP-40 Sheet Membrane—a 40 mil thick sound reduction and anti-fracture membrane.
Then we have an expanded diamond metal lath and a series of polymer-modified cementitious coatings. This is going to give you reinforcement and strength, and it’s going to be installed so thin—about a quarter of an inch thick only, right over your plywood. With this system we have really unlimited finishes; we can do almost anything because it can have integral color, it can be stained, and you can add topcoats, sealers, glosses, and all kinds of textures. We can meet or exceed your slip resistance, and we can produce smooth finishes because it’s hand-troweled. There’s a lot of versatility and a kind of artistic approach to this finish. And it’s a very long-lasting option.
What about epoxy or resinous flooring?
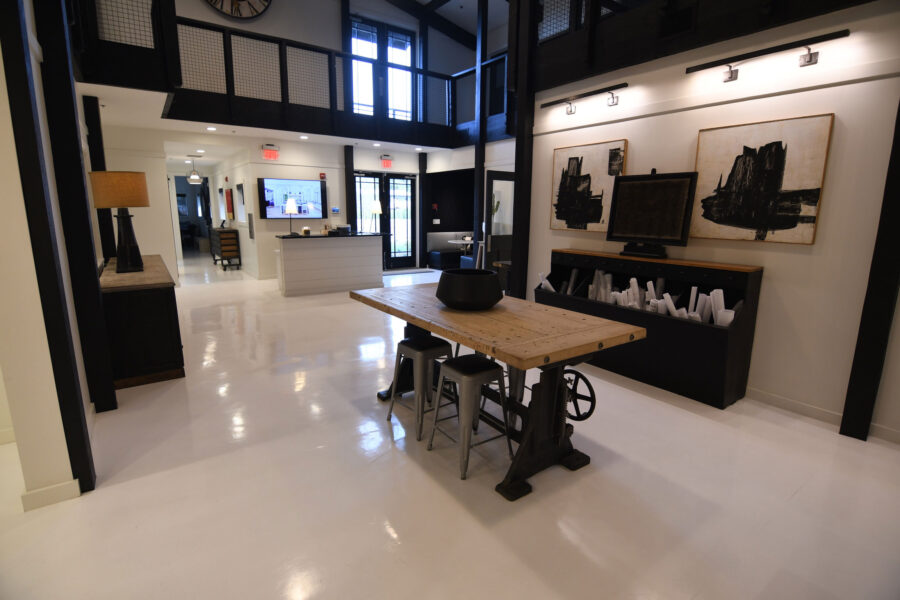
Epoxy flooring as seen in an architect’s office. Photo courtesy of Westcoat
We get this question a lot from architects and designers. A lot of people associate resinous flooring with warehouses; they think of it as utilitarian, that it comes in gray and tan only, that it’s just a workhorse. The reality is resinous flooring has transitioned over the last 15 to 20 years, in some cases even longer, to be a very decorative medium for interior flooring.
You’ll often hear about resinous flooring as epoxy flooring or poured flooring. Resinous flooring covers a wide variety of chemistries and technologies. It’s well known for its durability, adhesion, and seamless nature, which is a really important aspect with regards to cleanability, antimicrobial maintenance, and you don’t have any of the grout lines or seams like you would with vinyl. The systems are generally offered at 20 to 30 mils thick. They offer really exceptional chemical impact and heat resistance. There are also flexible membranes that can be used, moisture vapor barriers that can be used, UV resistant finishes, slip-resistant textures, and more.
What about color?
Most manufacturers are going to have grays and tans and maybe safety colors and standard colors available, but we’ve worked with a lot of architects and designers and produced a lot of custom colors for clients. Over the years we’ve done bright blues, bold greens, vibrant reds, even millennial pink. If a team says, “This is the color of our brand. Can you incorporate that into this technology?” in many cases we can take that color to our laboratory and match it. Now designers and architects don’t feel limited to their palette.
We can match almost anything, and that’s empowering.
A lot of times with traditional flooring you have to work with the tiles or carpet swatches available to you, but we can match almost anything, and that’s empowering. Now when we work with the Googles or the Amazons and they want the floors to maybe wrap up the walls to create really dynamic looks with multiple colors, we can do that. We can even create seamless colors with beautiful gradients of color. It creates a unique look that’s easy to maintain and can greatly change the impact of a space. Sometimes we’ll even put a satin finish over some of these colors so it becomes warmer and a little more organic. Some people don’t even realize it’s resinous flooring.
What other decorative aspects are there?
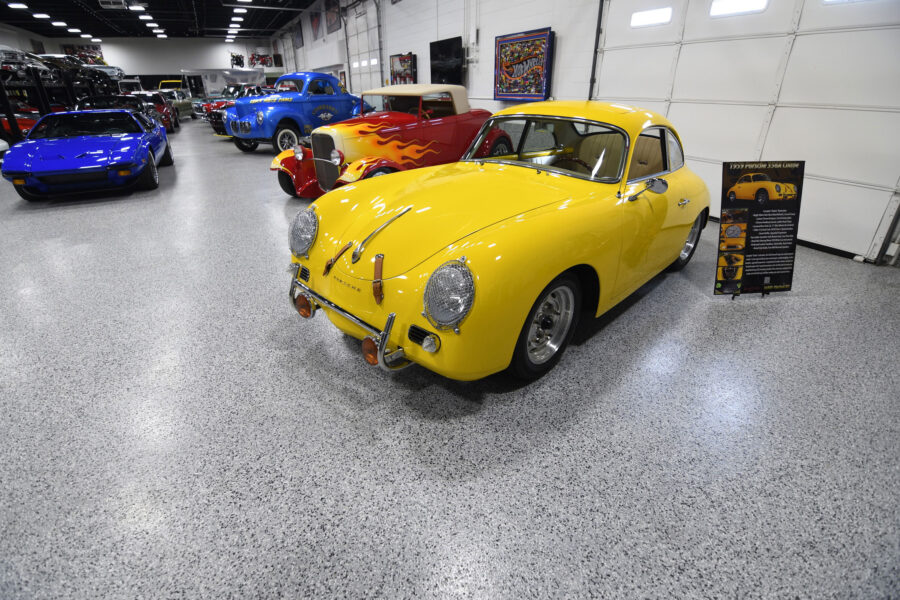
Liquid Granite epoxy flooring is seen here in a vintage car showroom. Photo courtesy of Westcoat
Resinous flooring has a wide array of decorative aggregates that can be incorporated into the material itself and then later exposed or broadcast and sealed. We have our epoxy coat category that will cover a wide variety of decorative finishes. We’ve got aggregates that can be broadcast in the wet film and then sealed, and that’ll provide you with a functional and aesthetically pleasing option.
Our Tidalstone floor is a beautiful aesthetic offering. We also have our Dubro Quartz system, and we have our Liquid Granite system. These will help provide a uniform look to help ensure your project is consistent, and they can be utilized in a lot of different chemistries based on the use of the space. If you’re looking for extra flex we can help with that, if you’re looking for extra chemical resistance we can support that, or if you need heat resistance or to tackle moisture issues we can do that in tandem while preserving the aesthetic. These systems are ideal for office spaces, laboratories, recreation rooms, and showrooms.
What about epoxy terrazzo?
Epoxy terrazzo is a really nice way to get a balance between function and form. It has that very timeless look, very elegant, but it also provides exceptional durability and tensile strength over traditional cement or terrazzo floors, with better chemical resistance.
Not only is it very durable, but you can now implement aggregates like terrazzo, marble, or glass—things you see in airports where there are really astounding decorative looks. These systems hold up to immense traffic so you’ll see them in places like airports and government buildings, for example.
What is metallic epoxy?
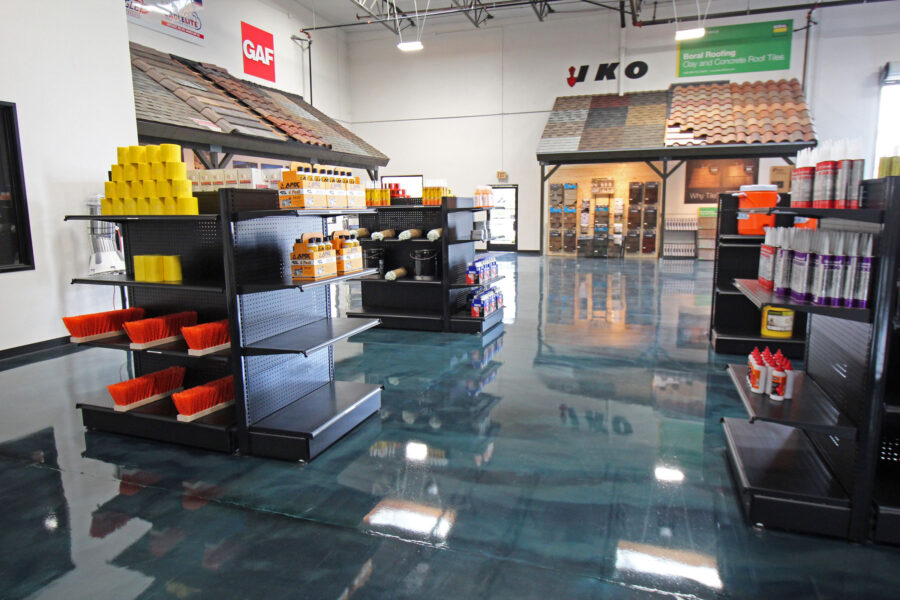
Liquid Dazzle brings life to a pool retail store. Photo courtesy of Westcoat
Metallics make for exciting floors, sometimes in multiple colors. Our Liquid Dazzle system is 100% solid epoxy with a proprietary metallic additive. You can take multiple colors and blend them to create a masterpiece. These are perfect for hotels, casinos, salons; they’re showstoppers. And you still have all the functionality of resinous flooring—the chemical resistance, seamlessness, durability, they’re easy to clean, and it’s a beautiful, monolithic floor.
Why should architects consider resinous flooring in general?
You have an extensive amount of options available to you. When you’re approaching your next flooring project don’t rule out resinous flooring because in many cases you may need the functionality of that type of chemistry. The aesthetic principles and properties are there and available for you to still have your design appeal and reach those aesthetic principles you might be looking for.
Some of the polished concrete and grind and seal cementitious and resinous flooring, while they may be considered alternative flooring, they really are invaluable flooring options for design professionals.