Hardwood flooring adds inviting warmth to any space. If properly specified, installed, and maintained, this beautiful and sustainable flooring material will last for decades. Yet unlike some other building materials, climate is a key consideration for ensuring the floor will remain consistently beautiful.
When considering hardwood flooring for a design project the Form, Fit and Function (FFF) rule serves as a great resource. For example, different wood forms—which include narrow and wider boards and varied wood species—react differently to relative humidity (RH). Considerations for those living on the flooring will determine the best fit—high foot traffic, soggy shoes, the presence of animals and plants, and so on. When a hardwood flooring system is chosen based on proper form and fit, it will function as intended and yield satisfied end users.
Follow these three tips on how to care for hardwood floors to protect the wood flooring system in any space or climate.
1. Understand the environment.
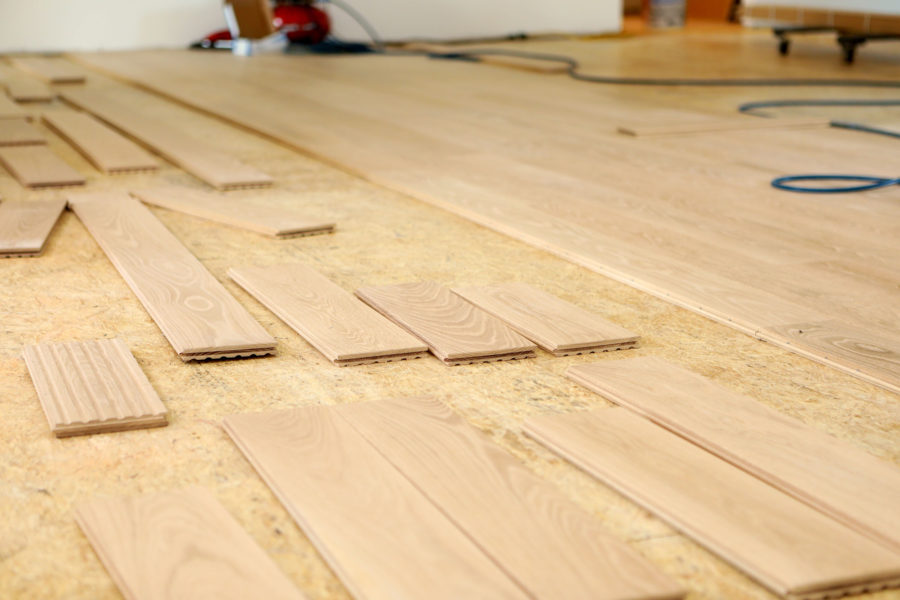
Photo courtesy of Bona
Climate is key to choosing the right wood and wood floor products. Plan accordingly based on the humidity of the region and indoor moisture content, as well as the daily activity and foot traffic the floor will experience. Then build for the type of anticipated environmental conditions that will be encountered and impact the surrounding environment.
Before recommending any hardwood floor, conduct proper research on the climate where the wood will be installed and used, including any regional climate variations that may be present. The regional variability of the exterior climate will affect the indoor conditions of the space.
Hardwood responds differently in humid versus dry climates. Various types of subfloors, adhesives, and sealants are developed to protect flooring in humid and extra dry areas by ensuring the moisture remains at the correct level. When moisture levels or RH dip too low, gapping and “creaking” noises oftentimes occur.
A standard annual range for the best flooring performance is a swing of 20% RH from the most wet to most dry times. Knowing those RH levels for the region is key to choosing the right products for the project, while educating end users on how to maintain those RH levels for the flooring environment is key to long-term performance, look, and functionality of the floor.
The area’s physical climate is also a vital consideration for the flooring type and maintenance. Take into consideration the type and volume of foot traffic walking on the flooring system daily. Are there likely to be wet, muddy shoes walking on the floor? Will children and pets with untrimmed nails be running on the floor? Is the floor in a bathroom where water and steam are prevalent or in a room with no blinds or draperies on harsh, sunny days? All of these factors can lead to increased wear on the floor and potentially create damage or less than ideal results.
2. Use the right products and tools for the job.
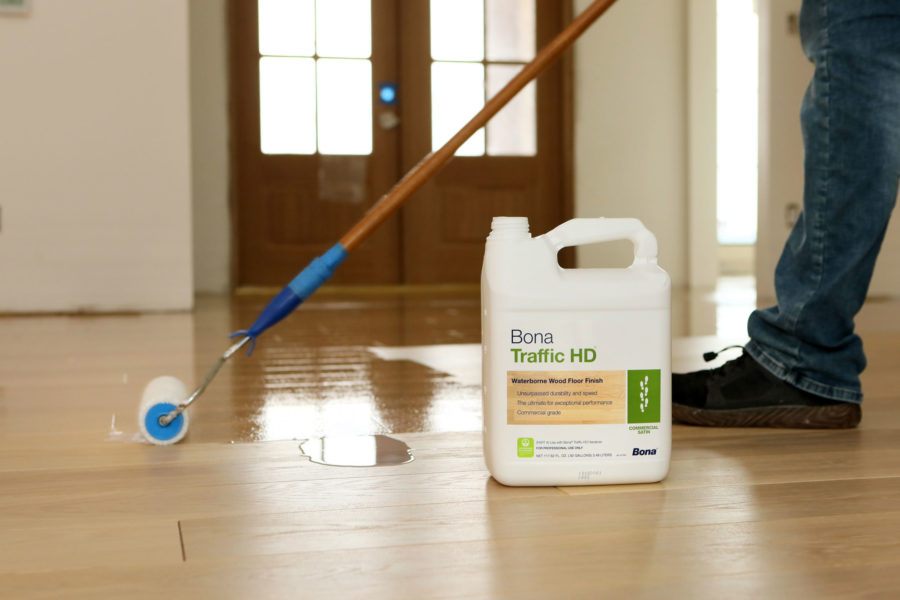
Photo courtesy of Bona
New primers and adhesives allow contractors to install wood floors that were deemed prohibitive years ago due to climate variations or potential moisture issues. These new adhesives in turn have contributed greatly to the increased use of wood flooring in all types of construction and remodeling. The appropriate products make all the difference, so be sure to choose the subfloor, moisture barriers, adhesives, finishing coats and installation team wisely for your wood flooring application.
Moisture barriers help protect against mold, mildew, and other serious issues that can jeopardize the life cycle of a beautiful floor. There are different types of barriers, so be certain the installation team uses the correct product for the specific environment. Consider these factors when choosing the right moisture barrier:
- The geographic location of the home or building (i.e., climates with harsh winters, plentiful rainfall and/or high humidity)
- The grade level (Basements typically contain more water vapor than other areas of the home.)
- Type of subfloor, should you specify a moisture barrier or a vapor retarder to achieve your objective.
Use a moisture barrier or primer that is trusted and tested to properly mitigate vapor transmission on absorbent and non-absorbent subfloors, including Gypsum-based underlayment.
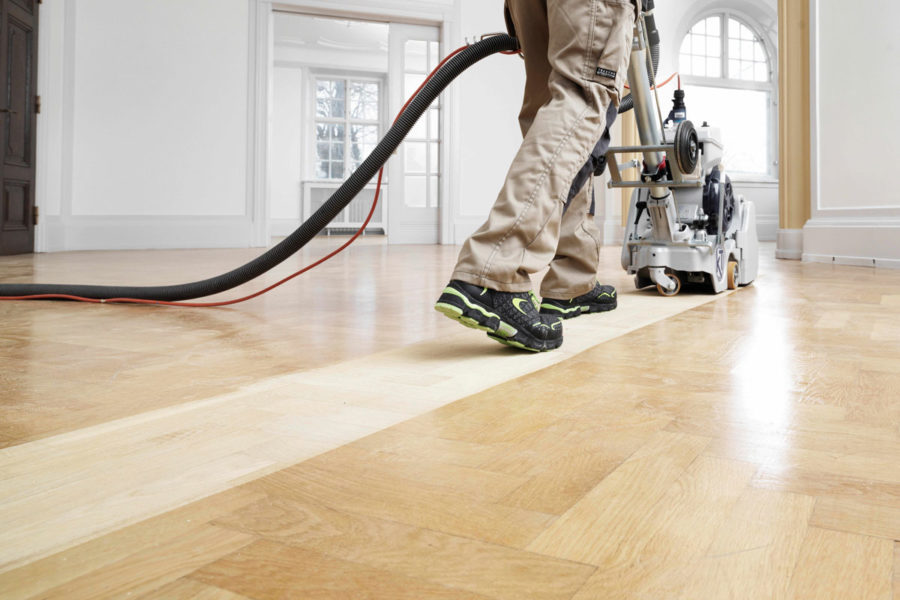
Courtesy of Bona
Across every region, wood floors can be installed successfully; however, all wood floors cannot be installed in the same manner in all climate zones. Educating end users on proper humidity levels to maintain—stable range is 30% to 50% humidity per the National Wood Flooring Association (NWFA)—can alleviate issues.
When installing hardwood flooring in very dry climates, source flooring materials that have been kiln dried at a lower moisture content, like 6% MC, particularly for regions where 20% to 40% RH may be a more realistic humidity range.
To maximize success, ensure the installation team is properly trained to avoid common mistakes, and follow NWFA guidelines, including these best practices:
- Only apply adhesives to clean, dry surfaces. Otherwise, the adhesives may bond with the debris instead of the surface. Avoid bond-braking contaminants, such as paint overspray, plaster, or adhesive from the previous floor covering. Flooring adhesive failures can become a very costly business disruption.
- Don’t install hardwood flooring until you’ve tested for and corrected all moisture conditions. Test the subfloor to ensure there are no moisture issues by doing a calcium chloride or RH test. ASTM F2170 now recognizes results from an in-situ RH moisture test performed in concrete floor slabs in 24 hours, verses 72 hours for most calcium chloride testing.
- Be wary of any adhesive manufacturer that promotes not checking for moisture content of the substrate prior to installation. Every species of wood has a dimensional change coefficient (DCC), which is calculated by evaluating the moisture content (MC) of the substrate, the MC of the wood the room temperature, and the RH of the space. Each of these qualitative values are required to accurately measure the DCC.
- Allow the wood to acclimate to a conditioned environment. Planks may be installed immediately or may require several weeks on-site. “Moisture matters more than time” is a good mantra.
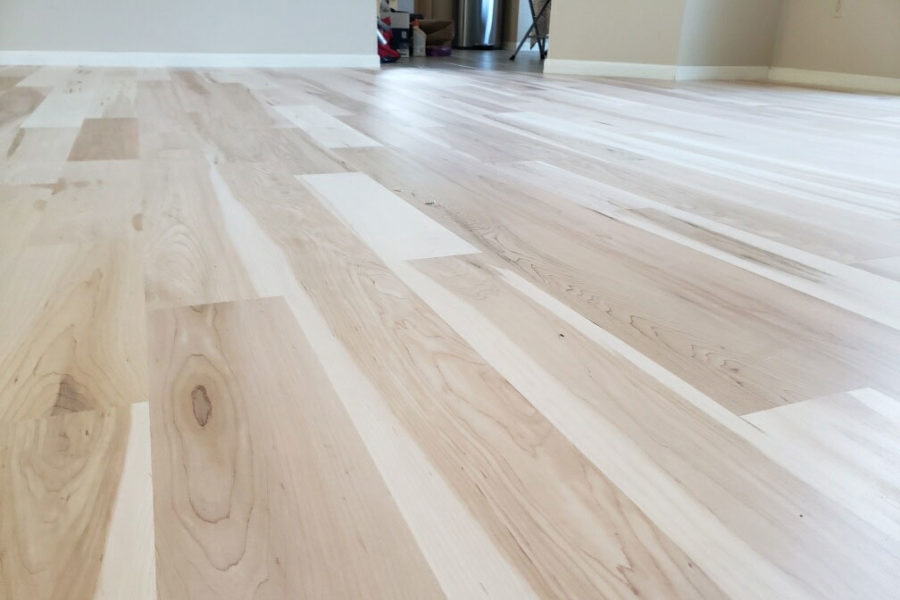
Photo courtesy of Bona
Wood floors should be finished properly to allow for beauty and lasting durability in the environment they will experience. Focus on products that are environmentally safe (like waterborne finishes), offer proven durability, and provide the desired design aesthetic (for example, stain type and color or sheen level of the finish). Elements to consider include:
- Ability to resist chemical exposure and scratches
- Sufficient dry mil film thickness
- Type of sheen desired (extra matte to high gloss)
- Impact on environment and air quality
In addition to being known for high-quality products, designers choose Bona for its deep bench of experience with floors as well as our long-term commitment to high-performing, sustainable products and systems. Our full system of waterborne hardwood floor stains and finishes have been GREENGUARD certified since 2005. Other products have received the coveted GREENGUARD GOLD certification, including Bona’s full line of adhesives.
3. Remember that continual hardwood floor care matters.
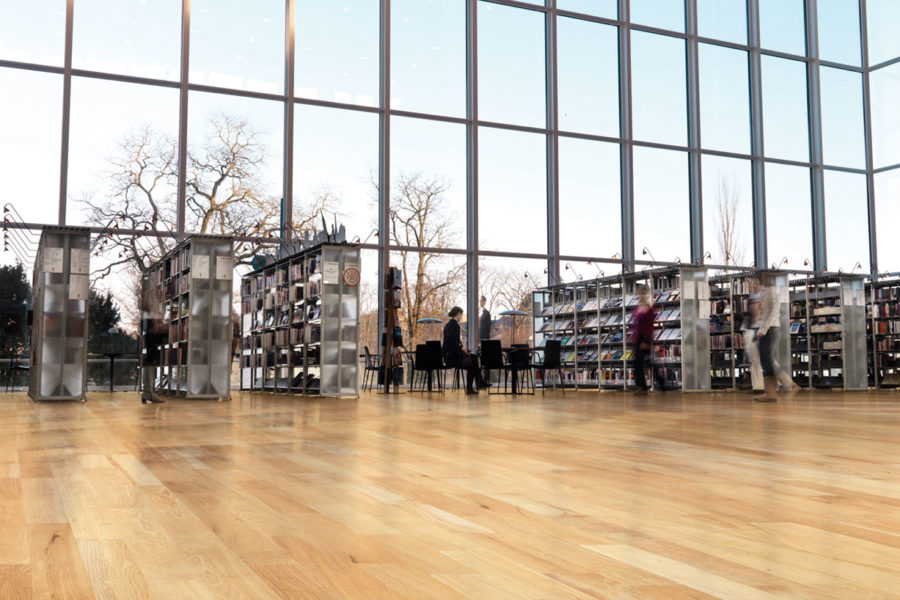
Photo courtesy of Bona
Wood floors are a valuable investment that can offer a lifetime of beauty in a home or building. To protect the customer’s investment while maximizing the floor’s lifecycle, the surfaces must be properly maintained.
Moisture is necessary to preserve wood flooring; yet, it is can also be one of the most dangerous elements for wood. Damage can include too much water used in the cleaning process (we’re not swabbing the deck here!) or ice melt and rock salts carried onto the floor from winter foot traffic.
Improper cleaning methods that include harsh chemicals designed for other types of flooring surfaces can also quickly dull out and haze hardwood floor finishes. Steam mops can also be especially problematic for many of today’s thinly engineered composite flooring materials, often resulting in damage.
Finally, here are a few last tips to keep floors looking beautiful:
- Specify to the floor owner the proper humidity variances of the area’s HVAC system.
- Know what is normal and when you need to call in the experts. For example, wood floors often shrink and swell due to seasonal climate changes that cause RH to increase and decrease.
- For moisture mitigation and to ease the likelihood of outdoor elements coming indoors, encourage the use of waterproof mats and frequent vacuuming near entryways.
- When maintenance is needed to revive or refinish wood floors, recommend floor owners work only with a properly certified and trained Bona Certified Craftsmen.