Story at a glance:
- Modularity should be at the forefront of design conversations to reap the most benefits, including scheduling.
- This new citizenM hotel took four months less to build than a traditional building project, with 60% less construction waste.
- Gensler designed the hotel to blend in with its trendy Seattle neighborhood.
Tucked in Seattle’s trendy South Lake Union is a seven-story slate gray building built using modular construction. Designed by Gensler, it’s a foray into the West Coast by European hotel chain citizenM. The new building blends in well with the neighborhood, not obtrusive in size nor shape, and largely mirroring its surrounding buildings. But below its gridded facade are layers of impressive structural problem-solving, all fitted into a steel cage body.
A bright, large-scale art piece wraps around the two street-facing facades of the building. Abstracted nods to pine trees and rain are rendered in magentas and turquoises. The piece, by Seattle-based artist Jesse LeDoux, features prominently in the concept renders for the building, where every window and their respective inhabitants are depicted in a myriad of colors.
On the ground floor, a similarly colorful mural wraps around the elevator core—a piece by local indigenous artist Jeffrey Veregge and a personal favorite space in the hotel, according to Case Creal, design manager and senior associate for Gensler Seattle.
All of the hotel’s public spaces are housed on the ground floor, which serves as a base for the steel cage supporting all private rooms above. The two murals highlight and, at the same time, bring a liveliness to their respective structure, harkening to the 9 square grid—that famous architectural exercise that teaches how to play within a structure.
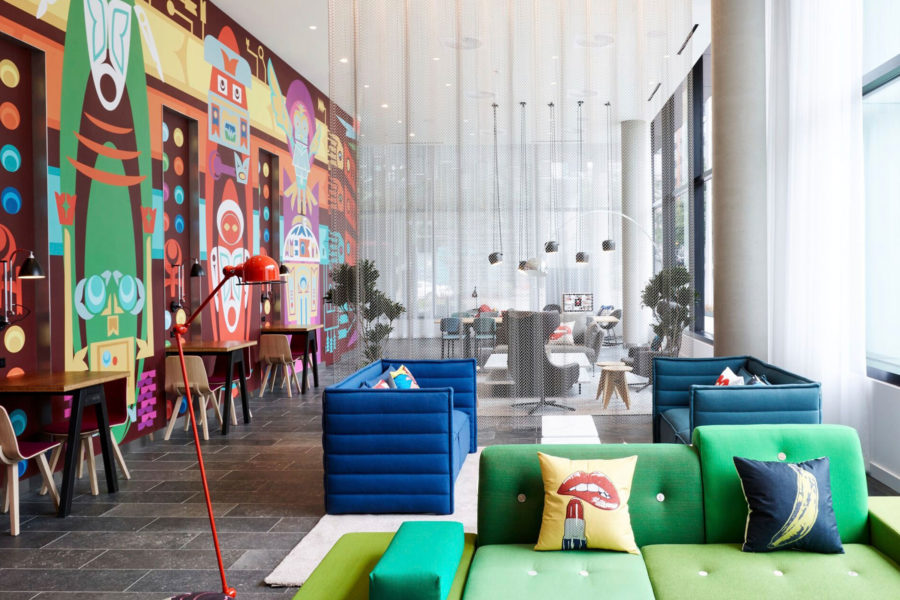
Bright colors and plentiful natural light are consistent throughout this Gensler-designed citizenM hotel. Photo by Richard Powers
Modular architecture is still a relatively new method of building. Despite its prevalence in postwar architectural theory when prefabrication came into being, modular buildings are still not that common to see in the wild—especially in seismic zones. “Whenever we would go into a new jurisdiction that was a new challenge for them by and large. We had to work with [that jurisdiction] to craft a process for permitting and for inspections that the local and state jurisdictions could feel good about,” Creal says.
But citizenM’s model made modular building even simpler. Standard across their locations, the hotel chain offers one type of room—a single, king-sized bedroom—and an accessible iteration. This allowed Gensler to quickly agree on what Creal calls a modular go or no-go process. “We commit to that really early. It’s a pretty deep dive, but we work together, commit to that, and don’t second-guess it as we go. When you step away from pursuing modularity as rigorously and quickly as you can, you lose all the benefits of modular construction, chief of which is the schedule benefits.”
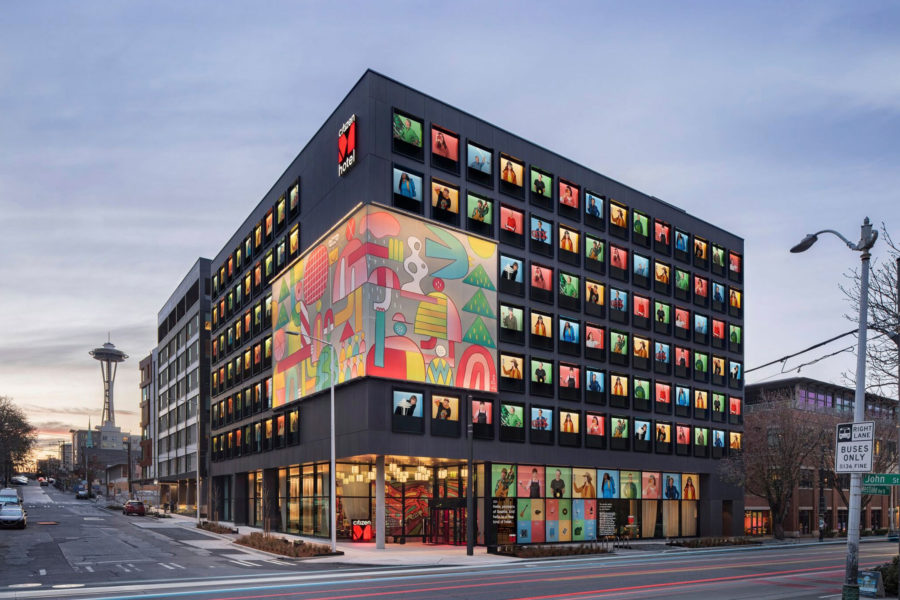
Gensler designed the new citizenM hotel to blend in with its trendy Seattle neighborhood. Photo by Richard Powers
Everything above the ground floor was built as units via citizenM’s longtime fabrication partner Polcom in Poland, then shipped to Seattle. While the relatively long transportation route takes a toll from an environmental perspective, the design team says it doesn’t outweigh the environmental benefits that come from building in a factory (especially one already equipped to fabricate for citizenM), and especially when compared to the toll of shipping raw materials across the world as needed in a traditional site-built project.
Manufacturing the units in a factory setting has a myriad of benefits from an environmental perspective; where the average building will involve shipping more materials than needed to any given site, the excess of which will need to be disposed of, a factory is able to aggregate materials and distribute them between projects as well as plan out what’s needed precisely, so waste is minimized.
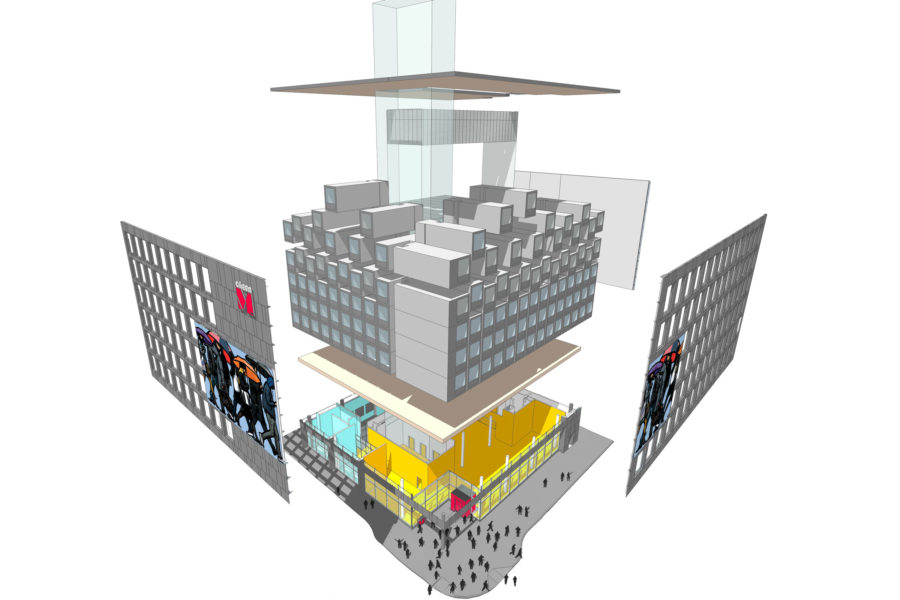
Assembling the new citizenM hotel in Seattle. Drawing courtesy of Gensler
The team designed for fabrication, transportation, assembly, and, finally, so each unit would perform well in a high-seismic activity zone. They had to design so the units could withstand the dynamic loads of transportation and the gravity loads that come with being picked up onsite, as well as in a way that was flexible enough to sway with the building in the event of an earthquake.
Modular building in seismic zones is rare; in this case, because the building isn’t low-rise, it was built with concrete cores that absorb the lateral, seismic forces from the units and carries them back into the ground. The payoff of all these design considerations is a project that took four months less than a traditional building project, and with 60% less construction waste. The shorter timeframe and fewer deliveries also contribute to less pollution “down to the number of Porta Potty visits, Dunkin’ Donut cups, and hours of idling vehicles,” Creal says.
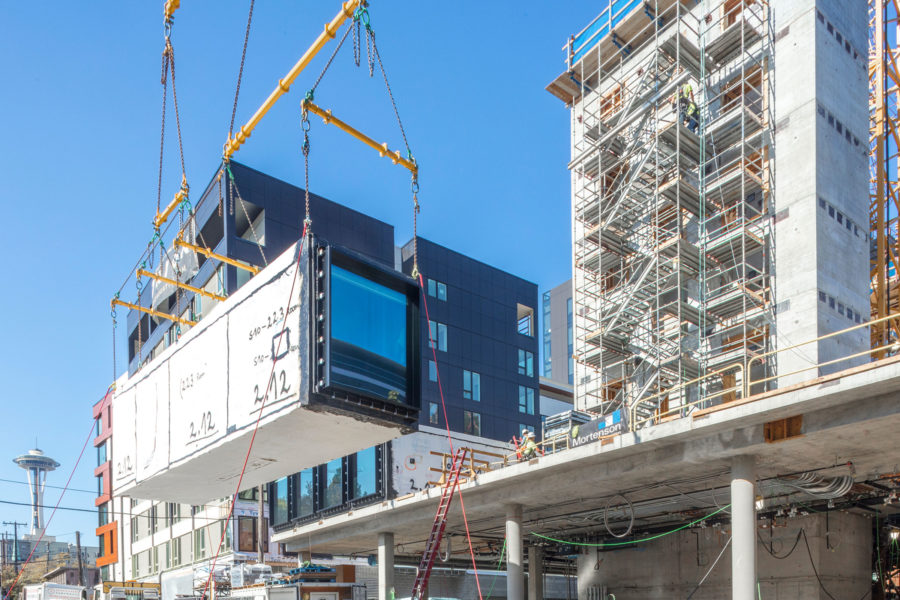
Dropping in the modular units of the citizenM hotel in Seattle. Photo by Heywood Chan
On top of those environmental benefits, the building also boasts solar panels on its roof as well as a heat pump, a measure that is rarely used for hotels. The result is a LEED Gold certification and a building that uses 29% less energy than otherwise.
Modular building, originally conceived of as a thing of the future, may be having its moment now. Increased globalization and the capacities of industry now allow prefabricated units to be produced on a scale never seen before. Creal is hopeful for the possibilities of modular. “I think we need to start taking on a different approach to building. We often think of these buildings as bespoke creations, and I think if we can get away from that and think of them as a series of products that go together, we’ll really be able to bring the efficiency, effectiveness, and reduced environmental impact onto projects.”
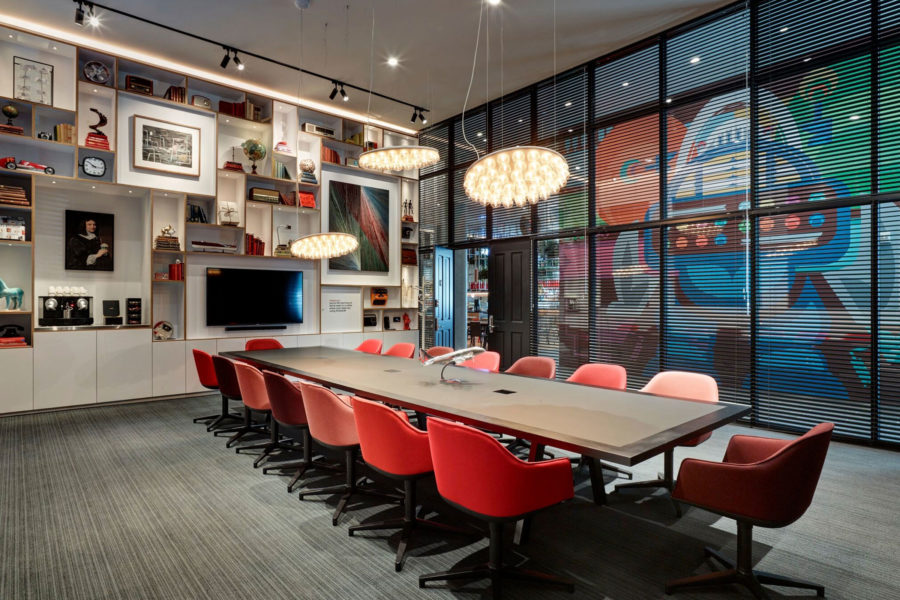
Inside Seattle’s new citizenM hotel. Photo by Richard Powers