Story at a glance:
- Specifying the right protective floor coating means business—including repeat business.
- With cutting-edge performance and lower VOC and odor, there’s never been a better time to go ultra-low.
- Leaders at Covestro explore a concrete solution to sustainability in the built environment.
Any experienced architect knows a variety of products exist for any given application in the built environment with different price/performance ratios. One must understand the customer’s needs for a given space and manage the project within those desires with both an eye to the short-term budget and application requirements, as well as the longer-term sustainable operation and maintenance targets. Misjudge these requirements, and you may sacrifice company image, client confidence, and repeat business.
These tenets of project management are certainly evident in the world of protective concrete floor coatings. Specify a floor coating system with poor initial or long-term aesthetics and durability, objectionable odor, or that is disruptive to occupants or other trades for long periods, and the client won’t be happy. However, today’s customers are concerned with far more than how something looks on day one. And they are often under social, cultural, or regulatory pressure for their facility to be as sustainable as possible, as future-proof as possible, and as healthy as possible for the people who occupy their spaces.
In the past sustainability efforts were primarily driven by regulations from above. Today the push is coming from below—from architects, specifiers, clients, and material manufacturers with a new understanding that the ways we build have environmental consequences—and that environmental consequences affect every person on the planet. This understanding is driving excellence and evolution in concrete floor coatings, one that judges materials not merely by their cure times and initial looks, but by what they emit, how they are sourced, the energy used to make them, and how they affect the built and natural environment over the long haul.
In other words, the adoption of environmentally friendly technologies and materials is no longer a hurdle to overcome, but an opportunity to expand the potential of the built environment as a lever to create a better future through intentional design and execution. By not just meeting but exceeding the existing regulatory standards, we can not only fully serve our customers; we can also meet their desires for a safer work environment and planet.
The hard part is already done with increasing options for more durable yet lower VOC polyurethane floor coatings. Low-VOC, high-performance polyurethane-based concrete floor coatings are widely available in the market today, and they look and perform just as good as traditional coating systems. So why are they not specified into every flooring application already? The reasons are often linked to past behaviors—habit, miscalculation of total cost, and lack of awareness of technology advancements.
Cost
It’s true that, gallon-for-gallon, polyurethane floor coatings still carry about a 30% price premium over conventional epoxy or acrylic floor coatings. This percentage represents a major improvement over a few years ago when the premium was 50%, and the price gap is expected to narrow even further, but still, cost always matters.
While the pricing of conventional products might seem attractive at first glance, once you factor in durability over time—the life cycle cost—the argument for using a higher performance option becomes more evident. To that end, ultra-low VOC polyurethane floor coatings are not only better for the environment, but they also last three to four times longer than many typical floor coating products. If we’re looking for something beyond a band-aid solution for our concrete floor spaces that considers the future, the math is simple—high-performance polyurethane floor coatings offer roughly 300% more value for only a 30% increase in price. When an architect or specifier is considering their fiduciary responsibility to their client, it is important to consider the initial costs, as well as the owner’s longer-term operation and maintenance costs.
Winning on both price and performance would be enough to convince most people that ultra-low VOC polyurethane products are the floor coatings of choice. But the picture looks even more favorable when we start factoring in other sustainability externalities.
People
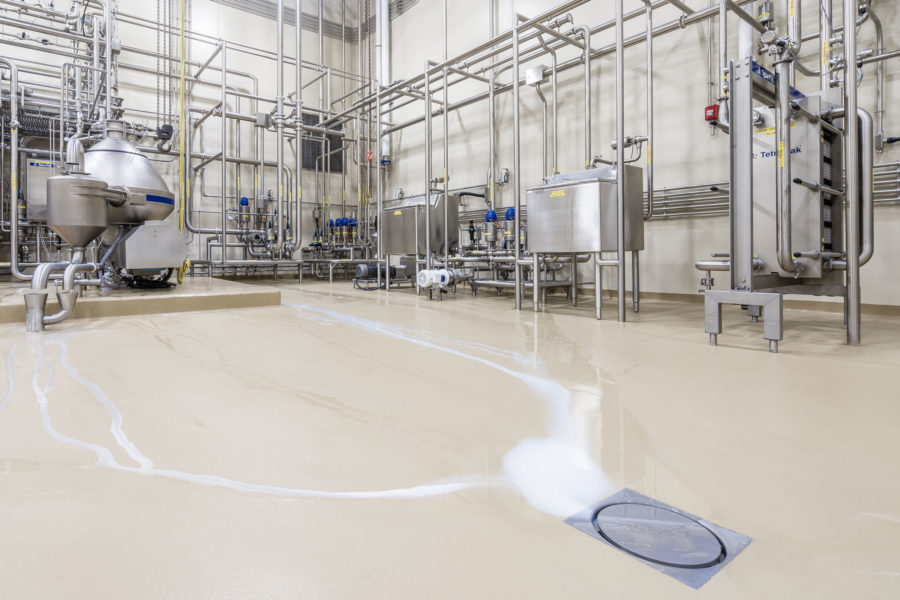
Excellent chemical and stain resistance allows for use of polyurethane coatings in demanding industrial applications. Photo courtesy of Covestro
People are the reason we make buildings in the first place, and city dwellers now spend around 90% of their time indoors. Today building envelopes are built tighter, with less air exchanges to maximize energy savings. But with new approaches come new considerations. For one, when you create a more sealed environment, you also need a strategy for what can be released into the indoor environment. Less air exchanges mean compounds that go into building products can linger inside the facility. That means the stakes of introducing harmful materials into modern buildings are higher than ever.
VOCs have well-documented negative effects on humans. Single exposures can create eye, nose, and throat irritation as well as dizziness, headaches, and fatigue. Long-term effects include respiratory disease, heart disease, and cancer. And with a wide range of reaction levels in people, it’s hard to even estimate what “safe” levels of VOCs would be. The EPA estimates avoidable costs associated with indoor air pollution amount to more than $100 million every year.
It’s just basic math—the more VOCs there are in a coating product, the longer they hang around, smelling bad and causing a possible reaction in building occupants. The longer spaces remain out of service to enter, the unhappier clients get. Ultra-low VOC polyurethane coatings cure with less odor, enabling quicker return-to-service in spaces and lower concentrations of VOCs into the air.
Environmental Concerns
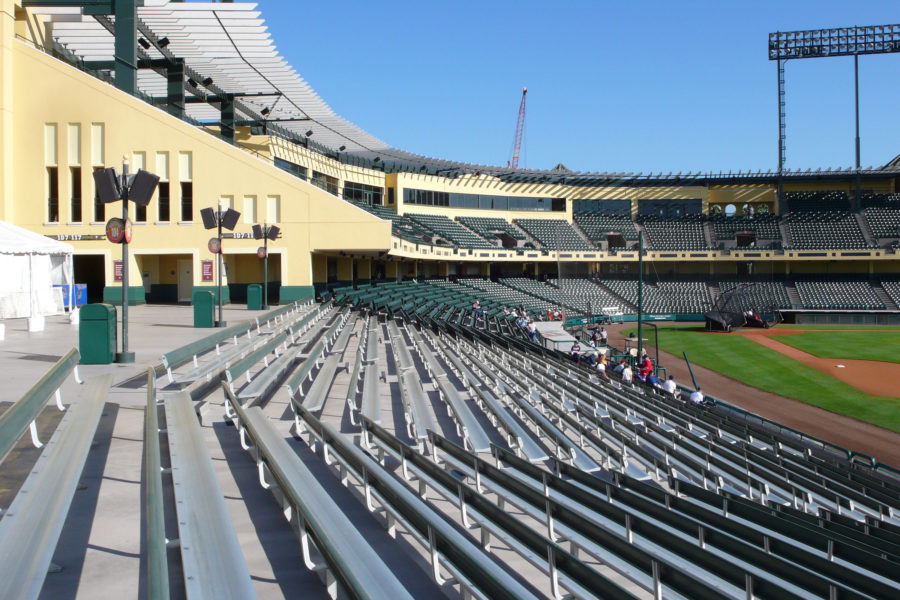
Weather stable polyurethane coatings protect exterior stadium floors for the long run. Photo courtesy of Covestro
When VOCs are released into the atmosphere where they can mix with nitrogen oxides (released by vehicles and power plants) in the presence of sunlight, the two combine to form ozone. So, on sunny days, areas with both VOCs and cars tend to experience high levels of ground-level ozone and the resultant smog, which can irritate the eyes, nose, and throat as well as exacerbate asthma symptoms and other lung issues.
The EPA’s concern about VOC emissions from the use of coatings and the resulting ozone led the agency to start regulating VOCs at the federal level in 1998 as part of the Clean Air Act. While the regulations moved the needle—it’s estimated that VOC emissions have been reduced by more than 100,000 tons per year—we still have levers we can pull to further reduce ozone and smog from our cities.
Regulation and Compliance
Voluntarily reducing VOCs is clearly the right thing to do, but the government isn’t leaving it up to individuals. Progressively stricter state and federal regulations on VOCs are expected over the coming years, with several individual states and regions leading the way by already enacting tighter regulations.
The California Air Resources Board (CARB) and the South Coast Air Quality Management District (SCAQMD), both operating in California, have enacted the strictest pollution control requirements in the nation. Their rules govern “anyone who supplies, sells, markets, offers for sale, or manufactures any architectural coating…as well as any person who applies, stores at a worksite, or solicits the application of any architectural coating within the district.” The simplest way to not have to worry about the myriad of regulations is to specify an ultra-low coating solution that meets or exceeds even the most stringent national or regional requirements.
That’s one more benefit of ultra-low VOC floor coatings. Many products that call themselves “low-VOC” products are formulated primarily with the aim of complying with the law, rather than reducing VOCs to their minimum level. In places where regulations limit VOCs in coatings to 50 grams per liter, there are products being sold as “low-VOC” in the vicinity of 49 grams per liter. However, true ultra-low VOC products are down around 10 grams per liter or less. Additionally, VOC exempt solvents are often used instead, which is allowed by current regulations. VOC-exempt solvents are organic compounds that are exempt from restrictions placed on most VOCs because they do not contribute to ozone or ozone depletion. However, there is new activity by regulatory bodies that seeks to delist several of these solvents due to their detrimental health effects rather than environmental effects.
Scope 3 Carbon Emissions
Today’s architects are all too aware of limitations clients are putting on Scope 1 and Scope 2 carbon emissions (emissions from direct production and indirectly via energy consumption). But Scope 3 emissions are some of the hardest for architects to get their arms around. Scope 3 involves the carbon footprint of all third-party materials, excluding energy itself. That means finding vendors who are themselves using energy-efficient means of producing their goods and services.
The solution here goes back to the durability-over-time issue discussed earlier. When a coating lasts four times as long, you need to apply it four times less, using four times less product. On a per-gallon basis, ultra-low VOC polyurethane coatings take about the same amount of energy and release similar quantities of CO2 in production as conventional coatings, but the higher durability means you reduce Scope 3 emissions on those materials by roughly 75% over the life cycle of a commercial floor space.
Field-Tested Technology
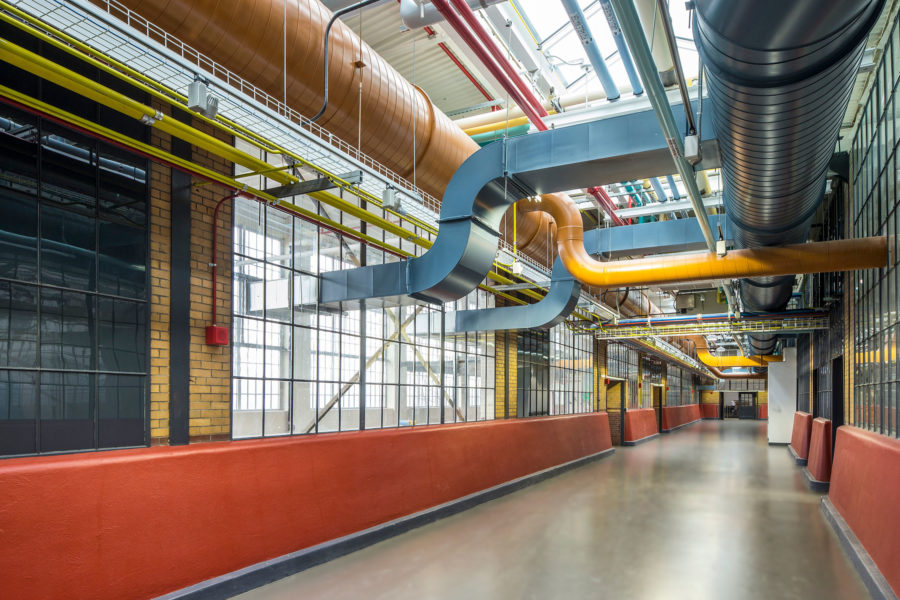
The Energy Innovation Center’s central “racetrack” floor is enhanced with ultra-low VOC polyurethane floor coatings. Photo courtesy of Covestro
It’s natural to be concerned about new technologies and materials. Fortunately polyurethane-based concrete floor coatings aren’t theoretical projects just emerging from the lab. These coatings have proven performance and are widely used in commercial and industrial spaces by some of the most forward-thinking leaders in the environmental building movement. It took some courage for the pioneers to go first, but their commitment means now you don’t have to take a manufacturer’s word for it; you can see it working for yourself.
If you’d like to walk around on one of these flooring applications, you can do so at one of my favorite buildings—the Energy Innovation Center (EIC) in Pittsburgh. Originally built as the Clifford B. Connelly Trade School, the building is 172,000 square feet of Classical Revival and Art Deco, listed on the National Register of Historic Places. Built in 1929, the school it housed closed in 2004. It sat empty for seven years until, in 2011, Pittsburgh Gateways undertook a renovation with the intent of creating an educational center for high-demand skilled trades organized around curricula focused on green energy and sustainability. Naturally its green mission extended to the techniques and materials used in the renovation, and developers set an ambitious goal of achieving LEED Platinum certification. However, given the building’s landmark designation and the desire to retain historic tax credits, this objective was no easy task.
In the end, the architects (DLA+ Architecture and Interior Design) managed to preserve the character of the school while updating it with the latest innovations in green design, including absorption chillers, efficient lighting that maximizes daylight without glare, and a host of automated systems that boost efficiency. The EIC was only the fifth renovation in Western Pennsylvania to achieve LEED Platinum, and it managed to retain a $6.5 million tax credit. It won the Engineering Society of Western Pennsylvania’s 2014 Sustainability Project of the Year and may be the only LEED Platinum structure that qualifies for historic tax credits.
Low-VOC polyurethane floor coatings were used throughout the building on both concrete and wood surfaces, but the best example of their combination of effectiveness, durability, and green factor is in the “racetrack”—a common space that loops around the interior of the main floor.
After 80 years of heavy use, the concrete floor was cracked and spalled, and significant concrete repair work was needed to create an acceptable surface to coat. Once major flaws were addressed, a cementitious overlay was applied to the entire floor, which was used to level the floor and prepare it to accept a high-performance coating system. Next, a 100% solids epoxy primer was applied to promote long-term adhesion, and a two-component (2K) waterborne polyurethane topcoat was selected by the EIC design team to protect and seal the surface. This 2K waterborne polyurethane coating offered high durability, ultra-low VOC, and low odor, with excellent sheen retention and workability. Two coats of the 2K waterborne polyurethane floor coating were applied as the protective clear topcoat to the floor surface to a wet film thickness of 6 to 7 mils.
The waterborne floor coating technology was available in a satin finish, which was a desired design attribute from the owners since they wanted to retain the neo-industrial aesthetics throughout the building, as well as reduce glare from the clerestory running the length of the floor space.
Impact You Can Feel Good About
We all want our work to reflect our values. And increasingly those values have a lot to do with sustainability and doing what’s right for people, planet, and profits. Humans need the natural environment every bit as much as they need the built environment. There was a time when specifying sustainable coating options required making sacrifices on performance or cost, but with today’s ultra-low VOC, high-performance polyurethane floor coatings, the choice couldn’t be more concrete. Higher durability is achievable with waterborne, ultra-low VOC coatings that, amortized over their full lifespan, are far cheaper than the conventional (dare I say stinky) alternative.