Story at a glance:
- The metal roof on a North Carolina school was in bad need of repair when experts recommended a fluoropolymer-based roof coating.
- Proper removal of existing coatings is crucial for the ability of a new coating to perform as intended.
The damage started to become apparent during a roof inspection in the spring of 2015. After 25 years of service life, the metal roof on Central Middle School in Dobson, North Carolina was showing its age. Back-to-back winters with heavier-than-average amounts of snow and ice caused the blue, factory-applied coating on the standing seam roof to flake and peel off, exposing large sections of gray primer and the underlying steel roof panels to the elements.
“As snow and ice slid off the roof, they took chunks of paint with them,” says Robert Draughn, director of Construction, Planning & Design for Surry County Schools. “The coating failure got worse and worse, to the point where we were concerned that the exposed metal panels could rust and create opportunities for leaks.”
Eager to avoid the expense and disruption of replacing the roof, Draughn reached out to the plant operations division of the North Carolina Department of Public Instruction for advice. The division’s engineers inspected the roof and recommended recoating it with a fluoropolymer-based roof coating—a strategy that had been used successfully in other school districts in the state.
Assembling the Team
The engineers invited several coatings manufacturers to visit the school and provide recommendations for remediation. APV Engineered Coatings, maker of NeverFade® Exterior Coatings, was one of only two coatings suppliers to take them up on the offer. The company sent Product Application Engineer Ernie Porco to inspect the roof and evaluate the condition of the existing coating.
“We conducted a visual inspection as well as mil thickness readings and scratch testing,” Porco says. “In many areas you could easily scrape off the degraded coating with your finger.”
As the scope of the project revealed itself, it became apparent that all the existing coating would need to be removed—a process that involved more than just simple power washing. Custom Coatings was selected to manage the entire job—from removal of the existing coating to recoating with NeverFade. “We reached out to a couple of other contractors, but due to the complexity of the coating removal process, they wouldn’t touch the job,” Porco says. “Custom Coatings was ideally suited for the task.”
Custom Coatings is known for providing a range of commercial services throughout the southeastern United States, including expert sealing, restoration, and high-tech coatings for the entire structure, from roof to basement.
“We had successfully completed a prior roof coating removal and replacement project for the Department of Public Instruction, so there was a level of trust that we would also be successful with this job as well,” says Joe Brindle, president of Custom Coatings.
Draughn praised the project team’s dynamic, noting that everyone communicated well, worked well together, and responded quickly to concerns or issues throughout the project. “I couldn’t have asked for a better relationship, from start to finish,” he says.
Coating Removal Process: Eye on the Environment
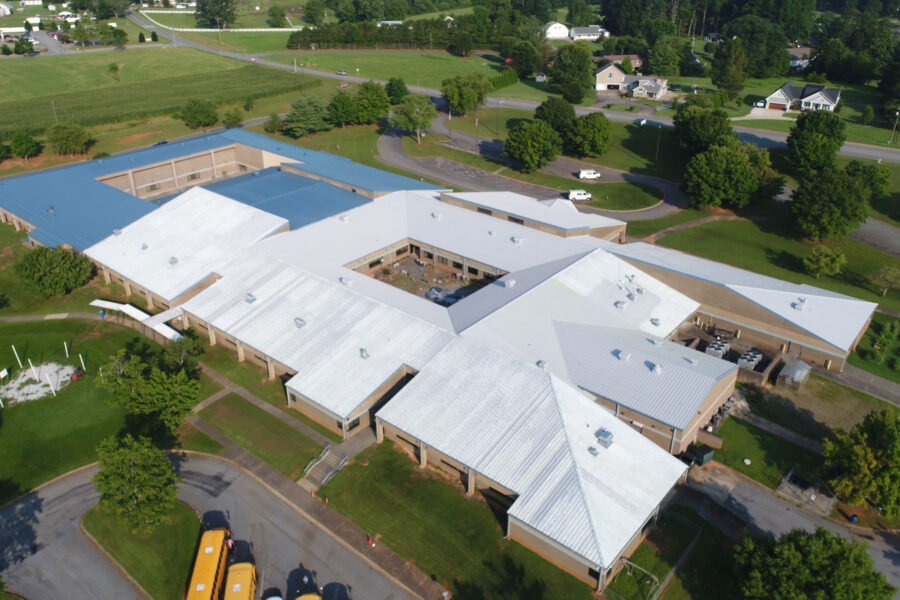
This in-progress photo shows the lefthand side of the roof with primer and topcoat applied. On the right, prep work is happening before primer is applied. Photo courtesy of APV Engineered Coatings
Brindle says proper removal of existing coatings is crucial for the ability of a new coating to perform as intended. Without it the new primer and topcoat will fail. During the company’s 30-plus years of experience, it has developed advanced coating removal methods—including the use of a proprietary paint stripping material—that are both effective and cleaner than other methods. The stripping material works quickly; during an initial test it completely removed a patch of existing coating down to bare metal in under 15 minutes.
“I discussed options for removing the existing coating with our engineering team and asked each bidding contractor how they would address it,” Draughn says. “The chemical stripping recommended by Custom Coatings won out over options like bead blasting for the cleanest, most efficient, and environmentally safe way to remove the paint with minimal impact on students and staff.”
As part of its standard waste disposal policy, the Custom Coatings team took care throughout the removal process to keep the stripping chemical and coating residue from contaminating the environment—a special concern because a farm with a pond was located adjacent to the school property. They set up a series of drainage pipes and collection bins across the 125,000-foot roof to capture the chemical and solid waste so it would not get into the storm drain system and groundwater. Once captured, all the waste was placed in a dumpster and disposed of according to local waste disposal regulations.
PVDF-Based Coating Extends Roof Lifespan
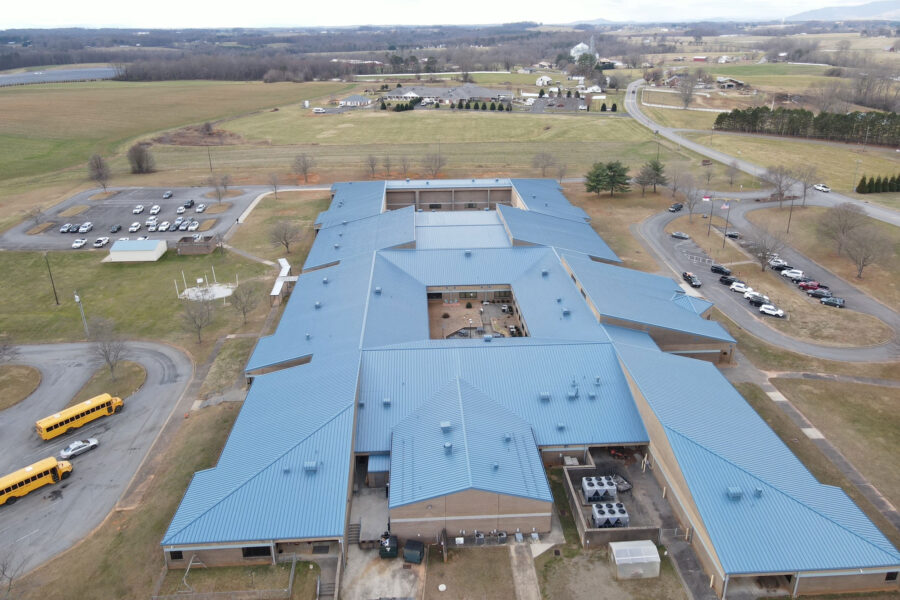
The school has a fresh, new look after the roof coating project was completed. Photo courtesy of APV Engineered Coatings
After stripping the old paint from the roof, the Custom Coatings team thoroughly pressure-washed the entire surface to ensure no paint remover or residual materials remained. Then they sprayed a coat of APV’s W-1650 Bonding Primer at a thickness of 1.5 to 2.0 mils. The primer is designed to adhere to tough surfaces, including metal and pre-coated metal. Its water-based, low-VOC chemistry provides early water resistance, protects against corrosion, and applies with a smooth, uniform finish for optimum aesthetics.
Next they spray-applied two 2.5 to 3.0 mil layers of NeverFade Metal Restoration Topcoat in a custom-tinted blue color to perfectly match the roof panels’ original factory finish. Engineered for coated or uncoated ferrous and non-ferrous metal surfaces, the topcoat resists the harmful effects of UV degradation like fading, erosion, and chalking. It safeguards against salt spray and corrosion, protects against a wide range of abrasions, and has exceptional resistance to algae, mold and fungal growth, dirt pickup, and stains. It also is water-based and low in VOCs, meeting SCAQMD Rule 1113.
NeverFade Coatings contain Kynar Aquatec®, a polyvinylidene fluoride (PVDF) resin with super-strong carbon-fluorine bonds that do not break down under exposure to the elements, thus resisting the film erosion common with exterior-grade, acrylic-based latex coatings. When exposed to UV energy and environmental stressors, the additives, pigment, and resin in latex coatings break down, creating a chalky residue. Eventually the chalked coating wears away from the substrate—or is washed away by rain, wind, pressure washing or cleaning—until the coating film is gone and no longer protects the substrate. In addition, the chalky residue changes the coating’s surface energy and serves as a food source for mold and mildew growth, which further degrades a building’s appearance and creates cleaning and maintenance problems.
Kynar Aquatec also resists fading. It has a 20-plus year demonstrated record of performance in extreme conditions, allowing APV to offer a 15-year product-and-labor guarantee that the coating will not fade by a Delta E of five or higher. Transferable to future building owners, the guarantee is unique to the architectural coatings industry.
“For decades architects have trusted the long-term, fade-resistant performance of Kynar 500® solvent-based finishes, which are baked onto metal surfaces of exterior building products like aluminum doors and window frames at the factory,” Porco says. “Today Kynar Aquatec allows specifiers to get similar performance in a water-based resin formulated for field applications.”
Ensuring Quality at Every Step
Quality assurance was top of mind throughout the four-month project, which took place primarily during the school’s unoccupied summer months. Even before the job started the APV/Custom Coatings team conducted multiple installation mockups to test coating adhesion. During installation the team did adhesion testing and x-cut tests after each coating layer was applied. At the end of installation they inspected the coated roof, checking mil thickness to ensure the job complied with the terms of APV’s guarantee. Because the paint removal process caused some sealant degradation, the Custom Coatings team also replaced those sealants, re-waterproofing the entire roof, then coated over the sealant.
The project was Custom Coatings’ first time using NeverFade Coatings, and the company has since become a NeverFade Certified Applicator. The certification process includes special training to learn about the chemistry behind the product, details around pre-job testing, color matching, application mockups, on-the-job troubleshooting, and post-installation quality assurance—all steps that give customers the confidence that NeverFade will perform throughout its guaranteed life cycle.
“We’ve worked with other fluoropolymer coatings before, but NeverFade is by far the best,” Brindle says. “It’s easy to use, easy to spray, and has a phenomenal finish that looks just like a new, factory-coated metal roof.”
Draughn adds that between the performance of NeverFade and the skills of the Custom Coatings team, the roof coating project met the goals set out at the start. “We’re very pleased with the results. The coverage is impeccable, and it looks great all around.”