Story at a glance:
- Similar to a life cycle assessment, a life cycle cost analysis (LCCA) breaks down all of the present and future costs associated with a new build or major renovation from its beginning to its end.
- The usefulness of an LCCA is its ability to compare different scenarios and select the most inexpensive one that also provides the greatest value over the entire life of the structure.
- An LCCA requires a systems approach to building and design taken from a broad (long-term) perspective.
Sustainability is always at the forefront of a green designer’s mind, and rightly so. But is it enough? While this mindset is vitally important, an accompanying life cycle cost analysis (LCCA) of any project will provide quantitative and data-driven proof that your new build or major renovation will simultaneously be cost-effective, energy-efficient, and low-carbon over a period of time compared to other options you consider. In other words an LCCA can make your project truly sustainable.
In this article we explore the LCCA and consider a few examples to demonstrate how they can help green designers and builders.
What is a Life Cycle Cost Analysis?
A life cycle cost analysis (LCCA) is an economic methodology used to quantify all the costs associated with a new construction or major renovation from its inception to its end of life. It includes present and future costs, not just initial costs to design and build. An LCCA can also be used to evaluate existing facilities.
An LCCA counts the costs of building materials, labor, energy and water used to build and operate, maintenance and repair costs, replacement costs, embodied carbon, carbon emissions, and salvage or disposal costs. An LCCA accounts for inflation and minimizes uncertainty.
Calculating a Life Cycle Cost Analysis
Based on the LCCA a designer, builder, or prospective owner will know the life cycle cost of a building or one of its systems as the total discounted dollar cost of owning, operating, maintaining, and disposing of it over a specified time period (usually 25+ years).
The qualifier discounted refers to the real discount (interest) rate set annually by the US Department of Energy in Handbook 135 and adopted for general use in LCCAs. Along with the real discount rate, costs are expressed in LCAAs as constant-dollars (dollars tied to a reference year and do not include inflation).
Using constant-dollars and the real discount rate simplifies LCAA calculations because there’s no need to project what future labor and material costs will be. Those costs are set to what they were in the reference year (often the year of initial build or renovation). Changes in the value of money are accounted for by the real discount rate.
To combine initial and future costs in an LCCA, their present values are first calculated. Present values (PV) are stipulated to be those of the base year (when building or renovating began).
Using a Life Cycle Cost Analysis
A life cycle cost analysis (LCCA) may be used to compare two or more of anything related to a structure. This includes building frames, materials, insulation, HVAC, plumbing, or electrical systems, windows, roofs, furnishings, landscaping, and so on. An LCCA can be extremely comprehensive and consider all of these elements or just a few.
Whatever you’re including in an LCCA, it becomes evident that a structure’s systems are interconnected. For instance, windows may possess varying insulating abilities, which, in turn, impact energy usage. Similarly, would increasing energy efficiency by stacking more traditional (high embodied carbon) insulation be worthwhile in the long run compared to the energy gains from a different design?
Generally, because of the high carbon emissions and energy-intensive process of making new concrete and steel, an LCCA will show that leveraging existing assets is the long-term, eco-friendly solution. “Avoid overreacting to ‘first cost.’ Instead, look at the entire lifespan of that investment,” Daniel Jaconetti, associate principal and national sustainable design leader at HED, previously wrote for gb&d. “Upfront expenditures may result in bigger savings in the long run. Your design team can perform a life cycle cost analysis (LCCA) to provide data to justify your financial planning. The most sustainable building is likely the one that already exists. While company leadership could be attracted to the idea of a shiny, new headquarters or think the current workplace may be beyond improvable, often it’s worth doing some deep thinking to strategize how you can work with what you already have. This can save time, money, operational disruption, and embodied carbon.”
Examples of Life Cycle Cost Analysis
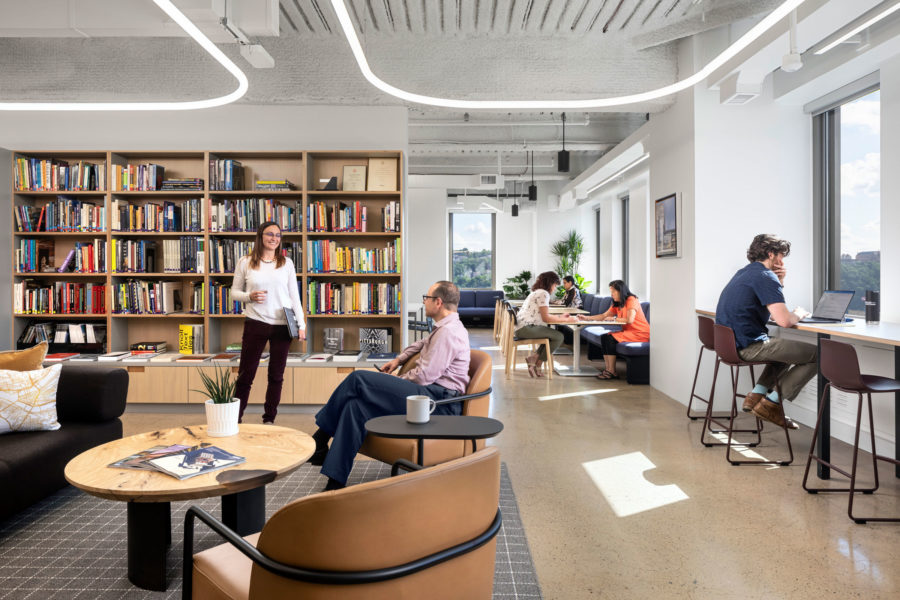
Inside Perkins Eastman’s Pittsburgh office. Photo by Andrew Rugge
Conducting a comprehensive life cycle cost analysis may appear to be a daunting task. As the examples below show, an LCCA—in whole or in part—is worth the effort.
Perkins Eastman Pittsburgh
The Covid pandemic allowed Perkins Eastman to reconsider its own workspace as it integrated a flexible hybrid option into its operations in 2020, by reconfiguring its office space and trimming superfluous construction in an interior fit-out. As a result they lightened their footprint by 17% and their embodied carbon by 33%.
“Similar to the strategy of building less, the strategy to prioritize quality over quantity has numerous other benefits that are easy to quantify: reducing attic stock, providing fewer opportunities for supply chain problems, and giving clients confidence that each material was carefully specified to meet a project’s particular goals,” Jennifer Askey, associate principal at Perkins Eastman, told gb&d. “Convincing a client to build sustainably isn’t always easy; the benefits can sometimes seem remote or burdened with the barrier of a higher initial cost. However, a strategy to build less is better justified when each element eliminated from the project has multiple benefits: eliminating barriers, opening sweeping views of downtown, reducing construction costs and schedule, minimizing waste, and lowering the project’s embodied carbon.”
Westlake Royal Building Products
Westlake Royal Building Products uses life cycle analysis—essential components of LCCAs—to show how sustainable their building materials are.
“It’s long been thought that vinyl siding was not the sustainable choice because it’s made from plastic, which is an understandable point of view when you think of all the harm that single-use plastic does. But when you really start looking at everything in the life cycle analysis, from manufacturing process and the ingredients that go into vinyl to the durability and the lifespan of the product, it really comes out on top,” Steve Booz, vice president of marketing for Westlake Royal Building Products, previously told gb&d. “Vinyl siding is so durable it’ll be on your house for 50-plus years, which is the most resource-efficient way to go. Vinyl has 79% less impact on climate change than fiber cement and 85% less impact than brick and mortar cladding. You’re far more likely to find recycled materials in vinyl than in other products.”
Stanford Health Care
Stanford Health Care is a leader in sustainable healthcare design and is continually striving to improve. Recently they were looking into modular design so spaces can be easily reconfigured depending on clinic needs from an office to an exam room or even a treatment room. Modular design doesn’t require costly and material-intensive renovations and is a sustainable, long-term option.
“It’s a bit of a learning process as we go, as greener materials become available. We do look at things from a life cycle analysis perspective, moving away from just looking at the first cost,” Molly Fries, Stanford’s interim director of operational excellence, previously told gb&d.
Hospitals have complex HVAC systems composed of multiple individual zones, each with its own regulated humidity, temperature, airflow, and air pressure. Designing it to be energy-efficient is difficult and requires designers, architects, general contractors, and subcontractors to work as a team. “It has to be an entire flow of change that occurs. All the parties along that chain have to be committed,” Helen Wilmot, Stanford’s chief facilities and sustainability officer, said in a previous gb&d article.