Story at a glance:
- A homeowner in Marietta, Georgia wanted to prove high-performance homes could be built on a budget.
- The three-bedroom house has four to seven inches of continuous stone wool insulation.
- The house is more airtight than required by passive house standards.
Clients usually go to Chris Laumer-Giddens with a wishlist of things they want in their homes. “The folks who have reached out to us over the last few years, some of them are very well researched, and they’ve followed a lot of the industry from the homeowner’s perspective,” says Laumer-Giddens, who runs LG Squared, an architecture and construction firm specializing in high-performance buildings. In addition to the typical requests of wide open views and natural light, LG Squared’s clients have a long list filled with sustainability buzzwords like solar panels and passive house.
The client for a home in Marietta, Georgia was no different. “She was trying to prove you didn’t have to be a millionaire to build high performance,” Laumer-Giddens says.
The client originally wanted to remodel and retrofit the home to be more energy-efficient. “Her father was a general contractor and taught her a lot about where you really want to invest your money. One of those things is a slab foundation,” he says.
But the foundation of the existing home was cracked and the home wasn’t well insulated. It would take just as much money to renovate it to her standards, so the team at LG Squared convinced her to tear it down and completely redesign it.
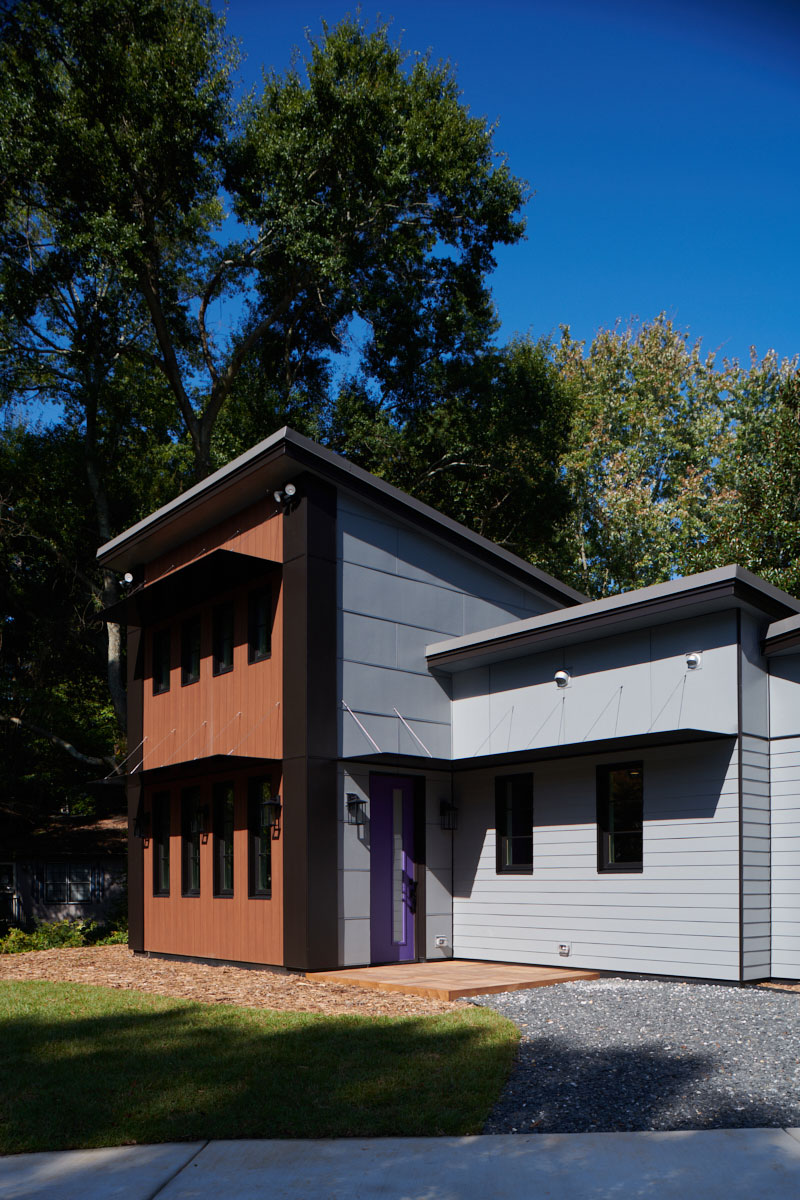
The house uses metal trims as opposed to typical corner trims because they are more durable and hide the cut corners, giving it a cleaner look. The door is purple—the owner’s favorite color. Photo courtesy of LG Squared
The result was a single-story, three-bedroom house with an attached garage. Surrounded by trees, the house sits in a cul-de-sac, which gave the architects a unique challenge. Instead of laying the house in a long rectangle, the home comes together in five segments, angled to create an arc. The main segment stands out the most. Unlike the other parts that are covered in gray fiber cement, the main section is clad in a composite material with a warm wood tone. It is also noticeably taller than the other sections to accommodate a loft space.
The inside of the house was designed to be open and spacious. “It’s not just voluminous and expansive, but also intimate,” Laumer-Giddens says. Almost all of the space is usable, with less than 1% of the floorplan dedicated to circulation. Most of the house is covered in hardwood, but other parts use tile or polished concrete. The kitchen is fitted with dark cabinetry, which provides a contrast to the light colors used throughout the house. The client chose the lights, including modern pendant lights and a classic chandelier.
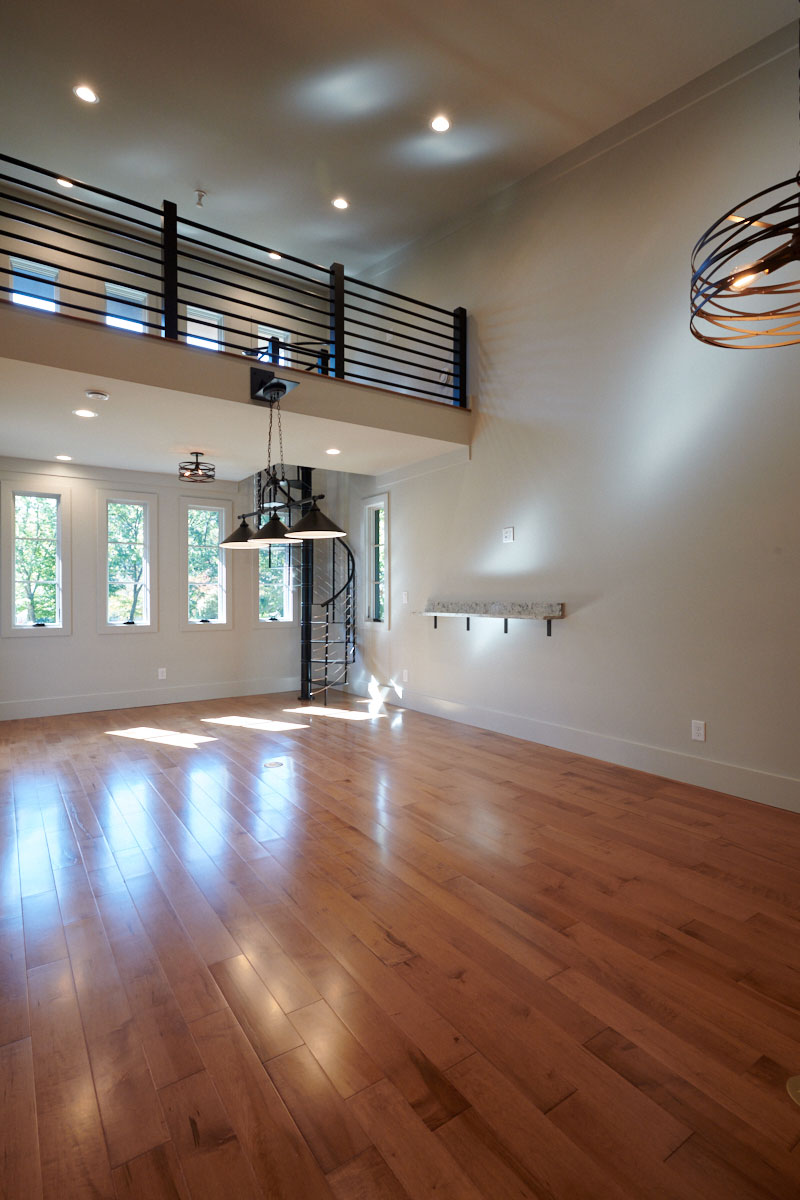
The inside of the home was designed to be open but cozy. Photo courtesy of LG Squared
This contemporary home may seem fairly straightforward, but the building’s superpower is hidden from sight. “We put a lot of effort and attention toward making the building envelope,” he says. Built on wooden frames on top of a concrete slab foundation, the house has four to seven inches of continuous stone wool insulation.
Laumer-Giddens says he used stone wool because it has many of the properties he looks for when thinking about insulation. Not only does it have high thermal performance, it prevents moisture and mold and is fire- and bug-resistant. It’s also rigid, which makes it easy to stack during installation. “It’s not load-bearing, but we can put it underneath the slab. It just takes care of everything that we need,” he says.
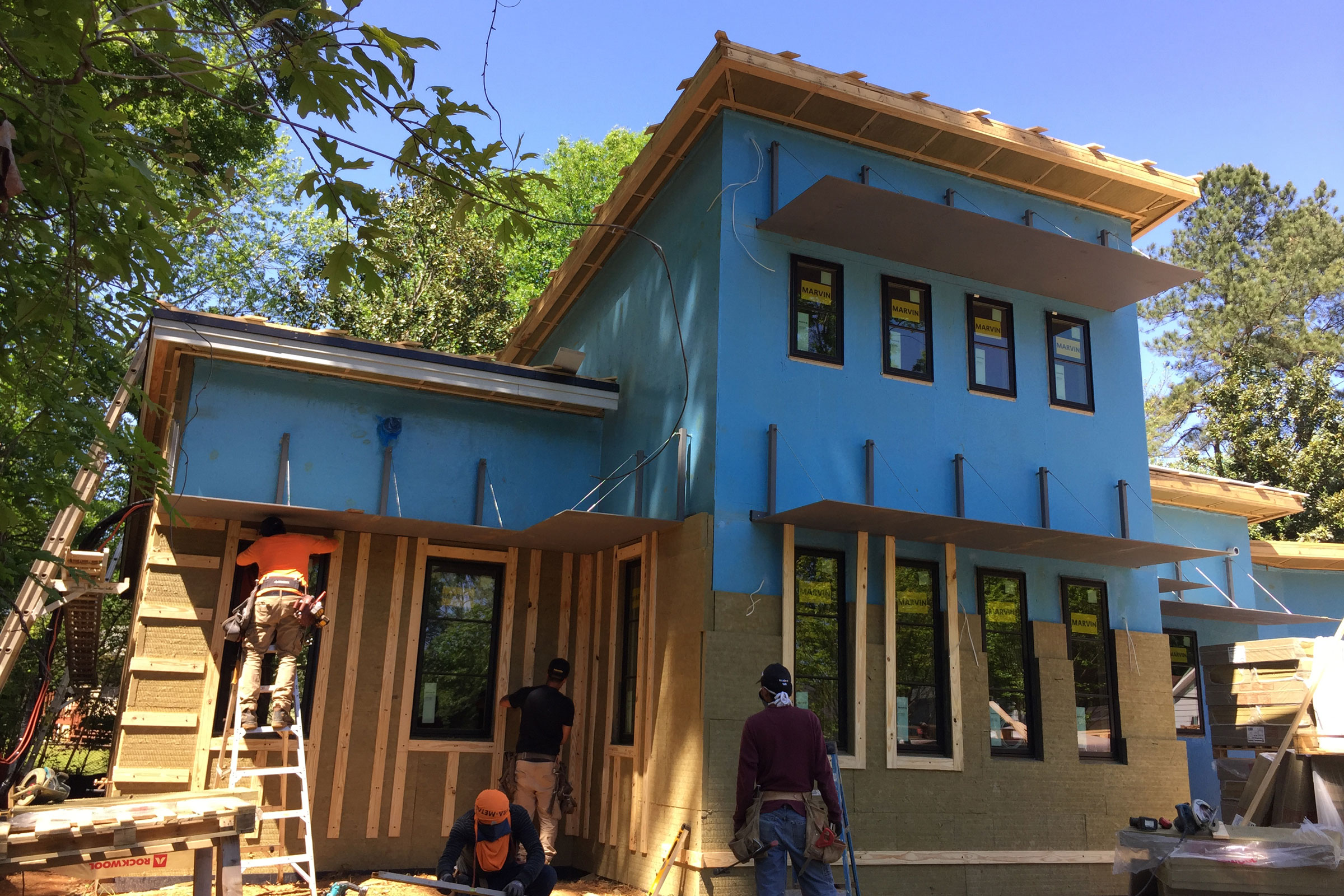
Chris Laumer-Giddens of LG Squared says he like using ROCKWOOL insulation in his projects because its formula has less irritants and is easier to work with. Photo courtesy of LG Squared
“We tend toward ROCKWOOL on all of our projects,” he says. “They’re making it more accessible to the residential construction market, which is where we spend most of our time. I’ve tried the other stuff, and it just doesn’t have the same performance and usability.”
By designing a custom house, the team was able to account for the insulation in the design. “The analogy that is used in the industry is you’re warmer if you wear your sweater rather than swallowing your sweater,” Laumer-Giddens says. Sometimes rafters create overhangs that interrupt the insulation layers. “We didn’t use the typical method of construction where the rafter went through the building.”
Instead they used outriggers placed inside the insulation. Making sure the envelope was airtight was made “easier because we designed it from scratch, rather than trying to figure it out in the field.” This resulted in a house that surpasses passive house standards for airtightness.
They were also able to incorporate the insulation into other design elements, such as recessed windows. “Because the installation is four inches thick we had the opportunity to create these deep pockets for the windows. There’s an architectural look, but there are some practical advantages to it as well,” Laumer-Giddens says. The recess provides some protection from sun and rain.
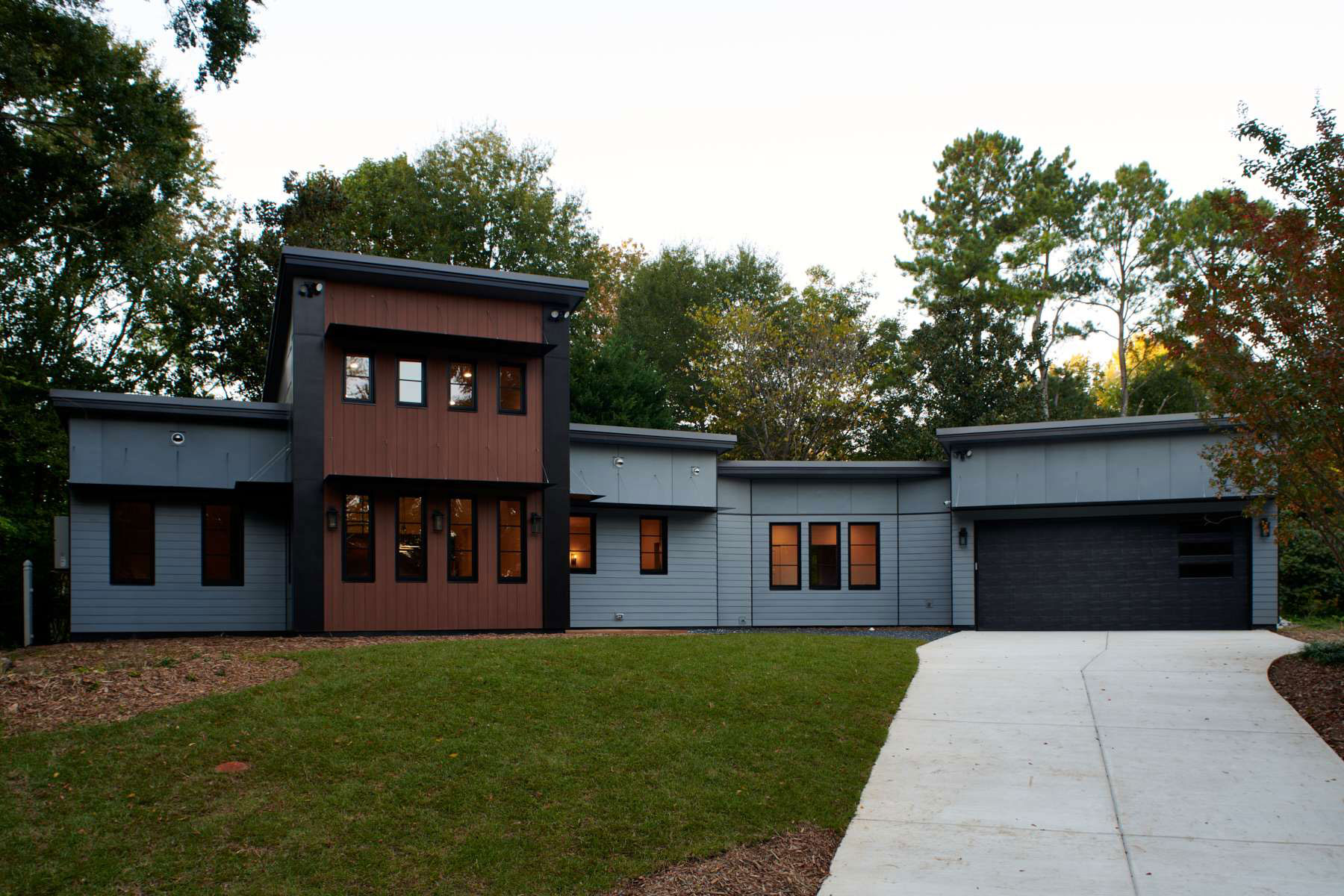
Rain is collected in the rain gardens designed by Shades of Green Permaculture. LG Square designed downspout pipes that are connected to the rain gardens and can be funneled to a cistern if the owner wants to add one in the future. Photo courtesy of LG Squared
In addition to a very efficient envelope, the team also designed steel canopies to hang above windows. “They keep a low profile but provide plenty of shade,” Laumer-Giddens says. The windows are south-facing, and the team wanted to make sure they had full coverage during high noon.
He says it makes more sense for homeowners on a budget to invest in a more robust envelope than spend money on an off-grid energy system. The owner initially wanted to add solar panels. “The orientation of her site was not good for solar. It faced south, but there were trees on either side, so she would have had a window from like noon to 1 to 2pm where she had some sun, and that’s just not enough to justify the cost of a full on system,” he says. He encouraged the owner to live in the house for a few years to see how much energy she really needed before installing an energy system.
Laumer-Giddens was able to experience the effectiveness of the building envelope for himself during construction. “We had insulated the home right before the summer broke, and as it started to get really hot, it stayed in the 60s inside the house,” he says. “I know it works, but it’s just fun to go in there and see how well it works. I’m so glad it feels exactly the way I explained it was going to feel or actually better.”