Story at a glance:
- Compared with similar insulation types, polyisocyanurate (polyiso) insulation has the lowest embodied energy according to their EPDs.
- Polyiso is manufactured from a chemical reaction involving substances associated with adverse health outcomes in exposed workers.
- The high R-value of polyiso falls significantly at temperatures below 50℉.
More than 70% of all commercial and residential buildings in the US and Canada are insulated with polyisocyanurate (polyiso). This synthetic, foam-based material performs well as continuous insulation on a rooftop and in a building’s walls.
Polyiso’s environmental product declaration (EPD) states this insulation has low embodied energy. Does this mean it’s a sustainable material?
Let’s explore how polyiso is made, used, and disposed to answer that question.
What is Polyiso Insulation?
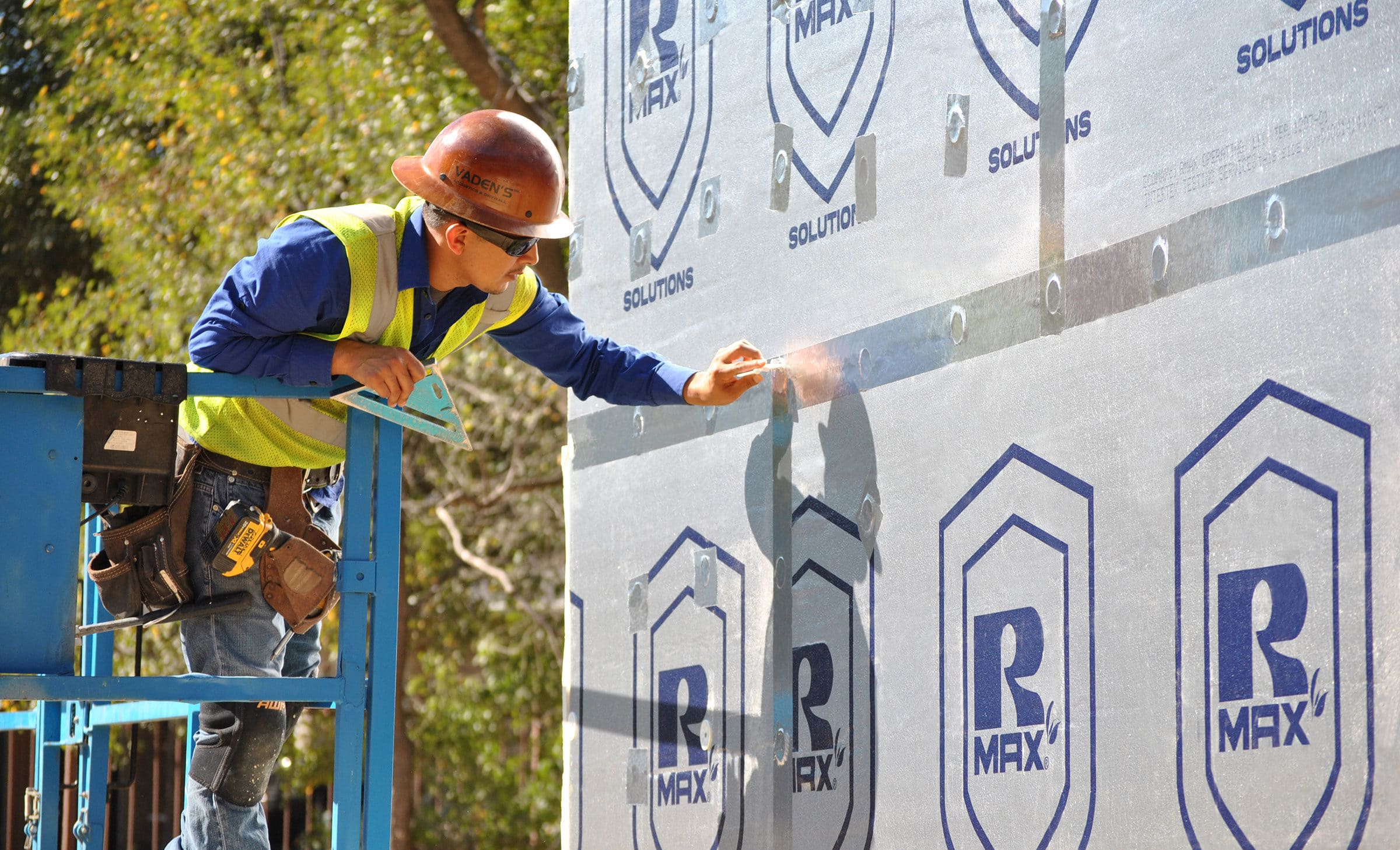
Photo courtesy of Rmax
According to Rmax, a leading manufacturer of polyiso, polyisocyanurate (polyiso) is a closed-cell, rigid, foam-board, continuous thermal insulation used in roof, wall, ceiling, and other applications in commercial and residential buildings.
How is Polyiso Made?
Polyiso is made from a chemical reaction between methylene diphenyl diisocyanate (MDI) and a polyol with the fossil fuel-derived pentane acting as the blowing agent. Compared to other polyurethane foams, polyiso has a much higher MDI-to-polyol ratio. There are documented cases of workers using MDI developing asthma or lung cancer.
According to the Polyisocyanurate Insulation Manufacturers Association, tris (2-chloro-1-methlyethyl) phosphate [TCPP] is commonly used as the flame-retardant chemical in polyiso. TCPP is considered a potential carcinogen, and has been banned for use in certain products in some US states.
Benefits of Polyiso
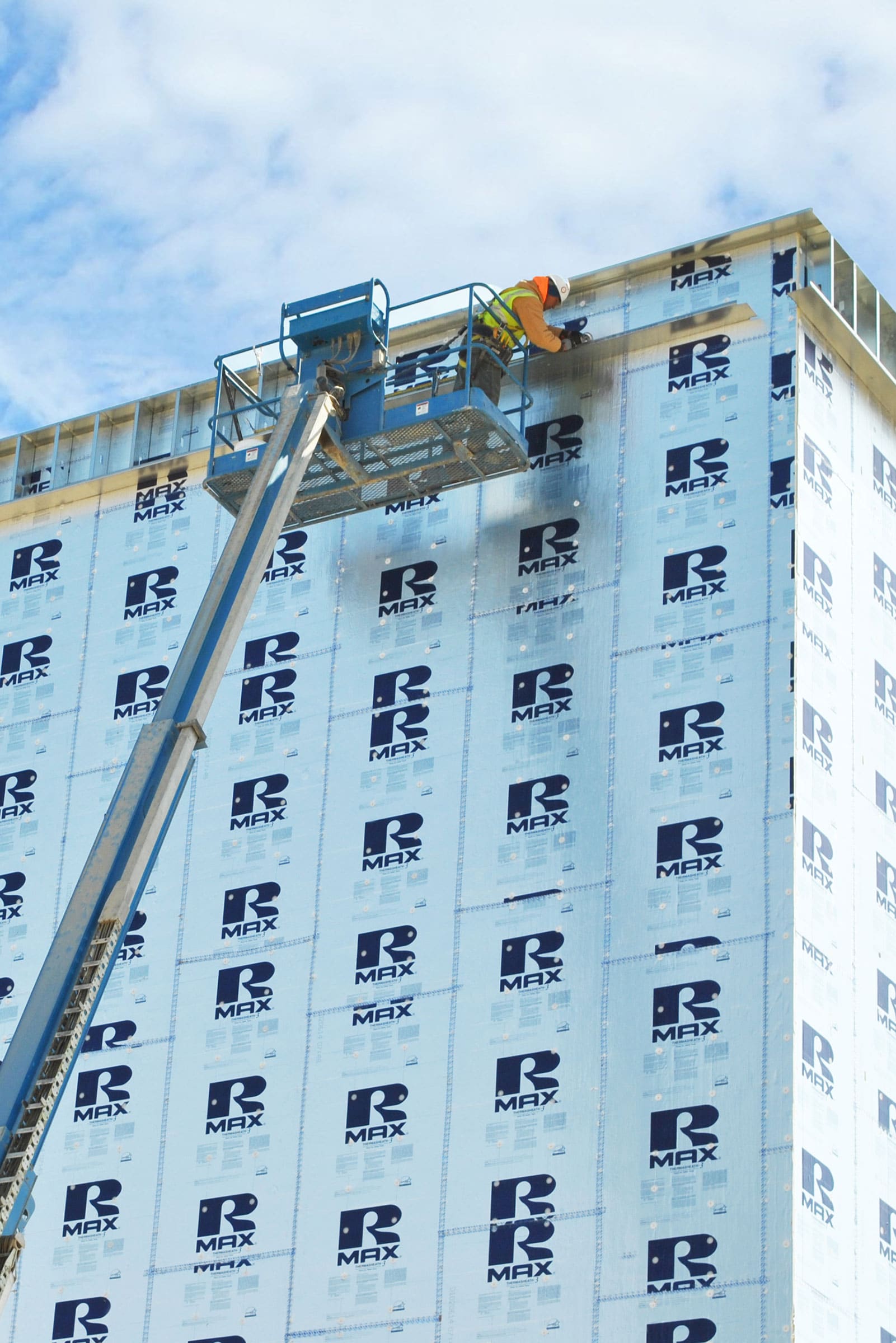
Polyiso remains the first-rate choice for wall applications, with an R-value of 6.5 per inch and a service temperature of 250Âş Fahrenheit. Photo courtesy of Rmax
Here are some of the benefits of polyiso:
- A higher R-value per inch compared to other insulation materials
- Low global warming potential
- Low embodied carbon
- Lower installation costs per R-value
- Minimizes space, material, and labor requirements
- Low water absorption and low vapor transmission
“With an R-value of 6.5 per inch, polyiso’s thermal properties surpass other rigid foam plastics by 20 to 70%, making it a clear choice for continuous insulation—a must for any sustainable project, given that HVAC costs often make up the vast majority of a building’s energy bill,” Greg Fantin, vice president of marketing at Rmax, previously wrote for gb&d.
As a type of continuous insulation, polyiso meets stricter building code regulations designed to eliminate energy inefficiency due to thermal bridging. “Continuous insulation requirements, which are increasingly prescribed by building codes, require that insulation is consistent across the entirety of a structure, lest thermal bridges—gaps in a building’s envelope caused by conductive surfaces like wall studs and cladding—allow heat to flow in and out, lowering occupant comfort and raising energy bills. Simply put, utilizing continuous insulation on a rooftop but not a structure’s walls would be like putting a plastic lid on an icebox made of wood. It would be an ineffective product,” says Technical Vice President Laurie Hill of Rmax in an earlier article for gb&d.
“Contrary to popular belief, polyiso is also highly moisture-resistant. Often when employed in roofing applications, polyiso utilizes less expensive paper facers that have been criticized for their poor moisture resistance. But this is only because, in these instances, roofing membranes encapsulate the polyiso, acting as their own air and water barriers. When transitioning to wall applications, foil facers are often used instead, which effectively prevent water and vapor absorption,” Hill added.
Disadvantages of Polyiso
The major disadvantage of polyiso is its R-value (5.6/in.) drops by up to 28% at very cold and hot temperatures, just when it’s most needed. This is due to pentane as the blowing agent. Pentane replaced ozone layer-destroying CFCs to serve this function, but resulted in a major performance deficiency.
According to PIMA’s EPD, it takes approximately 50 L of water to make one square foot of polyiso that’s 3-inch thick. The final value varies depending on the facers used. The total amount of water used for large, multi-storied buildings (over 5,000 sq.ft.) with roof, wall, and ceiling polyiso can surpass hundreds of thousands of gallons.
How Sustainable is Polyiso Insulation?
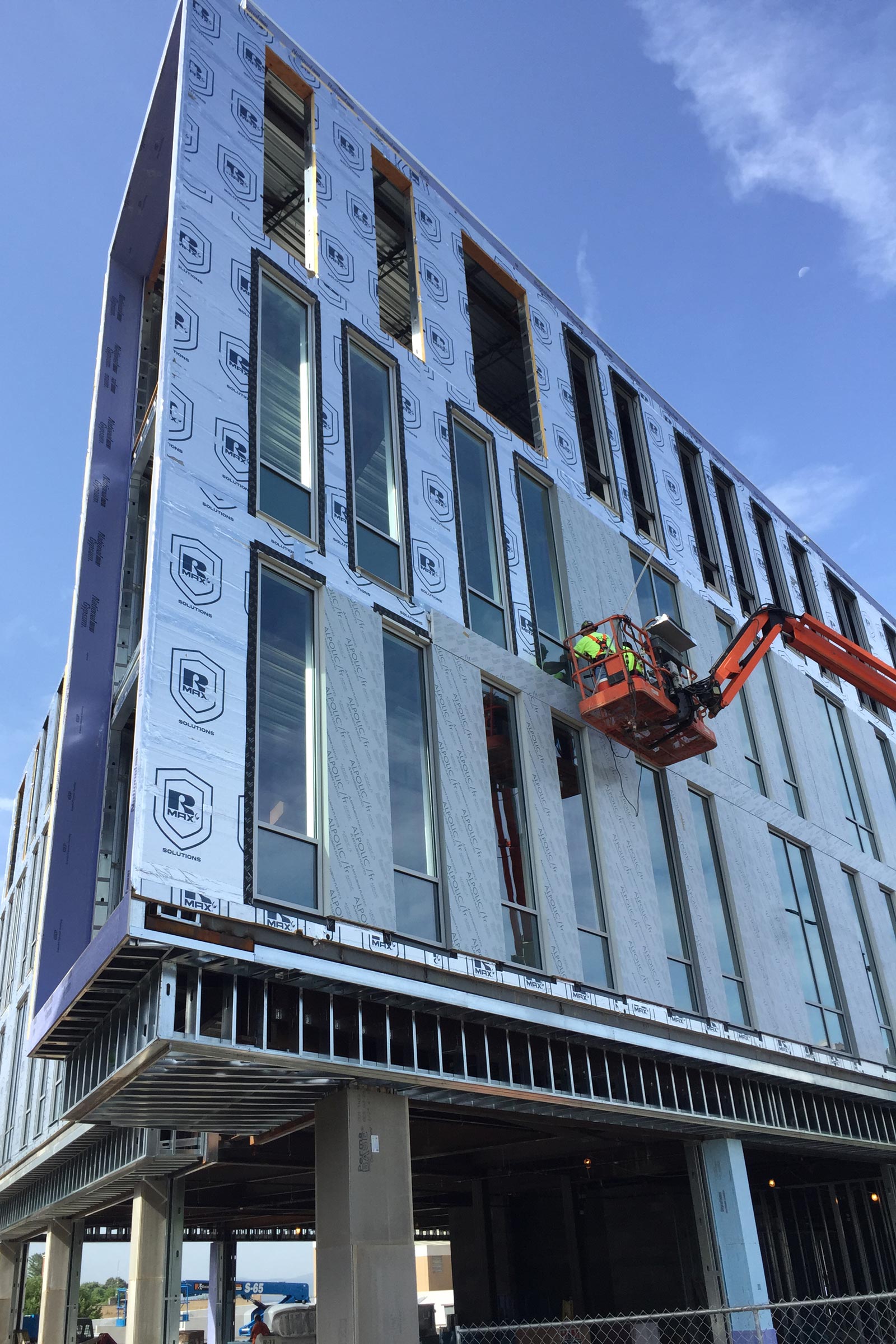
Polyiso is fast becoming a preferred material for sustainable building and design, considering it simplifies the construction process and has other economic and environmental benefits. Photo courtesy of Rmax
Polyiso has a high R-value at moderate (50-75degF) temperatures and a low global warming potential. It also has low embodied energy. These are important sustainability elements. However, in a world of prolonged heat waves and polar vortices due to the climate crisis, polyiso alone won’t meet high standards for building insulation when people need them the most.
Negative effects on worker’s health during polyiso’s manufacture detract from its sustainability. Since polyiso is a thermoset plastic, it cannot be re-melted and recycled to form new products. Reuse is the only way polyiso can achieve long-term sustainability and there are some companies that coordinate these efforts.