Story at a glance:
- The mass production of conventional textiles has numerous negative environmental consequences.
- All fabrics generally fall into three categories: naturally derived, semi-synthetic, and synthetic.
- Industry leaders are pioneering sustainable textile products using recyclable materials.
Fast fashion continues to have harmful effects on the planetāand textiles can be part of the problem or the solution. The textile industry generates one-fifth of the world’s industrial water pollution, and textile dyeing is the second largest water polluter in the world. Chemical pesticides involved in cotton farming and the petroleum required to create synthetic fabrics are just the tip of the proverbial iceberg.
The United Nations estimates that by 2050 the population will increase to 9.6 billion. That means that we could require almost three planets worth of finite natural resources to sustain our current rate of consumption. With the increase in population the built industry will be forced to accommodate eco-friendly alternatives based on the inevitable environmental limitations.
Sustainable fabrics are on the rise in an attempt to reverse the negative environmental effects associated with the textile industry. To help make more environmentally friendly choices on your next project, reference this guide to sustainable fabrics.
Why Textiles Typically Arenāt Green
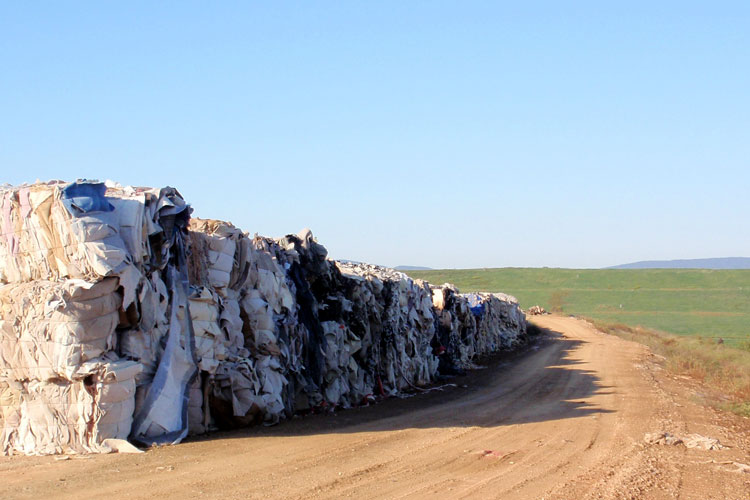
Carpet waste in a landfill. Photo courtesy of Aquafil
Often textiles aren’t sustainable in part due to a global model of mass production that supports a culture of consumption. Conventional textile production is reliant on the unregulated use of pesticides, toxic fertilizers, overuse of water, coal, and petroleum.Ā
For example, cotton, a natural fabric, and polyester, a synthetic one, are not significantly different in their environmental impacts. Conventional cotton depletes land biodiversity, uses mind-blowing amounts of water, and is one of the most chemically intensive crops in the world. In fact, seven out of the 15 most commonly used pesticides in the production of cotton are listed as āpossible,ā ālikely,ā āprobable,ā or āknownā human carcinogens by the EPA.
Polyester, on the other hand, is the most popular synthetic fabric and is derived from a chemical process involving coal, petroleum, air, and water. While polyester does not use as much water as cotton does, the carbon emissions and energy needed to produce it make it a very high-impact textile. In 2015 polyester produced for clothing emitted 620 billion pounds of CO2ānearly three times more than that of cotton.
Illustrative of all conventional textiles, both fabrics are produced in factories on a mass scale, undergoing chemical processes involving detergents, bleaches, and chemical softeners. Additionally, if factories producing these textiles do not have wastewater treatment systems, potentially toxic chemicals like antimony, cobalt, manganese salts, sodium bromide, and titanium dioxide go straight into the environment affecting waterways and aquatic life.
What Makes for Sustainable Fabrics
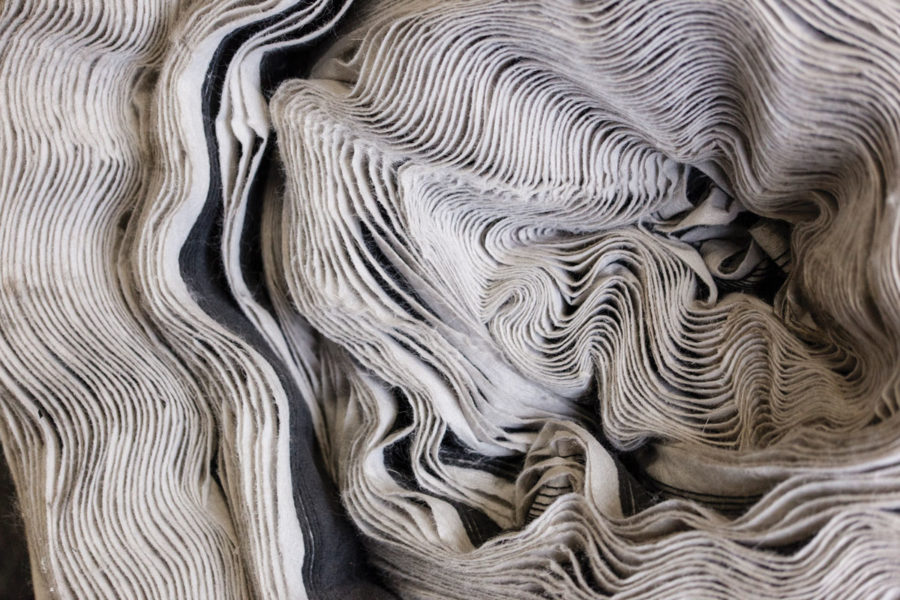
Aquafil’s ECONYL is a type of regenerated nylon made from recycled plastic. Photo courtesy of Aquafil
Given the range of materials used in textile manufacturing, some fare better in the way of pollution than others. Conventional cotton and polyester are at the worse end of the spectrum for their significant carbon footprint and water consumption. Materials like linen, hemp, and organic cotton are innately more sustainable due to the reduced water and pesticides needed to produce them.
What is tricky about sustainable textiles are the trade-offs. For example, organic cotton is not genetically modified nor does it use pesticides the way conventional cotton does. However, with organic cotton, there can be up to 25% lower yields. This suggests that to produce the same amount of cotton as a conventional plant, more cotton plants need to be tendered. Thus organic cotton farmers require more land and more water but save on the chemical processes.
Ideally textiles of all kinds can become more sustainable through conscious consumer and manufacturer actions. By implementing slower production schedules and designing small-batch collections, textiles can be created more sustainably.
The reality is that every ton of reused discarded textiles prevents 20 tons of CO2 from entering the atmosphere. From a consumerās point of view, choosing to purchase used, upcycled, or recycled fabric extends its lifetime and reduces its carbon footprint.
Types of Sustainable Fabrics
Natural, semi-synthetic, and even synthetic fabrics can sustainably be used in shade structures, carpets, wallcoverings, and more.
Naturally Derived Fabrics
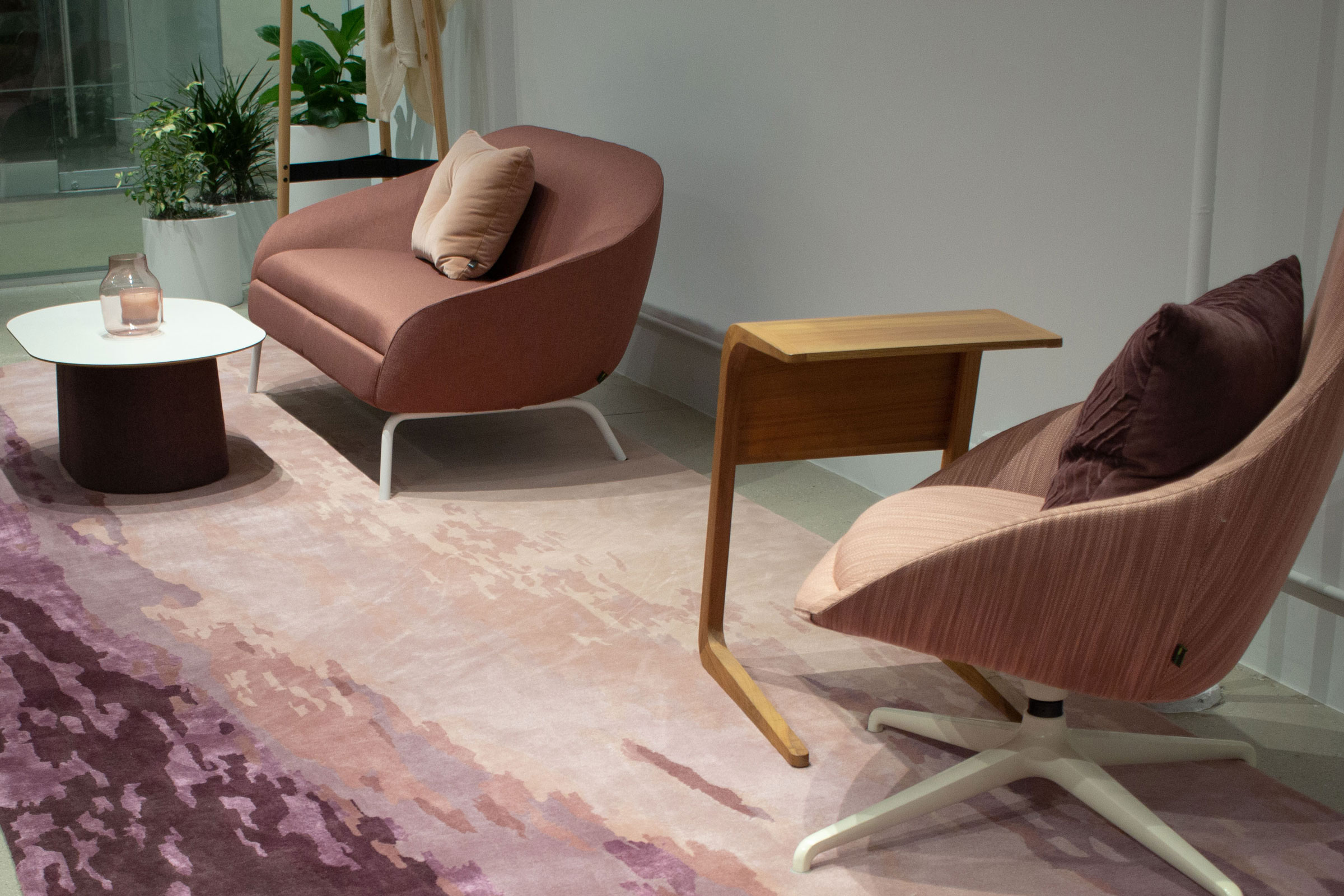
Prima Vista by Bentley offers customizable wool area rugs. Photo courtesy of Bentley Mills
Natural textiles are made from plant and animal sources such as bamboo, wool, hemp, linen, and silk. These types of fabrics predate man-made synthetics. Natural fabrics are inherently biodegradable and can be sourced sustainably but are dependent on the manufacturersā individual processes.
Organic Cotton
As stated above, organic cotton is much more sustainable than conventionally-grown cottonābut not all organic cotton is the same. Because the term āorganicā is legally controlled, farms must be certified to their relevant government-controlled standard, all of which have their own slight differences in required agricultural practices.
Most of these standards require that farms grow their cotton from non-genetically modified plants and without persistent and synthetic agricultural chemicals (e.g. pesticides and fertilizers), helping to prevent soil, water, and air pollution.
When choosing organic cotton fabrics, look for those brands that use tools like the Textile Exchange’s Organic Content Standard or the Global Organic Textile Standard to trace and verify that their products contain the accurate amount of organically grown cotton.
Wool
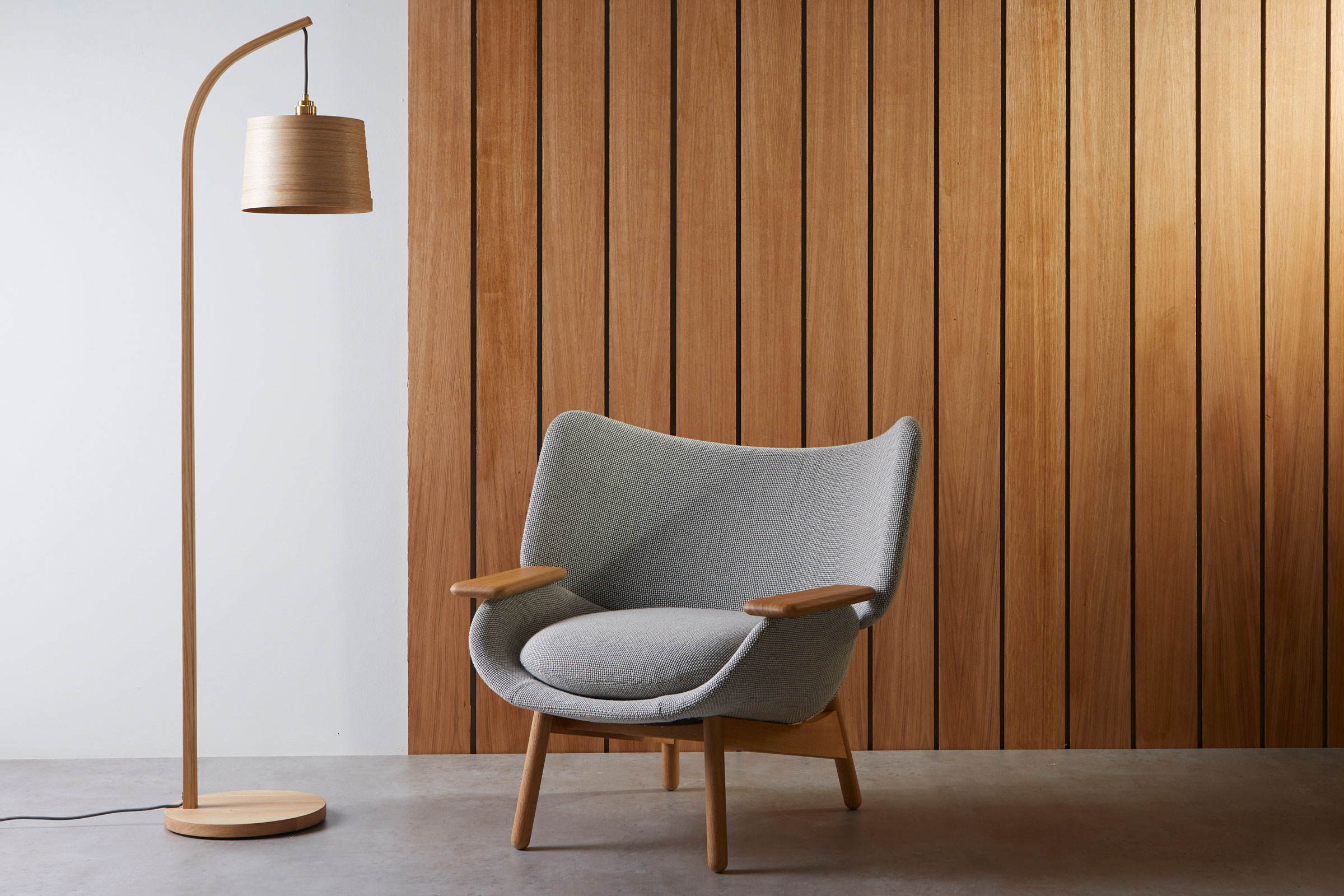
Crafted from a blend of wool and flax, the new Craggan Flax fabric retains the raw appeal of its natural composition while maintaining its contemporary aesthetic of a chunky weave. Photo courtesy of Camira
Wool is a natural animal byproduct that is constantly regenerated throughout a sheepās lifespan, thus making it a renewable resource. From a sustainability standpoint, wool fabric is considered to be low-carbon, as carbon makes up a significant amount of woolās molecular structure (50%) thanks to sheep’s diet of grasses, legumes, and forbs. Like all ruminants, however, sheep do contribute to methane emissions.
After it is shorn, wool is soaked, scoured, and dried before being combed and carded. Combing refers to the process of sorting the wool into long and short fibers whereas carding describes the process of detangling and aligning the fibers, after which point the wool is peeled off as a roll or rolag. These long-fiber rolags are spun together into a continuous thread to create woolen yarn.
This yarn is then woven by hand or using a machine to create wool products like carpets or garments. Because wool is a natural material, wool fabric is biodegradable and will eventually break down into essential nutrients once it has outlived its operational lifespan.
Camira, known for its low-impact textiles, has created a natural fabric made from wool and flax called Craggan Flax. Its chunky weave gives the fabric a unique textured quality and has earned the Queenās Award for Sustainable Development. Along with its numerous bright and neutral colorways, this is a sustainable option suited for task and lounge seating as well as panel construction.
Hemp
Hemp is an incredibly fast-growing plant that goes from seed to harvest in just 70 to 140 days. It is considered to be much more sustainable than cotton in that it uses up to 75% less water, requires fewer pesticides, and possesses a higher versatile utility value, as almost the entire plant can be used in manufacturing textiles. Thanks to its deep, complex root systems, hemp also acts as a form of erosion control and ultimately improves soil health by cycling nutrients and aerating the soil.
Hemp that is destined for fabric is harvested with a specialized machine, cut, baled, and then allowed to rett in a field for four to six weeks. This period of exposure causes the pectin in the plant to decay, which in turn loosens the stemās soft bast fibers from its non-fibrous woody core. After retting, the dried hemp fibers are separated from their cores using a decorticator and scutched or beaten to remove any remaining woody plinths.
Similar to wool, these fibers are then carded and combed to separate the line fibersāor the long, straight, and strong fibersāfrom the short, weak, and/or bent tow fibers, both of which have their own uses. At this point the fibers are ready for spinning, with wet spinning being the preferred method for producing finer, softer yarns from the line fibers and dry spinning the traditional method for producing coarser yarns from the tow fibers.
This hemp yarn is then woven, either by hand or by machine, into hemp fabric. Hemp fabric is commonly used in the garment industry but can also be used to fashion rugs, upholstery, bags and totes, bedsheets, blankets, towels, and a range of other household textiles.
Flax (Linen)
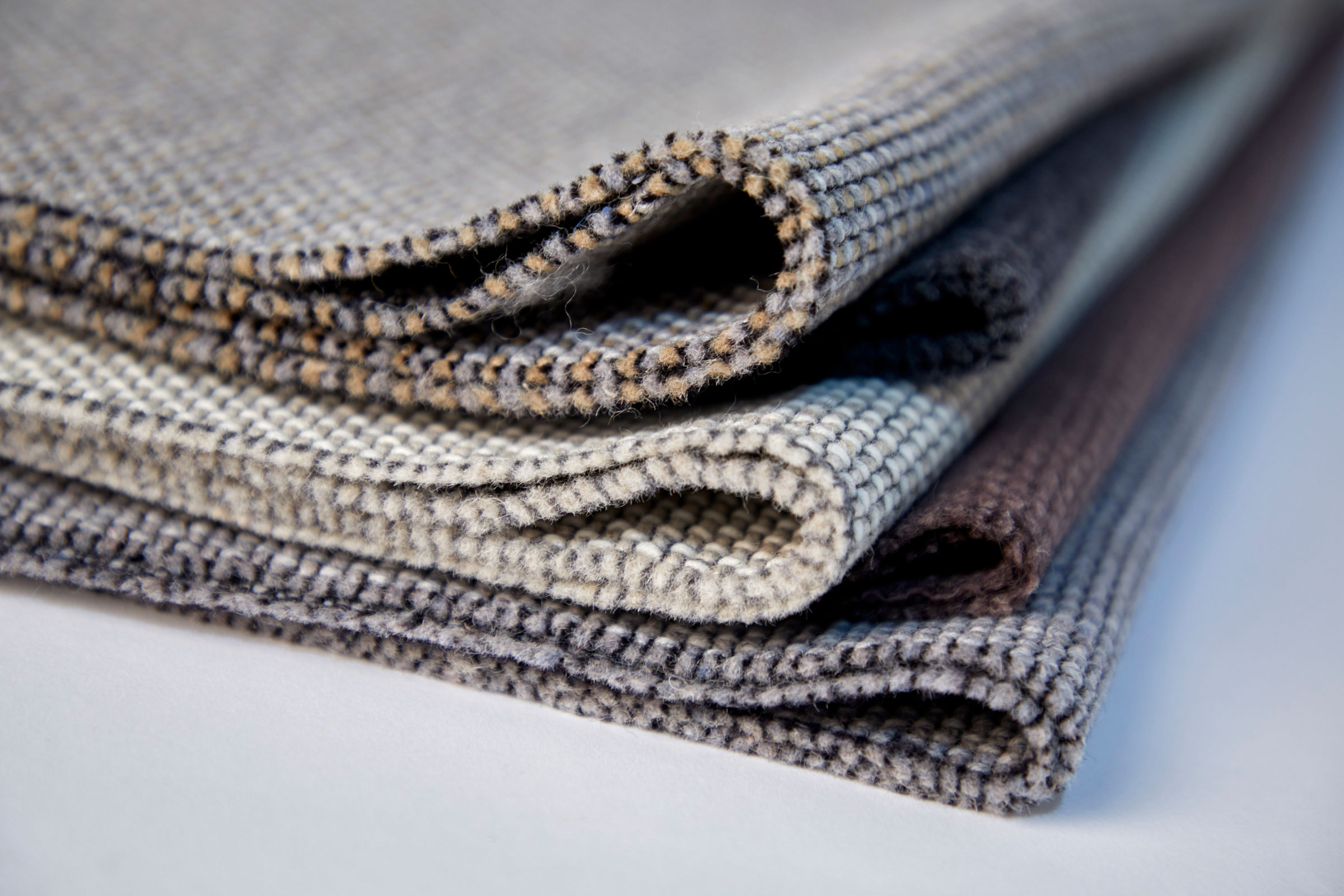
Camira’s Craggan Flax fabric blends the best qualities of flax and wool. Courtesy of Camira
Linen is a natural and biodegradable fabric made from flax, another fast-growing crop that requires fewāif anyāchemical fertilizers or pesticides, making it incredibly easy to cultivate using organic methods.
The process for creating linen from flax is quite similar to that of creating hemp fabricābut rather than use the stalkās outer fibers, it is the plantās inner fibers that are separated out, combed, shortened, and prepared for spinning. Once spun, linen thread may be woven into linen fabric.
As a fabric linen is highly absorbent, stronger when wet, and softens the more it is worn and washed. Its sturdiness also makes linen an ideal choice for upholstery or industrial uses. Because of the laborious nature of producing linen yarn, however, linen products may be more expensive than others.
Semi-Synthetic Fabrics
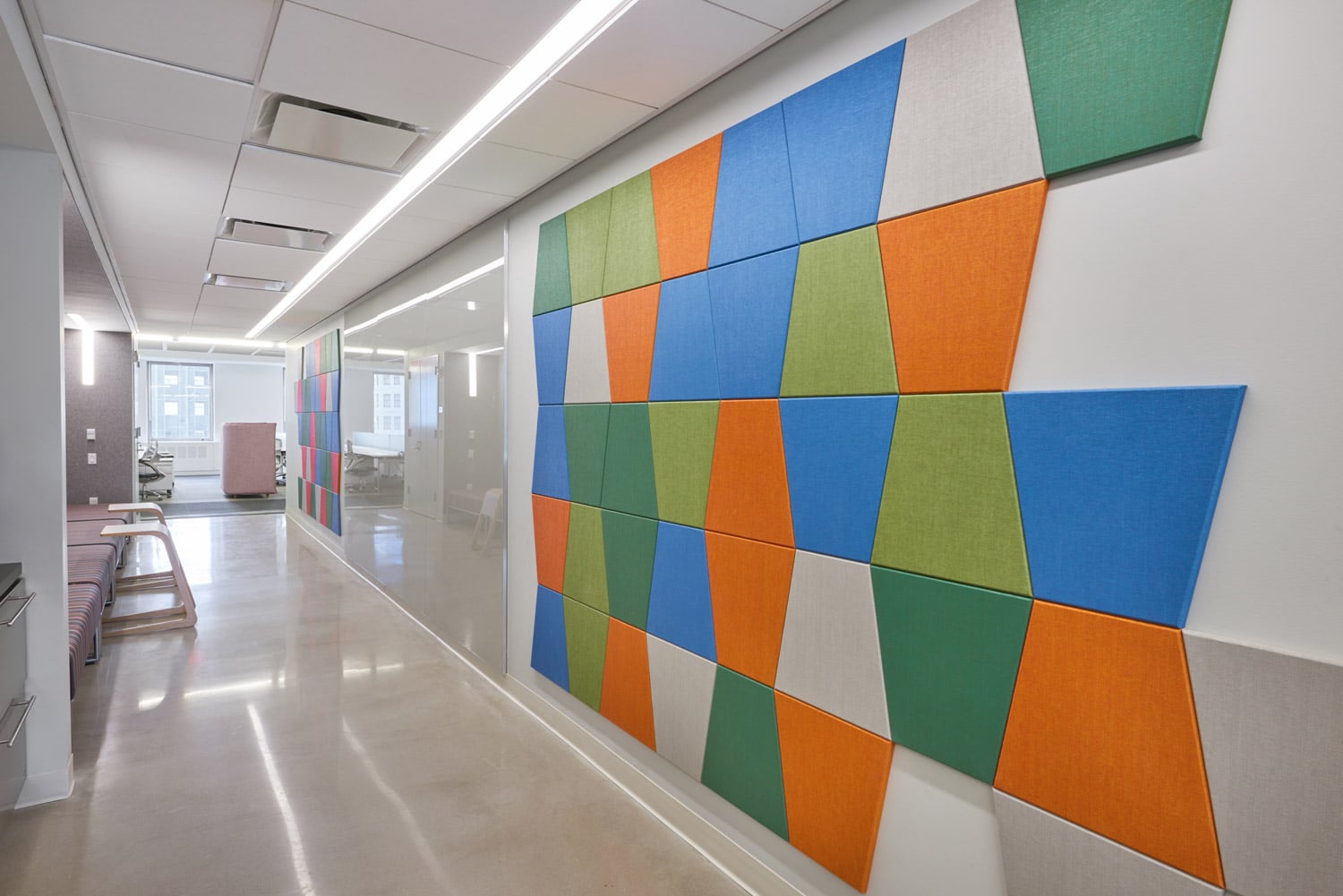
Carnegie’s Biobased Xorel is a semi-synthetic fabric made in part from sugarcane. Photo courtesy of Carnegie
Semi-synthetic fabrics are made in part from naturally occurring fibersāsuch as tree pulp or bamboo grassāthat are broken down by a chemical reaction of acid and alcohol and eventually spun into yarn. Some semi-synthetic fabrics were created to mimic silk or to reduce costs inherent to higher quality textiles. Semi-synthetics are considered beneficial due to their stain resistance, technical performance, waterproofing, and their cheaper price point.
Unfortunately the treatment processes that go into making many semi-synthetic fabrics typically involve toxic chemicals like ammonia, formaldehyde, and sulphuric acid. These chemicals can leave residues that linger on the textiles post-production and cause adverse health effects such as skin irritation, nausea, headaches, or chronic respiratory infections.
Some of the most common examples of semi-synthetic fabrics include rayon and cupro, both of which are often touted as being relatively sustainable, but in reality are detrimental to both human and environmental health. There are, however, a few lesser-known types of semi-synthetic fabric that do have fairly eco-conscious manufacturing processes.
Bamboo
While it may not go from seed-to-harvest as quickly as hemp, sugarcane, or even cotton, bamboo does not require the whole plant be cut down for harvesting; indeed, the same bamboo culm can be harvested every three to five years as individual shoots reach maturity. When cultivated using traditional methods bamboo requires very little supplemental watering or fertilizing and does not require the spraying of pesticides for successful growthābut like many natural fiber fabrics, there are both sustainable and unsustainable methods of making fabric from bamboo.
The widely-used viscose method involves extracting the cellulose from bamboo using chemical solvents, compressing said cellulose, and then exposing it to carbon disulfide. The cellulose is then filtered and pushed through a spinneret to create strands; these strands are soaked in a vat of sulfuric acid to form filaments, which are then spun into yarn. The resulting fabric is typically not sustainable, as its manufacturing produces considerable waste and utilizes chemicals that are known to have a negative impact on human health and the environment.
There are, however, other methods for manufacturing bamboo fabric that do not chemically alter or extract the plantās cellulose. These methods involve soaking crushed bamboo fibers in a natural enzyme solution and then mechanically combing out the strands, at which point they may be spun into yarn. Bamboo fabric produced in this manner is environmentally friendly, durable, breathable, and can be used in everything from clothes to towels, sheets, and other household textilesābut because the process is extremely labor intensive, it’s also much more expensive.
Biobased Xorel
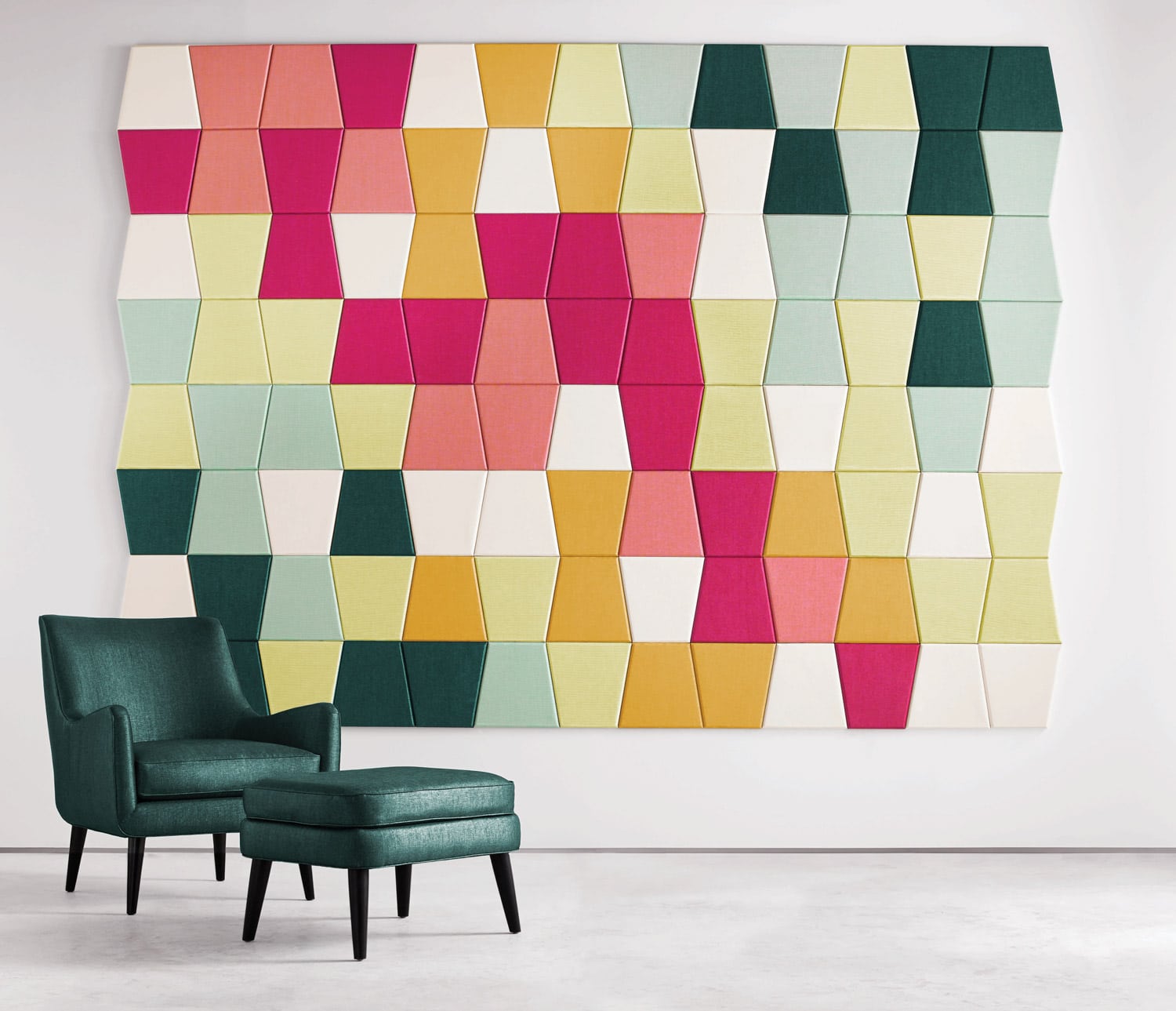
Biobased Xorel is a semi-synthetic sugarcane-based fabric manufactured by Carnegie. The fabric is both Cradle to Cradle and Living Product Challenge certified. Photo Courtesy of Carnegie
Another example of semi-synthetic fabric is Carnegieās Biobased Xorel, an alternative to the company’s proprietary fossil-fuel based polyethylene Xorel fabric that is instead derived from rapidly renewable sugarcane. Manufacturing ethylene from sugarcane is estimated to use 60% less energy and produce 40% fewer greenhouse gas emissions than petrochemical ethylene.
Containing anywhere from 60 to 85% biobased content, Carnegieās Biobased Xorel is a durable textile generated without a significant carbon presence, possessing an embodied carbon footprint of only 1.12 kg of CO2 per yard. But thanks to sugarcaneās natural ability to sequester carbon in the soil as it grows, 2.5 tons of carbon is actually removed from the atmosphere for every one ton of raw material produced.
As further testament to its sustainability, Biobased Xorel boasts both Cradle to Cradle Gold and Living Product Challenge certification. Xorel can even help projects earn points towards LEED certification in the Indoor Air Quality, Material Transparency, Rapidly Renewable Content, and Material Optimization categories.
All Biobased Xorel yarn is free of chemical finishes and contains no PVC. This high-tech fabric is inherently non-absorbent, antimicrobial, and extremely durable, making it a great option for acoustic panels, upholstery and upholstered walls, or wallcoverings.
Lyocell
Lyocell is a semi-synthetic fabric derived from regenerated cellulosic fibers that is comparable to silk. Hardwood logs (such as oak or birch) are chipped into small squares and then made into pulp using either the sulfite process or prehydrolysis-kraft process, which in turn removes both the hemicellulose and lignin. The pulp is then bleached, dried, rolled onto spools, and transported to a lyocell mill.
At the mill, rolled spools of pulp are broken up and dissolved in N-methylmorpholine N-oxide, filtered, and pumped into spinnerets to create continuous strands. The fibers are then immersed in a water bath containing diluted amine oxideāwhich helps set the strandsāand washed with demineralized water. The strands are then left to dry.
Once dry, the strands are detangled, crimped, carded, cut, and baled, at which point they are ready for spinning into yarn and woven into textiles. TENCEL is a brand of biobased lyocell fibers owned by the Austrian company Lenzing AG, who have made sustainability an integral part of their operations.
TENCELās Lyocell fiber is manufactured with at least 50% less carbon emissions and water than generic lyocell, is certified as both biodegradable and compostable, and is certified by the EU Ecolabel for environmental excellence. TENCEL uses eucalyptus for their Lyocell fibers and sources all of their wood from controlled or certified wood sources. TENCEL employs a closed-loop process that recycles and recovers 99.6% of the solvent used in producing Lyocell.
Modal
Modal is another semi-synthetic fabric made from wood pulpāspecifically that of beech treesāand is a genericized trademark of Lenzing AG. Modal is a version of viscose rayon, which is traditionally produced by dissolving wood into pulp and treating said pulp in a carbon disulfide solution. The pulp is then forced into a spinneret and converted into long continuous strands, which are then stretched, washed, and cut.
The problem with viscose rayon, however, is that carbon disulfide is highly toxic and can cause serious harm to workers and the environment. TENCELās version of viscose rayonāModalāon the other hand, is produced using a much more sustainable method that recovers a majority of all process ingredients from waste gas streams so that they may be reused.
Once spun into yarn and woven into fabric, TENCEL Modal is lighter, softer, and more breathable than lyocell, making it ideal for clothes and undergarments. Modal also has a higher capacity for water absorption, meaning it will stretch rather than shrink over time.
Synthetic Fabrics
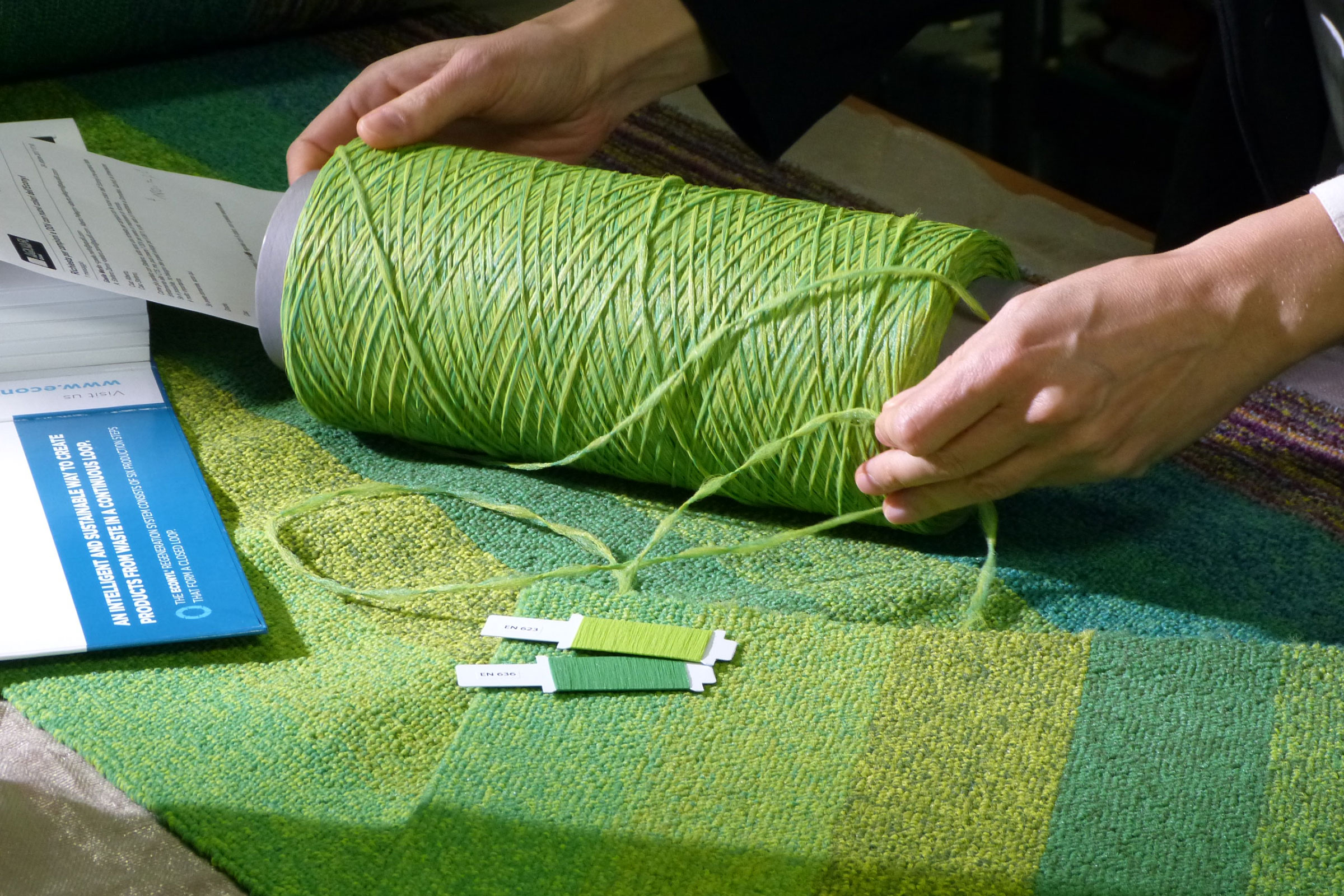
With ECONYL nylon designers are empowered to create new collections and styles over and over again without using new resources. Photo courtesy of Aquafil
Synthetic fabrics like polyester, nylon, and acrylic are textiles created from plastic, a fundamentally finite resource produced using crude oil. As with anything, there are positives and negatives to these man-made fabrics. Namely, they can be advantageous in that theyāre often more durable and accessible than natural fibers.
Part of the debate between natural and synthetic fabrics is their usage. Synthetic fabrics are generally better for technical use and have a wide range of applications. Some companies are disrupting the industry by creating fabrics that are both synthetic and sustainable by incorporating recycled plastic products in their designs.
ECONYL
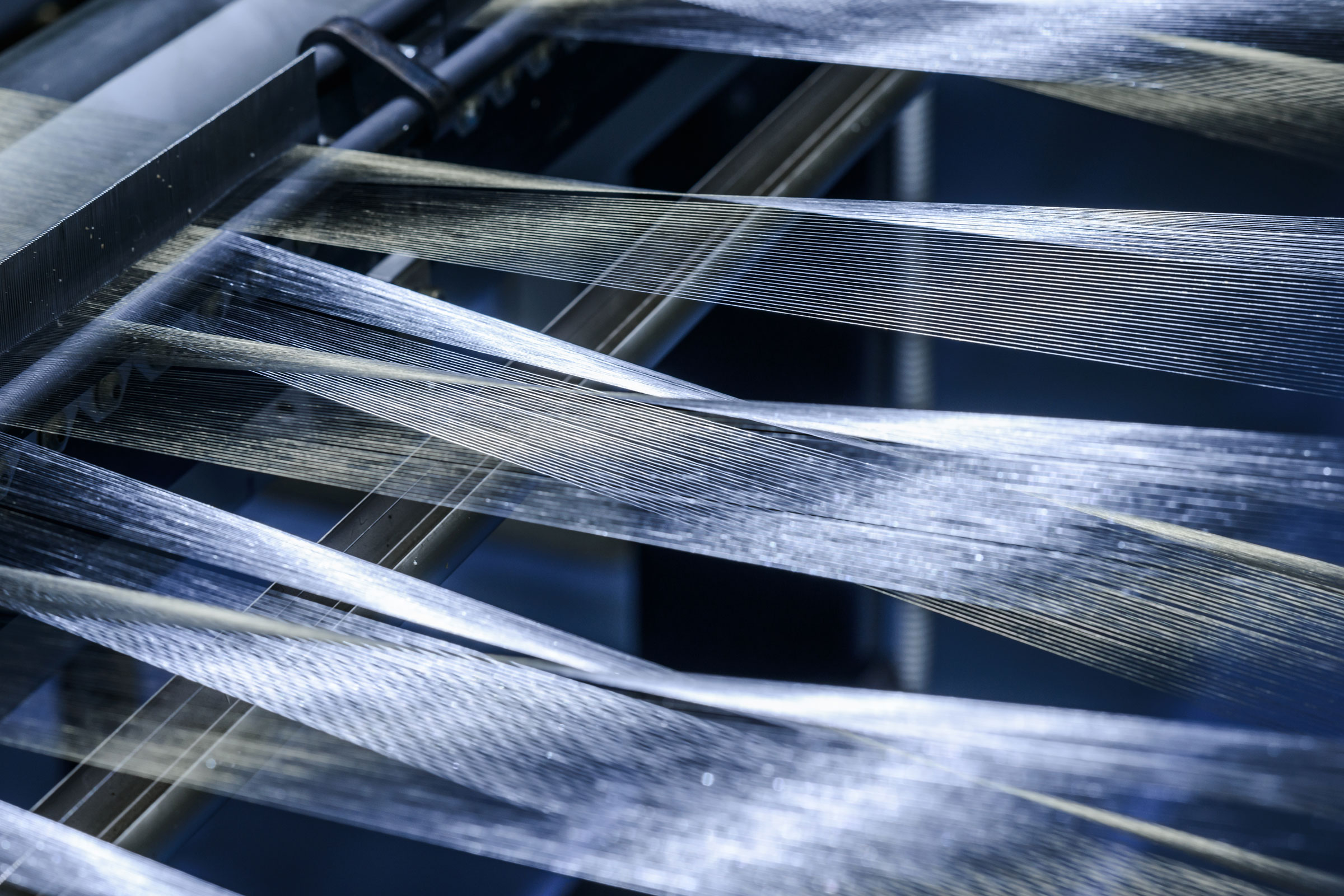
ECONYL regenerated nylon is being spun into spools. Photo by Peter Skrlep
One such fabric is ECONYL, a regenerated nylon fiber created by industry leader Aquafil and made from plastic waste derived from materials like reclaimed carpets and fishing nets.
āECONYL is made from 100% waste instead of oil. For every 10,000 tons of ECONYL raw material, 70,000 barrels of crude oil are saved, and 65,1000 tons of CO2 equivalent emissions are avoided. Using ECONYL yarn offers up to 90% reduction in global warming potential compared to nylon from fossil sources,ā Franco Rossi, president of Aquafil USA, previously wrote for gb&d.
Aquafil collects approximately 35 million pounds of carpet each year and deconstructs it to produce yarn and generate new nylon fabrics with the same quality as traditional nylon. ECONYL is infinitely recyclable and does not lose quality after reclamation. This fabric is versatile and particularly well-suited for interior products like rugs and curtains.
Designtex
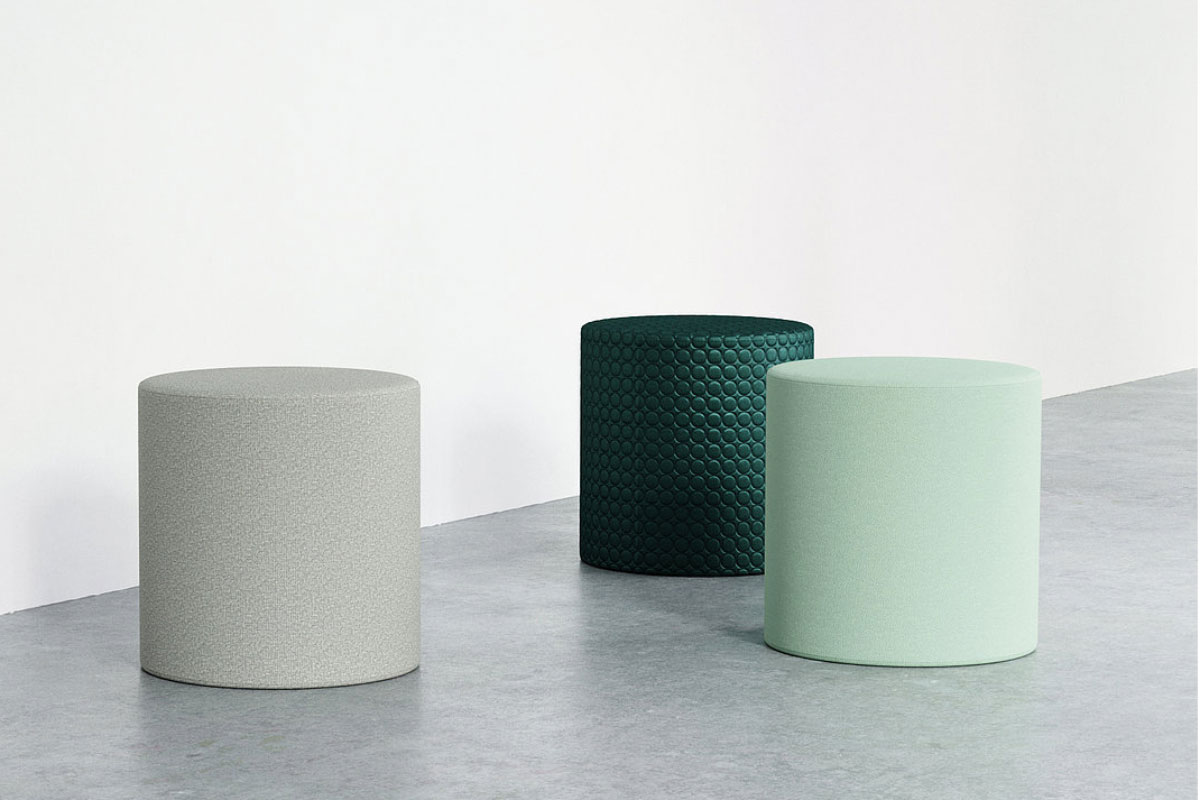
Designtex uses recycled polyester in many of their products, including their Rider, Taylor, and Wend collection. Photo courtesy of Designtex
American design and manufacturing company Designtex also uses recycled polyester in many of their products, including the carbon neutral Rider, Tailor, and Wend collection of high-performing upholstery fabrics. All three textiles meet mindful MATERIALS program criteria and Wend is made from 100% post-consumer recycled plastic water bottles.
The versatility of recycled polyester means that Designtex can offer its sustainable fabrics in 52 colors and several textures. This synthetic fabric achieves the same desired look as virgin polyester but with a sustainable impact.
āDesigntex is committed to improving the material health and transparency of our products,ā Deidre Hoguet, director of applied research at Designtex, previously told gb&d. āWe use our material chemistry knowledge along with sustainability certifications to continually improve our productsā contribution to human and environmental health.ā
Aside from the products themselves, Designtex has also worked to reduce or offset their operational carbon emissions. āThrough Designtexās support of 13 innovative emission reduction projects, the company has balanced its total footprint since 2010 and is keeping more than 27,000 metric tons of CO2 from the global atmosphere, while investing in communities across North America,ā says Hoguet.
Margaux Kelly contributed to this article.