Story at a glance:
- Demand for carbon-neutral materials continues to be on the rise.
- Still, most buildings depend on global supply chain logistics and manufacturing processes.
- New housing is a challenge worldwide, but a disconnect between material systems and the local environment causes poor building performance.
The magnitude and urgency of climate change is affecting every corner of our world. In architecture, concerns about embodied carbon and lifetime energy use have yielded a host of proposals for making our buildings greener. In particular, there has been a growing interest in the use of local and renewable materials for constructing buildings.
But even as the demand for carbon-neutral materials grows, most buildings (like any other consumer product) continue to be dependent on global supply chain logistics and manufacturing processes. Although sustainable certification programs like LEED and Living Building Challenge are becoming more commonplace in our industry and encourage the use of local materials, a vast majority of buildings are fabricated from resources originating in radically diverse locations. The result? A large carbon footprint and the loss of economic benefit for local communities.
One sector where this challenge is particularly pressing is the development of new housing across the globe. Over the past century, a steady flow of industrially produced materials, along with the desire for a higher social status and quality of life, has caused a sea change in how communities build their homes in many parts of the world. A “one-size-fits-all” approach to construction, shaped by globalized, market-driven development, often creates a mismatch between material selection and place-specific climactic requirements.
A ‘one-size-fits-all’ approach to construction, shaped by globalized, market-driven development, often creates a mismatch between material selection and place-specific climactic requirements.
As a result, we might find massive concrete homes in tropical climates or wood frame construction in areas prone to extreme heat and fire. This disconnect between material systems and the local environment can cause poor building performance, increasing energy consumption for things like air conditioning, or contribute to a structure’s vulnerability to extreme weather events like fire or hurricanes.
As populations increase alongside global temperatures, sustainable solutions for housing are becoming ever more critical. This is made even more urgent as international manufacturing and supply chains continue to be disrupted and fuel prices reach record levels. Rather than depend on new technologies or automation for solutions, we might also consider returning to principles found in older forms of construction that prioritize minimally transported and processed materials. In short, we could look back to move forward.
Niamey 2000, Niamey, Niger
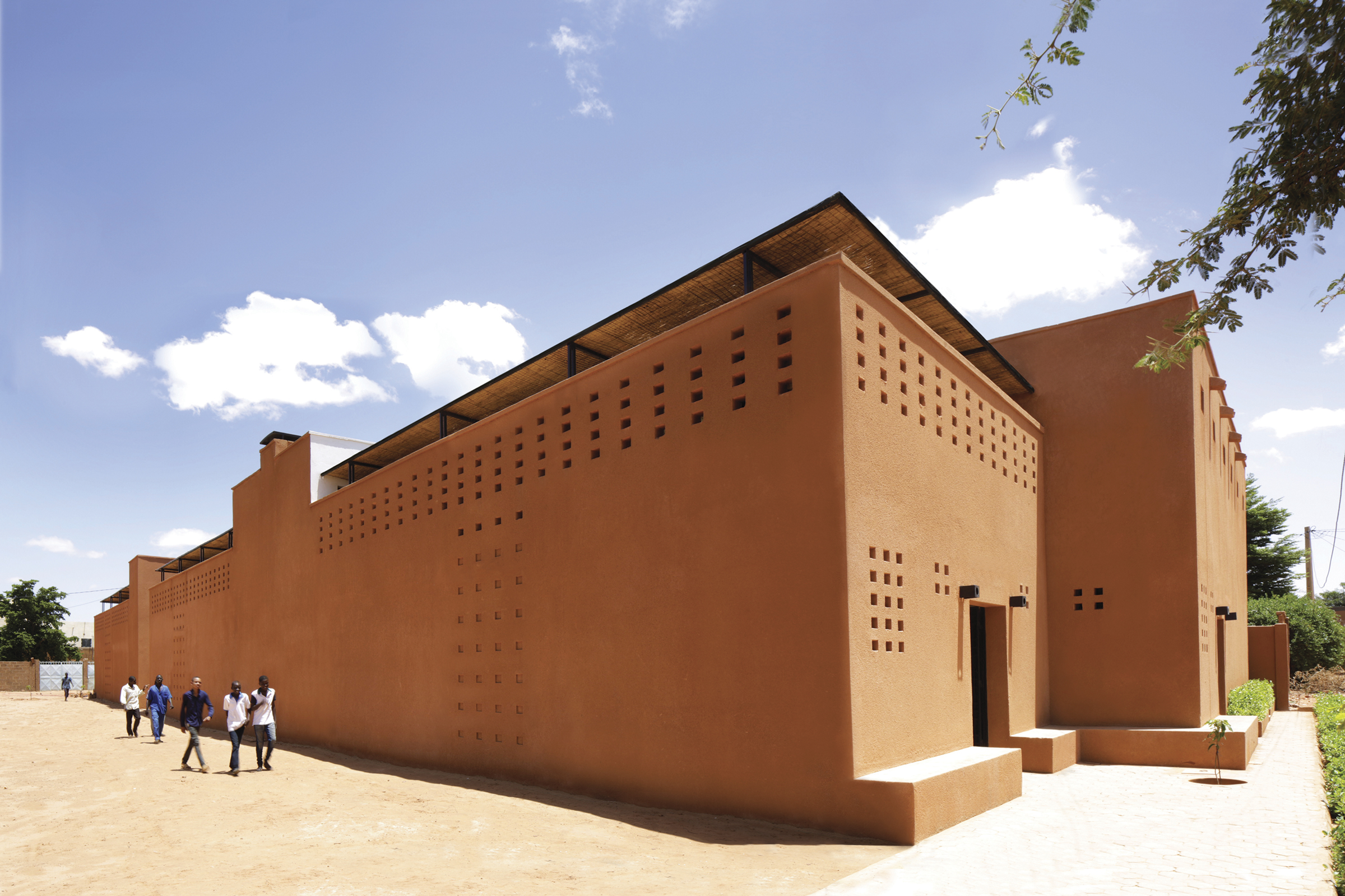
Photo by T. Seidel
In designing the Niamey 2000 housing project, our team took just such a tack, exploring the benefits and challenges that locally derived resources can bring to a housing complex and its community. Early on we made the strategic decision to use compressed earth blocks (CEB) as the primary building material, which was a radical departure in a city where much of the building stock consists of steel and concrete. Compressed earth block offered the best method for integrating earth-based construction with the contemporary requirements of urban housing, which has been in high demand in recent years, in Niamey and elsewhere.
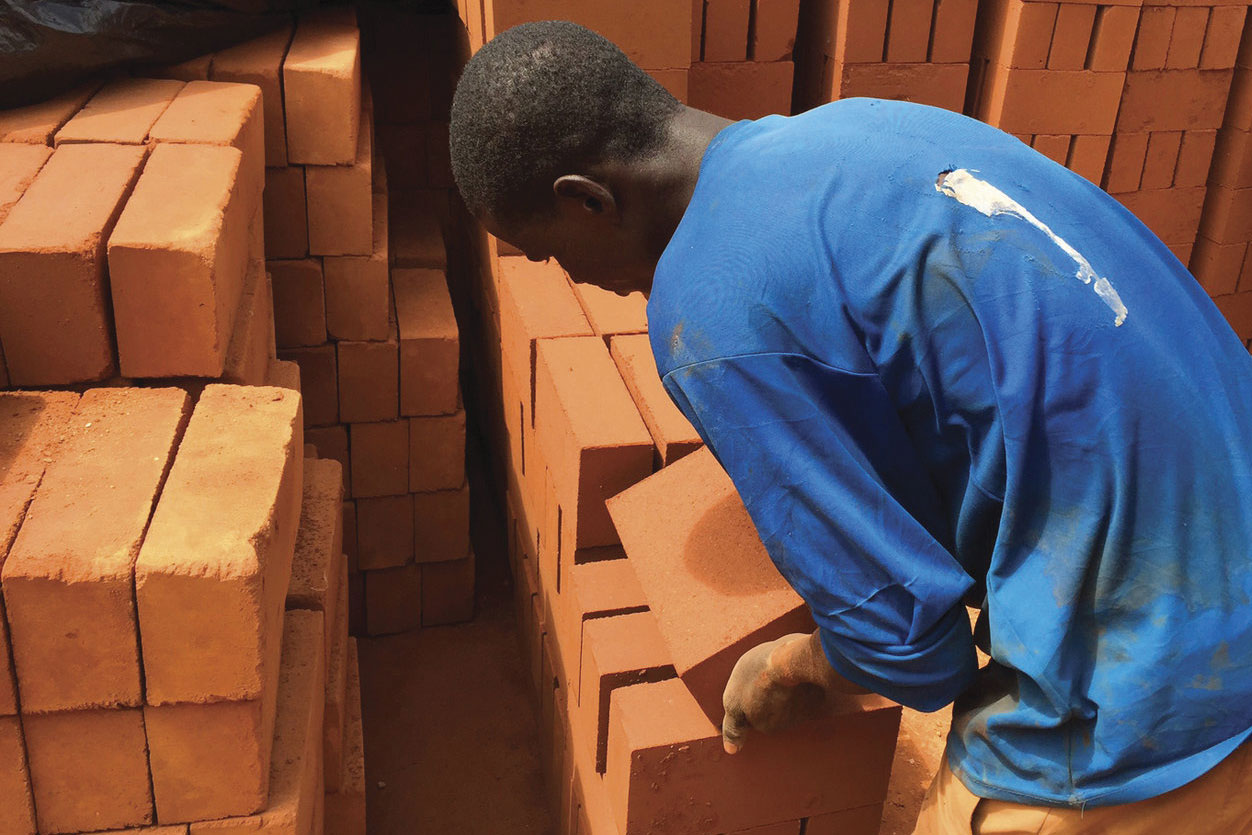
Compressed earth blocks are made by combining earth with cement (typically 4 to 8%) and compressing the mixture with either a manual or mechanical press. Photo by M. Kamara
We felt that housing made from CEBs could set a valuable precedent in a rapidly growing urban center, where most construction materials are imported long distances at great expense. Earth-based construction also provides a buffer against outdoor temperature fluctuations, slowing the transmission of sub-Saharan heat, which is a distinct advantage over other contemporary systems currently in use in Niger. Further, if produced locally in quantity, CEBs can be highly economical and provide low-barrier employment for community members.
Overcoming Challenges
Although we faced fewer constraints than if we had built the project in the US, where these forms of construction are often cost prohibitive or fall outside of code regulations, we still had to contend with prevailing local building practices and cultural preferences. CEB construction is not well known in Niger; most engineers are only familiar with conventional structural systems based on steel or reinforced concrete. Not to mention, traditional materials such as earth are often associated with poverty and have negative connotations despite having a long history of use in the region.
Despite these challenges, Niamey 2000 has successfully introduced CEB construction to the local building sector and familiarized the general public with the benefits of earth-based construction at a time when deadly heat waves are becoming more frequent. The homes remain cool in summer with little or no additional air conditioning, and their contemporary aesthetic has been popular enough with the locals to prompt the construction of a second phase of the project, which was just completed last year.
A Model for the Future
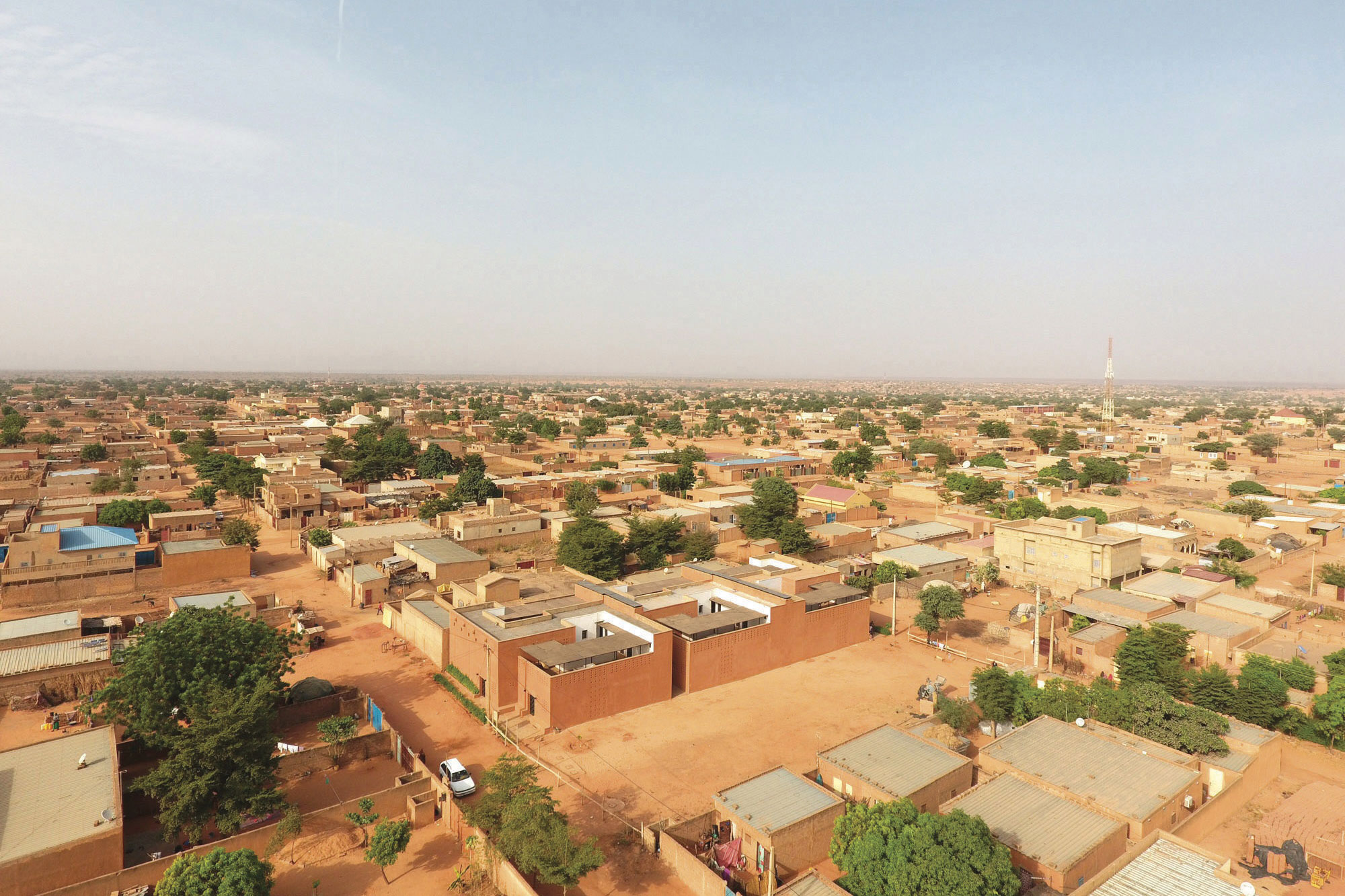
Photo by T. Seidel
Niamey 2000 has also brought CEB construction to the international spotlight as one of the shortlisted projects for the 2020-2022 Aga Khan Awards for Architecture, hopefully inspiring these types of locally sourced housing solutions in other parts of the world. Highly industrialized nations like Germany and Austria have already witnessed the successful development of new systems based on traditional materials like earth and wood. For example, the Vorarlberg region of Austria has seen the proliferation of solid wood construction, with artisans, industry professionals, and architects working in close collaboration, continuing a place-based building culture grounded in craft traditions. The timber industry is a primary driver of economic development in Austria, and as a result, the number of trained carpenters is higher there than anywhere else in Europe.
I also continue to study how principles from Niamey 2000 might be applicable here in the US, where changes to construction practices are often hindered by cost, building regulations, and prevailing conventions. There is a high barrier to entry for new products to the market, which must meet technical challenges like fire regulations just as they address consumer preferences. In the US, despite our field’s current enthusiasm for local and renewable materials, these products have been slow to find their way into mainstream construction scenarios.
I’ve been particularly interested in how traditional building materials and methods could benefit cities like Phoenix—one of the nation’s fastest growing metropolitan regions, which is also facing the distinct prospect of becoming uninhabitable by the end of this century due to extreme heat. Most of the city’s 2,000 square miles of urban sprawl consists of buildings constructed from lightweight wood framing and insulation, which contribute to the region’s dependency on imported resources and mechanical systems for heating and cooling year-round. This has not always been the case. Early inhabitants such as the Hohokam, and later Spanish missionaries, relied on earth-based construction to shelter from the harsh climate of the Sonoran Desert. Could these time-tested, low-tech concepts still have relevance today?
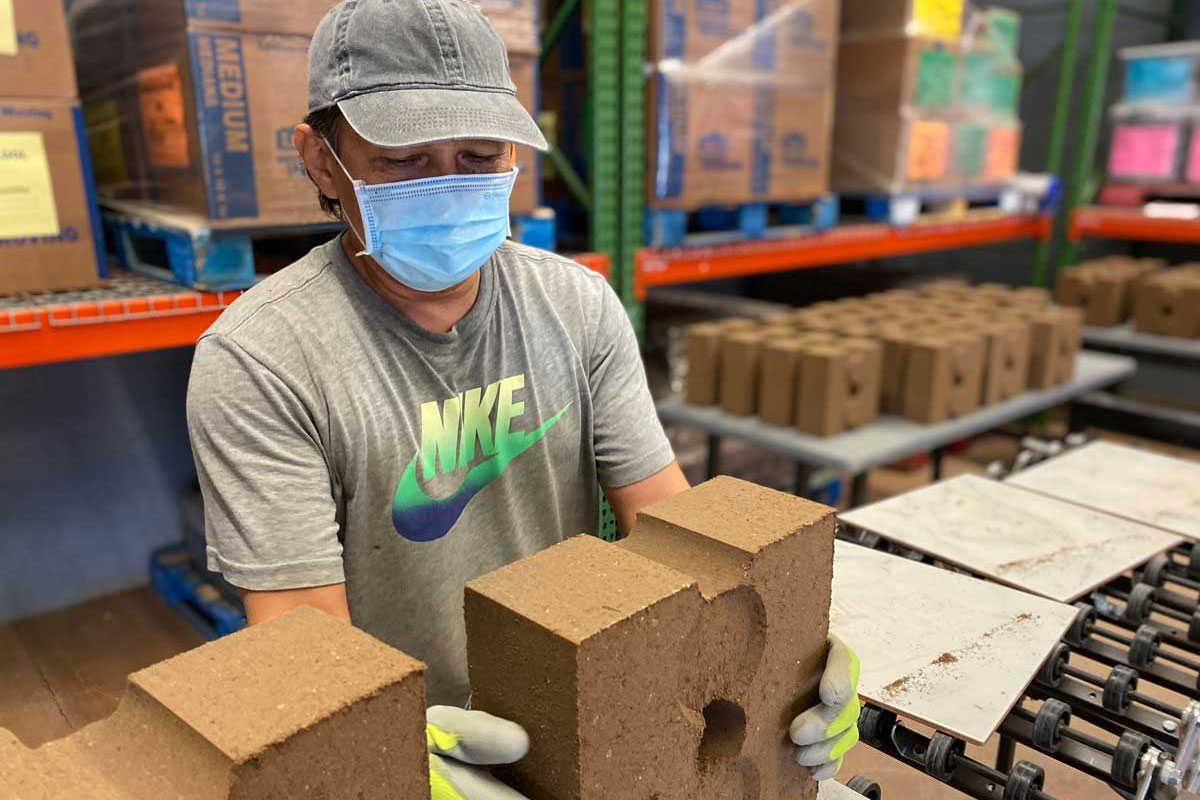
Photo courtesy of Brick by Brick
Groups like Brick by Brick are working to find out. The social enterprise program is part of the City of Scottsdale’s Human Services Department and is manufacturing CEBs in partnership with a local non-profit called Phoenix Rescue Mission. The program provides low-barrier employment for people experiencing homelessness, while working toward the construction of supportive housing for those in need. I see enormous potential in cities manufacturing their own locally sourced, low-carbon building materials like compressed earth block to construct much-needed affordable and energy-efficient housing. Building on this momentum, I am developing multifamily prototypes for Phoenix that, if constructed, would not only demonstrate CEB’s capacity and potential, but also celebrate the material’s cultural significance and connection to the region’s landscape and history.
Of course, we know the AEC industry is slow to adopt change, and it’s a long shot to expect that earth or any other “alternative” material will ever rival the speed and efficiency of wood frame construction or other established methods elsewhere in the industrialized world. However, as Niamey 2000 shows us, there is power in taking small steps toward resource networks that are more closely tied to local environmental, economic, and cultural systems. Step by step—or brick by brick, as in Arizona—we can create buildings that are better for the environment, and for the communities who inhabit them.