Story at a glance:
- Viega offers hands-on training and press technology credentials for tradespeople.
- Virtual trainings for engineers, contractors, and end users are also available.
- Press technology is growing in popularity in the US for its safety, efficiency, and durability.
Press technology is changing the way you join pipe in the field. Experts at Viega say press is more efficient, safer, and faster than traditional methods, but not everyone knows what’s possible with this technology yet. Fortunately Viega has a large training program with continued educational opportunities—whether you’ve been in the field for decades or are considering joining the industry for the first time.
“Training is one of the most important parts of what we do,” says Colton Henkowski, a Viega technical training consultant who trains contractors, engineers, and wholesale reps through in-person and online workshops. “If we have people out there just slamming fittings in and doing it incorrectly, that gives press a bad name and makes us look like we don’t sell the proper fitting for what they’re using it for when 99% of the time it comes down to how it was installed.”
Installation, he says, is simple once you go through a brief training to understand how press technology works. It’s also exciting.
What is press technology?
Press technology is the method of joining pipe using a specialized tool to create a permanent mechanical connection. Viega offers press fitting solutions that make installations on a variety of applications faster, safer, and more durable.
Press technology is growing in popularity in the US and has long been popular in Europe. This technology allows for the same reliable pipe connection every time, and MegaPress fittings have been proven to withstand up to a 9.2 level earthquake.
Why is training important?
- Students are introduced to Viega’s ProPress. Photo courtesy of Viega
- Demonstration of Viega ProPress. Photo courtesy of Viega
Henkowski worked as a pipefitter for 15 years before joining Viega. He has more than a dozen welding certifications. He often used Viega’s fittings in the field even before he joined the company.
“Working in the field, I’d worked with every single press fitting that we sell, and I installed them. But then coming to Viega and being trained to be a trainer, I realized there were a lot of little missteps I had been making,” he says. “I saw the benefit of training right off the bat, because even somebody seasoned like me who’s been doing it a long time, there’s a lot of little things you miss if you’ve never been shown the right way to do it.”
What are some things even the experts can learn?
When Henkowski began training to become a trainer, he was surprised to learn about some of Viega’s capabilities—like the ability to rotate.
“I didn’t know you could rotate any of the fittings and repress them after you’d already pressed them,” he says. “If I didn’t like it or it looked weird I was cutting out fittings when I could have just made a slight adjustment and moved on with my day.”
What training does Viega offer?
- Viega offers in-person training in a classroom setting. Photo courtesy of Viega
- Viega offers hands-on learning experiences from its location in Nashua, New Hampshire. Photo courtesy of Viega
Viega offers a variety of training opportunities, and often people will train in the field. Viega offers a credential for those who want to get field-verified by Viega, asserting that they understand how to install products like ProPress or MegaPress. A quick reminder on each technology:
ProPress: Viega’s flagship begins with the ProPress System, available in sizes of one-half-inch to four inches. The ProPress system for copper tubing can be used on things like potable water, heating and cooling glycol lines, and even compressed air.
MegaPress: The MegaPress system is available half-inch up to four inches, and every Viega MegaPress fitting has Smart Connect® technology to help easily identify unpressed connections. MegaPress is made for black iron and steel pipe and stainless steel pipe systems.
Viega has a dedicated training team—something unique in the press industry, Henkowski says. “We have seven people who can offer different types of training. We do in-person trainings where people can spend the whole day with us. It’s an eight-hour course on anything they could possibly want to learn about ProPress, MegaPress, and PureFlow.” Viega PureFlow PEX fittings, manifolds, and tubing are also easy to install and engineered to help reduce water waste in potable water systems.
Henkowski says the trainings provide installers with hands-on experience and an opportunity to ask questions on the spot.
What about online opportunities?
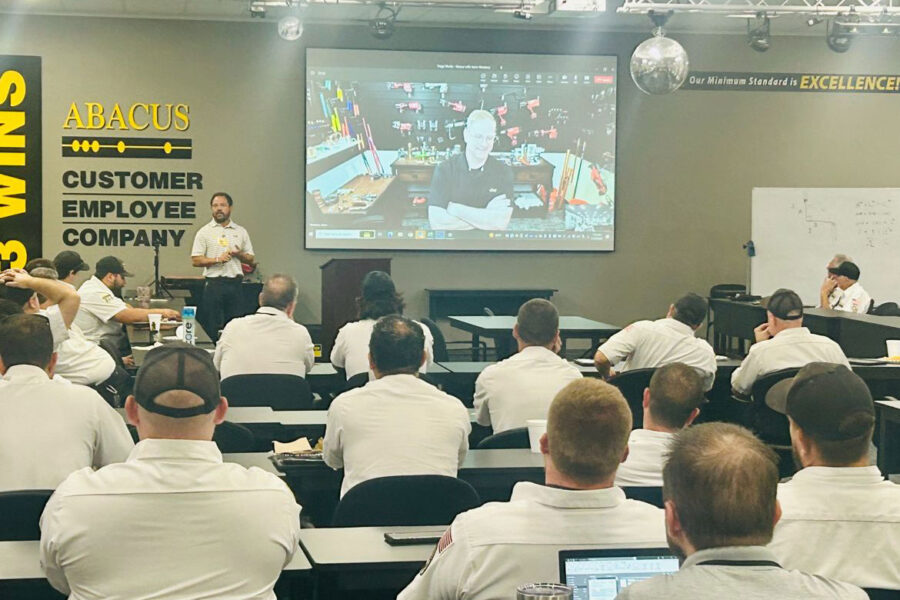
Students attend a Viega Works session. Photo courtesy of Viega
If the pandemic taught us anything it’s that we can learn and stay connected remotely, too. As such Viega offers a virtual training platform called Viega Works. Each video session runs approximately 30 minutes to an hour, with insightful training to help engineers, contractors, and end users with anything they need—from understanding a product for the first time to installing something they haven’t installed before.
Viega’s expert technical consultants troubleshoot, answer specific questions, explain products and processes, and provide hands-on demonstrations. The sessions are designed in response to customer requests and continue to be popular since launching in late 2020. “I believe last year we did 7,000 virtual trainings. That means we reached at least 7,000 people, but most of the time there’s more than one person in the group,” Henkowski says.
How has the industry changed?
“The industry has changed so much. When I first started I was doing things a lot differently. Most of my jobs were solder weld or thread,” Henkowski says.
Today the industry is moving toward press, he says, with about 20% press technology in America compared to 80% in Europe. The first established press fitting patent was developed in 1960, and it’s been widely used there since. Viega introduced press technology in America in the late ’90s.
Change takes time, but Henkowski has seen firsthand how people come around to better processes once they see the benefit. “I’m a union pipefitter, and when welding first came out all the unions thought welding was horrible. They thought it was going to kill the trades. Now if you look at union workers, their bread and butter is welding,” he says.
He expects people will also be excited once they get to experience more press technology hands-on.
What does the future hold?
Viega believes the future is bright for press technology. They are also working very hard to educate tradespeople from the beginning—from apprenticeships and even earlier. They recently attended a job fair at a high school to show students what other skilled trades are out there, for example.
“The younger generation is definitely tied into it,” Henkowski says. “Long gone are the days when you go to work and kill yourself all day, working super hard to make a basic living. We’re moving in the direction of how do you make the connection simpler and gain your knowledge in other spots and understand your mechanical systems? You can take your skills to another level where you’re using more mind power than just brute strength to get these jobs done. The whole industry is going in that direction.”