Story at a glance:
- Designing for flexibility and future changes is important in an ever-changing space like the airport.
- A new terminal at Orlando International Airport used a large amount of raised access flooring to limit future disruption.
- Fentress incorporated into their design a six-inch raised access flooring totally approximately 80,000 sq.ft. to route power and data cabling to the kiosks and to the technologies used at the security checkpoints, ticketing and customs entry areas
Plentiful natural light, palm trees, and a wide open boulevard fill the new International Terminal C at Orlando International Airport (MCO). While daylighting and designing for a sense of place are key to everything Fentress Architects does, some surprising and exciting trends are happening in airport design, too, says Curtis Fentress, who founded the firm in 1980.
“Currently, there is a massive amount of money available for infrastructure—and airports fall into that category,” Fentress says.
Many airports are in the process of upgrading their facilities, adding buildings or new gates or modernizing overall. “It seems like all the airports in the US are trying to upgrade their facilities. It’s an exciting time in the aviation industry,” he says.
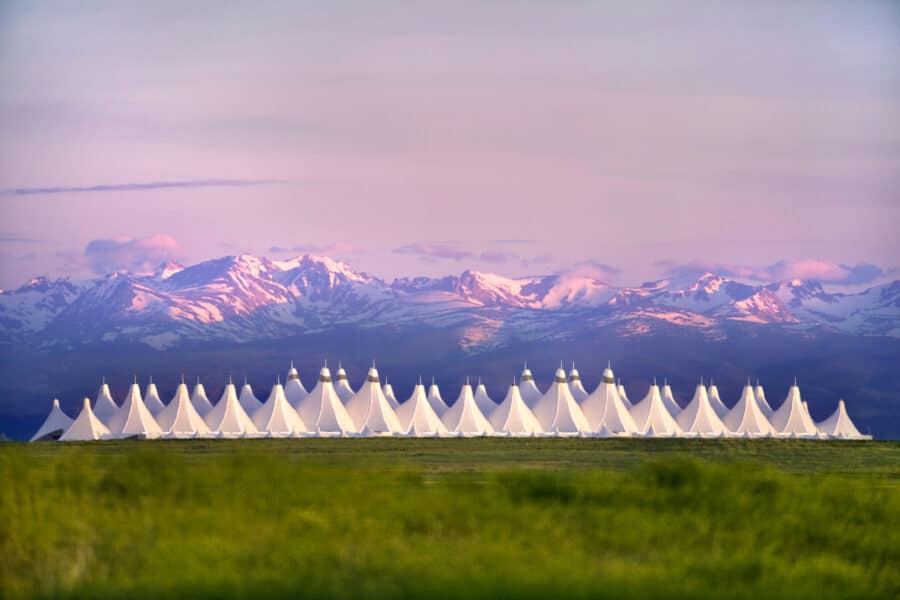
Denver International Airport’s iconic roof is a Teflon-coated fabric, stretched into a fluid and symbolic form that captures the West’s pioneering spirit, culture, and ecology. The translucent roof material reflects up to 90% of solar heat gain while allowing 10% of sunlight to pass through for natural daylighting. Photo by Ellen Jaskol
Of course, not all firms are experienced in aviation design, so the demand for the expert team at Fentress is high. They’ve been designing sustainable airports, starting with the inspiring Denver International Airport (DEN) in 1995, long before sustainability was a buzzword. Fentress became internationally recognized for their work after the DEN project, known for its unique roof and streamlined “curbside to airside” design. DEN is consistently recognized as one for the most sustainable, efficient, and significant airports worldwide. The design set a new standard, from relocation of the building’s mechanical system from the roof to underground and, at the time, innovative automatic bathroom sinks that only ran water when your hands were beneath the faucet.
“At the time we designed the terminal, we took many risks,” Fentress previously said. “A lot of creative decisions we made had not been done before on such a massive scale. To all the young architects, don’t be afraid to push the limits to create great architecture.”
Fentress also designed Incheon International Airport in Seoul, another “world’s best airport” serving millions of international travelers every year, and in 2008 was chosen to modernize the Tom Bradley International Terminal at Los Angeles International Airport (LAX), the fifth busiest airport in the world.
More than 650 million passengers travel through aviation facilities designed by Fentress each year; that’s more than 84 million square feet of projects, from the LEED Gold LAX project to South Terminal C at MCO.
Designed to be Adaptable
Making the most efficient designs is paramount—from getting passengers comfortably through airports to reducing energy bills to being able to upgrade facilities to keep up with technology and other needs with minimal disruption, Fentress says.
Raised access flooring is one solution that helps minimize possible disruption. The relatively new adoption for US airports is used more widely internationally; Fentress was excited when the team behind the Orlando project came on board to use a large amount of raised floor.
We made the entire area where you go through TSA all on raised floor.
“We made the entire area where you go through TSA all on raised floor,” he says. “We had proposed that on many airport projects previously because we saw that changes were in the pipeline for the industry—and many more to come, of course, with advances in technology. They agreed to it in Orlando, and so it was much, much easier to do the first installation.”
With raised access floor, as things need to be altered, it is much easier to make changes, Fentress says, getting beneath the floor to install new technology or wiring systems if needed, for example. “Protocols are going to continue to change in the area of security,” he says, citing a need for raised access flooring.
Raised access floors provide flexibility and adaptability so the airport can evolve with changing needs by allowing point-of-service terminals and kiosks to be added or moved anywhere on the floor plate without core drilling or trenching the building slab.
The Evolution of Raised Floor
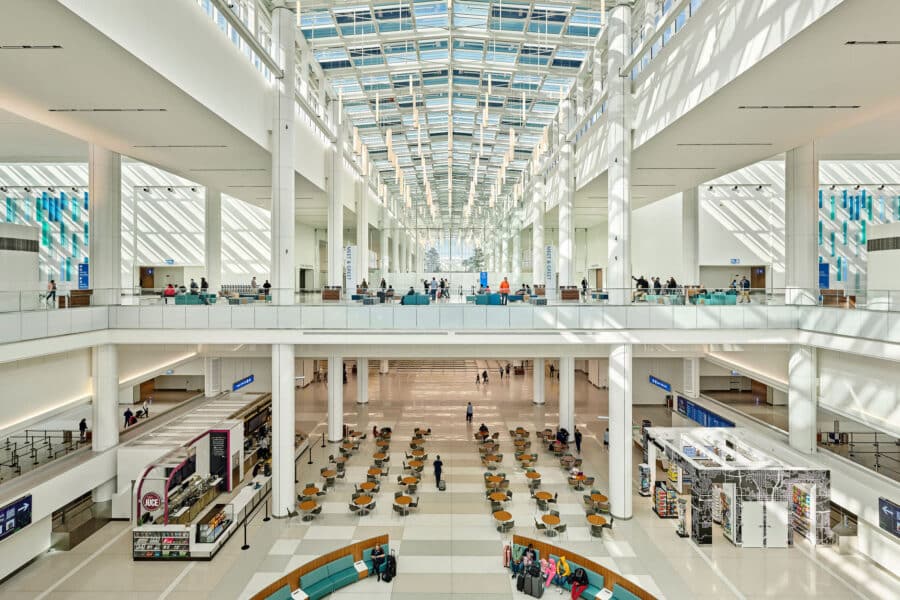
The Boulevard at Orlando International Airport Terminal C is characterized by its continuous skylight of varying blue frits that expresses the design themes of sky, water, and flora. This project also included a large application of raised access flooring to help with any future needs for the airport to adapt. Photo by Michael Robinson
Raised flooring began showing up in airport security areas about 10 years ago, according to Mark Johnson, commercial sales director at Tate Access Floors, but he’s seen an increase in demand as of late. The Orlando Terminal C is the biggest airport application Tate has completed as of 2024.
“It provides you a lot more flexibility to move your services and, specific to airports, the power and data that are sitting under a raised floor. I think Orlando was a six-inch high raised floor, which leads to about a four-and-a-half-inch space under the raised floor to run power and data.”
That area of raised access floor then extends over to an electrical closet with electrical panels. The Orlando airport project includes raised access floor from the checkpoints to ticketing kiosk areas, with power and data coming from beneath the floor. Johnson says the project covered about 80,000 square feet.
The decision to use raised flooring needs to happen early in the design process because it affects the structure of the building and a lot of other decisions, Johnson says. “In terms of the installation, raised floor makes all of the other components easier to install. It accelerates the construction, shortens the construction schedule, and allows people to move in quicker.”
Walking into the new MCO terminal, you’d likely not realize you’re standing on raised flooring. While the access flooring of years past—often in data centers—was lightweight and may have felt creaky, the flooring in airport projects like these is far superior, Johnson says. With a terrazzo finish on the raised floor panel, what’s under your feet in Orlando looks like a beautiful new terrazzo-style floor.
“When we installed the raised floor we installed the terrazzo finish at the same time. That’s huge because doing poured in place terrazzo takes weeks,” Johnson says. “We offer a lot of high-end finishes with the raised floor. And when it comes pre-finished, it’s a lower cost than doing that same finish in the field.”
The biggest benefit, though, continues to be that flexibility—being able to get back into a project and run different technology or make changes if needed. Without raised flooring, teams would have to take all of that power and data from its central location and run it horizontally in the ceilings below the floor above.
“Then wherever you need it up above you core drill the slab; it could be 8 inches of concrete and terrazzo finish; you pull your power data up, you put the electrical device that you plug into right there, and you stick a kiosk over it. You keep drilling holes and obviously that’s very expensive. It’s very disruptive. It’s not fast, as compared to if the power and data is under a raised floor,” Johnson says.
With raised floor you simply pick up a panel, pull cable, plug in, and put the panel back. “You can move them around. It’s way less cost of change, and, because nobody knows exactly what the future is going to call for, you’re future-proofing that design.”
Other Airport Changes
Johnson says Tate is starting to see more raised floor at airport gates, too—another area dominated by technology as people scan their tickets and board planes. He’s also heard talk of a future in which passengers go directly from their parking spot to their gate.
“At some point in time we’re going to pull into the parking garage, walk right through the airport and onto the plane,” he says. “All that technology that continues to evolve needs to be easily adapted and updated and changed, and that ties back to raised floor.”
Internationally Tate has seen raised floors incorporated across whole airports, in part because, even if there isn’t a lot of technology under the floor, tenants still come and go across food, beverage, retail, and more. “It needs to be flexible and adaptable.”
More airports are rethinking how they entertain passengers while also generating revenue, too. “Airports are now being designed or renovated to have added food, beverage, and shopping everywhere,” Johnson says.
Abundant seating at the gate is largely being removed to encourage people to shop and dine instead. “They want you to sit across the hallway at the bar, the restaurant, or shopping. You are within eyesight of where you need to be to get on the plane, but you’re spending money.”
Giving Airports a Sense of Place
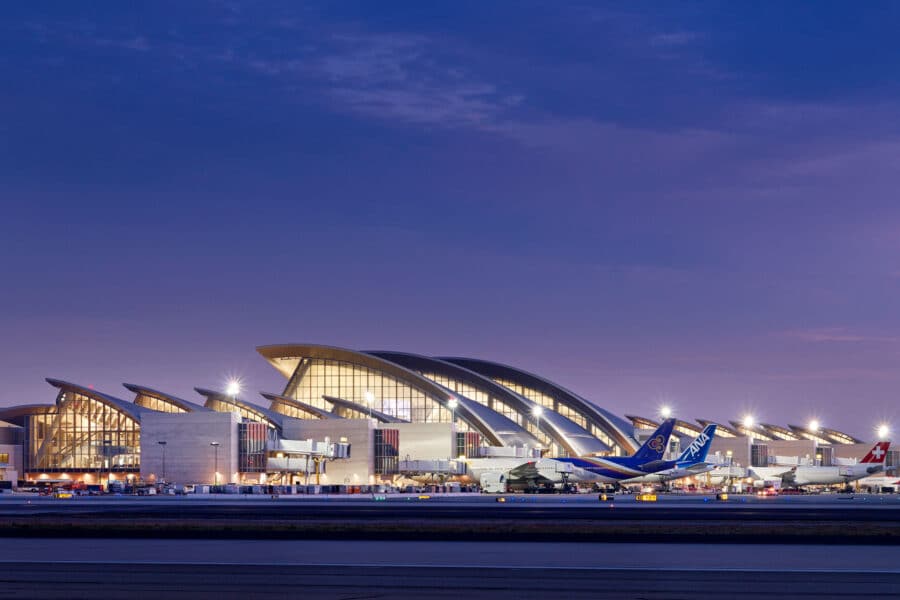
“It’s a really exciting structure that won a lot of architectural awards,” Curtis Fentress says of the Fentress Architects–designed LAX project. “It was the largest LEED Gold building at that time in the aviation industry throughout the world.” Photo by Nick Merrick, Hall+Merrick+McCaugherty Photographers
Beyond being able to quickly make changes, Fentress designs airports to feel their place. In Orlando, for example, you can feel a buzz of excitement as many people are on their way to or from vacation. Palm Court, located airside, was designed as a vibrant location with ample opportunity to shop, dine, or socialize in bright, garden-like settings.
Of course, light looks different in various places, whether you’re in Seattle or Orlando, for example, and it continues to be a top consideration in Fentress designs. “We try to capture that as well and use it to our advantage in terms of making these buildings special. It’s part of our craft as architects,” Fentress says. “We build lots of scale models and test how the light is coming in and try to make it a unique place.”
More Sustainable Successes
In Orlando Fentress designed a large, light-filled boulevard that goes from the train station all the way into the building, the ticketing hall, the security checkpoint, and onward into a large dining and shopping concourse.
“Airports are trying to find every way possible to conserve energy and to bring daylighting into the building if possible. We’ve been using daylight to guide people through the building since DEN in 1995. South Terminal C in Orlando is a recent example,” Fentress says.
He likes to ask teams, “How can you think smarter?” How can you recycle air, for instance? How can you use high-speed, low-volume fans? How can you recycle waste?
“Recycling waste is something we do in all of our buildings—certainly during construction but also within the building. About 90% of the construction waste was recycled for Orlando’s South Terminal C.” The team also strives to pick materials that are low in carbon.
Designing buildings to have more efficient mechanical and electrical systems continues to be key. The Fentress team set out to reduce their energy cost by at least 29% in Orlando. “Reducing the amount of electricity helps with that, and the glass we used in the building is more performance-related; it cuts the rays of the sun coming in. Then we had about a 45% reduction in the energy cost for water. These things are a crucial part of the design.”