Story at a glance:
-
- Green concrete uses waste and recycled materials as ingredients.
- Green concrete is more cost-efficient and energy-efficient than normal concrete.
- Manufacturers are developing systems and technologies to manage green concrete.
Concrete has been used in construction for centuries and is still widely used to this day. But with growing concerns about the environmental impact of concrete, it is important to find a more sustainable alternative to projects that use concrete. The answer to this was the development of green concrete.
But what exactly is so special about green concrete? Here are some important details to know about this material.
Uses recycled materials
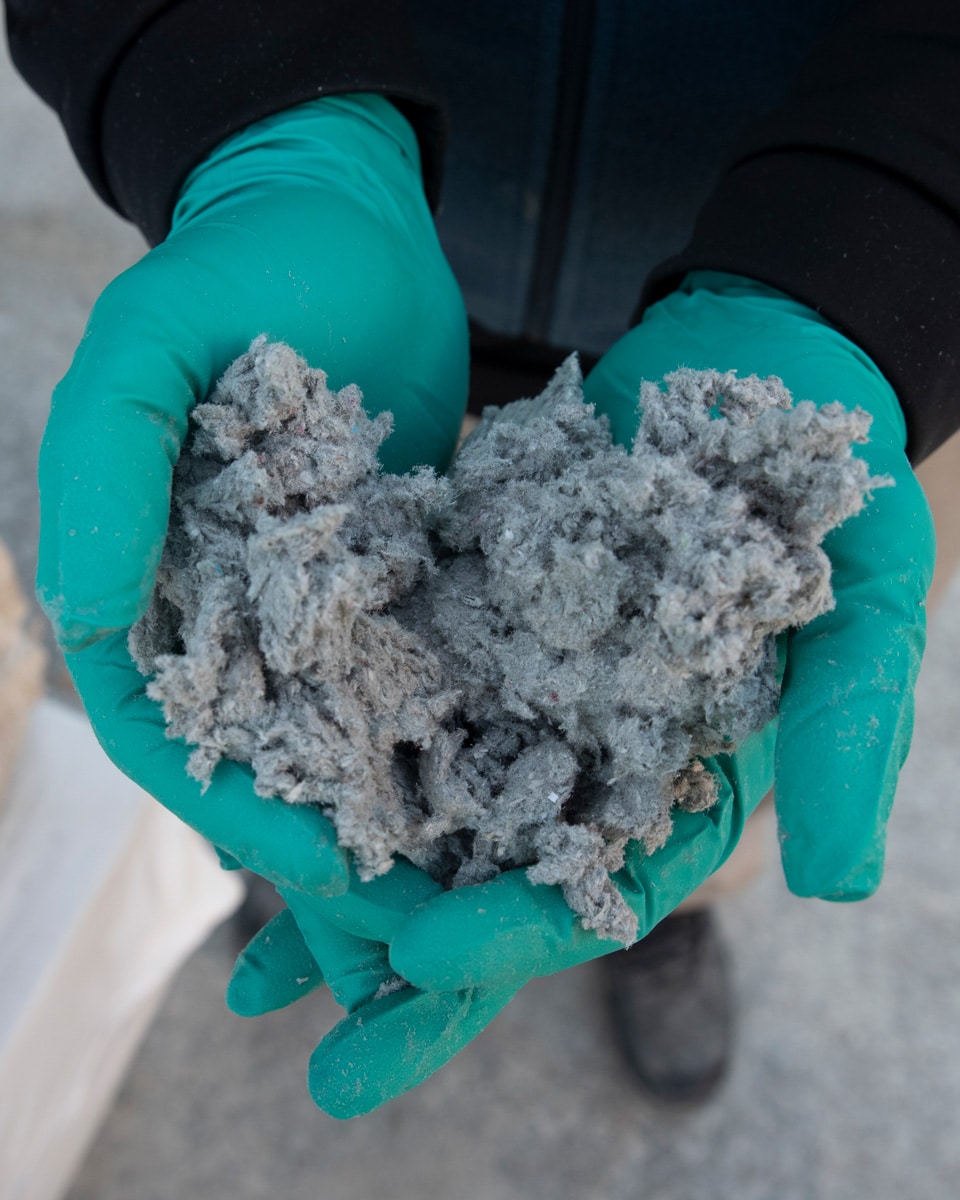
Photo courtesy of GCP Applied Technologies
The ingredients for making green concrete mainly consist of recycled waste materials. According to an article from Madhav University in India, this waste can include blast furnace slag, recycled glass aggregate, and fly ash produced in the making of normal concrete as well as construction and mining.
Another material that can be used to produce green concrete is actually unused concrete. This concrete is broken up into a hardened granular state and reused in later batches as a partial replacement for fine and coarse aggregate. Geneva Rock Products recycles 1 million tons in materials such as asphalt and concrete every year for its own concrete.
Requires less energy to produce
Making normal concrete requires breaking down the materials before heating them up, which can use up more energy. Green concrete’s recycled waste materials are already broken down, either during the process or naturally, which consumes less energy and fossil fuels. Geneva Rock Products uses highly fractured quartzite pre-fractured from seismic activity, broken-down sand, and gravel in the concrete it produces.
Reduces the amount of waste
The process of making green concrete includes using waste materials from other processes. Some ingredients include material that may seem insufficient or unusable in making normal concrete.
GCP has developed products to mitigate the amount of resources wasted in making green concrete. CLARENA® is a chemical additive designed to reduce the amount of wasted aggregate by mitigating the negative effects of clay, while their ADVA® water-reducing admixture technology aims to reduce the amount of water used in the making of concrete by up to 35% while maintaining its workability.
Reduces carbon dioxide emissions
According to an article from Madhav University, the process of heating up limestone, clay, and sand is responsible for between 5% and 8% of worldwide carbon emissions. Alternatively, development of green concrete releases up to 80% fewer carbon dioxide emissions.
Companies are developing new systems
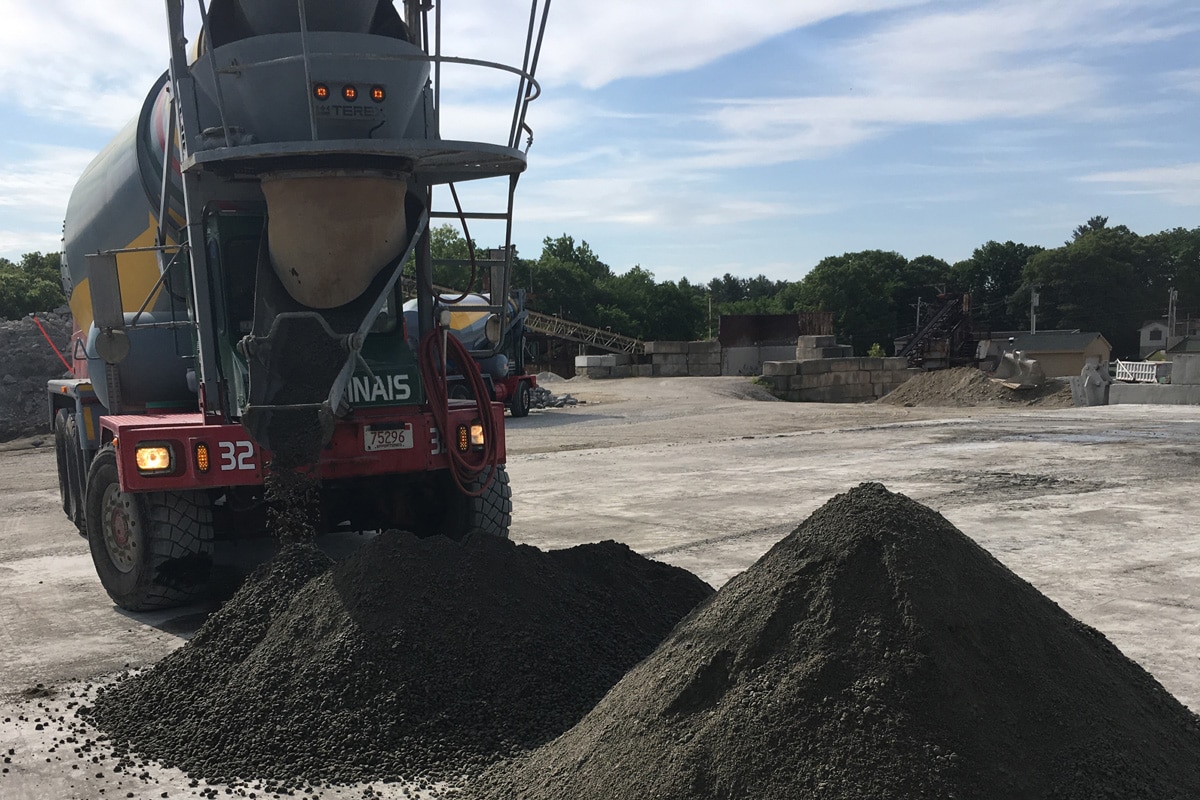
Photo courtesy of GCP Applied Technologies
The development of green concrete is inspiring companies and manufacturers to develop new systems for producing and managing green concrete.
Geneva Rock Products has implemented a unique energy-generating downhill overland conveyor system in their Point of the Mountain site in Utah that is powered solely by gravity and the weight of the rocks it carries. This system of transporting rocks also serves to generate electricity to be used for the plant’s electrical network.
GCP developed the VERIFI system to monitor, measure, and manage each batch of concrete that uses their CLARENA aggregate in real time from their ready mix truck. This allows concrete producers to deliver more consistent concrete quality to the jobsite using less energy and cement.
Less expensive to produce
The ingredients for green concrete are usually waste produced in the making of normal concrete. These materials are comparatively less expensive than the materials for normal concrete. The manufacturing process also uses less fossil fuels, which tends to bring costs down.