Story at a glance:
- Standing seam metal roof systems are strong, with the average lifespan approaching 50-plus years.
- Engert’s metal roofing systems include ULTRA-Cool™ technology, which reduces energy consumption and utility bills.
- Englert’s roofing systems are available in steel, aluminum, and copper—all of which are sturdier than traditional asphalt
It used to be that metal roofing systems were primarily utilized for commercial, industrial, or agricultural uses. It was more common to see a metal roof on a barn than on a typical suburban street. Yet, as their many benefits became widely known and environmental sustainability rose as a critical factor for developers, architects, and homeowners, metal roofs have proliferated across residential areas as a stylish, durable alternative to traditional asphalt roofs.
As the Covid-19 pandemic recedes and the metal roofing industry returns to a robust rate of growth across a variety of use cases, one of the industry’s original pioneers continues to drive innovation and set standards for the market. Englert—a leading manufacturer of metal roofing systems—is testing out new products at its Pennsylvania research facility and gearing up to meet increased demand from a post-pandemic building boom.
Founded in 1966 in New Jersey by Herbert Englert, the firm was one of the first companies to sell portable gutter machines and originated the concept of a total system—in which it sold the aluminum gutter materials, the installation equipment, and accessories, as well as its technical know-how. As the business evolved and grew, Englert moved into the metal roofing business and began manufacturing portable roll forming machines for roofing systems.
Andy Jasani, Englert’s director of client solutions, is tasked with taking the company’s innovative solutions to the next level. The company has moved beyond simple gutters and roof coils and today offers complete end-to-end metal roofing solutions for architects, contractors, and homeowners looking to increase the value of their property. Englert’s product portfolio includes numerous lines of architectural, structural, and curved panel metal roof systems, in addition to gutters, soffits, and other accessories. The company even has its own in-house paint line.
Jasani recently took some time out of his busy schedule to discuss how a metal roof system can benefit any type of project.
What makes metal roofing systems superior to traditional roofing materials?
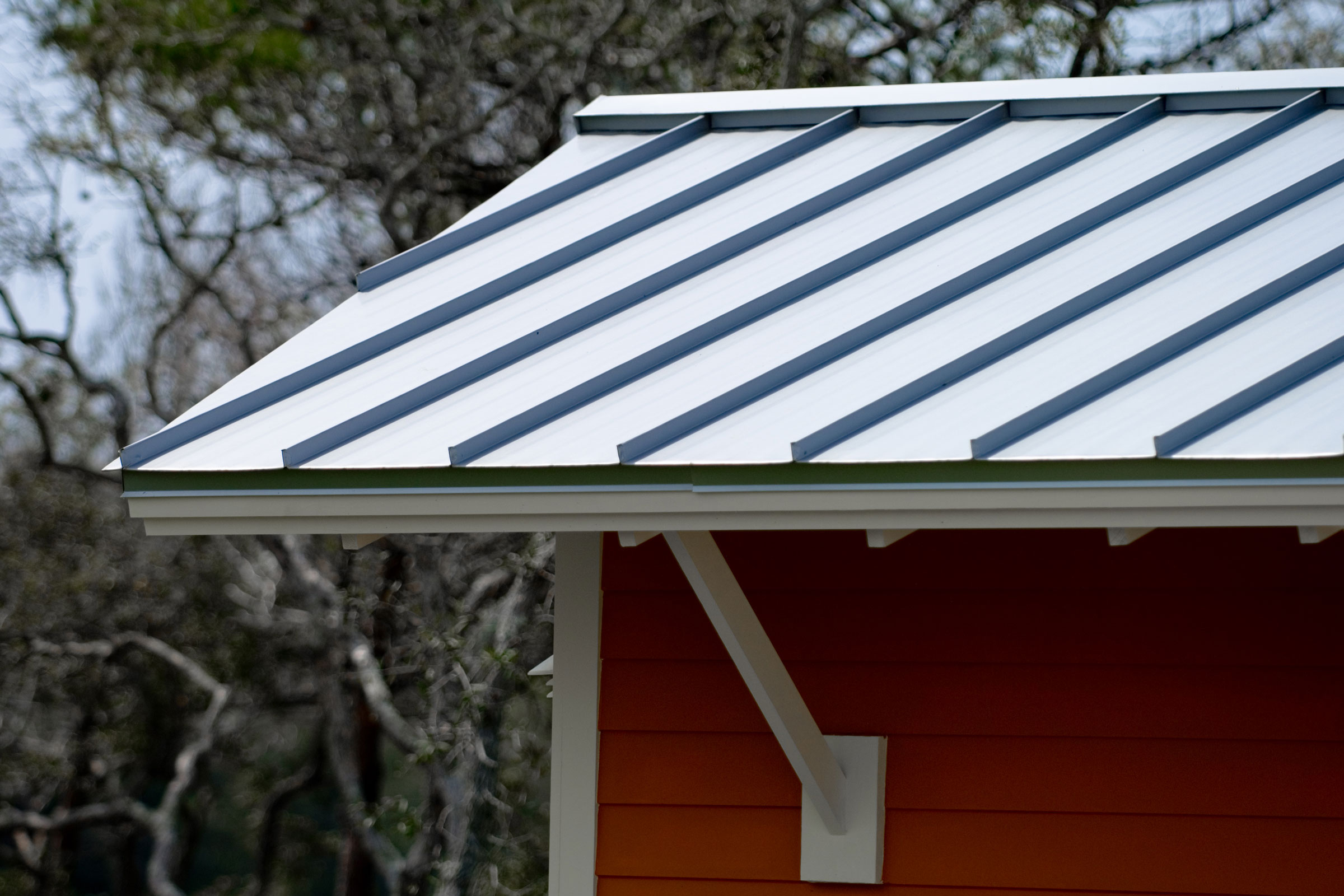
Photo courtesy of Englert
Standing seam metal roof systems are superior to traditional asphalt shingles in just about every way. First of all, there’s the strength and versatility aspect, with the average lifespan of a metal roof approaching 50-plus years. They’re not going to rot, crack, or crumble; and they require limited care and maintenance.
They’re also far more sustainable than the alternatives. Metal roof panels reflect the majority of sunlight back into the atmosphere and resist solar heat gain, which cuts down on energy consumption and utility bills for the buildings’ interior.
Our metal roofs are made from recycled materials and, at the end of their lifespan, the material itself is 100% recyclable. And, of course, they are aesthetically pleasing and versatile in their design capabilities. Architects love working with them because of the wide variety of styles and colors that are available.
How durable are metal roofs? What are the factors customers must remember when considering a metal roof system?
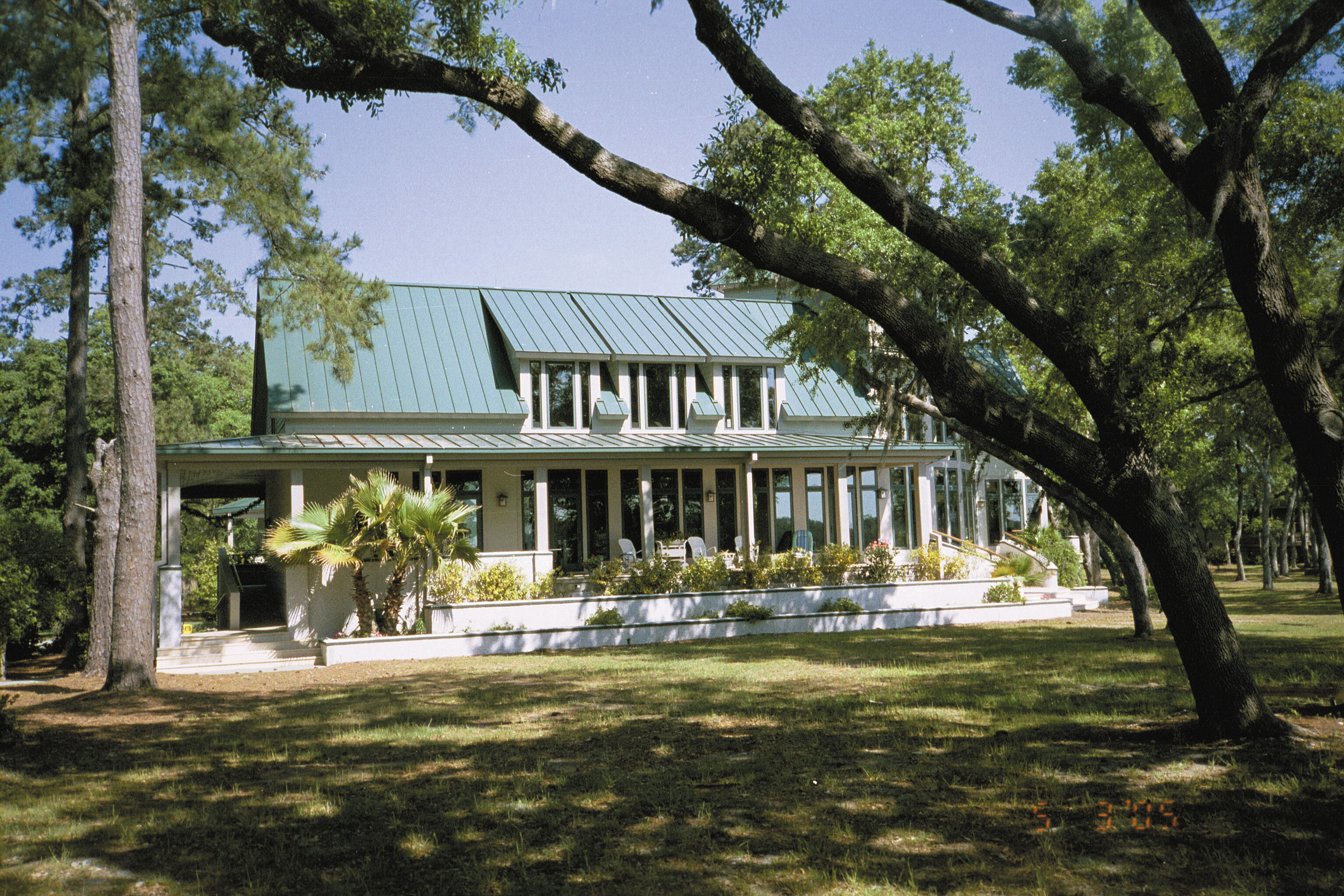
Photo courtesy of Englert
Metal roofs are extremely durable, and far more so than any alternative materials.
Our roofing systems are available in steel, aluminum, and copper, which are all sturdier than traditional asphalt. And while many people think steel is the most durable material, in fact steel can begin to corrode in about 10 years, especially in a coastal climate with a lot of salt in the air. Aluminum, or our Galvalume steel that is made from 45% zinc and 55% aluminum, is probably the most durable and can be guaranteed for up to 50 years.
But regardless of the particular material, our standing seam metal roofs are much better equipped than any other roofing system to withstand hurricane force winds. We’re constantly testing and upgrading our product line, which meets the very stringent Florida Building Code requirements that supersede other state or local guidelines. During Hurricane Irma in 2017, which struck Key West with 150 mph winds, a building with our Series 2500 structural roofing system sustained no damage, while the buildings near it all had roof damage.
What are the larger trends in the industry that are driving innovation at Englert?
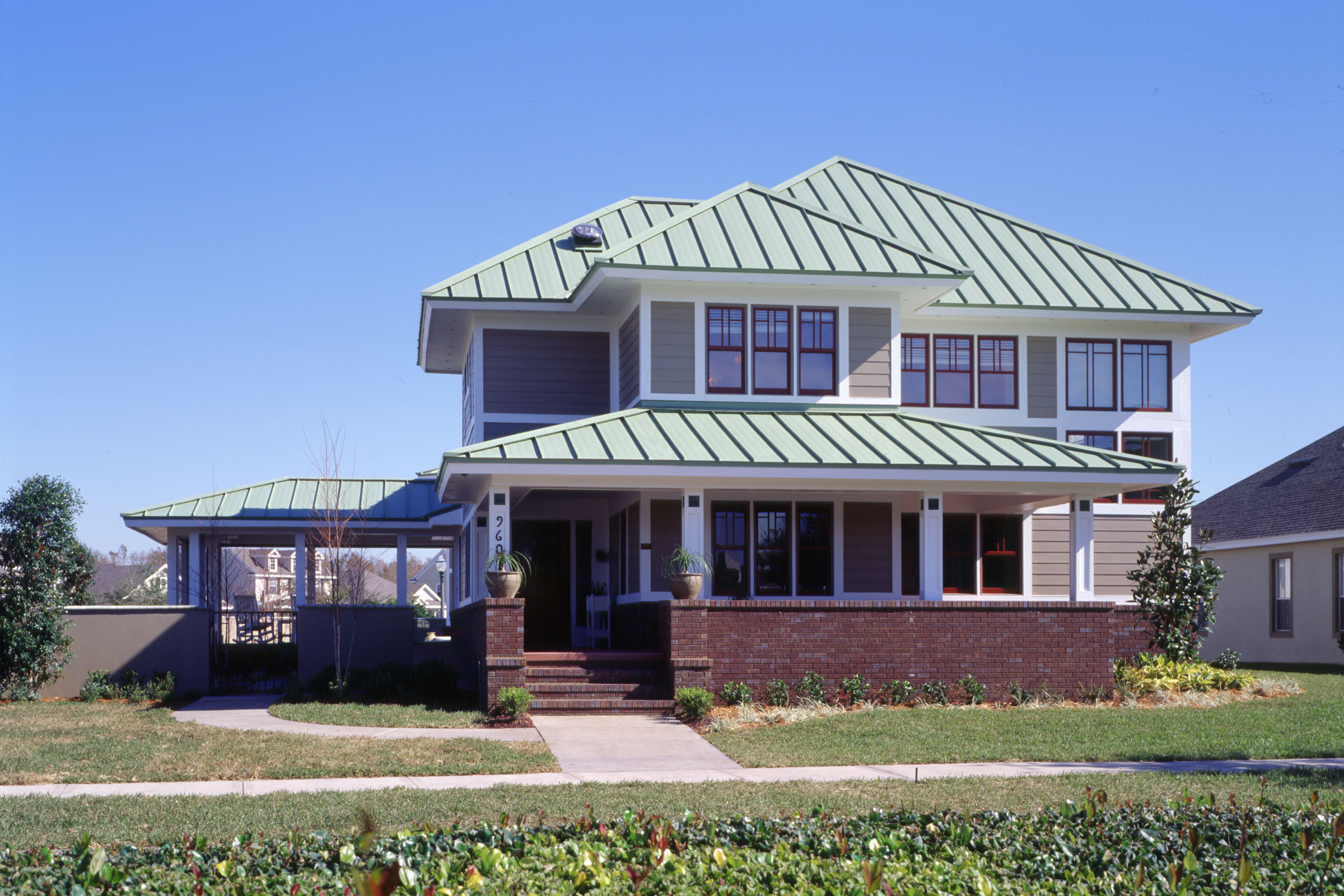
Photo courtesy of Englert
Architects are increasingly designing with the environmental impact of building products being paramount, so Englert is actively providing information regarding recycled content and regional supply of materials for products specified within the design community. Overall, sustainability features are becoming a necessity, not an added bonus. The massive increase in popularity of LEED certification and Environmental Product Declarations (EPD) have prompted us to embrace green building practices across the entire business. For example, we developed our cool roof technology, the ULTRA-Cool™ low gloss coating paint line, in order to meet LEED requirements for cool roofing. Our ULTRA-Cool™ finishes reduce energy costs and cool the interior of a building by dramatically increasing the heat reflectivity of the metal roofing, while meeting LEED’s 2.2 Solar Reflective Index.
Tell us more about the sustainability benefits of Englert’s roofing systems.
We have really tackled sustainability from all angles. You have the ULTRA-Cool™ technology, which reduces energy consumption and utility bills. Our steel and aluminum roofing systems also qualify for LEED credit requirements for both recycled content and recyclability. Englert’s prefinished Galvalume coated steel and aluminum materials are made from a high percentage of recycled material, and at the end of the roof’s useful life the steel and aluminum are easily recycled to benefit the environment.
We source our Galvalume steel and aluminum from US Steel, which utilizes the basic oxygen furnace (BOF) process that consumes 34% recycled scrap—which breaks down to almost 20% post-consumer scrap and 14% pre-consumer scrap. At Englert we are always making the extra effort to work with the general contractors and architects, compiling information to account for material sources and recycled content.
What is Englert’s most popular roofing system?
Our most popular item is definitely the Series 2000 integrated snap-lock panel system for residential, commercial, and institutional uses. The S2000 features a 1 ¾” seam with a 3”/12” minimum slope, and the system is highly versatile—you can install it over open framing or a solid deck. Architects love it for its cleanly detailed, continuous seam transitions that go from roof to mansard, fascia, wall panel, or soffit. At the same time, contractors appreciate that the snap lock panels are easier to install than mechanically seamed panels.
What is the ideal roofing system for the typical residential customer?
For residential customers I say the best option is generally the Series 1300 and 1301 architectural system, which has a slightly smaller 1 ½” & 1” seam and a minimum slope of ½”/12”, which is getting close to a flat roof. This means it can be utilized in dry desert climates where precipitation is not an issue. The mechanically seamed panels also provide a more secure, weathertight fit that helps keep rain and snow out and requires less maintenance.
Which roofing system do you recommend for the typical commercial or institutional customer?
For the heavy-duty commercial or industrial customer, the Series 2500 Armco-style, single-lock panel system is the way to go. The S2500 is one of the industry’s most extensively tested systems, with a 2” seam and a powerful interlock clip that holds the system in place while allowing for thermal expansion and contraction. This makes it ideal for Midwest or Northeast climates with heavy precipitation and plenty of temperature variation. The S2500 is available with seams of 90° or 180°.
Why do architects and contractors want to work with Englert?
Architects truly appreciate the aesthetics and flexibility of our product line. Unlike most metal roofing manufacturers, we have our own proprietary in-house line of paint with 26 colors to offer, as well as the ability to make special requests. They also appreciate the experience our architectural sales reps have in architecture and design. As leaders in the field with decades of experience we have the technical resources as well as the quality of services and materials that architects look for in a design partner.
In your 11 years with the company, what has been the most exciting job thus far?
I came to learn that I had to go onsite for an inspection at Joint Base Andrews outside of Washington, D.C., where Englert was going to provide a weathertightness warranty for a newly constructed building. We were installing the S2500 with 180-degree seams. I asked the contractor we were working with if I could get a chance to see Air Force One while we were there, but he said security was strict and civilians weren’t allowed close to the president’s plane. He did, however, hint that I could play dumb and turn left once I got onto the base, which would take me toward the hangar where Air Force One would be parked. I did exactly that when I arrived and was amazed at the beautiful flying machine right in front of my eyes. But before I knew it, I was quickly surrounded by Jeeps full of armed guards asking what I was doing over there. I told them I got lost and was looking for the new construction where Englert’s roof was being installed. They escorted me there and waited until I left the base. That’s a day of work I won’t forget.