With billion-dollar weather disasters on the rise in the United States, resiliency and sustainability are on the minds of builders and homeowners alike. In 2020 alone, there were 22 events that sustained over $1 billion in damage and rebuilding efforts, including severe storms, flooding, winter weather, tropical cyclones, wildfires, and more.
This number far surpassed the previous record: 16, occurring both in 2011 and 2017. With the threat of severe weather in mind, how can builders address homeowners’ concerns about the resiliency of their homes while also contributing to the health of the planet?
The answer lies in a product portfolio approach that emphasizes improved sustainability and resiliency. Builders must undergo a shift in their mindsets. They can choose from a wide variety of products manufactured by several manufacturers or a portfolio of solutions sourced from one innovative supplier with a primary goal of increasing resiliency with sustainable building products.
Let’s dive into why sustainability and resiliency matter—and how approaches like LP Structural Solutions’ portfolio can help you build better.
What is resiliency?
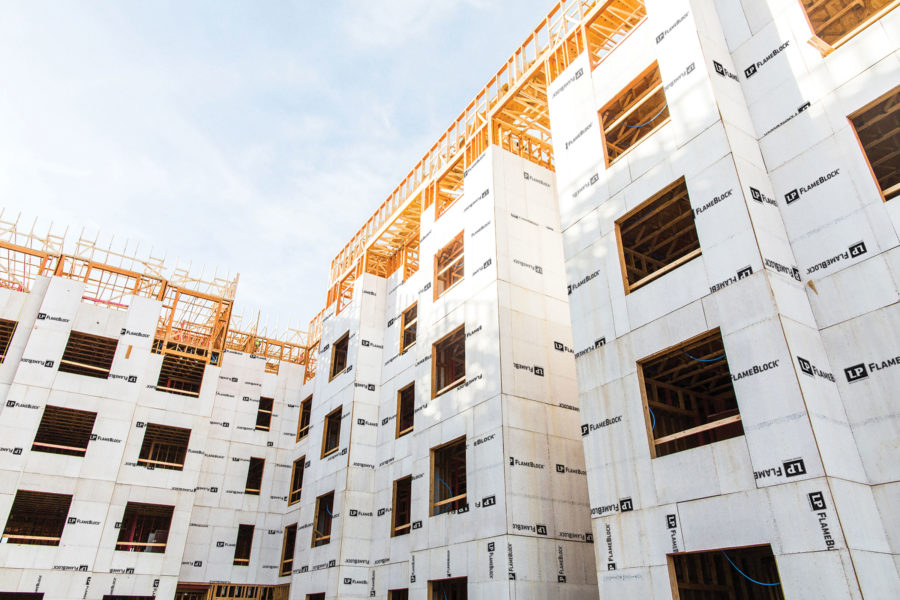
Photo courtesy of LP Structural Solutions
Simply stated, resiliency refers to the ability to stand up to adverse conditions. When it comes to buildings, we generally think of resiliency in terms of whether your build will stay standing—and that is certainly part of resiliency in the building industry. However, LP Building Solutions seeks to define resiliency a little more broadly.
LP manufactures products that are engineered to help a build withstand many types of unpredictability. This goes beyond weather events and includes other factors, such as ever-changing energy costs, repair costs, maintenance, and even the rigors of the jobsite and the build process.
How are sustainability and resiliency connected?
Sustainability is closely tied to resiliency, as weather disasters often lead to rebuilding efforts. When a build is more resilient, ideally only the most severe weather events may cause the need to rebuild. The original products used in the build are designed to stand up to severe weather events of many kinds, making it less likely that they’ll be wasted in a weather disaster.
Additionally, when building products can be made and sourced sustainably before they’re even installed, builders can be even more confident that their choices are contributing to a healthier planet.
How can my product choices make my builds more resilient and sustainable?
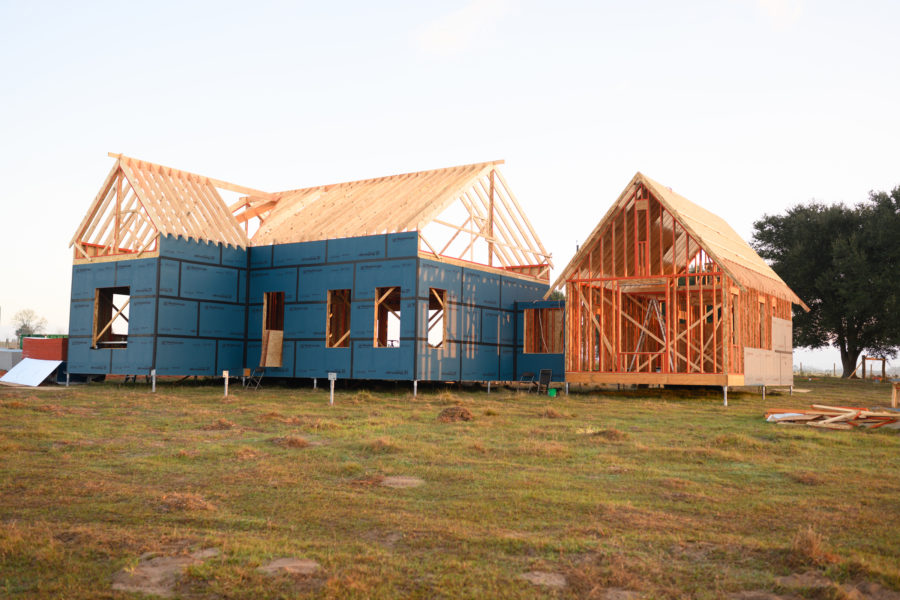
Photo courtesy of LP Structural Solutions
With this expanded definition of resiliency, a builder’s needs for their structures become clearer. Instead of simply requiring strength and stability, for example, a builder may need a product that diverts radiant heat and helps save on energy expenses. It may also require resistance to excess moisture in a particularly humid or rainy climate.
Choosing a product that addresses each of its outside threats can help increase the build’s overall resiliency. Keep in mind that what is needed varies widely depending largely on the climate in which it is built. A home in Miami, Florida, will require different precautions than a home in Sioux Falls, South Dakota, and a home in Phoenix, Arizona, will differ still in what is required. However, according to the National Oceanic and Atmospheric Association (NOAA), every state in the country has been impacted by a $1 billion weather disaster since 1980, so all geographies can benefit from more resilient construction.
That’s where the portfolio approach comes in handy. Because there isn’t a one-size-fits-all approach to resiliency, building with a portfolio allows you to choose the products that are most relevant to your build’s location. And because the products all come from one manufacturer, you can count on them to be engineered to be used together.
What is the LP Structural Solutions portfolio of products?
Designed to defend your build, the LP Structural Solutions portfolio is a collection of four core products that work together to make a build more resilient. While all four products do not have to be used at once, each is designed with consistency that allows them to complement each other and come together to withstand many different severe weather concerns.
- LP WeatherLogic Air & Water Barrier takes care of moisture threats for your builds, providing protection as a Structural I wall and roof sheathing system. It has an integrated water-resistive barrier bonded to the panel, and when edges are sealed with LP WeatherLogic Seam & Flashing Tape it helps create a tighter building envelope that meets Zero Net Energy (ZNE) requirements.
- LP Legacy Premium Sub-Flooring gives your structures a super-tough, moisture-resistant APA-rated sub-flooring with outstanding stiffness. LP Legacy sub-flooring boasts a lifetime limited warranty, which provides confidence for builders and homeowners alike.
- LP TechShield Radiant Barrier sheathing helps block radiant heat in the roof panel from emitting into a home’s attic, providing a solution for energy efficiency for years to come and possibly lowering HERS (Home Energy Rating System) scores.
- LP FlameBlock Fire-Rated Sheathing is evaluated to help meet code requirements and expedite the construction process. LP FlameBlock sheathing serves as a great solution for homes in areas where wildfires are a concern, such as wildland-urban interface (WUI) zones.
As you can see, the four products that make up the LP Structural Solutions portfolio all boast superior innovation that addresses many common sustainability and resiliency concerns, from structure and moisture to fire, heat, and energy costs. When you build, you can choose which will help each structure perform at its best and protect it from factors outside your control.
How does the LP Structural Solutions portfolio perform on the jobsite?
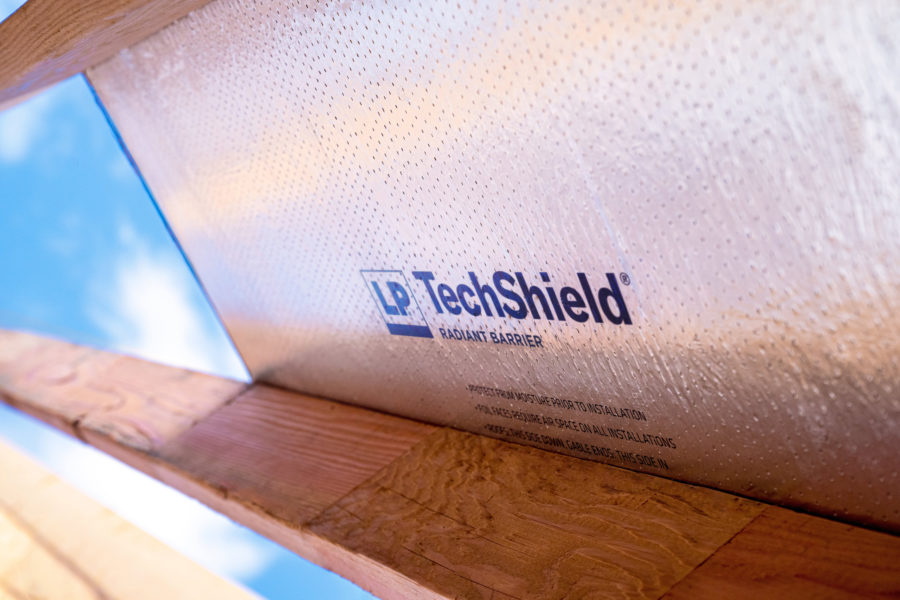
Photo courtesy of LP Structural Solutions
LP manufactures products that aren’t only resilient once they’re installed on the structure; they can stand up to jobsite conditions. Durability is the main factor that helps bolster the products’ resiliency on the jobsite. LP Structural Solutions products are highly engineered and designed to take advantage of wood’s natural strengths, beginning with wood strands arranged in cross-dimensional layers.
They are additionally reinforced with waxes, resins, and other technologies to build in even more strength, stiffness, and moisture resistance. Each product in the portfolio is designed to withstand the rigors of the job, ranging from accidental bumps to excess rainfall that may collect during weather delays.
Furthermore, with consistent dimensions the products complement one another and make it easier for builders to install them. This consistency also leads to less cutting, reducing scraps and waste. This helps you use the sustainable resources you have and avoid wasting both resources and money.
When you build with one manufacturer you’ll also have the support you need, whether you have an installation question or need to discuss the warranty.
How can I build more sustainably with LP products?
LP believes that “one of the greatest environmental opportunities we have is to ensure that the forest resources we rely on are managed sustainably.” As a leading manufacturer of engineered wood products, LP partners with the Sustainable Forestry Initiative (SFI) for forest management certification.
When you build with any wood products from LP, you can rest assured your products were sourced from within a 50–100-mile radius of their mill location. LP also ensures that all products meet environmental requirements of supply chain standards.
Ultimately, LP can help you build more sustainably because LP is dedicated to a healthy environment as we manufacture building solutions that align with the highest sustainability standards.
Can LP Structural Solutions help me meet sustainability certifications?
Because LP Structural Solutions products are sourced and manufactured sustainably, they are often able to help builders meet certifications for their builds, such as LEED certification and the WELL Building Standard. Additionally, select products may help you achieve net zero energy status.
Your build can earn LEED certification points for sustainable choices in several categories, one being material selection. You can earn one of four certification levels depending on the amount of points your build scores. Many SFI-certified products within the portfolio qualify under LEED rating systems. The WELL Building Standard helps foster environments that improve daily life across 11 foundational concepts; structures can be classified in one of three levels of certification.
With resiliency and sustainability at the heart of its portfolio of solutions, LP Structural Solutions is ready to help you start building better.