Story at a glance:
- Standing seam metal roofing systems are becoming a more popular option for residences.
- Englert is a leader in onsite roll forming and standing seam metal roofing technology.
- Englert offers more than a dozen lines of architectural, structural, and curved panel metal roof systems.
For architects and developers who are looking for a stylish, durable, and sustainable alternative to traditional asphalt shingles, metal roofing systems offer the ideal solution. While they were once more commonly seen on commercial and industrial projects, standing seam metal roofing systems have quickly gained popularity among residential customers as word has spread on their countless benefits.
Yet when choosing a roofing solution, geography is key. As the effects of climate change become more evident and the weather becomes more unpredictable, having the appropriate roof for your region’s climate is critically important.
“Metal roofing systems outshine competing materials in just about every metric,” says Jeff Barnard, technical representative at Englert. “But finding a trusted supplier who is familiar with local regulations and testing requirements is the key to success for any roofing project.”
Englert is widely recognized as the leader in onsite roll forming and standing seam metal roofing technology. The firm pioneered the “total system” for metal roofing solutions—they manufacture all of the roofing materials as well as the innovative machinery used to shape and cut the metal into customizable panels at the job site. Their suite of products includes more than a dozen lines of architectural, structural, and curved panel metal roof systems, as well as the gutters and accessories that accompany them.
Barnard recently sat down with us to discuss the regional variations in roofing testing requirements and explain the benefits of a metal roofing system in any climate.
What makes standing seam metal roofing systems superior to traditional roofing materials like asphalt or slate?
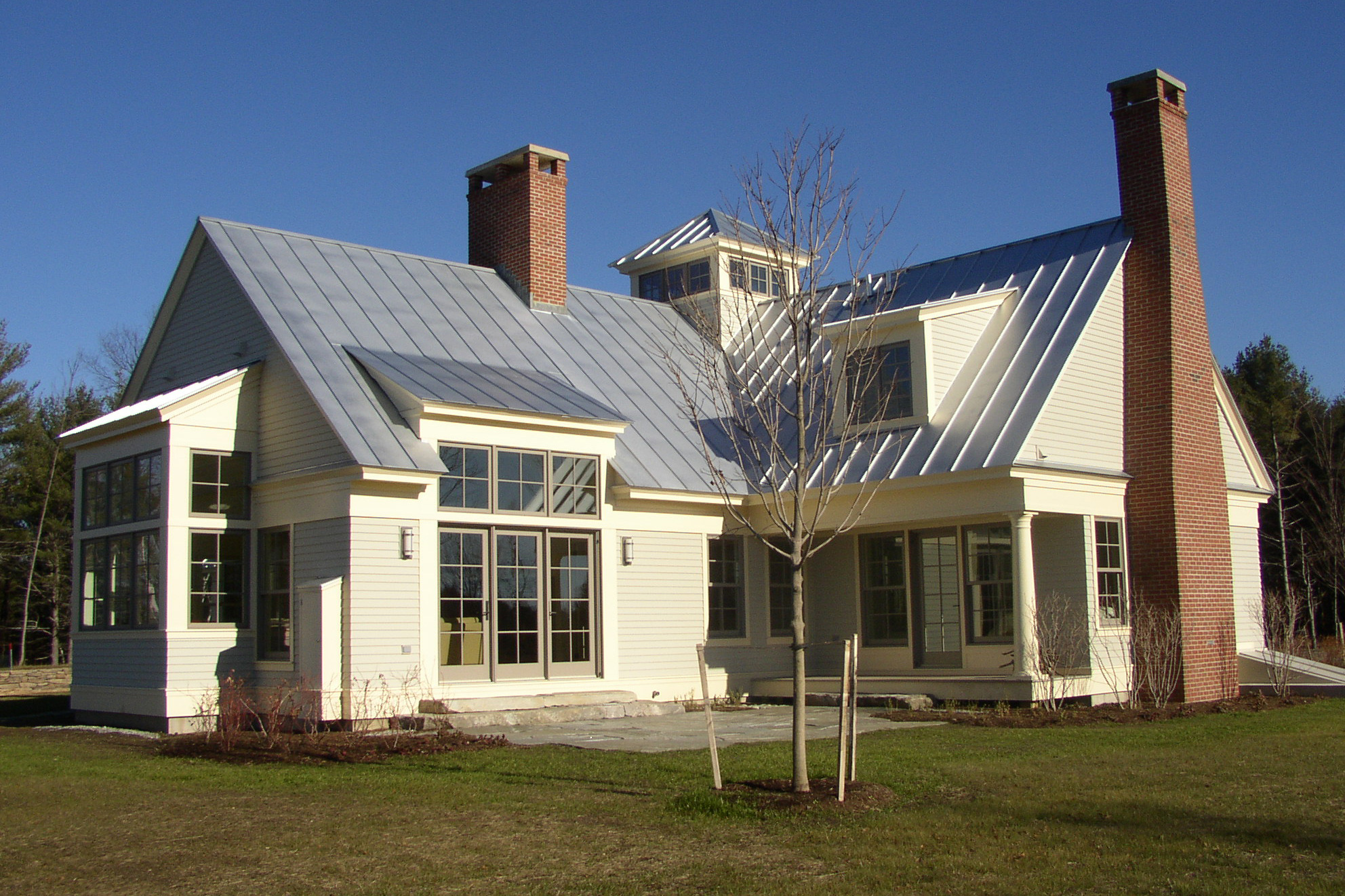
Photo courtesy of Englert
The first thing that comes to mind is the longevity and durability of standing seam metal roofing systems. They have a useful life of up to 80 years, whereas traditional shingles can last anywhere from 15 to 30 years. Concrete tile and slate roofing systems are more durable than asphalt shingles in a milder climate, but they’re not resistant to hail storms or large branches landing on the roof. This can be a problem in places with more extreme weather, like the South or Midwest.
Standing seam metal roofs are also unique in that they’re weather tight. The fasteners that attach the roofing system are concealed inside the panel’s seams, and there are no rubber washers that eventually fail and cause leaks. This makes them ideal for the rainier climate you see east of the Mississippi River.
Then there’s the simple fact that metal roofs look great. Architects often compare metal roofs with tile and slate for higher-end homes. Both options offer a more refined look than asphalt, but slate is so heavy, it’s going to add a lot to your construction costs.
Tell us a bit about testing requirements and regulations around the US. How do various regions differ?
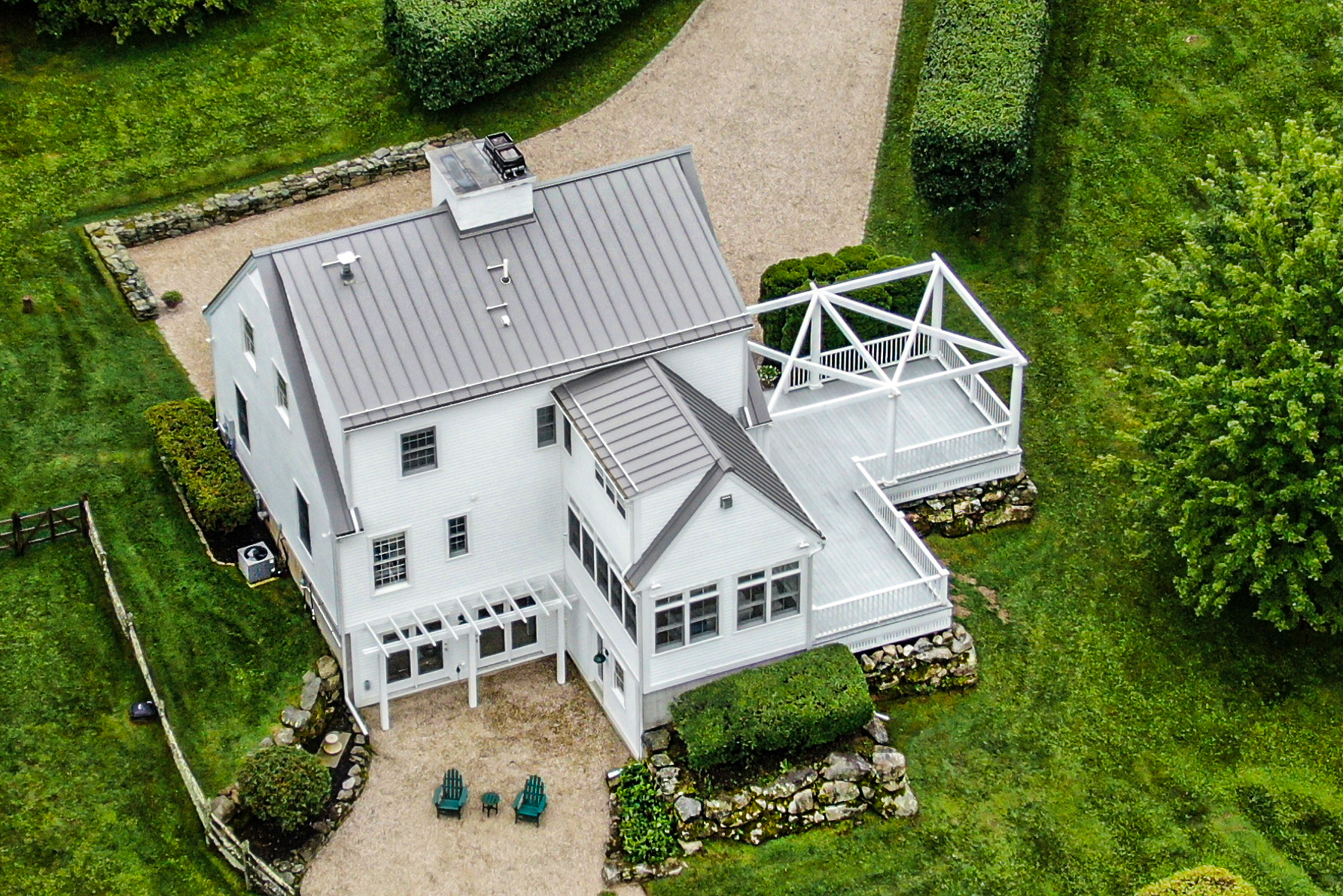
Photo courtesy of Englert
Throughout the country overall, the UL 580 Class 90 wind uplift tests are pretty universally referenced in construction specifications. This tests the roof deck and any attachments or coverings and lets the engineer know that a roof can withstand 90 mph winds. For metal roofs in particular, the ASTM E1592 wind uplift test evaluates the performance of metal panels and attachments by uniform static air pressure difference. These are testing standards you’ll see throughout the East Coast and Midwest.
Naturally, regions like Florida and the Gulf Coast that get a lot of hurricanes have tougher requirements than other areas. When Hurricane Andrew hit Florida in 1992, it was a wakeup call for the industry. The Florida Building Code (FBC) has its own product approval evaluation and usually follows UL 1897, which is a continuation of 580 but tests to failure and evaluates roof covering systems. In Florida, builders need to be prepared for a possible Category 5 Hurricane, and since you’re testing for the worst-case scenario, that’s about 200 mph winds.
In Texas the Texas Department of Insurance (TDI) has its own product evaluation index for roof coverings. It’s generally pretty similar to FBC, in that TDI evaluates the test data and accepts or rejects it. The TDI listing also provides installation instructions and lists the panel clip spacing and types of fasteners.
How have wind testing requirements evolved as climate change has become a more serious problem?
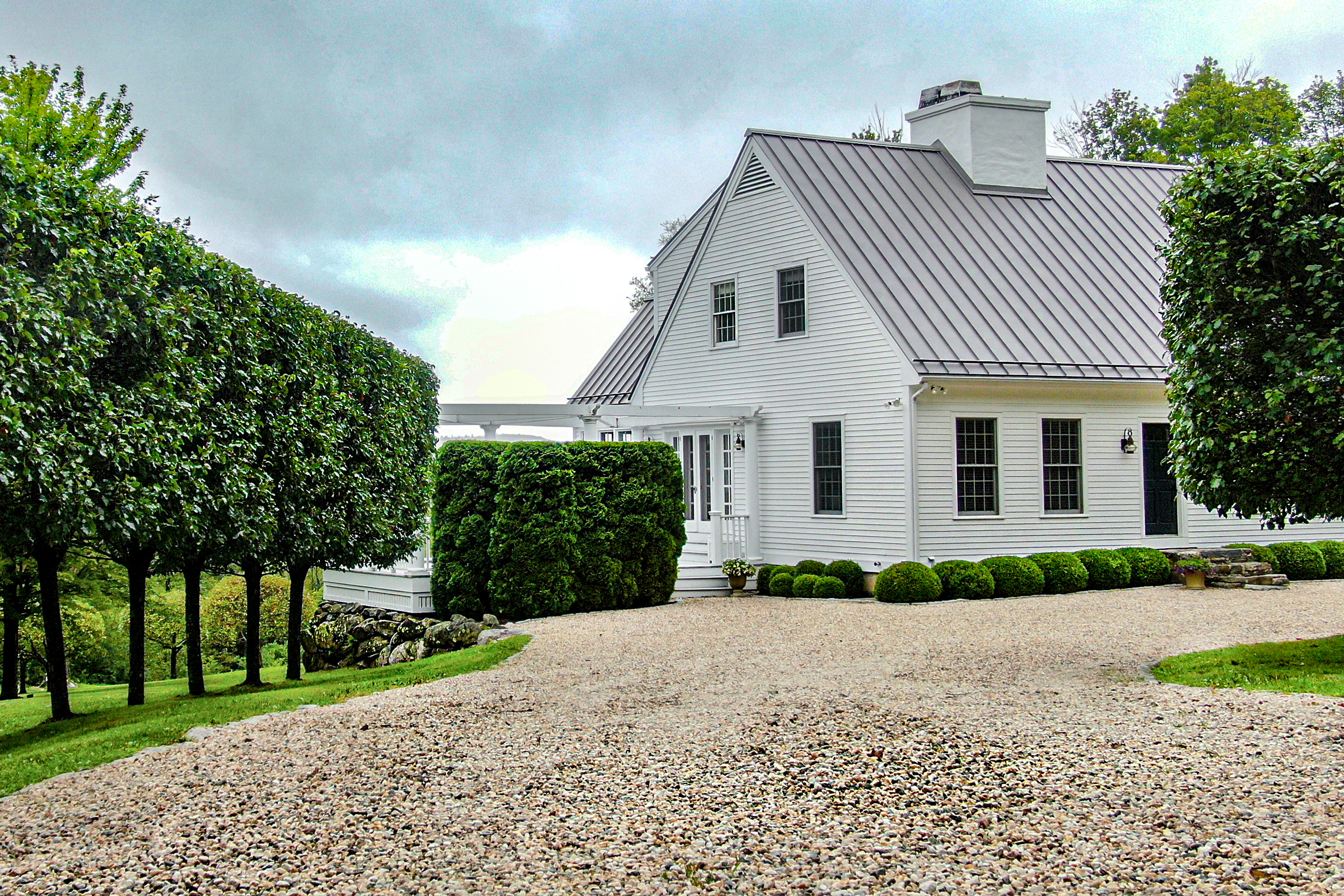
Photo courtesy of Englert
When you consider that storms have been getting stronger, it’s become more of a challenge for building code officials to anticipate the necessary requirements ahead of the next big storm. We only have about 100 years of climate data to go off of, so every time a new record is broken, local regulators need to adjust their standards. This happens in Florida quite a bit. That’s why Englert is constantly aggressively performing wind uplift and other testing, in order to keep pace with the escalating building code requirements.
What other types of environmental factors are important to consider?
The amount of snowfall a region gets is a huge factor when designing a metal roofing system. For mountainous and northern regions of the country, S-5! Metal Roof Attachments are designed for snow retention, with extruded aluminum bars that run horizontally across the roof, perpendicular to the panels, and prevent snow from falling off the roof and injuring people or damaging property.
And while it’s important that snow doesn’t fall off the roof, we also have to consider the weight of the load that’s being held up there. That’s why S-5! specifically designed heavy-duty set screws to secure the panels in climates with heavy snowfall, and they’ve also designed their screw attachments so that each panel can expand and contract with the thermal change each season.
Wind and precipitation aren’t the only environmental issues that need to be factored in. If your metal roofing installation is within one-half of a mile of the ocean, the base metal needs to be aluminum due to the salt-rich environment. Many people think steel is stronger than aluminum, but steel will corrode relatively quickly around salty ocean air. That’s important to consider in coastal areas.
What are the sustainability benefits of metal roofing systems?
This is something just about every architect, contractor, and client is thinking about right now. And that’s great news for us, because metal roofs are far more sustainable than alternative roofing materials. Our aluminum is made from about 97% recycled materials, and it can be recycled at the end of its life cycle.
And unlike shingles or slate, metal roofing systems reflect sunlight back into the atmosphere instead of absorbing that heat. This can have a real impact on your electricity bills since it’ll require less air conditioning to cool your home. On top of that, Englert has its own proprietary paint line, our ULTRA-Cool™ low gloss paint finishes, that meets LEED’s 2.2 Solar Reflective Index. And when you consider the fact a metal roof can last up to 80 years without needing to be replaced, it’s one of the most sustainable solutions on the market.