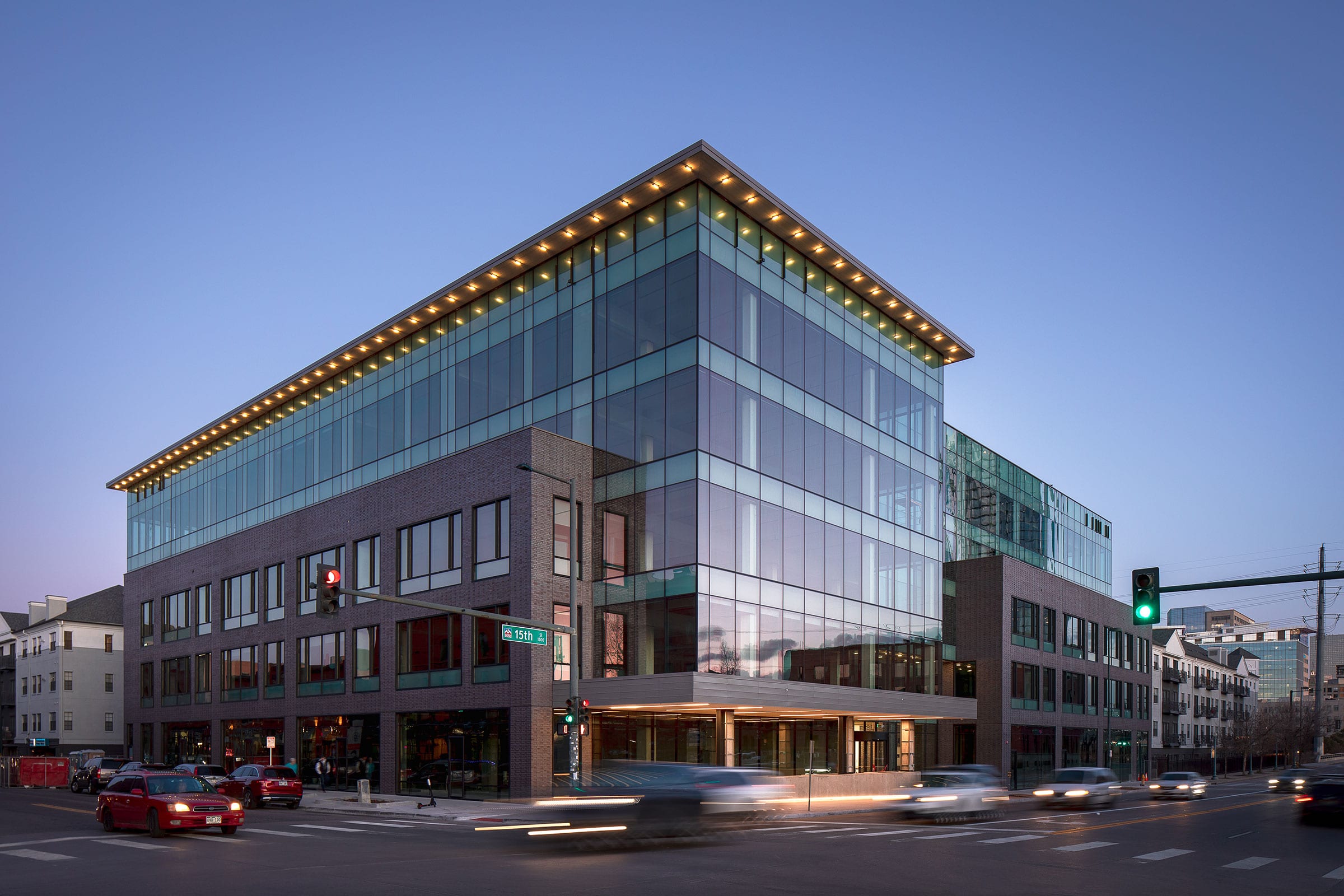
“It’s important to respond to what clients want while also finding the most economical system that meets their needs,” says Chris Kendall, principal at KL&A, Inc. “We did an extraordinary number of studies on Platte 15 to confirm that we had both. I would argue that we could not have been any more efficient with the CLT for Platte 15.” Photo by JC Buck
Nordic Structures makes better buildings possible with mass timber.
Eight hours drive north of Montreal lies a vast boreal forest with acres upon acres of black spruce trees dotted with peat bogs. There the founders of Nordic Structures’ parent company Chantiers Chibougamau saw an opportunity to make better building products while maintaining the longevity of the forests they were harvesting. It was in these woods that the masterminds at the Quebec-based mass timber company developed a way to not only minimize waste, but to also promote growth of new trees that absorb more carbon dioxide than those that are past their prime.
Jean-Marc Dubois, director of business development USA for Nordic Structures, explains the process. “It takes 80 years for those trees to achieve peak maturity, and they’ve got a 40-year window during which they’re viable before dying,” Dubois says. “The average diameter of these trees is only four-and-a-half inches, which is very small when compared to much larger and longer lived southern yellow pine or Douglas fir, the other primary species for manufacturing mass timber components like glulam beams and cross-laminated timber (CLT) panels. You have to think differently when you only have such a meager resource to work with if you want to elevate a product to its best and highest use.”
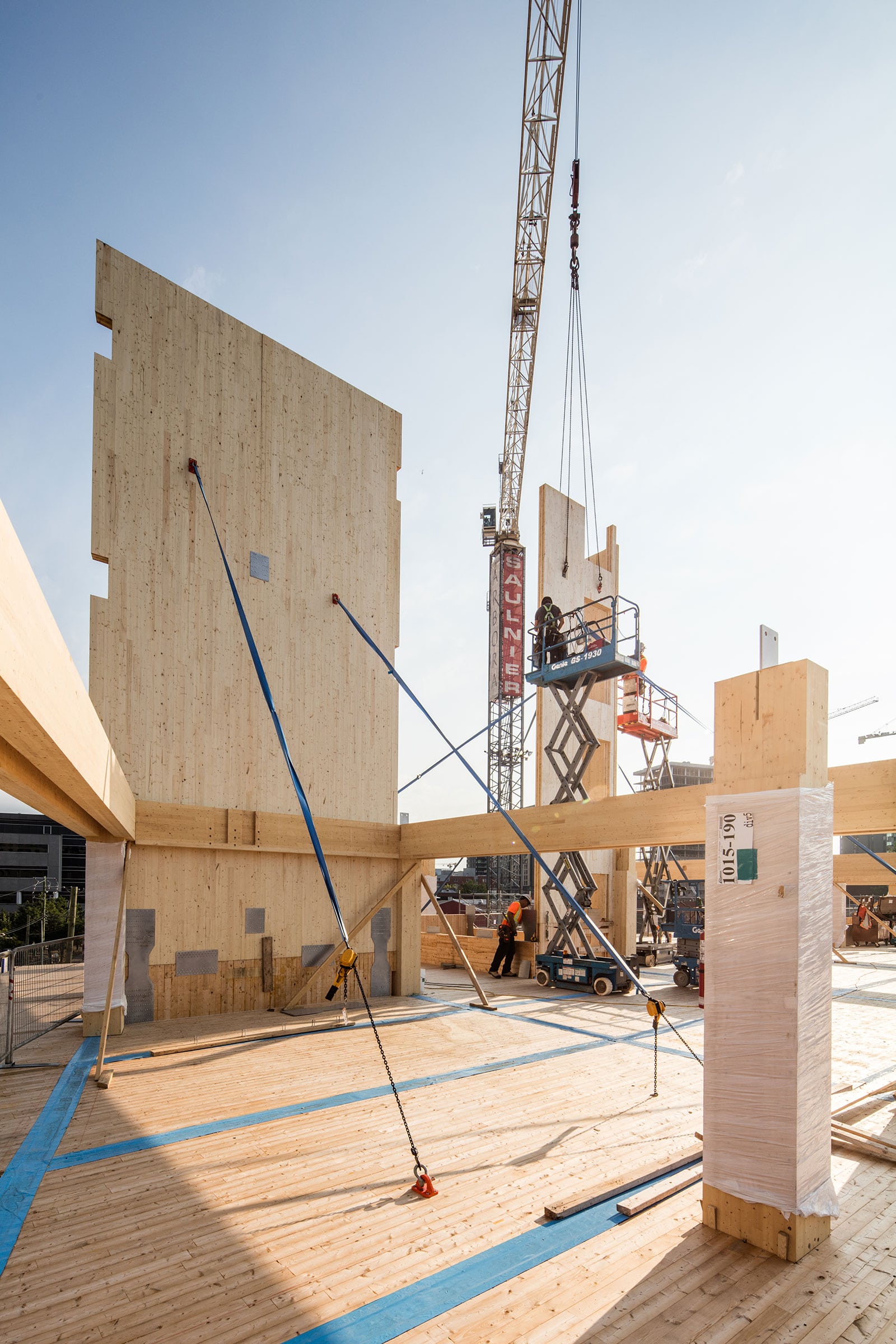
In Quebec Arbora was the largest complex in the world built from massive timber when it was finished. The 597,560-square-foot project has more than 130 condominiums, 30 townhouses, and 272 rental units. This development distinguishes itself with 40% of its area dedicated to green space, and it has achieved LEED Platinum status. Photo by Adrien Williams
But Nordic Structures (a family-run business founded in 1961) is a known innovator, and better building materials are possible because of it. They use component pieces as small as three-quarters of an inch by an inch-and-a-half by 24 inches long as well as the tree tips. “To other people that would be considered waste that either gets left in the forest or gets chipped and thrown away,” Dubois says. “We’re extracting nearly 20% more yield from the same trees than has been possible in the past, and we’re not just turning it into fencing or furring strips. We turn it into mass timber components for large structural projects being built across North America.
These are some of the benefits of building with engineered wood.
Sustainable.
Waste is eliminated by mass timber. Every piece of engineered wood that arrives on a job site is integrated into the building because you know from the start what you need, which also reduces dumpster fees and waste remediation.
Air quality is improved, considering these mass timber components are manufactured without using formaldehyde-based glues, and Nordic products are Red List–free, making them ideal for LEED and Living Building projects.
Exposed mass timber elements also contribute to the biophilic response in humans, as studies show reduced stress and heart rates in these environments. They’re carbon negative, too, as they encapsulate one ton of carbon dioxide in every cubic meter of wood for the life of the building. Buildings made of mass timber can be deconstructed at the end of their life cycle and re-utilized rather than sent to the landfill.
Flexible design.
Buildings made of mass timber can be modified more readily to adapt to changing market dynamics. The best designs are made possible in part because Nordic Structures has its own design office with more than 50 employees in Montreal dedicated to design, engineering, and drafting. “We build the materials in the computer first and then manufacture the product to the design,” Dubois says. “We can build a large structure and be more accurate than a traditionally framed structure. That accuracy comes from multiple design iterations, as that process is fully CAD driven in the modeling phase.”
The Nordic team can find any structural inconsistencies or areas of concerns early—before construction starts. “You eliminate errors and you’re putting together a model kit with instructions. Every piece is numbered, and every piece has its place on the job.” Millimeter precise CNC finished material greatly reduces the need for onsite adjustments. “When you’re building with steel and concrete, many times the designs are not completely finalized when construction starts.”
Fast construction.
“Fast construction is predicated on good design to begin with,” Dubois says. With mass timber you’re not building onsite with saws, hammers, and nails. You already have the large precise panels ready to go. “Panel wall manufacturers improved the product stream and reduced waste by taking those components and building them in a factory ahead of time. We do the same with all the elements that comprise the structure.”
Construction is fast, quiet, and exact, as the design was solidified in advance. This speed typically reduces project time by 30 to 50%. Construction is simple; assemble using conventional hand tools, fasteners, and connections. That also means you need less people onsite—less than 10 compared to as many as 40 on a concrete job. “From a work safety standpoint, having less people on the job is pretty impactful, but then we’re also in a labor crisis, so the fact that you can build these structures more quickly with less people is a better use of overall manpower, and it’s a very learnable skill.” Consistent wood supplies also reduce or eliminate jobsite delays due to unforeseen raw material supply constraints common to steel and concrete availability.
High performance.
Timber is an insulator, as compared to steel and concrete, both of which are thermally conductive, and mass timber has the added benefit of thermal mass and thermal inertia. Buildings built with mass timber require less energy to heat and cool and maintain their temperature more readily, making for a more comfortable working and living environment.
The development team behind Platte 15, a five-story project and Denver’s first cross-laminated timber building, couldn’t have been more pleased with their decision to work with Nordic Structures. “This building will store 1,790 metric tons of carbon dioxide within the wood. Another 3,800 metric tons of carbon dioxide greenhouse gas emissions will be avoided for a total potential carbon benefit of 5,580 metric tons,” says Conrad Suszynski, co-CEO of Crescent Real Estate. “We have proven wood is a cost-viable, sustainable structural option with regenerative benefits for mid-rise commercial construction. That’s a genuine evolution, and that’s a big deal.”
Cost-effective.
“People think about cost per square foot without looking at the holistic impact in the overall projects,” Dubois says. Wood’s lighter footprint can help reduce foundation size, and since the large panels delivered to sites are lighter than precast concrete, mass timber may allow for larger structures in areas with low compacted or remediated soil conditions.
The architects at Platte 15 indicated that working with engineered wood saved time, and time, of course, saves money. “The mass timber was precisely engineered prefabricated using CNC machines,” says Joe Anastasi, senior associate at OZ Architecture. “This level of precision helped improve delivery speed and construction time and eliminated a significant amount of waste.”